What is the biggest misconception you’ve come across regarding oil analysis?
TLT Sounding Board March 2013
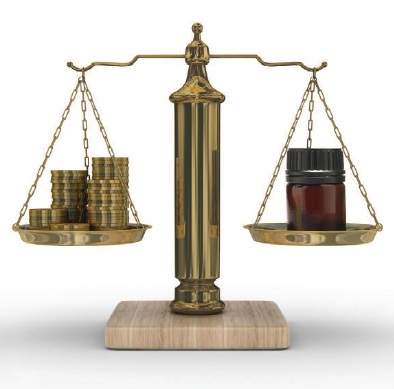
www.canstockphoto.com
Oil analysis (OA) certainly ranks as one of the more misunderstood areas of lubrication engineering among end-users. TLT readers responding to this month’s survey say the No. 1 misconception they see in their jobs is the notion that one sample is all that is needed to answer all questions. Experienced lubrication professionals know that it is trend information that tells the greater tale about how a machine is performing. Many end-users also continue to see OA as an unnecessary expense rather than an effective preventive maintenance program that can save time and money and reduce expensive downtime. And far too many think OA is something to do after the machine or component fails. Finally, according to several survey respondents, the TV show CSI has not been a positive educator when it comes to oil analysis.
Tough question because how a sample is pulled directly impacts accuracy. It can also be that the lab running the sample does not understand the chemistry of the sample and gives false readings. Results can be skewed if a slight bit of water ingresses into a fluid sample and the tester is using a laser particle counter.
That OA can predict every equipment failure in a timely manner. Sometimes things just break.
That many method developers consider oils to be water soluble! Especially in the respect of biodegradation analysis.
All oil is the same. Same color, same oil.
How often it needs to be done.
That it will save you money.
That it won’t save you money.
That FTIR reading of used oil to determine oxidation and nitration level is sufficient without comparison to new oil.
That an individual reading means something. Trends are what matter.
Why don’t I see wear metals in my analysis when I find large particles during physical inspections?
That problems are only found
after damage has already occurred in a component.
That there is no need to do it. It is a waste of money. It will not tell you anything.
Misunderstandings abound regarding proper sampling procedures.
The biggest misconception I’ve heard is that oil analysis is not useful when there are no current problems. Predictive maintenance is key to minimizing downtime, and oil analysis can be one of the biggest assets in predictive maintenance.
That one test will give you a ton of information where in reality you have to do many tests to develop a trend. Also people expecting CSI TV show-type results with one simple test.
That oil analysis data will tell the equipment operator everything about the condition of the equipment. Oil analysis should be combined with vibration analysis, thermography, etc., to get a more complete picture.
It doesn’t have thermoxidative properties.
That it doesn’t provide any value or the lab doesn’t provide enough information/action items.
Overheard: “I put drill cutting shards into my engine oil sample to see if they would show up on the report and they didn’t. Oil sampling doesn’t work.”
That there is no added value to it.
That it’s not cost effective.
New oil is clean oil.
That it’s time-consuming and not very useful.
That oil analysis can replace normal maintenance.
That it is the be-all and end-all and you don’t have to do anything else.
That oil analysis is required after the problem or failure is observed in the machinery and equipment.
Assuming that one analysis gives a clear picture of what happened to the equipment.
It’s a waste of time and doesn’t have any value. Salespeople only use it as a scare tactic.
That oil analysis is guaranteed to diagnose a sudden failure in advance.
That quick, simple and routine testing will reveal all potential problems.
That the way to attack any problem is to just change the oil.
That Total Acid Number (TAN) can always effectively measure or correlate to varnish potential.
That analysis of one oil sample from an engine tells you exactly what is wrong with it.
End-users assume that all oil testing laboratories provide the same quality results.
That a standard oil analysis can identify with certainty the specific product (brand, etc.).
That oil analysis is not necessary or is only needed when something goes wrong (failure of lube and/or machinery).
Viscosity is a sufficient indicator of oil quality.
That additive depletion can be monitored by trending the zinc and phosphorus concentration in emission spectroscopy.
That data is equivalent to knowledge.
Not really a misconception but more of a problem. Maintenance managers do not train their mechanics to pull samples properly. Sometimes the samples get pulled properly and sometimes they do not. Makes a huge difference with the OA.
That you can establish absolute condemning limits on lubricant samples. Condemning of the lubricant always should be done on a trending basis and take into account the specifics of the particular application.
Don’t need to do it, just change the fluid instead.
That the only way to have an effective OA program is to have a lab, that it can’t be done in the field.
That there are only certain aspects of the oil analysis process that are vital or necessary. Meaningful oil analysis includes the sampling procedure, lab techniques, meaningful tests, among others.
All oils are the same.
That oil analysis solves all problems. It is an indicator of the condition of the oil and provides insight into the health of the machine.
Editor’s Note: Sounding Board is based on an e-mail survey of 13,000 TLT readers. Views expressed are those of the respondents and do not reflect the opinions of the Society of Tribologists and Lubrication Engineers. STLE does not vouch for the technical accuracy of opinions expressed in Sounding Board, nor does inclusion of a comment represent an endorsement of the technology by STLE.