Polyalkylene glycols: Present and future applications
Dr. Martin R. Greaves | TLT Webinars June 2013
60 years after their introduction, these unique lubricants are being used in new applications.
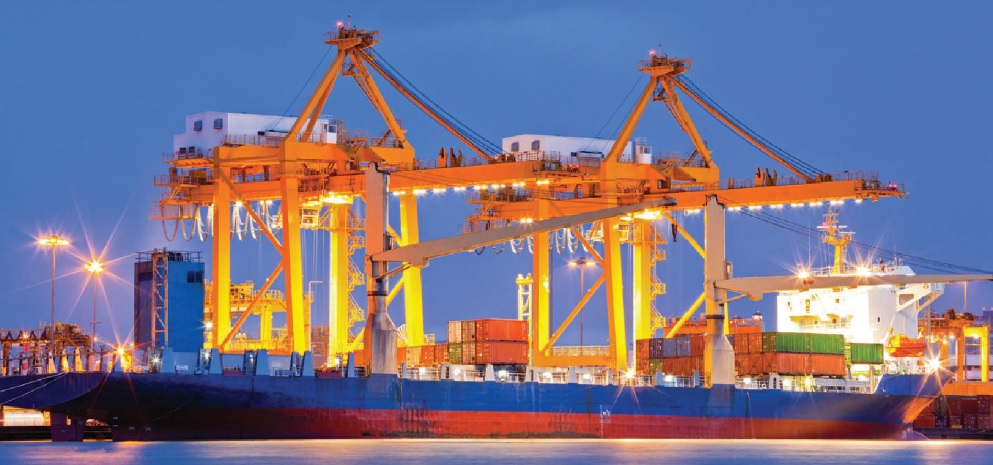
www.canstockphoto.com
KEY CONCEPTS
•
PAGs are commonly used as viscosity builders in fire-resistant, water-glycol hydraulic fluids, as well as friction reducers in synthetic water-based MWFs.
•
A major advantage of PAGs is they rarely form deposits during ageing in contrast to some hydrocarbon oils.
•
There are several practical benefits of using oil-soluble PAGs as performance additives in hydrocarbon lubricants.
MEET THE PRESENTER
This article is based on a Webinar originally presented by STLE University. In some cases, the Webinar presenter will author the article, like this one, and in others, the Webinar is adapted by a TLT writer.
STLE-member Dr. Martin Greaves is research leader for Dow Europe GmbH in Horgen, Switzerland. He serves as a technical editor for TLT and is an instructor for STLE’s Synthetic Lubricants education course. You can reach Martin at
mrgreaves@dow.com.
STLE University has sponsored dozens of Webinars and podcasts on a wide range of technical topics. To see Martin Greaves’ Webinar in its entirety, review all STLE University offerings and view the lineup of future events, log on to
www.stle.org. Webinars are $39 to STLE members and $59 for non-members.
Dr. Martin R. Greaves
POLYALKYLENE GLYCOLS (PAGs) ARE A VERSATILE FAMILY OF POLYMERS that continue to solve lubrication problems that hydrocarbon oils cannot. Although PAGs were invented over 60 years ago, the innovation of these polymers remains strong as our industry continues to look for new materials to solve modern tribology challenges. Two key areas of innovation are (1.) application development using conventional PAGs and (2.) the design of new polymers.
This article, based on a September 2012 Webinar presentation sponsored by STLE University, provides a brief overview of some of the traditional applications of PAGs and discusses some of their unique features in bringing new solutions to modern equipment challenges. We’ll also look at the emergence of new polymers (for example, oil-soluble PAGs (OSP)) and how these offer formulators an additional tool to upgrade their hydrocarbon-based lubricants.
CONVENTIONAL PAGs
Most PAGs in use today are manufactured from downstream derivatives of ethylene oxide (EO) and/or propylene oxide (PO). Simplistically these oxides can be grafted onto an initiator, typically an alcohol, to form homopolymers or copolymers such as random, block or reverse block structures (
see Figure 1). These three variables of initiator, EO and PO can lead to a vast number of polymer architectures with differing rheology and tribology behavior. Indeed, there are at least 100 different polymer chemistries that find use in lubricant compositions. The most common are random copolymers (EO/PO). These are sometimes described as water-soluble PAGs. In contrast, the polymers derived from propylene oxide are often referred to as water-insoluble PAGs.
Figure 1. Typical synthesis of a variety of PAGs.
WATER SOLUBILITY
A unique property of random copolymers is their water solubility. This has led to their use as performance additives in water-based synthetic lubricants. PAGs are commonly used as viscosity builders in fire-resistant, water-glycol hydraulic fluids, as well as friction reducers in synthetic water-based metalworking fluids. In some metal cutting operations, wear and friction at the interface of the cutting tool and metal substrate can be significantly reduced by taking advantage of the inverse solubility properties of PAGs. At this interface, significant heat is generated resulting in the PAG “clouding” out of solution and coating the interface with a polymeric film that provides a lubricating cushion between the contacting surfaces.
FRICTION CONTROL
A common use of PAGs, particularly in Europe, is in industrial worm gears. PAG copolymers, derived from a high level of EO, offer excellent friction control, leading to prominent energy efficiency benefits over hydrocarbon lubricants. Modern tribology tools are helping researchers understand friction behavior of PAGs and how differing polymer architectures can influence further optimization. Figure 2 compares an ISOVG-320 PAG gear oil with a PAO gear oil in a simple mini-traction machine experiment that measures traction under different sliding and rolling ratios.
Figure 2. ISOVG-320 PAO (red) and PAG (blue) industrial gear oils. Traction measured using a mini-traction machine at 75 C, 1.2 GPa and speed = 1m/sec.
Significantly lower traction values are observed for the PAG. Recent research looking at pressure-viscosity coefficients and calculating film thickness values also suggests PAGs form much thicker elastohydrodynamic films under high contact pressures and temperatures, which may help extend gear life, especially in high-temperature and high-load gear systems.
DEPOSIT CONTROL
A further important property of conventional PAGs is their deposit control benefits, which is best illustrated with PAG rotary screw air compressor fluids. This application represents a severe test for any lubricant. The fluid will experience high temperatures and significant aeration, which can accelerate the ageing process.
A major advantage of PAGs is they rarely form deposits during ageing in contrast to some hydrocarbon oils. Therefore, fluid change intervals for PAGs are several times longer. The primary reason for this is probably that the oxidation of PAGs yields shorter chain polar compounds, which are soluble in their parent polar base oil. In contrast, hydrocarbon oils can form higher molecular weight oxidation byproducts, which are more polar than their parent base oil, leading to deposits on surfaces and the risk of varnish formation.
A new application for PAGs that utilizes this concept is synthetic gas turbine oils. Many gas turbines use traditional API Group II or III hydrocarbon oils, and some have experienced excess varnish buildup leading to turbine equipment failures. This led to the search for technologies that minimize the risk of deposit formation. The experience gained from using PAGs for more than 20 years in rotary screw air compressors was leveraged, and today there are gas turbines that have operated successfully using PAGs for five years.
The ability of PAGs to help control deposits can be used in other severe applications. For example, the hydraulics of tunnel boring equipment can operate under extreme temperatures. But one unique property of these PAG fluids relates to their environmental benefits. If leaks occur, lubricants can find their way into waterways, which presents a pollution hazard. Since PAGs are water-soluble, they are also non-sheening and, therefore, very different than petroleum oils. Nonsheening behavior combined with biodegradability makes them an excellent choice for specialty fluids for the marine industry and around waterways where there may be environmental concerns due to lubricant loss.
PRACTICAL CHALLENGES
Conventional PAGs do have some practical challenges. For example, since they are not oil soluble, converting equipment from a hydrocarbon oil to a PAG lubricant requires care to avoid excess contamination. Since PAGs are polar, care in the correct choice of some seals and elastomers is needed. Finally, PAGs are more hygroscopic than hydrocarbon oils, and this is perceived as a disadvantage and a potential corrosion risk. In practice PAGs operate very successfully at higher water levels than petroleum oils. When moisture ingress occurs, PAGs act like polymeric sponges—binding the water within their structure and rendering it inert.
Researchers have continued to explore the development of new PAGs that retain the benefits of conventional PAGs such as high viscosity indices, good low temperature properties, good friction and deposit control, which are also oil-soluble. This has led to the recent development and commercialization of oil-soluble PAGs (OSPs).
NOVEL OIL-SOLUBLE PAGs
There were several attempts at developing oil-soluble PAGs from some of the synthetic base oil producers. Unique oxides were used that, in practice, were not available on an industrial scale. One key building block that is available is 1,2-butylene oxide and downstream derivatives of this, with other precursors, can led to unique polymers that offer many of the traditional benefits of conventional PAGs, but offer improvements and allow them to be used as components of hydrocarbon oil formulations. Figure 3 provides a simple diagram that illustrates the comparison between conventional PAGs and OSPs. In addition, Table 1 provides some of the typical property data of a select range of OSPs.
Figure 3. Spider diagram that generically compares conventional PAGs and OSPs.
Table 1. Typical Properties of Some Select Oil-soluble PAG Base Oils
Simplistically, Figure 3 illustrates several notable aspects. First, OSPs offer significantly improved oil solubility over conventional PAGs. Solubility behavior in most API Group I-IV base oils is good. The products are also less hygroscopic and offer better compatibility with elastomers such as low nitrile acrylonitrile butadiene types. The polymers have higher viscosity indices compared to hydrocarbon base oils and are typically in the 145-200 range. Many have good low temperature properties with their pour points being less than -50 C.
Interestingly, like conventional PAGs, some OSPs are readily biodegradable while others are bioresistant. This is a function of their polymer architecture and molecular weight. Like conventional PAGs, OSPs show mild antiwear activity since every third atom along the polymer backbone is oxygen, which provides surface activity. Research also has shown that the materials offer similar oxidation stability and deposit control benefits as conventional PAGs.
There are a number of practical benefits that OSPs can offer when used as performance additives in hydrocarbon lubricants. One of these is to help control deposits. Figure 4 shows a visual example of this concept. A Group II hydrocarbon compressor oil containing an OSP (10 percent) was examined in an oxidation ageing experiment using a modified ASTM D2893B test over a two-month period. Without the OSP, there is significant visual evidence of deposit formation. However, when the OSP is included it helps to control deposits and a translucent fluid is evident. The polar OSP probably functions by solubilization of the oxidation byproducts of the hydrocarbon oil.
Figure 4. Group II compressor oil (shown on the left) and the same with 10 percent OSP addition (shown on the right) visually showing fresh fluid and aged fluid after two months of oxidation testing using a modified ASTM D2893B test.
Some OEMs continue to tighten their specifications for deposit control in areas such as engine oils, turbine fluids and compressor fluids. The inclusion of an OSP to hydrocarbon oils may provide a helpful tool in bringing new solutions to tighter OEM specifications.
A further example is their friction control behavior in hydrocarbon oils. Figure 5 shows an example of the improvement in boundary friction in a mini-traction machine experiment when an OSP is added at 1 percent to a Group III base oil, especially at slow speeds. This feature provides a further option for formulators to consider using OSPs as friction reducers if improved energy-efficient lubricants are desired.
Figure 5. Group III base oil (red) and Group III base oil with 1 percent OSP measuring friction using a MTM at 40 C, 0.9GPa and 30 percent slide roll ratio.
OSPs have very low aniline points (typically -30 C). This parameter is a measure of the polarity and solvency power of a material. Low values (e.g., <50 C) indicate high polarity. Modern API Group II and III hydrocarbon base oils and polyalphaolefins typically have high aniline points (e.g., 100 C and higher) and usually higher than Group I base oils, which contain a degree of aromaticity. This presents a challenge to formulators of Group IIIV oils that wish to use polar additives to boost performance, as these are sometimes not soluble.
Polar materials such as synthetic esters have lower aniline points (e.g., 10 C-50 C) and are often used as blend components to add back some solvency. In some environments, esters are known to be hydrolytically unstable. OSPs present the formulator with another option but remove concerns with hydrolytic stability.
OSPs also have some practical benefits if used as primary base oils in fully synthetic industrial oils such as gear and hydraulic fluids. For example, formulations can show exceptionally fast air release. Table 2 shows air release times for a range of hydrocarbon and synthetic gear oils. Air entrainment is air that has been dispersed in the oil in the form of very small bubbles. In equipment where the residence time of the fluid is short in the sump, the air bubbles may not be released fast enough and, therefore, travel through the equipment, leading to problems such as cavitation, vibration, increased oil oxidation and micro-dieseling. Fluids with low air release values are highly desired. Furthermore, fluids with fast air release times may allow smaller gear or hydraulic systems to be designed and result in lower capital costs to manufacture them.
Table 2. Air Release Times for Commercially Available Industrial Gear Oils
Although PAGs have been known for over 60 years, innovation continues as solutions to modern tribology and equipment challenges are developed.