Fire-resistant fluids: Will they ever be good enough?
Jean Van Rensselar, Contributing Editor | TLT Cover Story July 2013
New regulations and increased performance requirements are changing the way researchers develop modern fire-resistant fluids.
KEY CONCEPTS
• There is no affordable fire-resistant fluid on the market that offers safety assurance and acceptable in-use performance.
• Despite ever-increasing performance demands and new regulations, the incentive for research isn't there.
• Coming to a consensus on key fire-resistant definitions continues to be a significant problem with no resolution in sight.
What is preventing researchers from creating a fire-resistant fluid that offers safety assurance, affordability and equipment compatibility—qualities that no single fire-resistant fluid (FRF) has today? Unfortunately, there are several factors.
STLE-member Brian Goldstein, product marketing manager, lubricants & fuel additives, Dow Chemical Co. in Houston, explains, “From my point of view, while breakthrough innovation in the area of fire-resistant properties has been slow, researchers continue to look at ways to improve overall performance attributes of FRF formulations. In the past, certain chemistries, which may inherently provide improved performance, have not been cost-effective due to economies of scale or availability of raw materials. With changing regulations and equipment design, the need for innovation does exist, whereby alternative chemistries can be considered.”
“Another hurdle to development has to do with the commercial feasibility of successfully introducing a new technology. Without a clear economic payoff for the development effort required, base fluid suppliers and formulators have little incentive to invest additional R&D capital in developing FRFs,” Goldstein says. “That said, changes in industry standards and regulations will naturally stimulate further development if the scope of the expected changes was deemed realistic.”
Regulations for FRFs continue to tighten, and new FR and environmental standards are emerging in regions such as Asia. In addition, equipment builders are developing machines with higher power densities and operational output, putting further demands on lubricants and especially water-based FRFs.
Since their inception more than 60 years ago, FRFs have offered an added degree of safety protection over hydrocarbon-based fluids in industries such as steel/aluminum processing and mining. But the degree of actual fire protection for the many types of FRFs is controversial.
Today’s FRFs span a wide range of technologies including water-based fluids (e.g., water glycol HFCs) and anhydrous fluids (phosphate esters, polyalkylene glycols [PAGs], vegetable oils and esters). Each fluid type brings its own specific advantages. Waterbased fluids are inexpensive and offer excellent fire resistance, but they only work in moderate pump operating conditions. Anhydrous fluids can operate under severe pump conditions, but their fire-resistance performance is limited.
In the area of anhydrous-based, fire-resistant fluids, there has been much debate about the different types of fluids and their fire-resistant properties. It is generally accepted that phosphate esters offer the highest degree of fire protection. But on combustion, highly toxic and corrosive fumes can generate and create a deadly environment (1).
Others would say that newer fluids such as synthetic esters and PAGs don’t provide acceptable fire resistance and that protection is barely better than hydrocarbon oils.
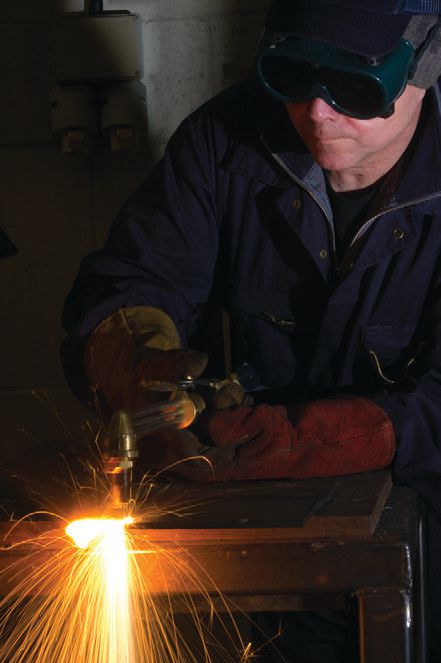
Fire-resistant fluids offer safety protection over hydrocarbon-based fluids in industries such as steel/aluminum processing and mining.
RISK FACTORS
Regulators and test developers look at the fire risk that a lubricant poses, especially where enclosed spaces such as mines and tunnels are involved. Five factors they consider are:
1. The possibility that a release will occur
2. The likely scale
3. The possibility that it will ignite
4. The possibility that it will combust
5. The potential safety, health and financial consequences.
The environments at most risk for hydraulic fluid fires are mines, mills and planes. Put two of those together—a coal-handling facility integrated into a steel mill—and the danger multiplies exponentially.
Mines. While most maintenance facilities and especially any mobile equipment pose a fire risk, underground mine maintenance facilities are a particular hazard. Fires in diesel-powered mining equipment most often occur because of leaking high-pressure hydraulic lines that spray heated and highly combustible fluid onto an ignition source such as superheated metal exhaust. Fires that ignite in this way tend to spread quickly.
Adding to the danger is that much of the mobile equipment used in underground mines contains not only fuel sources but also ignition sources—making them virtual fire factories. Given this, it’s not surprising that welding and cutting operations, which are carried out regularly, are a leading cause of mine fires. Then there’s the presence of coal dust, which is extremely combustible. An additional consideration is the grim fact that enclosed mines not only encourage the rapid propagation of flames into full-scale fires, they also leave their occupants with limited opportunity for a quick escape.
Steel mills. Heated metal is a pervasive ignition source in most industrial environments. Because of the abundance of heated metal (in both liquid and solid form), steel mills pose a particular fire hazard. This is especially true if the floor plan doesn’t provide adequate separation between hydraulic lines and ignition sources. A small hydraulic fluid leak almost anywhere on the floor in many steel mills could either cause an explosion or a fire that quickly becomes out of control.
Airplanes. Some people wonder why fire-resistant hydraulic fluid is so important in airplanes since there are also thousands of gallons of highly combustible fuel. There are two reasons: (1.) hydraulic fluid typically circulates throughout the aircraft. This means a single ignition could quickly spread through the structure and (2.) hydraulic fluid—unlike fuel—is under extreme pressure. A small leak can quickly mushroom into a high diameter, three-dimensional spray that will interact with any ignition source, including super-heated metal.
World War II was a watershed moment for FRFs. Modern war machinery, especially tanks and airplanes, caused far too many fiery deaths on all sides. It became glaringly apparent that anything that could be done to prevent or reduce the consequences of fire-related casualties should be done. Also, as a result of modern machinery (more ignition and combustion sources), around this time there were many tragic coal mine fires. Although fuel was responsible for a percentage of these fires, ignitable lubricants were responsible for many more.
One of the solutions researchers looked at was adding water to existing fluid. This led to the development of nearly self-extinguishing, water-based lubricants. Another solution was developing an entirely new category of synthetics capable of resisting and extinguishing flames. Some of these (imperfect) products are still in use today—a fact that points to the need for a renewed research effort and better products.
CONFUSION OVER TERMINOLOGY, DEVELOPING CONSENSUS
Asked if he thinks the current definition of an FRF is clear, David Phillips, hydraulic fluid and lubricant consultant with W. David Phillips & Associates, says, “No, there is still a dichotomy between the requirements of ISO and those of Factory Mutual Corp. ISO has recently published a revised specification for fire-resistant hydraulic fluids, and attempts will be made to obtain precision data on the different ISO fire-resistance methods. If this is successful, it may then be possible to classify fire resistance on the basis of performance in the different tests.”
Coming to consensus definitions of fire-related properties is of utmost importance because the consequences, in terms of injury and death, legal proceedings and financial losses, are so high. The meaning of fire resistant varies from discipline to discipline, industry to industry and material to material. Both fire resistant and fireproof are (wrongly) used as synonyms for incombustible and not ignitable. Actually combustion and ignition can create a fire independently of each other. For example, water-based lubricants can ignite without combusting. When the temperature is sufficiently high, a fluid can combust but not ignite. Fireproof should refer to a substance that is neither ignitable nor combustible. Fire resistant should refer to the degree of resistance to ignitability and combustibility. It’s important to note that the terms flame-propagating and combustible are not synonymous. Following are some very basic consensus definitions:
FIREPROOF: Impossible to ignite, combust or propagate a flame.
FIRE RESISTANT: Extremely difficult or impossible to ignite and not capable of propagating flame.
FIRE RETARDANT: Difficult to ignite and will not significantly propagate flame.
IGNITABLE: Energy from an ignition source can raise the temperature to point of ignition.
COMBUSTIBLE: Burning (combustion) results in a flame.
FLAME PROPAGATING: Roughly the same as combustion (but there must have been an original ignition). Fluid continues to burn (as a flame) when it is no longer in contact with the ignition source.
AVAILABILITY
The ideal FRF doesn’t exist, but if it did, it would have the following three qualities:
1. Safe: It would actually be fire resistant in all applications and environments.
2. Equipment friendly: It would possess basic lubrication properties that prevent erosion, corrosion, sludge and other equipment-unfriendly conditions.
3. Affordable: It would be financially practical for applications that require a continuous and significant amount of fluid.
Then there are a lot of nice-to-haves (requirements in some applications) such as biodegradability, low environmental toxicity and quick availability.
Following are three main types of fire-resistant hydraulic fluids:
1. High water-based HFAs
2. Water-glycol HFCs
3. Synthetic HFDs.
According to STLE-member W. David Phillips, hydraulic fluid and lubricant consultant, W. David Phillips & Associates in Stockport, U.K., current test data ranks fluids in the following order—from most to least fire resistant: water-based fluids (depending on the water content), aryl phosphate esters, polyglycol ethers/polyol esters/ vegetable oils and mineral oil.
High water-based HFAs. High water-based fluids, also known as HWBFs, high water-content fluids (HWCFs) or ISO HFA fluids contain droplets of specially refined oil dispersed in water. This means the fluid behaves more like water than oil. Microemulsions, with a considerably smaller droplet size, are nearly transparent.
Advantages
• HFAs have both cost and environmental advantages. They can be made from concentrate and are less toxic than other FRFs (2). HFAs are highly fire resistant and have excellent cooling characteristics. When properly formulated, these fluids offer strong protection against rust and acceptable steel-to-steel lubricity.
Disadvantages
• Compared to the other two groups, HFAs can have inferior performance and operation. For example, they have much lower viscosity, film strength and lubricity than oil-based lubricants. A significant disadvantage is that equipment components must be designed specifically for use with HFAs. The high water content creates susceptibility to freezing, which also reduces the effectiveness of additives. High turbulence produces bubbles that lead to cavitation and wear. Also, seal materials that deteriorate in water (such as paper, cork and leather) cannot be used.
“Water-containing fluids have been in use for many years, and their performance has undoubtedly improved, but limitations remain regarding lubrication, volatility, low temperature behavior and corrosivity,” Phillips says. “To be used successfully, they require a tight operating envelope, components that are compatible in terms of both corrosion and lubrication and possibly a pressurized tank. The lower cost of these fluids is therefore usually more than offset by more expensive systems.”
STEEL MILLS AND HFCS
Tony LeBarge, director of technology, KOST USA, Inc., says that today’s steel mills need HFCs with a number of key characteristics, including the following:
OPTIMAL WATER CONTENT. The water content provides the primary fire resistance. A minimum of 35 percent water is typically required to maintain optimum fire resistance. Too much water can adversely affect pump performance and cause premature failure. For this reason, less than 41 percent water is recommended.
SHEAR STABILITY. As machine and maintenance practices improve, there are greater demands on fluid. The higher pressures, temperatures and flow rates, along with reduced down times, expose the fluid to more shearing stress. This can result in permanent viscosity loss, which can make equipment more susceptible to premature failure. The correct choice of customized or optimized polymer thickeners will become increasingly important.
CORROSION CONTROL. Because they contain a high proportion of water, HFCs have a greater tendency to corrode ferrous parts. A fluid properly formulated with corrosion inhibitors will reduce or prevent this. However, the area of most concern is where the fluid does not come in contact with the parts needing corrosion protection. Due to elevated operating temperature and the volatility of water in the fluid, water vapor tends to condense into the cooler-head space of components such as reservoirs and storage tanks. This is why many fluids contain vapor-phase corrosion inhibitors. The challenge is to maintain the proper levels throughout the fluid life. These inhibitors are designed to evaporate and protect the metal surfaces from corrosion due to water vapors. The challenge is to select a corrosion inhibitor that volatizes slowly enough to maintain protection over an extended service application.
Water-glycol HFCs. Water-glycol fluids (ISO HFCs) are composed of 35-45 percent water for fire resistance, a glycol, a water-soluble thickener to improve viscosity and additives that prevent foaming, rust, corrosion and improve lubrication. But compared to most fire-resistant anhydrous fluids, HFCs are poor lubricants.
Advantages
• HFCs generally have good wear-resistance properties where there are not high speeds and high loads. Synthetic seal materials used with petroleum oils are also compatible with HFCs.
Disadvantages
• The cost of HFCs is greater than conventional oils. HFCs must be continually evaluated for water content, and any evaporated water must be continually replenished. Evaporation might also reduce certain additives, which will shorten the fluid life and hydraulics. In order to avoid evaporation, operating temperatures must be kept as low as possible. As with HFAs, seal materials that deteriorate in water cannot be used. Metals that react adversely with HFCs such as cadmium, magnesium and zinc will generate a machine-destroying gummy residue. Even parts alloyed/ plated with these metals cannot be used with HFCs.
Anhydrous synthetic HFDs. Synthetic fire-resistant fluids (ISO HFDs) are lab-synthesized chemicals that are less flammable than petroleum-based oils. HFDs include phosphate esters, polyol esters, halogenated (fluorinated and/ or chlorinated) hydrocarbons and mixtures of phosphate esters or polyol esters and petroleum oil.
HFDs ignite easily. They may also contain a polymer thickener that will increase the droplet size in a spray. While this makes the spray less ignitable and might improve the performance of new fluid, as the polymer shears down during use, the fire resistance reduces to the point of being on par with a polymer-free fluid. This means that the actual fire resistance of HFDs can be hard to pin down (3).
Advantages
• Since HFDs do not contain any water or other volatile material, they operate better at higher temperatures than water-containing FRFs. They also are better for higher-pressure systems than water-containing FRFs. Also, unlike other FRFs, they degrade very little in use and perform well in low temperatures.
Disadvantages
• Despite this, HFDs are not the best among FRFs for low-temperature operations. There is also the issue of toxic fumes as these FRFs degrade. But Phillips points out, “All non-aqueous hydraulic fluids can emit noxious products when they combust or thermally degrade—not just phosphates. The volume and type of decomposition products will, in part, depend on the conditions under which combustion or thermal decomposition occurs. For example, the availability of oxygen will determine whether full or partial oxidation products are formed (the formation of CO as opposed to CO2).”
Low water-based HFBs. Primarily used in Great Britain, low water-based HFBs are water-in-oil emulsions with a maximum of 60 percent combustible (petroleum) material. This means they must contain at least 40 percent water. Because of the relatively high petroleum- to-water content, they are commonly referred to as invert emulsions.
Additives. Despite many attempts, there are currently no additives—other than droplet-size modifiers—that will make a flammable material more fire resistant. As it stands, the fire properties of a lubricant are determined by the fire properties of the base stock, rather than the additives.
FACTORY MUTUAL ACCREDITATION (4, 5)
Factory Mutual Global (FM) approval testing for flammability is considered among the world’s most rigorous. FM statistics show that fire protection deficiencies for lube-oil systems were a major factor in 17 large turbine building fires that resulted in over $400 million in gross losses during a recent 15-year period. FM says that the use of an FM-approved industrial fluid can prevent or significantly reduce the extent of damage in a fire.
FM Approval Standard 6930, Flammability Classification of Industrial Fluids, evaluates the ignitability characteristics of industrial fluids by determining a spray flammability parameter for industrial fluids that have a fire point (6). For water-based fluids without a fire point, the standard requires the calculation of a different parameter.
FM-approved industrial fluids represent a low fire hazard and do not require additional automatic sprinkler protection. While specification-tested fluids are less ignitable than mineral oil fluids, they still may stabilize a spray flame and may require sprinkler protection.
For many years, the U.S. Mine Safety & Health Administration (MSHA) has had a similar FRF evaluation program for qualifying fluids that are used in coal mines. MSHA test procedures are similar but not identical to FM.
Brian Goldstein, product marketing manager, lubricants & fuel additives, Dow Chemical Co., explains, “In the U.S., FM Approval is a requirement for doing business with most industrial end-users who operate equipment in environments where fluids can be exposed to extreme heat. FM accreditation of fluids continues to be leveraged across lubricant markets, as end-users become more conscious about safety and loss prevention. For fire resistance, FM accreditation remains the standard that industry tends to accept.”
STAKEHOLDERS
Although everyone is primarily concerned about the safety and welfare of those who work with and around hydraulic fluids, OEMs tend to place greater importance on equipment compatibility and in-use performance than end-users.
Equipment builders. Dow’s Goldstein explains that OEMs are interested in evaluating new fluids, but it is not always possible for OEMs to vet all fluids. “Therefore they may take a general approach to ensure compatibility and performance with conventional fluids,” he says. “While some OEMs are in the business of selling aftermarket products and service, others are in the business of selling long-life equipment. Different OEM business models will dictate to what extent fluids are tested and approved. An OEM who sells long-life equipment may recommend the use of a fluid that complements performance expectations and warranty claims, thus completing more rigorous fluid testing. In the case of building smaller, faster, longer life equipment, OEMs are considering innovative base fluid chemistries and formulations.”
End-users. “Fluid users need many things from their suppliers,” explains STLE-member Tony LeBarge, director of technology, KOST USA, Inc., in Cincinnati. “Today’s fluids must perform over longer service intervals for many reasons, including the increased cost of disposal. As a result, the need for specific and timely fluid analysis continues to be more important. Also, as companies strive to increase shareholder value, end-users are asking their suppliers for help with improving performance and reducing expense.”
In the U.S., many end-users require that fluids have Factory Mutual (FM) accreditation. Goldstein explains that while FM approval provides a standard for fire resistance, it does not take into account a fluid’s chemical properties, tribology characteristics and any resulting impact on equipment performance. “End-users must perform additional due diligence by considering operating conditions, rate of fluid top-off, equipment design (including construction materials) and economics,” he says. Goldstein also believes that as regulation continue to drive up the total cost of ownership for conventional fluids, it will improve the relative affordability of advanced synthetic fluids.
WHAT A HYDRAULIC FLUID FIRE LOOKS LIKE (7)
When hydraulic fluid is released under pressure, the usual result is an atomized spray or mist of oil droplets that may extend as far as 40 feet from the break. The flammable oil spray can be easily ignited by hot surfaces such as heated or molten metal, electric heaters, open flames or welding arcs. The resulting fire usually is torch-like with a very high rate of heat release. Automatic sprinklers can protect the building and prevent involvement of other nearby combustibles, but the torch-like fire presents very little burning surface for cooling or wetting. The high-heat release can continue, triggering multiple sprinklers until the oil discharge is stopped.
DEVELOPING NEW FRFs
Phillips isn’t optimistic that any new FRFs will be on the horizon soon. He points out that FRFs are a niche market and any new chemistry would be extremely expensive to develop.
The only intriguing relatively new products are fire-resistant polyol esters—first introduced in 2005.
Fire-resistant polyol esters (8). For many years, some industrial users have preferred polyol ester fluids to phosphate esters for reasons of cost, system compatibility, environmental concerns and worker health and safety. Some of these industrial users would also prefer to use a new FM Global Approved product and have created a demand for new organic ester technology. These products would combine the environmental benefits of polyol esters with the FM approval status of phosphate esters.
Because of this demand, research is focused on organic esters with higher intrinsic fire-resistance properties. The result is a class of esters that can be formulated into FM-approved fluids without the presence of water or phosphate ester. They have excellent lubrication properties, as well as intrinsic resistance to ignition and flame propagation.
Through selection of the acid and alcohol components, custom esters can be designed for use in fire-resistant hydraulic fluids that meet all performance requirements and approvals without the use of (non-fire-resistant) polymer-based additives. This makes new polyol ester fluids available for applications that require new FM approval and/or ISO approval where operators prefer not to use fluids that contain water or phosphate ester (9).
The chemical nature of these new polyol ester bases also makes them readily biodegradable for applications that require environmentally friendly fluids. Drain intervals and cold-weather performance are superior to that of vegetable-derived fluids.
“There’s always a need for innovation, whether to improve fire resistance, extend fluid life, reduce wear or prevent varnish build-up,” Goldstein says. “Further, there’s always a push to reliably produce the most cost-effective fluid once chemistry is proven. As long as there are changes in the way operators run and OEMs design their equipment, there will be a need for innovation.”
LeBarge says that while FRF research isn’t at the forefront at KOST USA, it’s not at a standstill either. “We continue to develop our fluids, but due to the competitive nature of larger volume FRFs the return on investment on a product modification must be evaluated. The cost of obtaining FM-approval registration of a new or slightly modified formula is greater than $20,000 per product, and this is just for FM. This does not include third-party pump testing or field trials to qualify the performance of the product.”
As FRF regulations continue to tighten and lubricants continue to operate under harsher conditions with no single fluid technology offering affordability and all-round performance, there is an opportunity for the industry to reinvent FRFs beyond what’s in use today.
WHAT CAUSES HYDRAULIC FLUID TO ESCAPE? (10)
High-pressure pipe with welded and screwed joints, steel and copper tubing, and metal-reinforced rubber hose are used to distribute hydraulic fluid at pressures as high as 10,000 psi. Failure of piping, particularly at the threaded sections, failure of valves and gaskets or fittings, pulling out of copper and steel tubing from fittings, and rupture of flexible hose are the principal causes of oil releases from systems. Repeated flexing and abrasion of rubber hoses against other hoses or machine parts can create weak spots, which eventually result in rupture. Lack of adequate supports or anchors that lead to vibration or movement of piping has been a factor in some of these failures. Also, tubing under pressure can release oil when accidentally cut by welding torches or other equipment.
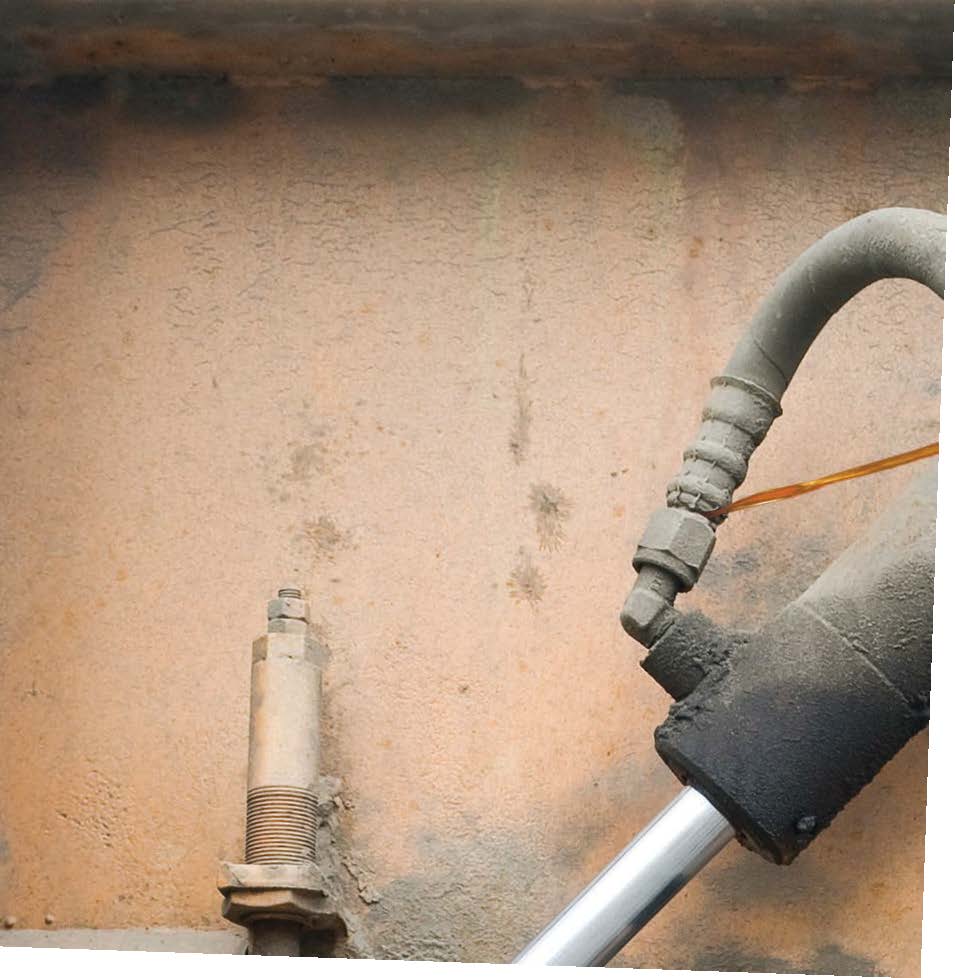
REFERENCES
1. Research suggests that anhydrous fumes may not be as toxic as fumes from other FRFs.
2. FRFs as a group generally have a very low toxicity, so this advantage is debatable.
3. From here.
4. From here.
5. FM Global conducts property loss prevention research to optimize its international commercial and industrial property insurance, underwriting and risk management products and services.
6. The fire point is the lowest temperature at which a fluid’s vapors will sustain combustion once ignited.
7. From here.
8. From here.
9. ISO 12922:2012, which replaces ISO 12922: 2002, specifies the minimum requirements of unused fire resistant and less-flammable hydraulic fluids for hydrostatic and hydrodynamic systems in general industrial applications. It provides guidance for suppliers and end-users of these fluids and to OEMs of the hydraulic equipment in which they are used. It does not apply to aerospace or power-generation applications, which have different requirements.
10. From here.
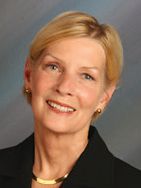
Jean Van Rensselar heads her own communications firm, Smart PR Communications, in Naperville, Ill. You can reach her at jean@smartprcommunications.com.