What is the biggest issue facing the metalworking fluids industry today?
TLT Sounding Board August 2013
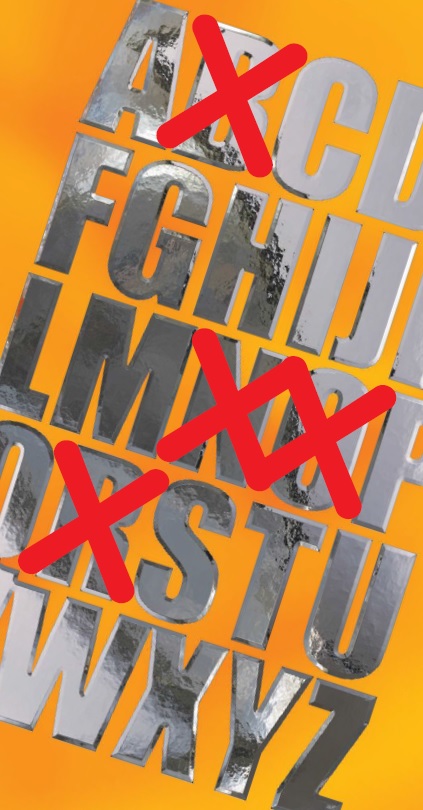
www.canstockphoto.com
The Globally Harmonized System (GHS) of Classification and Labeling of Chemicals, already in place in some parts of the world and slated for 2015 adoption in the U.S., is on the minds of TLT readers, according to responses to this month’s survey. The education process already is under way, with 27 percent of readers saying they are confident in their GHS knowledge. Other readers are concerned about the dwindling number of chemicals that can be used in metalworking fluid formulation, with several respondents citing the loss of boron in particular. “It’s like trying to make the same words with fewer and fewer letters in the alphabet!” says one. The pressure of complying with ongoing and ever-changing regulations remains a challenge. Says one reader: “There is no one controlling body. Rather, it’s a cornucopia of states and countries, each with a different focus or concern.” Also mentioned by several readers is the lack of worker training about the proper use of MWFs. Poor education can increase the risk of health issues to workers and prevent the fluid from performing at its highest level.
Excellent relation price/technology!
Global Harmonized Standard mislabeling. Lots of potential for confusion and mistakes.
Banning of additives used in the fluids. Very difficult to find alternatives.
Separating specialty product claims from good science.
Environmental and health issues.
Quality and productivity.
Lack of adequate housekeeping in the plants.
The biggest issue facing us in the industry is the progress toward more environmentally friendly types of products and the cost of raw materials.
Replacing chlorinated paraffin with more environmental friendly additives.
Regulation, especially with regard to triazine, boric acid and the insane pictograms required for the safety data sheets. Really? If you can’t read the MSDS, you shouldn’t be using industrial chemicals, metalworking fluids, etc. Pictures will only confuse people, and what a mess for us to have to incorporate them on everything.
Environmental issues such as waste disposal.
Distribution and technical knowledge support.
Skilled people/staff to make the fluid perform at the highest level possible.
Health issues such as fumes around the work site. Environmental pollution issues.
Constituents and the health and safety legislation affecting them.
Restriction by legislation for biocide; uncertain situation about usage of boric acid.
Handling boron-free chemistries and low/no-formaldehyde release biocide chemistry.
Monitoring of the MWF by the operator of the machines. Our customers fail to see the advantages of monitoring.
CARB in Southern California. We had to remove products instead of trying to comply with the regulations.
REACH ECHA. Substitution of substances.
The adverse impact of MWF on the environment and how to handle these to achieve the “zero discharge” targets attempted by some plants.
The major issue is the lack of fundamental understanding about emulsion formation and properties, especially lubricity and rust protection. Technical personnel do not know why one product works and another does not. As a result, MWF sales mostly rely on marketing and not on the lubricant quality.
There is no consistency in the performance of the products. Customers have now gone into the mode of price instead of cost per component. Also the slowdown in auto sector and volatility in the base oil market is making it tough for manufacturers to sustain their margins.
Extending the life of a MWF.
Cost of regulatory compliance.
Knowledge on how to properly handle MWFs at the customer’s facility by the employees who use the fluids (concentration, cleanliness, contamination, bacteria, etc.)
Environmental challenges in that there is no one controlling body. Rather, it’s a cornucopia of states and countries, each with a different focus or concern.
Worker health and safety.
Long-lasting coolants that do not produce odors and last for a long time while producing excellent tool life and corrosion protection while minimizing carry off on parts.
End-user friendliness, safety.
Permanent cost pressure, higher customer leverage.
Low sales! No business!
Environmental constraints causing an increase in tooling costs.
Product labeling and the safety data sheets outlined by GHS.
The restrictive California VOC regulations will most likely spread nationwide and push more manufacturers and customers toward green-fluid technologies.
The ever-tightening regulations and restrictions on raw materials.
Governmental guidelines regarding chemicals used within our industry.
EPA and other government agencies. Will we still be able to manufacture in the U.S.?
High prices. Customers, when confronted, look around, which is not a good thing for me.
The limitation of triazine dosage.
No standardizations or approved products for applications.
Chemical costs regarding disposal, handling, human contact (health concerns).
(1.) The demand for cheaper products and (2.) regulatory issues that cause raw materials to be removed from the marketplace. It is like trying to make the same words or at least synonyms with fewer and fewer letters in the alphabet!
REACH compliance and the Chinese equivalent of REACH.
Imports from developing countries, especially China and India. Some products may not be up to North American standards but are inexpensive.
How to keep products performing while meeting the requirements of regulatory agencies.
GHS, particularly the confusion over safety data sheets, REACH and BPD dossiers. How they relate to products manufactured or formulated in the U.S. has created considerable confusion.
Fewer raw materials to work with.
Health issues. Some fluids could make harmful fumes and vapor. Others would sustain bacteria growth, which is a health hazard.
Regulatory restrictions and requirements. Increased cost, over-burdened workforces.
Biocide restrictions.
A number of MWF suppliers in the market producing and supplying low-quality products at a lower price compared with those reputable manufacturers who have been in this industry for years and produce and offer high-quality products and great services.
Bacteria growth.
Regulation of hazardous materials, particularly mists. Developing more environmentally friendly alternatives.
Regulatory issues. Environmental restrictions.
Fewer and fewer additive choices. Loss of boron, for example.
Fungi, lubricity and environmental concerns are at odds—one suffers when you satisfy the other. If you can’t machine products, you can’t make money or products.
How well versed do you feel you are about GHS?
I’m confident in my knowledge about GHS.
27%
I have a basic understanding but need more information.
37%
What standard?
36%
Based on responses sent to 13,000 TLT readers.
What emerging technologies will most affect MWFs in the next decade and beyond?
A technology that supports all types of public water hard or soft.
Biobased coolants.
New tooling and environmental friendly fluids.
Working materials and tool design.
3D printing.
Getting away from the boron amide technology will have a major impact on MWFs.
The use of other base stocks besides Group I base oils.
Dry machining.
Extending the life of machine tools.
Proper filtration, new techniques on hazardous-substance handling, PPE.
I am a fan of the near-dry lubrication machining technology concept in MWF.
The need to move to safer, biodegradable and synthetic materials.
New molecules with high biostability but no harm to the environment or humans.
Perhaps more in-line monitoring? Chemical regulation.
Nanotechnology for performance enhancement and efficient treatment techniques to mitigate adverse environmental impacts.
Surfactant package is the key to MWF. The formulators who can develop synergistic mixtures with good lubricity and RP at high dilutions will dictate the MWF trends.
A robust tool design along with a lubricant source device should give a boost to the MWF sector, as well as the industrial sector as a whole.
Better synthetic lubricants, better biocides and better tool construction through better materials.
Technology surrounding longevity of MWFs and the use of different chemistries that incorporate silver into the formulas and potentially other special metals that aid the ability to fight bacteria and fungus within sumps.
Biobased fluids that are more worker friendly.
The development of formulas that do the job without having to use tankside additives and biocide/fungicide treatments.
MQL, nano-based fluids.
Machining ceramics or using ceramic tools, porosity and absorption characteristics of materials.
Low VOC base stocks to produce low-VOC MWFs.
Printing may be an issue depending on the speed and development of this technology.
New base stocks, the shift in manufacturing to new and alternate alloys, tooling design and regulatory and registry strangulation.
Waste and reuse.
REACH, reusing biocides, ongoing regulations and MSDS issues.
3D manufacturing.
Continued development of synthetic base stocks and performance additives.
Actual testing of chemicals instead of just banning them because one 30-year-old study says they might be harmful 1 percent of the time.
Vegetable base fluids, low-VOC fluids and chlorine removal.
Coatings.
Chlorine-replacement chemistry.
Better recycling processes.
Perhaps better cooling methods will be developed that allow for the use of less mist-intensive alternatives.
Editor’s Note: Sounding Board is based on an e-mail survey of 13,000 TLT readers. Views expressed are those of the respondents and do not reflect the opinions of the Society of Tribologists and Lubrication Engineers. STLE does not vouch for the technical accuracy of opinions expressed in Sounding Board, nor does inclusion of a comment represent an endorsement of the technology by STLE.