Complexity in Oil Analysis: Part X
Jack Poley | TLT On Condition Monitoring May 2013
How real-time oil analysis creates synergy with other condition monitoring tools.
I CONFESS TO BEING BIASED TOWARD OIL ANALYSIS (OA) as the most comprehensive condition monitoring tool in the toolbox. Belaboring the point in this article, the reason I favor OA as the first CM tool of machinery defense is because oil analysis deals in precursors to failure, rather than the imminence of failure, while still possessing the ability to greatly assist in spotting the onset of abnormal wear or failure.
This is a critical notion and a particular way of thinking. It is the essence of preventive maintenance. The question might be posed: At what level of trauma should prevention begin? Not an easy question, because the answer depends on the economics, application and logistics of each group of monitored machines.
Lubricant failure of one sort or another is often the pre-existing cause of excessive wear in machinery such that the machine cannot perform its function adequately or at all. If this is true more often than not, as many posit, and by some significant margin, as many also claim, then it makes oil analysis near essential for the purpose of assessing in-service lube quality and efficacy.
Vibration signature analysis (VIB) simply cannot perform this type of function at root level. For this reason, VIB usually lags oil analysis time-wise in terms of alerts to potential machine trauma, particularly when the lubricant’s efficacy is under siege (see Figure 1).
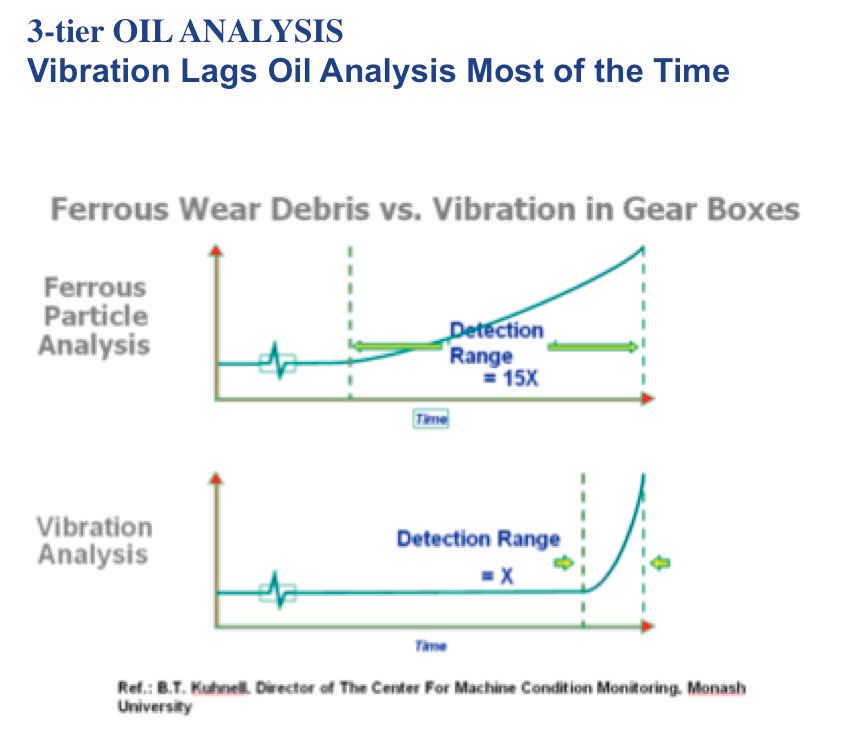
Figure 1.
Suppose, for example’s sake, that we regard oil analysis’s CM partner, vibration analysis, as a competitive CM tool. Each has its strengths and each scores condition monitoring victories by providing early warning of impending trauma. VIB can spot misalignment and imbalance immediately while oil analysis is of no help in such instances. Nevertheless it has been well established that VIB is not very forthcoming with respect to detecting lubricant compromise until sufficient displacement (wear) has occurred. So it is reasonable to state that a compromised lubricant is an event type in the domain of OA. The implication is that maintaining serviceable lube in the machine forestalls wear events much of the time.
Why not just change the lube “like we used to do?” The quick answer is obvious: waste and expense. Oil is not cheap anymore, nor is environmental conservation. Moreover it’s simply bad business. But it’s not really about changing oil.
Oil analysis reveals a variety of typical problems that can occur, including coolant seepage, fuel dilution, water, soot, additive depletion, premature oxidation and thickening. This is straightforward, surely, but what is really important is to get at the root cause of the lube’s trauma. Sometimes it will simply be that the lube has run its course and should be changed accordingly.
However, when that is not the case, and the lube is traumatized well in advance of a typically expected in-service time interval, something’s likely amiss, and it’s likely fixable. That’s straightforward, too. But what’s really happening is that VIB is going to have its victory forestalled or even snatched away and, because we’ve put the two CM disciplines in the role of competitors, that’s a victory for OA. It’s also a victory for the maintenance budget’s wallet and the corporation’s product output. Paraphrasing the late Sen. Everett Dirksen, “A few victories here, a few victories there, pretty soon it adds up to a lot of money.”
Are the two disciplines really at odds? No, but today’s economic climate really shouts out for taking all the money off the table one can, so it makes sense to combine CM monitoring techniques to best advantage for maintenance cost savings and maximized production.
Well, then, why did I put the two disciplines at odds? Because that’s how they often are seen. One is favored over the other to the point where the other is used half-heartedly or eschewed altogether.
In the 1970s VIB won a huge following in the industrial world where durables manufacturing occurred and where hundreds and occasionally thousands of gear sets were being live monitored in real-time. OA couldn’t compete but, sadly, could have contributed to reduced VIB alerts, thereby reducing failures. Over the last 30 years, a huge number of plants have adopted OA in partnership with VIB. When that occurs, isn’t everything now in order? Despite best intentions, many times it is not. What’s missing?
What is not done much is to combine VIB output with OA and co-evaluate the data, often because there are different personnel, even departments, involved in executing each technique and also because the significance of finding pre-wear trauma within an oil sample doesn’t always gain the traction it should. And let’s hear it for simplicity: VIB is a well-established technique where certain frequencies and periods indicate very specific event occurrences. In other words, there is a lot of “go-no go” in VIB (such as an absolute inspection limit in many substantiated cases).
Not always with OA. Lots of data, imperfect numbers at times due to contamination interference and so forth, make life with OA difficult at times. Most of us prefer go-no go when it will suffice. This is the dirty little secret that is still OA. It’s not as cut and dried as one would prefer, it’s not often go-no go and, while it’s getting more powerful, it’s also getting more complex in its own right.
Nonetheless, with real-time OA sensors in play (Tier 1), and increasing gains and versatility in VIB technology vis-à-vis acoustic signature monitoring, there is more opportunity than ever to approach CM holistically. OA is indeed more powerful than it has ever been at this juncture, but it is still a subset of condition monitoring. Other disciplines need to be in the evaluation mix, utilizing appropriate software support for the myriad possibilities in today’s systems and lubes.
We’ll look at some of the logical algorithms next time.

Jack Poley is managing partner of Condition Monitoring International (CMI), Miami, consultants in fluid analysis. You can reach him at jpoley@conditionmonitoringintl.com. For more information about CMI, visit www.conditionmonitoringintl.com.