Tribology and metal cutting
R. David Whitby | TLT Worldwide March 2013
Several processes are available to reduce energy and increase tool life.
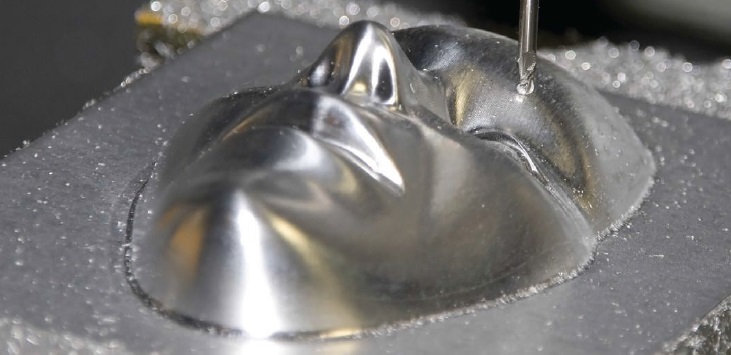
www.canstockphoto.com
METALWORKING CONSISTS OF TWO BASIC PROCESSES: metal removal (cutting) and metal deformation. Metal cutting has been considered as a plastic deformation process on a submicronic scale and occurs just before chip fracture, while metalworking fluids help to optimize metalworking processes.
With metal cutting, tribology is often regarded as something employed to reduce the tool wear, thus increasing tool life. Although this is generally true, greater application of tribological knowledge in metal cutting is possible. Many publications do not treat metal- cutting tribology in a systematic way. Instead, there is a collection of non-correlated facts on tool materials, tool geometry, cutting regimes, tool life and its assessment, cutting fluids, tool coatings and other factors.
The ultimate objective of metal-cutting tribology is to reduce the energy used. Increased tool life, improved integrity of the machined surface, higher process efficiency and stability can help achieve this goal.
A cutting tool should be designed to take maximum advantage of the forces that the machine applies through either the tool or the workpiece. The cutting action in a machine tool is not the same as that of a knife. A cutting tool is relatively blunt and is only able to cut because of the large forces applied.
For example, the total force involved in a single-point turning operation can be divided into three components: tangential, axial and radial. Tangential force, the largest of the three, is usually used in calculations of power consumption. This force tends to deflect the tool vertically. If the torque applied to the machine fluctuates, the tangential force also fluctuates, setting up tool vibrations that cause chatter marks, thus spoiling machined surface finish and dimensional accuracy.
The mechanical properties of the workpiece material affect the cutting operation. These properties include shear strength, work-hardenability, hardness and abrasiveness. Reductions in shear strength, coefficient of friction, hardness, strain-hardenability and abrasive inclusions all contribute to improved tool life. Lowering shear strength, hardness or abrasive inclusions has no effect on surface finish, which is usually improved by reducing the coefficient of friction or strain-hardenability.
Material is removed from the workpiece by shearing action, which forms a chip of metal. Chips can be discontinuous, simple continuous or continuous with built-up edge. Machined metals include carbon, alloy and stainless steels, cast-iron, aluminium and aluminium alloys, copper alloys, nickel and nickel alloys and titanium alloys.
Many cutting processes exist. Grinding is high-speed, multipoint cutting, which generates much heat but does not involve large forces. Honing and lapping are variations of grinding. Sawing, drilling, turning and milling require more force for which lubrication reduces energy requirements and improves surface finish and tool life. Boring and tapping are variants of drilling. Gear hobbing, gear shaping and broaching are heavy-duty processes that require large forces in which effective lubrication is critical.
The tribology of metal cutting is entirely different from the tribology applied to operating equipment. In the latter, a process designer is limited by the shape of the contacting surfaces, materials used, working conditions set by the operating requirements and the use of suitable lubricants. In metal cutting, practically any parameters of the cutting system can be varied in a wide range.
Modern machine tools do not limit the designer in his selection of cutting speeds, feeds or depth of cut. There is a wide range of available tool materials, cutting insert geometries and tool-holders. The selection of cooling and lubricating media and their application methods are practically unlimited. Although the designer normally sets the chemical composition of the workpiece material, the properties of this material can be altered over a wide range by heat treatment, forging and casting conditions.
The main problem in the selection of optimum cutting parameters is knowledge of metal-cutting tribology. The study and optimization of the tribological conditions during the numerous alternative metal-cutting processes has great potential to reduce the energy used in cutting, increase tool life, improve dimensional accuracy, reduce waste material and optimize the use of cutting fluids.
David Whitby is chief executive of Pathmaster Marketing Ltd. in Surrey, England. You can reach him at pathmaster.marketing@yahoo.co.uk.