Complexity in Oil Analysis: Part XI
Jack Poley | TLT On Condition Monitoring July 2013
Exploring real-time oil analysis and other sensor data techniques.
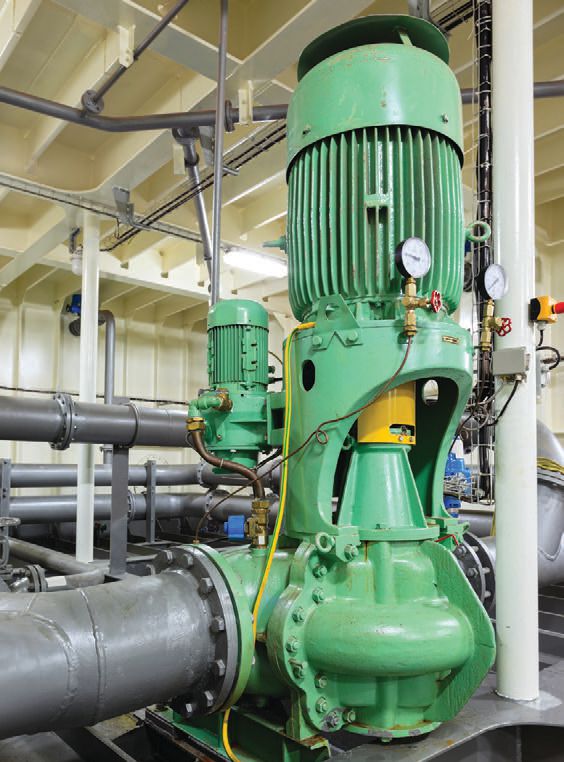
www.canstockphoto.com
WE DISCUSSED THE NOTION of combining static event data (oil-sample analysis or OA) involving a suite of tests, along with continuous data (real-time vibration analysis or VIB) in the
May TLT.
I noted that OA and VIB have heretofore not played nicely with each other. Often two different maintenance departments of an entity are involved for these separate functions and correlation between the two is unlinked more often than not. Further back in this series, I discussed real-time OA via smart sensors capable of detecting general problems and some specific ones. All of these techniques, including others that are appropriate, can and should be correlated in order to arrive at the best indications of machine and lubricant condition.
This is the essence of condition monitoring (the holistic health picture) complete with prognosis for the future and such notions as remaining expected machine life. We are already at remaining lubricant life estimation, but the Holy Grail is to predict a machine’s status over time based on present information. This is a tall order that will not be fulfilled easily, nor fulfilled for any and all machines. There will be practical and technical limits, but there is no doubt this is the pursuit that is continuing to gain traction.
We are all aware of the implied need to have useful information available as soon as possible. Modern technology has created and continues to fan a permanent impatience because we see these capabilities in one medium or another, and we want it in our milieu, too. If it’s condition monitoring, we want the instant gratification sensors provide.
I’ve mentioned several times that Tier 1 OA (online smart sensors) have changed the OA paradigm. The paradigm hasn’t nearly taken full effect because it’s the beginning of the Tier 1 era, though I can all but guarantee it will have an enormous impact on the way CM moves forward. Technology, fueled by demand for fast data, will make this prediction realized. Let’s look at what we have at the outset of this new era.
There is clearly a challenge to melding the two information types—dynamic and static (episodal)—to reach a synergistic proposition. As I’ve noted before, computers need to be involved from data gathering to data evaluation. Context will be complex, more so than ever as there are simply much more data to deal with.
Part of the notion behind sensor development is the prospect of curtailing routine Tier 3 OA in lab environments, or at least confining it to Tier 2 (on-site) testing hardware and instrumentation. This makes sense to an extent, as Tier 3 outside lab expense can be saved, but this is not always a straightforward decision, nor the best one to make, particularly when the stakes are high in terms of the machine’s value to production.
Here’s a table that presents both sides of the equation for a number of considerations, however, it should be noted that we are, for now, confining the table to OA and not its cousin, VIB, or any other data such as onboard machine monitoring (i.e., an ECM [engine control module]).
The Interplay of Online (Sensors) and Offline Oil Analysis
Following are some comments on the table:
•
Sensitivity. This is a consideration with sensors, and it affects the decisions one can expect to make with confidence based strictly on sensor data and their alarm levels. Usually it’s necessary to vet the sensor’s readings with a more specific suite of tests. Water may be the one exception.
•
Repeatability and accuracy. Both are important considerations. What the sensor lacks in pure detection capability, it makes up for being immersed in the circulating lubricant; thus it has the most representative sample. Keep that thought in mind when we get to water later in this list.
•
Robustness. Current sensor quality in terms of performance and expected longevity or MTF (mean-time-to-failure) is what made Tier 1 testing a valid term (i.e., the notion of online monitoring with good efficacy). It is still possible for sensors to malfunction or foul or fail to transmit in some way or other, but this is not a high-expectation event.
•
Scope. The obvious limitation that sensors have. Today sensors are available to:
1.
Count metallic ferrous particles and infer nonferrous metallic particles.
2.
Determine VIS.
3.
Determine water (usually via humidity measurement, excluding dissolved water).
4.
Oil condition—a general dielectric/conductivity test that discloses a change in the lubricant’s conductive property. Unfortunately, such a change can be triggered by a variety of unrelated problems or contamination. It is a valuable thing to know the conductivity, but it must be vetted with more specific testing (i.e., no decision to change a lube based on this test should be made without additional validation, unless one sees an obvious problem such as copious amounts of water).
5.
There are some algorithmic oil condition sensors that can infer certain characteristics such as oxidation or remaining useful life, but those applications are not necessarily generalistic, nor easily vetted at the sensor.
•
Water. Instruments such as Karl Fischer water testers can determine water at very low concentrations with excellent precision. Securing a representative sample, however, is not an easy proposition when water and the lube do not mix nicely (yes, an emulsion is a nice mix, to an extent, but it’s a bit late, wouldn’t one say?). Taking cold samples or sampling from the bottom of a sump, for openers, are nonstarters. For that matter, extracting an aliquot from the sample bottle submitted to the lab has its own repeatability issues, even when one is alert enough to shake the sample vigorously (in a shaker). Again, if the sample in the bottle is unrepresentative, what use will shaking be?
•
Metals. Magnetometry has put ferrous particle detection and quantification into the realm of sensor technology, which has legitimized the notion of Tier 1 testing— however, that’s the extent of things, for now. One cannot rely strictly on Fe to draw conclusions about wear, except in extreme situations. It is this limitation that needs to be overcome before it truly is a good idea to limit one’s lab testing. Proceed at your own risk until the technologists get over this hurdle.
•
Oil condition. See Scope above.
•
VIS. Sensors for VIS are now making their mark. A lab will likely always be more accurate, but a funny thing about VIS in an in-service oil is that accuracy can be sacrificed for good approximation. Thus, if a VIS is 10 percent “off” one way or another, it likely doesn’t affect the domain expert’s evaluation of the overall picture unless there are numbers of other test results that are deemed abnormal. In short, steady VIS monitoring is very desirable onboard/online.
•
AN (acid number). See Scope above.
•
BN (base number). See Scope above.
•
Particle count. If it’s necessary, a full-blown particle counter can be fitted to most machines, and it’s been done numerous times. This is a matter of how valuable, or necessary, a particle count is to the operation of the machine under scrutiny.
•
Fuel dilution. There really is only one strong way to be assured there is diesel fuel in excess in a lubricant— gas chromatography (actually a steam distillation works fine, too, but is a bit cumbersome these days). FTIR is a possibility but only if one has representative diesel fuel samples that match the fuel type being analyzed, else the values will be skewed. Most important, the sensitivity isn’t very good due to the chemical similarity between fuel and lube. What about VIS by itself? Well, that’s the problem—there are several reasons why a VIS could go up or down or remain in spec while two unrelated problems existed, one which would cause a VIS increase, the other a decrease. A flash test of some sort (open or closed cup) can help when fuel contamination is perhaps five percent or greater, and this can be accomplished at Tier 2 level. It’s a question of how credible or effective one wants one’s results to be. Be sure to bring the customer into the discussion.
•
Possible lube mixing. See Scope above.
We’ll continue with this theme next time.
Jack Poley is managing partner of Condition Monitoring International (CMI), Miami, consultants in fluid analysis. You can reach him at jpoley@conditionmonitoringintl.com.
For more information about CMI, visit www.conditionmonitoringintl.com.