Please describe the lubrication and wear issues involved with natural gas engines.
TLT Sounding Board April 2013
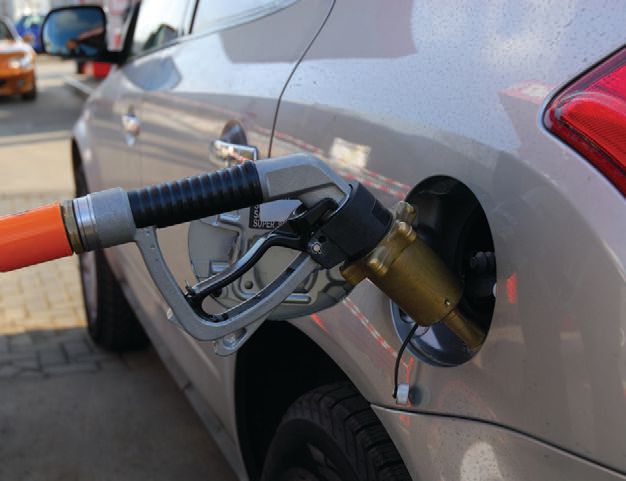
www.canstockphoto.com
Natural gas engines pose unique problems for the lubrication professional, and many TLT readers responded to this month’s questions by citing issues relating to alkalinity, viscosity, oxidation, acid number and nitration. Valves and bearings were the components most mentioned. Switching to low-ash lubricants, synthetics and Group II lubes were offered as possible solutions.
There will be no such issues for natural gas engines but for other parts.
Lubricant does not build up the proper valve recession.
Fouling valves due to nitration levels. Valve recession—use the correct ash content oil per OEM.
Gas as fuel is very dry, and I think that’s the cause of premature wear.
Deposits on the valve deck from oxidized and nitrated oil. Use oil with more robust performance and shorten oil drain intervals.
Mostly concerned about drop in alkalinity, viscosity drop, oxidation, acid number and nitration. Sometimes it requires matching the gas type with the lubricant without much information about either. Ash levels are also important, as some oils have low Base Number (BN) and low ash, while others have higher BN and low ash, and that can be confusing.
The main issues the industry faces with natural gas engines are oxidation and nitration due to current lean burn technology.
High viscosity index and good friction efficiency.
Ash pounding, premature valve wear. Solution: Monitor engine ash, move to lower ash or no-ash lubricant for two or more oil changes.
Usually researchers focus on the hydrogen embrittlement, but wherever there is sliding in the presence of hydrogen there is a combination of surface phenomenon between sliding and reduction, especially in steels. One solution is to use self-lubricating materials like PTFE, PEEK and their composites.
Corrosive materials at the inlet for engines running biogas. Buffering helps, but rebuilding is still more often than with diesel.
Years ago I worked on deposit formation problems and formulation of low-ash engine oil for gas engines.
The acidity of landfill gas has been a challenge. Unfortunately, we’ve solved these problems in an ad-hoc manner.
The one issue I have dealt with was soot and varnish. The engine wasn’t being operated in the proper temperature range (it was running too hot). Once the operator understood what needed to be changed, operation improved and it was no longer an issue.
The NGEO lubricant industry is a difficult proposition. Engine type and fuel supply drive recommendations. Gas analysis is a must if lubrication is to be optimized. Another issue is the cost to serve versus the competitive pricing in the field. Price competition is severe and margins slim. Players come and go.
Accessible combustion chamber deposits, leading to increased wear, high acidity and corrosion issues.
Adhesive wears caused by high loading of the gas engine to 90%-95% of engine load capacity. We cut short the ODI by 50% and advised the company to procure additional gas engine generators, which they have done now.
Due to the wide variety of engine applications (slow speed, high speed, low emission, rich burn) and fuel quality (dry, wet, methane number), along with oil type varieties (ash levels, base oil groups), choosing the right oil for a production area and engine type can make a difference in oil usage and engine life. Once chosen, keeping the oil pure can be challenging if not handled properly. Comparing samples from bulk retain, on-site storage tank and engine for a given machine have yielded information that led to determining contamination due to improper handling of oil and how to correct.
Corrosion and cleanliness.
Wear of intake valve insert due to lack of presence of any liquid.
Longer extended, oil-service life. Switched to an oil formulated with Group II base oils and special additive treatment.
Good quality engine oil designed for dry fuel use.
There are lubrication and wear issues because design features of the engines vary. Not all the fuel is the same, and operating conditions/climate can vary and affect the engines. Lubrication failure caused wear and wear particles in oil. We went to a synthetic and received much better lubrication.
Short drain intervals, valves, bearings, piston ring/liner. Many times updating the drain interval based on oil analysis and upgrading to higher quality oil with proper maintenance clears it up.
Lubrication issues: Oxidation and nitration of the oil are common with natural gas engines. Wear Issues: Exhaust valve recession and torching (guttering) are major issues with natural gas engines.
The main problem with industrial natural gas engines is not lubrication but fuel. Typically, natural gas is poorly filtered and barely separate from water. Water naturally carries minerals. Water is also a very poor top-end lubricant. Water fouls spark plugs and causes premature ring and bore wear. The addition of methanol in small amounts should help mitigate the effect of water in the fuel. In the case of a Cooper B-250, the demand for fuel is of such volume that it is difficult to find adequate filtration. I have yet to see a system that functions reliably consistently and adequately while allowing sufficient flow. Most operations are struggling to maintain production, and it is next to impossible to get anyone to spend money on new equipment, even if it is to keep old equipment running more reliably. I have never been in a position where I was allowed to experiment with my ideas, so it is hard to say what would solve such issues without creating new ones.
Due to hotter (than diesel, for example) burning of gaseous fuel, the oxidation and nitration effect on engine oil is more severe. Exhaust valve recession, sludge and varnish formation can be caused by insufficient ash level of lubricant. Effective and balanced additive package with the necessary ash (low or medium) content provides valve protection and acid neutralization characteristics.
High bearing wear rates due to high siloxane levels in the gas.
Bearing wear becomes evident when the base number falls below the level of the acid number. This can be used to set extended drain intervals.
Ring and cylinder wear. In a bus fleet, the operator reported the oil was darkening and they were “losing” bearings. In fact, they were burning engine oil, making soot and accelerating bearing wear. Oil analysis identified the root cause.
Wear of the cylinder head valve seats.
Editor’s Note: Sounding Board is based on an e-mail survey of 13,000 TLT readers. Views expressed are those of the respondents and do not reflect the opinions of the Society of Tribologists and Lubrication Engineers. STLE does not vouch for the technical accuracy of opinions expressed in Sounding Board, nor does inclusion of a comment represent an endorsement of the technology by STLE.