Complexity in ISFA (in-service fluid analysis): Part XIV
Jack Poley | TLT On Condition Monitoring January 2014
Balancing cost and evaluation of particle testing.
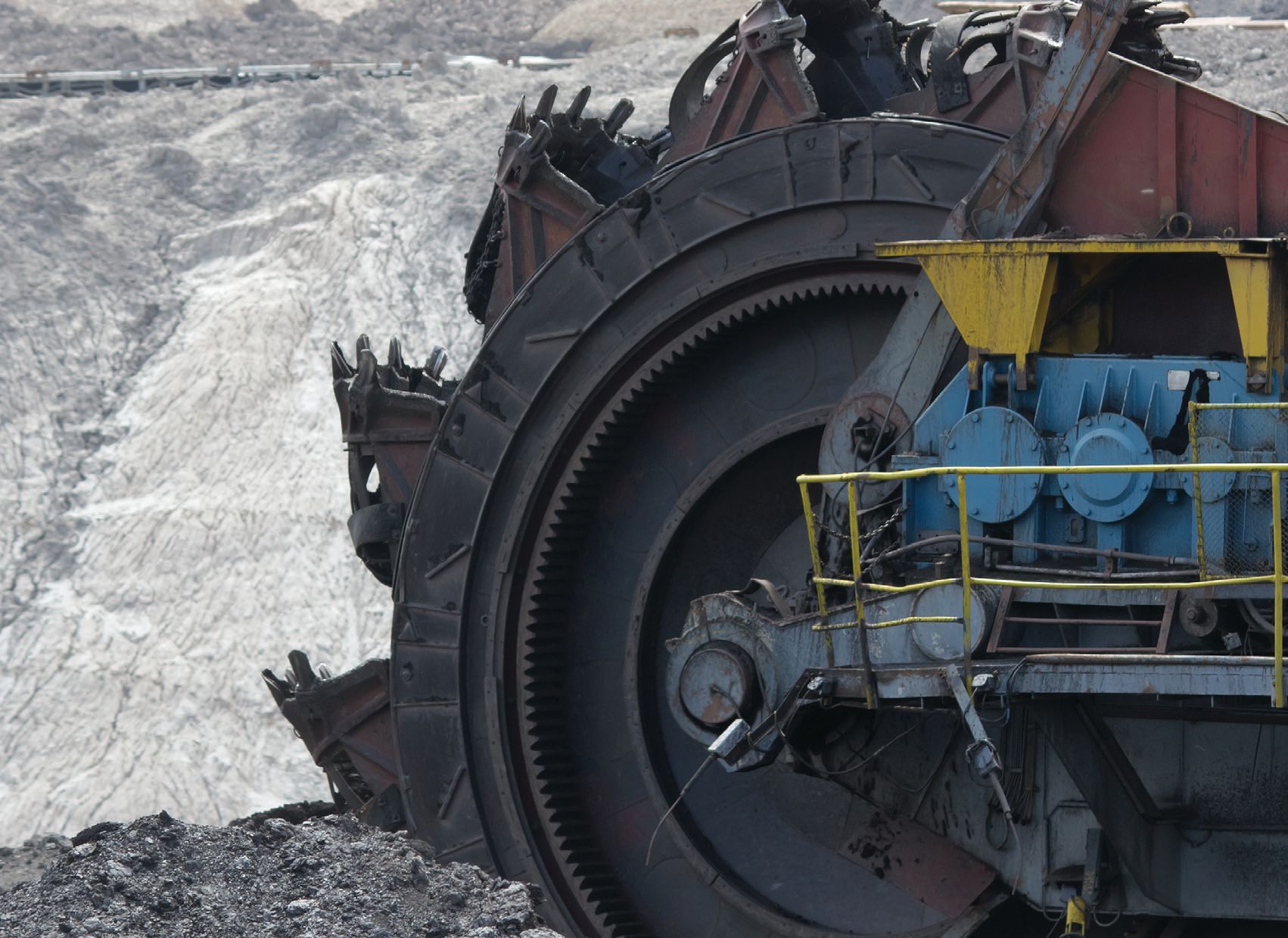
www.canstockphoto.com
LET’S CONTINUE TO CEMENT SOME ACRONYMS like MCM (machine condition monitoring), the ultimate purpose of ISFA. Machinery must perform at full capability to maximize production, whether in a mine, a plant or on a drilling rig. Time is, literally, money.
Downtime* is an expense;
uptime is profit. Everything else is subordinate.
One can break down ISFA yields as follows:
•
Lube/filter condition – indicators for potential wear, indicators for extended service (unsatisfactory VIS can be involved or caused with any of these).
o
Conformation: (is the correct lube in the sump?)
o
Contamination: (abrasives, water, acid, etc. Also, if diesel, fuel dilution or soot; if hydraulic, general particle count)
o
Degradation: (chemical alteration such as oxidation or additive depletion or compromise, e.g., BN or, say, hydrolysis due to water contamination)
•
Machine wear indicators – particles: their composition and their size.
o
Metallic parts
o
Seals
Dependent on the component type and perceived needs, a suite of tests is selected to address each aspect above.
Here’s a question: Are you using an encompassing analytical package to derive the best protection for your asset? And are you sampling at proper intervals to maximize the balance between the cost of the analytical and evaluating services you’ve selected versus the protection you have determined you need?
This is not a tricky question, but it has the age-old reply that often befits questions—
it depends. I’ll let you off the hook on lube/filter condition provided you grant me that satisfactory lube/filter condition
doesn’t necessarily guaranty a healthy machine. Failure to understand that truth has caused many a lube/filter change as a mitigation of a wear event (abnormal to severe levels of wear metals from UV spectrometric analysis or high ferrous wear particle counts or high particle counts not investigated as to composition), with failures occurring shortly thereafter.
What about the machine then? With respect to ISFA, this
does happen to be a tricky question that I’m in the process of exploring in some of the work I do.
PARTICLES OF WEAR AND CONTAMINATION
As noted in the last column, ISFA has expanded particle inspection from smallest possible (even including solutions and particles at molecular level) to “rocks” of 1000 µ or greater. But numbers of the methods are not inclusive of others. Again, you may want to take a look at the initial bar graph I presented in the September 2013 TLT (
available digitally at www.stle.org), with various possibilities (and limitations) for particle inspections. In fairness, not every type of particle analysis is represented, but the point remains that no single technique does it all, though the SEM comes close (and is rarely used for ISFA as its reward).
About three years ago, I introduced the notion of 3-tiered ISFA, which was plausible once the usage of online sensors became practical, in that they actually worked and they could survive the brutal experience of being in a hostile environment. Quickly reviewing:
•
Tier 1: Online ISFA – usually sensors of one kind or another, real-time analysis at last.
•
Tier 2: Onsite ISFA – instruments or testing rigs and setups that are within walking distance of the component being monitored. Rarely all-encompassing.
•
Tier 3: Offsite ISFA – can have capability for full testing options in lab but requiring a shipping effort and corresponding time penalty.
Why is the tier important? Because it’s not possible to perform all the tests currently in play within a single tier and because the tiers imply a sense of time as to information delivery that is increasingly demanded of ISFA. If one could economically inspect the lubricating fluid
in vivo and derive every datum needed for a quality evaluation, that would be the Holy Grail of testing, would it not? Instead we have bits and pieces of necessary/potentially-of-value tests in Tiers 1 and 2. Tiers 2 and 3, of course, cannot produce real-time Tier 1 data, the paradigm changer.
Having established that no single tier can yet do it all, what goes on with particulates in each tier? We want size, quantity and composition in our particles. Again, absent an SEM, we’re not going to get that suite of data as things stand. Nor are we likely to ever see a Tier 1 SEM for ISFA. A matrix for comparison and perspective is shown in the chart.
You can surmise that, if one wanted to have a fairly clear understanding of ferrous particle sizes, one would probably have to have all three instruments listed under Tier 1 in order to have a real-time indication available from rubbing wear, roughly <4 µ and lower, to fatigue wear, generally posited to be indicative from 14 µ and larger. What do we do with particles 5-13 µ? Anything we want, based on what we know about how a given component type wears. (As an aside, what do we do with ISO VG VIS results in between, say, 68 upper and 100 lower specifications, respectively?)
One would also have to finesse the various coverage limitations of each of the three to arrive at some sort of mathematical composite, perhaps using calculus. That would, even with all three instruments’ data facing you, still be assumptive. You also would not be especially pleased (but you should still do it) to have to send an emergency out-of-turn sample to a Tier 3 lab in order to get the smaller ferrous particles counted (as Fe ppm), then trying to make full sense of the added data. Time, however, becomes enemy No. 1 when a sensor fires an alarm.
The specter of time might/should cause one to consider Tier 2 instrumentation such as a traditional particle count and, perhaps, an fdMplus tester (total ferrous), possibly obviating two of the three possible Tier 1 sensors for a significant savings in hardware when multiple machines are involved. A delay of, perhaps, no more than 15-20 minutes might be incurred in order to get supporting data for decision- making once Tier 1 raises an alarm, not an unreasonable proposition. Still, there is no sure way to estimate ferrous concentration at rubbing wear size levels (<4 µ), save for UV spectrometers. Oddly the UV spectrometer’s Achilles heel of not being able to detect particles much greater than a few microns now provides a specific, preferred approach to identifying ferrous debris sized well below the sensors’ sweet spots.
I’ve partially answered the question, “Don’t small particles come before large in the wear continuum?” The remainder of the answer is still more doses of…
it depends. Here are some experience-based speculations for ferrous particle counters.
The Tier 1 ferrous particle sensor counts ferrous wear particles ~40 µ and up, thus such wear would appear to be all fatigue-oriented wear, and that type of wear would usually follow abnormal wear at smaller diameters, given typical wear progressions that one sees in, say, diesels and reciprocating compressors, for sure, and a number of other component types.
From my experience, however, large ferrous particles in diesel engines present significantly less frequently than for most component types, owing to the reciprocating (sliding) friction within cylinders that a diesel (or a reciprocating compressor) incurs in normal operation.
Gearsets, however, are prime candidates to throw off larger particles as quickly (but not necessarily as plentifully) as smaller particles in the operating time continuum. Here one might see traumatic wear more quickly with this type of sensor in play. Gas turbines, with their very high shaft speeds, have shown a propensity to generate large particles at significantly greater ratios to small compared to most other component types. Though I’ve surely seen the characteristics and patterns I’m referencing, I don’t have a lot of organized hard data to put out as proof and, in truth, we would be comparing apples and oranges once we start differentiating component types as disparate as diesel versus gas turbine.
Summing up, it is key to have a comfortable mechanical understanding of the physics and characteristics between component type wear particle generation and test instrumentation capabilities at given tiers, leading to a good scheme for one’s maintenance objectives. Diesel sleeve bearings, e.g., can throw off large particles at accelerated rates versus small when lube starvation and resultant boundary lubrication occurs. Unfortunately, the wear surface is usually non-ferrous (Al, Cu/Pb, Babbitt overlay), unless the bearing “spins,” in which case you’ll not need ISFA to tell you!
Presently, full particle inspection at Tier 1 is moot. We don’t have non-ferrous metal particle counters at full bandwidth, with metal identification,
yet. Grails take time.
*It is rare that the cost of repair or replacement is as great as the lack of a machine’s availability. For simplicity’s sake, we’ll just throw it all into the Downtime mix with the thought that less Downtime equals less repair expense.
Jack Poley is managing partner of Condition Monitoring International (CMI), Miami, consultants in fluid analysis. You can reach him at jpoley@conditionmonitoringintl.com.
For more information about CMI, visit www.conditionmonitoringintl.com.