GHS: New challenges for the lubricant & metalworking fluids industries
Neil Canter, Contributing Editor | TLT Feature Article March 2013
A global uniform standard is redefining the way companies provide health and safety information on chemical substances.
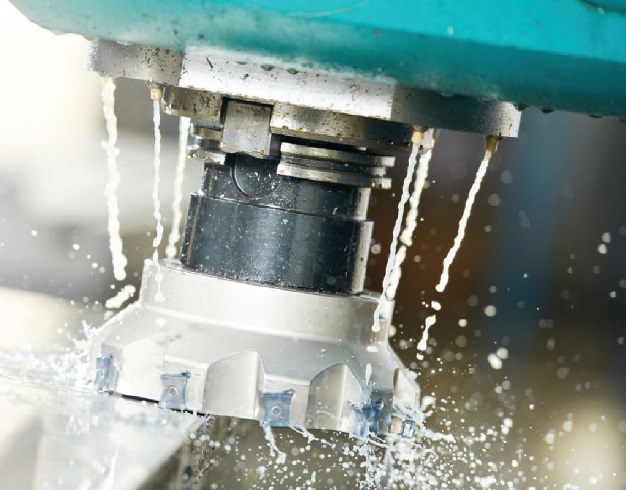
www.canstockphoto.com
KEY CONCEPTS
•
The Global Harmonized Standard of Classification and Labeling of Chemicals creates a uniform standard for providing health and safety information.
•
GHS involves the use of a new format for safety data sheets and new product labels. Regional differences will apply.
•
Lubricant formulators will need to gain a strong understanding of the regulation to ensure that the transition to GHS is done as smoothly as possible.
COMPLYING WITH HEALTH AND SAFETY REGULATIONS has presented enormous challenges for the lubricants industry such as preparing material-safety data sheets (MSDSs), product labels and answering questions about specific concerns from end-users.
To make things even more complicated, different regions of the world have developed different formats and regulations addressing these health and safety matters. For example, a MSDS in the U.S. is formatted differently than one in Canada and in the European Union.
In addition, each country or region may evaluate a specific chemical substance in a different fashion. An example showing how a specific chemical substance is evaluated by 10 countries and the EU is shown in Figure 1. This unnamed substance has at least four ratings, ranging from non-toxic to toxic.
Figure 1. This slide from a representative of the European Association of Chemical Distributors shows how one chemical substance is evaluated by 10 countries and the EU. This example helps to justify the need for GHS. (Courtesy of C.S.B. GmbH)
Also adding to the complexity of the situation is the process that needs to be used for developing MSDSs and product labels for lubricants, which are mixtures of various basestocks and additives. In particular, metalworking fluids (MWFs) can be extremely complicated to deal with because they are prepared from a diverse number of additives.
As today’s economy has become more global with lubricant companies shipping products to many different geographical markets, there is increased pressure to develop a standard, uniform format for providing health and safety information on specific chemical substances and on mixtures such as lubricants.
The initial efforts to develop a uniform standard were proposed by the United Nations in 1992 at the UN Conference on Environment and Development. Approval took place in 2002, and the regulation is known as the Global Harmonized Standard of Classification and Labeling of Chemicals or GHS (
1).
The five main purposes of GHS include:
1.
Enhance protection of human health and the environment.
2.
Bridge the differences among the systems implemented in the developed world (Canada, EU and U.S.).
3.
Develop a framework that can be used by those countries without a system (developing world).
4.
Reduce the need for testing and evaluation of chemicals.
5.
Facilitate international trade.
To date, some regions of the world have adopted the GHS. Those include the EU, Japan, Malaysia, New Zealand and Singapore. Two of the more important geographical markets are on the verge of implementing GHS. Brazil plans to do so at this time, while China is ready to adopt GHS but has not implemented it at this point.
With the world moving toward a uniform standard, the U.S. Government announced in March 2012, through OSHA, that it will adopt GHS by updating the Hazard Communication Standard (
2). The update is known as HazCom 2012, with final implementation to be done by all lubricant suppliers by June 1, 2015.
The implementation of GHS will lead to a change in the format for preparing regulatory information. Information on the health and safety of specific chemical substances and mixtures will change, and new labels will be introduced.
While these changes will undoubtedly lead to confusion, the purpose of this article is to describe the basics of GHS, provide information on the timetable for its implementation and gain the perspective of experts from the chemical and lubricants industries, U.S. Government and the EU, as well as representatives from MWF producers, about what to look out for when switching over to GHS. In addition, concerns and needs expressed by the MWF producers are addressed in this article with regard to the process.
To seek a broad range of opinions, TLT interviewed the following individuals:
•
David Morrison, HSE specialist, Castrol Industrial North America.
•
Dr. Eugene White, EHS manager, CIMCOOL Global Industrial Fluids.
•
Heinz Dobbertin, managing director, C.S.B. GmbH.
•
Tim Cawley, product sustainability leader, The Dow Chemical Co.
•
Dr. John Howell, vice president, GHS Resources, Inc.
•
Dr. Richard Kraska, president, GHS Resources, Inc.
•
An OSHA spokesperson who granted the interview provided it was conducted on a confidential basis.
BASICS
The first thing to note in moving to GHS is that the format for the MSDS changes. In fact, the document will be known as a safety data sheet (SDS). Figure 2 shows the differences between a format commonly used now and the new GHS format. There are 16 sections in the new format as compared to 8-10 sections that are most commonly used at present. Most of the same sections are included, though they are organized in a different fashion. The four new sections are listed in blue font.
Figure 2. The GHS format for SDS is different than what is generally used at the present time. New sections to be included are shown in blue font. (Courtesy of Chemical Solutions)
For the SDS, each of the sections must be written in order from Section One (Identification) through Section 16 (Other). But note that the ecological, disposal, transport and regulatory information sections are not required.
Other elements included on the SDS and the product labels are pictograms, signal words, hazard statement and a precautionary statement. Each pictogram represents at least one hazard class. Appendix C of HazCom 2012 provides a full description of these hazard classes and the mandatory language that must be used with them. Figure 3 taken from Appendix C shows the pictograms and the hazard classes covered by each of them. If the specific MWF is found to meet the guideline for one of the hazard classes, then the pictogram must be used on the SDS and product label. Only the environment pictogram is not mandatory under GHS.
Figure 3. This figure taken directly from Appendix C of HazCom 2012 shows the eight pictograms that will need to be used on SDSs and labels and what hazard class(es) they cover. (Courtesy of GHS Resources, Inc.)
From the MWF perspective, the most likely pictograms are the exclamation mark and corrosion. Figure 3 shows what it means for a product to have either of these labels. An exclamation mark means that the substance could be an irritant (skin and eyes), skin sensitizer, exhibits acute toxicity and is a respiratory tract irritant. For corrosion, the substance can cause skin corrosion/ burns, eye damage and also be corrosive to metals.
The signal words needed to classify a MWF are either
danger or
warning. The former is an indication that the fluid is a severe hazard, while the latter means that it is a less severe hazard. Hazard statements are used to describe the nature and, where appropriate, the degree of the hazard. Precautionary statements are used to recommend ways to minimize or prevent adverse effects.
Each of the hazard classes is further subdivided into several categories that are given a numeric rating. The number of subdivisions is dependent upon the hazard class. In general for GHS, the lowest number (usually one) represents the most hazardous category. This approach is completely opposite to how the Hazard Material Identification System (HMIS®) and the National Fire Protection Association (NFPA) are organized. Both systems, widely used in the U.S., rank the most severe rating with the highest number.
The optimum way to evaluate a MWF is to use test data. When not available, hazards can be estimated by using either the threshold or additivity method. The former involves determining the concentration of a specific component and comparing it to a specific concentration limit. In the latter, the sum of the concentration of specific ingredients is calculated to see if the value exceeds a specific concentration limit. Requirements for specific categories within hazard classes are provided in Appendix A of the HazCom 2012.
One of the most common issues for MWFs is skin irritation due to the high alkalinity of many water-based fluids. Under the GHS format, the threshold method applies, as shown in Figure 4. Either the pH of the mixture determines its classification as a skin irritant or else the classification of specific Category 1 and 2 raw materials that cannot be evaluated using the additivity approach.
Figure 4. The threshold method is shown as applied to skin hazards. Classification of skin hazards is made based on the pH of the mixture or on whether a specific raw material in Category 1 or 2 is at a concentration where the entire mixture must be designated in either of those categories. The table number refers to its location in Appendix A of HazCom 2012. (Courtesy of GHS Resources, Inc.)
One of the raw materials for which the additivity approach does not apply is acids and bases. As shown in Figure 5, MWF formulators also will need to evaluate the potential salts that can be formed from the variety of bases and acids used. These salts must also be taken into consideration in evaluating the hazardous nature of a MWF formulation.
Figure 5. Any one of the bases in the left column can form a salt with an acid in the right column in a metalworking fluid. Formulators will need to evaluate potential salts when determining how to properly prepare a GHS SDS and label for their products. (Courtesy of Chemical Solutions)
Guidelines for the additivity method are shown in Figure 6 for the Category 1 and 2 hazard categories. During their presentation on GHS at STLE’s 2012 Annual Meeting last May, STLE-member Dr. Richard Kraska, president of GHS Resources, Inc., in Bonita Springs, Fla., along with STLE Fellow Dr. John Howell, vice president of GHS Resources, Inc., showed how the additivity method is used in Figure 7 (
3).
Figure 6. Guidelines for using the additivity method for determining the skin hazard category for a metalworking fluid formulation are shown. Note the final designation involves not just the individual rankings of raw materials but their sum. The table number refers to its location in Appendix A of HazCom 2012. (Courtesy of GHS Resources, Inc.)
Figure 7. The process for using the additivity method to determine the skin hazard category for a metalworking fluid containing specific concentrations of MEA, TEA and sodium petroleum sulfonate is shown. (Courtesy of GHS Resources, Inc.)
In this example, they evaluated a fictitious MWF containing the following raw materials:
1.
Monoethanolamine (MEA) = 0.9% (Category 1)
2.
Triethanolamine (TEA) = 2.0% (Category 2)
3.
Sodium Petroleum Sulfonate (Na Pet Sulf) = 4.0% (Category 2).
As noted in Figure 7, the process involves first determining if there is sufficient concentration of all Category 1 raw materials for the MWF. The only Category 1 raw material is MEA, which is present at a concentration that does not equal 5%.
Then the process moves to evaluation of the two Category 2 raw materials: TEA and sodium petroleum sulfonate. In the calculations, MEA has to be included as a Category 1 raw material, and its presence in the MWF means that the concentration of Category 2 raw materials exceeds the 10% limit. The result is the MWF must be designated as skin Category 2 under the GHS system.
The timetable laid out by OSHA is for GHS training to be conducted by employers by Dec. 1, 2013. This process involves explaining how GHS will change the way SDS and product labels are prepared.
Compliance with GHS is mandatory by June 1, 2015. All companies involved (manufacturers, distributors and users) may continue to follow the same procedures for preparing MSDSs and labels that they currently use and that are in compliance with current regulations until converting over to GHS. Distributors may sell products in compliance with current regulations for six additional months (Dec. 1, 2015).
Armed with this information, the MWF formulator must now evaluate its product formulations to assess the nature of hazards. MWFs are extremely complex, making this process very difficult.
Typically, preparation of MSDSs is carried out in part by reviewing information obtained from raw material suppliers. At this point, raw material suppliers must meet the same timeline as MWF formulators, which mean they do not have to provide GHS SDS until June 1, 2015.
One source that MWF formulators should use to evaluate the rating of raw materials is the European Chemicals Agency (ECHA), Classification & Labeling (C&L) Inventory Database that can be accessed
here.
The information is provided by notifications from all companies using a particular chemical substance in the EU. Ratings for specific chemical substances can vary, and the ECHA does not make any recommendations about what rating to use nor does it verify the accuracy of the information uploaded into the database. In addition, the inventory is constantly updated, so any users should frequently check back to see what if any new data has been inputted into the database.
EMPLOYEE TRAINING
According to an OHSA spokesperson in Washington, D.C., “The updated Hazard Communication Standard (HazCom 2012) requires employers to train employees on the new label elements and the SDS format that are in HazCom 2012. The training on the new label elements should include pictograms, signal words, hazard statements and precautionary statements. For the training on pictograms, for example, topics covered should explain such things as what they are, what they look like, what hazards they represent and where the employee will see them.”
The spokesperson continues, “Training on the SDS format should include a review of the 16 sections and the type of information that would be included in each of these 16 sections.”
OSHA does not believe the concepts in HazCom 2012 are confusing but emphasizes that they are new. The spokesperson adds, “OSHA believes that to gain the maximum benefit from this updated standard, employees need to understand what they are seeing on the new label elements and SDSs. OSHA believes that once companies and employees are trained on the updated elements of the standard, it will be easier for employees to not only understand the hazards of the chemicals to which they are exposed but how to better protect themselves.”
Howell indicates that it is best to start employees with the basics. He says, “For employers, be sure that your employees, particularly those on the front line, such as warehousemen and chemical operators, are well-versed in the basics of the Hazard Communication Standard. While much is new, a lot has not changed, and it is best to be sure everyone is well-grounded in the basics. Then and only then can you progress to training, for example, on the meaning of the new pictograms, etc.”
Kraska agrees and adds that employers will need to reconcile old training programs with new requirements. He says, “Employers will then need to reconcile old training programs with new requirements and retrain on their new comprehensive training program by the second deadline.”
Howell considers the change in hazard severity of the product to be the most confusing aspect of converting to the GHS format. He says, “This occurs even though the formulation of a specific product has not changed, but the change in the hazard severity is due to the application of the new hazard classification rules for mixtures.”
Howell advises that MWF formulators need to go through several examples from their product line. He says, “The formulator will likely find several if not many examples of where the product hazard statement formerly said, “CAUTION: May cause skin irritation” changes to “DANGER: Causes skin irritation.” They need to go through the mixture classification process in detail so they understand why, for example, such new label statements are required.”
Kraska considers the pictograms and the hazard potency class numbers to be the most confusing elements of GHS. He says, “The pictograms are new, and most employees may not have seen them before. With regard to the new hazard classification, the lower the hazard potency class number (1-4) the more potent the hazard, while with NFPA and HMIS codes the higher the number the more serious the hazard. This will be confusing to the most workers.”
Tim Cawley, product sustainability leader for The Dow Chemical Co. in Midland, Mich., believes that as part of their commitment to Responsible Care, suppliers will be willing to come in and train customers on how GHS will affect their products globally. He says, “Additionally, there are third-party companies that can be leveraged to train employees on the GHS program.”
Cawley feels that CLP could be a confusing element for customers to understand as they determine how to orient towards using GHS. “The CLP Regulation is the EU commitment to implement GHS. It introduces new classification criteria, hazard symbols (pictograms) and labeling phrases, however, it also takes into account the elements, which are part of the earlier EU legislation,” Cawley says. “The information requirements laid down in Regulation (EC) No1907/2006 (REACH will ensure availability of hazard information). The close relationship of REACH & CLP and how to implement those could create confusion in the lubricant industry.”
To provide an EU perspective, Heinz Dobbertin, managing director for C.S.B. GmbH in Krefeld, Germany, was contacted. “Try to make people understand that GHS is using a different approach for classification and labeling. In a similar manner to the system used in the EU previously, GHS tries to identify all potential hazards a substance/mixture may have, regardless of potential use,” Dobbertin says. “The procedure to identify hazard is also quite difficult, as the parameters are not always easily understood and get even worse for mixtures such as MWFs. U.S.-based companies will need constant training and monitoring of all departments involved and workers will especially need to be trained to get used to the new way of labeling.”
GLOBAL PERSPECTIVE
An area of complexity to understand is that GHS will remain a regional issue as regulations specific to a country or a region will need to be taken into consideration. Cawley says, “It is important to note, though GHS standards are global, it is not a harmonized process. Therefore, multinational lubricant and MWF companies will see differences globally based on regional GHS differences.”
Cawley continues, “It is not necessarily the concepts of GHS that are confusing, but, rather, that each country applies their specific requirements on top of GHS that will need to be carefully explained. The concept of SDSs is not new. However, the system is being built based on the UN-GHS and the implementation and details for each country may be very different.”
Kraska agrees. “Canada is expected to publish its rules in the spring of 2013 and is a big unknown. Currently, Canada has a list of substances with mandatory disclosure requirements. The EU, Japan and New Zealand have mandatory hazard classifications for many substances,” Kraska says. “The classifications of these substances are not consistent among these three countries. The rules are sufficiently different in many countries so that country-specific SDSs are advised.”
The OSHA spokesperson comments on the need for chemical manufacturers such as raw material suppliers and MWF formulators to continue to follow both U.S. and specific country regulations applied specifically to shipments. “Raw material suppliers and MWF formulators would need to follow the requirements of the U.S. Department of Transportation (DOT) Hazardous Materials Regulations and comply with the requirements of the countries to which they are shipping, including providing appropriate labeling and SDSs for the hazardous chemicals being shipped,” The spokesperson says. “However, with OSHA updating its regulations to align with GHS, this should be much easier than it has been in the past since many countries have implemented or are in the process of implementing the GHS. You will find a link on the UN Web site that discusses GHS Implementation
here.”
EVALUATION OF MWF FORMULATIONS
The first task for the MWF formulator is to obtain raw material information from suppliers.
Kraska says, “Lubricant manufacturers should ask suppliers to provide GHS-compliant SDSs and labels as soon as possible.” Howell focuses on making sure that MWF formulators obtain confidential information from their suppliers. He says, “If the MWF formulator has not done so already, they need to request so-called confidential ingredient information for products used as raw materials, which themselves are mixtures. MWFs they manufacture cannot be classified unless information about these raw material mixtures is known to the formulator.”
An initial evaluation of every MWF formulation is advisable at this point, even with more than two years to go before compliance with GHS becomes mandatory. Howell says, “A critical review of raw materials—including purchased mixtures that the formulator is using—should begin now.”
Kraska cites that using the ECHA Web site to obtain information is advisable. He says, “Annex VI of the EU CLP regulation classified about 1,000 chemicals under GHS criteria. For other chemicals, people should check REACH registration dossiers, as well as the C&L Inventory. Subscription databases that compile various chemicals lists (IARC, NTP, ACGIH, DOT environmentally hazardous substances, global exposure limits, etc.) may be useful. A subscription is usually provided with licenses to software-authoring packages.”
When asked about specific additive classes that MWF formulators should pay close attention to, Howell reiterated that all formulators must know exactly what chemical substances are in the raw materials they are purchasing.
Kraska pointed out two specific substances that will be of concern for formulators. He says, “Now that diethanolamine is classified by IARC as a carcinogen, formulators should make sure they know the free diethanolamine levels in other alkanolamine and alkanolamine derivatives that are being used. With the new 0.1% threshold for Class 1 sensitizers, formulators need to ask suppliers to address the sensitization potential of the biocides they use.”
MWF FORMULATOR INPUT
Representatives from two MWF formulators were contacted to provide their perspective on the challenges, concerns and assistance they are looking for in complying with GHS.
STLE-member David Morrison, HSE specialist for Castrol Industrial North America in Naperville, Ill., says, “First off, in today’s world, where a host of information on the hazards of chemicals is available, a greater degree of guidance/structure has been needed in the realm of MSDS/SDS production. The entire transition to GHS will be a challenge because of its complexity. While it may seem simple to train people on the rules set forth in GHS for SDSs, there will be a significant amount of follow-up required once SDSs start reaching workers. In many cases, SDSs will expand and increase the amount of information provided to the end-user.”
In the final challenge, Morrison captures the essence of the difficulties facing MWF formulators. “Another challenge is the question of how OSHA will interpret and enforce the GHS rules. Determining the hazards on a SDS are quite clear as written. The question becomes how one interprets the available information on individual ingredients,” Morrison says. “For those compounds that have copious toxicity studies with varying results, it may become very difficult to determine the ultimate hazard that is imparted to the formulation. If one chooses to take the conservative view and report the most severe hazard result, how would that compare to another who chooses a more liberal or less hazard severity result? And ultimately is that most severe interpretation correct?”
STLE-member Dr. Eugene White, EHS manager for CIMCOOL Global Industrial Fluids in Cincinnati, Ohio, says, “A major challenge is to insure that all applicable aspects of North American business units will be in compliance with HazCom 2012. The goal will be accomplished by a thorough examination and understanding of regulations on a departmental-wide basis. Also, planning for worker training (in multiple phases) is in process.”
White believes that his company’s employees and customers will easily adjust to GHS changes because of the emphasis placed on training. He adds, “The paradigm shift from The Right to Know to The Right to Understand may require some explanation, along with considerable discussions on the GHS pictograms and precautionary hazard statements.”
Morrison expressed concern about the time span between SDS training and the first required issuance of the new SDS format. He says, “A year-plus is a long time between training and implementation!”
Morrison is uncertain about whether the recipients of SDS will understand the information. He says, “While the aim of GHS is to simplify hazard communication, there is a good chance that it will do just the opposite. The proscriptive methods of determining the hazards of a mixture and the disclosure rules may fill an SDS with copious amounts of toxicological information, some of which may be contradictory. Interpretation by trained professionals will be hard enough, let alone the layman.”
Both White and Morrison are looking for assistance from their suppliers. White says, “We have always relied on our suppliers to provide us with accurate, current and timely information about their products.”
Morrison is looking for his company’s suppliers to provide more detailed information in a periodic time frame to help his company prepare for GHS. “Comprehensive hazard information of the products they provide and perhaps some interpretation of the various studies that exist with the view of how operators are exposed,” Morrison says. “A set schedule of updates would be appreciated as well, except where information becomes available that significantly affects the hazard classification. Due to the large number of SDSs in our inventory, it is difficult to handle the necessary updates if information is received too often.”
White is pleased with the guidance information provided in HazCom 2012 for helping formulators properly categorize their mixtures. He says, “HazCom 2012 appears to give extensive guidance on the classification of hazards, especially as it pertains to chemical mixtures. Appendix A of the standard shows that OSHA put a lot of thought into this issue, especially the use of bridging principles when test data is not available.”
As a matter of focus, White provided advice on two additive classes that should be scrutinized carefully by formulators. He says, “Due to potential acute hazardous effects, corrosive chemicals and biocides should be examined closely.”
NEED FOR REFORMULATION
On the subject of reformulation, the respondents, in general, do not feel that the MWF industry will need to dramatically reformulate, but they caution that maintaining confidentiality will be more difficult. Howell says, “I would suggest that GHS compliance by itself will not force the MWF industry to make major formulation changes. However, particularly because of how the trade secret section of the regulation has been modified (
see 29 CFR 1910.1200 for details), formulators are going to have a harder time protecting their formulations from disclosure.”
Kraska suggests that two areas of focus for reformulation are diethanolamine removal and biocides. “The MWF industry needs to chase out residual levels of diethanolamine from many sources in their products now that it is listed by IARC as a carcinogen,” Kraska says. “Formulators need to have a heart-to-heart chat with biocide suppliers on the sensitization potential of biocides since the threshold for Class 1 sensitizers is now 0.1% instead of 1.0%. If suppliers do not have the expertise to answer these questions, then you need to find another supplier.”
Morrison places the focus on the reformulation issue on the reaction of the formulator’s customers—metalworking end-users. “It is the customer who generally forces change within the industry. If GHS is effective, then it will level the playing field between those who have strictly interpreted OSHA HazCom rules and produced conservative MSDSs and those who loosely interpret those rules to produce liberal MSDSs in the past,” Morrison says. “I do believe that this will force end-users to take a more in-depth look at hazards, exposure and risk to operators. It will certainly help maintain the current drive in the industry to produce safer products for the end-user.”
White says, “I think the industry has always been proactive in its attempt to foster health and safety in product development and, therefore, I do not anticipate any industry-wide changes in formulations in the foreseeable future. A significant outcome of GHS is that it heightens our awareness of the need to better understand and control industrial chemical hazards.”
RESOURCES
The OSHA spokesperson indicates that the Hazard Communication Web site contains a number of compliance-assistance products that can be viewed at
here. The spokesperson says, “OSHA is also developing a number of compliance-assistance products that will be posted once they are complete.” Products include:
•
An OSHA Brief on labels and pictograms.
•
Compliance guides for chemical manufacturers and users.
•
Several technical guidance documents, including those for Hazard Classification, Safety Data Sheet Preparation and Model Training materials.
•
Web applications for a SDS electronic form, label elements and an acute toxicity calculator.
•
Hazard Communication Compliance Directive.
Besides the OSHA Web site, Howell notes that the ECHA Web site (
here) is a good resource. He says, “This Web site allows the user to quickly and easily research information on classifications of hundreds and hundreds of chemical ingredients blended or reacted into MWF products.”
Kraska cautions that software packages are available to facilitate the preparation of SDSs and labels, but they are problematic to use. He says, “So far, many new or updated software packages have many problems in the quality of hazard data they use and many are not as easy-to-use as advertised.”
Dobbertin remarked that it would be useful for U.S.-based companies to work with contacts in the EU who can provide assistance. He says, “If companies have an EU subsidiary or are cooperating with EU companies, they should try to transfer experiences made in the EU. It might be worth sending people responsible for classification and SDSs to the EU to get training or have people from the EU come to the U.S.”
LESSONS FROM THE EU
According to Dobbertin, the EU implemented GHS for substances in December, 2010, but will not be implementing GHS for mixtures until the same time as the U.S., which is May 31, 2015. He says, “The task of implementing GHS has been quite difficult, and a lot of companies are still struggling. We are also noticing an increasing number of companies interested in outsourcing the classification process and SDS creation.”
Dobbertin also offered the following guidelines on implementing GHS from his experience in the EU. “The system of classification has become very complex and difficult to understand, and to me that will be the first and most important issue to deal with,” Dobbertin says. “Companies adopting an internal data organization to deal with GHS might also prove to be very difficult. In my view, each company will need to draw up an implementation plan identifying all necessary steps and implement them in a logical order. As this is an individual task, no general answer is possible because each company will need to identify the necessary steps.”
From his global perspective, Cawley offered an assessment on the differences in how each country will implement GHS. He anticipates most of the world will adopt the European precautionary principle, which looks at each chemical substance from a zero risk standpoint or a worst case scenario. Additionally, Cawley noted that an exception may be the U.S., which will use a GHS approach that he predicts will be based on analysis of health and safety data obtained for chemical substances. In other words, the U.S. will follow a performance-based standard, while the EU standard is prescriptive.
Cawley predicts that markets including Canada, China and Japan will follow the lead of the EU. He adds Dow is working diligently to implement GHS across the globe and is ready to help customers as they prepare to meet these compliance requirements.
However GHS implementation occurs, companies doing business in the U.S., Canada and the rest of the world need to be aware of regional differences. The goal of uniform SDSs and labels will be met to some extent, but there will be a good deal of confusion as companies try to meet this new standard. Use of available resources and training must be emphasized to ensure that the transition to GHS can be done as smoothly as possible.
REFERENCES
1.
The UN Regulation can be found
here.
2.
HazCom2012 can be found
here.
3.
Howell, J. and Kraska, R. (2012), “2012 OSHA HCS – A Close Look at Trade Secrets, Hazard Classification and Using the EU C&L Data,” Presented at the STLE 2012 Annual Meeting, St. Louis, Mo., May 6-10.
Neil Canter heads his own consulting company, Chemical Solutions, in Willow Grove, Pa. You can reach him at neilcanter@comcast.net.