Complexity in oil analysis: Part VIII
Jack Poley | TLT On Condition Monitoring January 2013
Non-routine elements from the spectrometer.
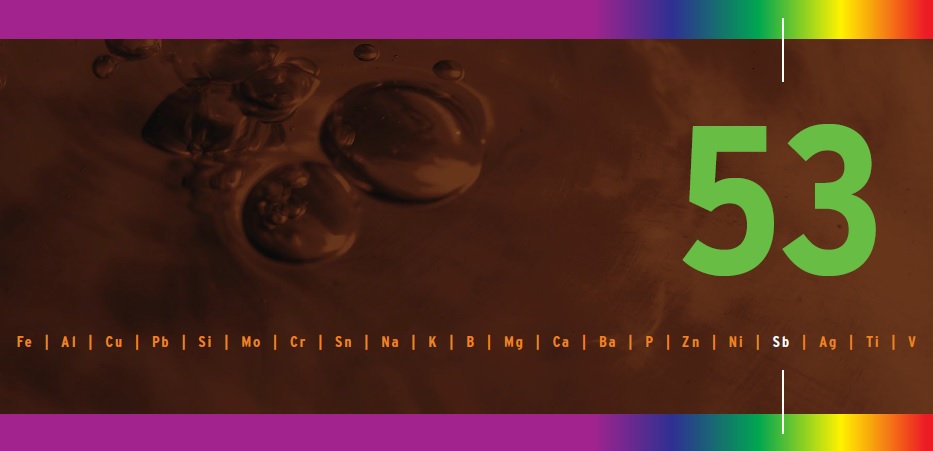
A TYPICAL SPECTROMETRIC METALS ANALYSIS for an oil sample might entail as many as 20-30 discrete elements even though most individual sample results don’t reveal nearly that many different metals in significant quantities. But commercial labs in particular cater to a full gamut of component types and applications such that they must be ready for metals that might be present or that are expected to be present for specific types of components or specific manufacturers and models—thus the need for a full suite of elements.
There’s no harm in monitoring as many elements as the spectrometer is configured to analyze. All semiautomated and automated UV spectrometers adapted to in-service lubricant testing simultaneously produce their entire array of elemental trace data in one testing pass, so there’s no money to be saved by selectively reporting elements (though this is occasionally done for some programs for various marketing and convenience purposes). The ultimate benefit is that, every now and then, a previously dormant element suddenly presents itself, and it should arouse some suspicions.
Let’s look at a few.
Titanium (Ti). As a metal, Ti is frequently found in aircraft parts, often presenting in oil analyses, but it’s rarely (never?) found in diesel engines as a part construction element. The first time I saw Ti in an unfamiliar situation, it was the consequence of the application, a titanium dioxide mine, at levels from 10-40 ppm! Thus in this situation, Ti was an environmental contaminant just like Si might normally be indicative of an air cleaner element or housing compromise or possibly poor lube transfer storage and practices. I did well with this—I figured it out in the first batch of samples, called the customer and was informed about the substance being mined. The rest was easy and normal diesel sample evaluation. But I’d had a previous, embarrassing lesson, which prepared me for this surprise.
Some columns ago I had mentioned that as a neophyte in the business in the 1960s, I mistakenly treated persistent Cu in several dozen diesel engines as a wear metal when, in fact, the engines were operating at a Cu mine, the operation of which generated a lot of Cu dust that permeated the engine sumps. That experience trained me to always question unusually large groupings of similar samples with persistence of even a common metal like Cu, as well as think spherically from all sides of the puzzle at hand, in terms of correctly sourcing a metal like Ti that suddenly appears or routinely appears but is seemingly out of place. The modern term is thinking outside the box.
One other (rare) source of Ti in non-aircraft lube sumps might be from Stellite, a proprietary alloy that is primarily cobalt (Co)- based, but I’ve never seen Ti present in this fashion. It is likely that any concentrations that might have existed were in amounts too low to be detected by the spectrometer.
Cobalt (Co). The only time I’ve seen Co is in diesel engines, and I learned the source was likely Stellite, a proprietary alloy of Co that features Cr or possibly Mo and other traces. When Co was presented, I noticed that nickel (Ni) accompanied it more often than not. Less occasionally, chromium (Cr) might appear, but I’m not certain that was necessarily from Stellite as there were also piston rings to consider as a source of Cr from chrome plating. Perhaps Co would be present at 6 ppm and Ni at 2 ppm (1). It was further explained to me that the Stellite alloy was only found in the exhaust valves of the engine, where temperatures were highest in the valve system. The effect was to minimize corrosion and deformation of the valves and seats.
It’s been decades since I’ve seen any Co (of course, some labs don’t test for Co). I’m not sure if Stellite is still utilized in valve and valve seat construction in the 21st Century. If any reader is aware of such, or other Stellite use in oil-wetted machinery, I’d appreciate being informed.
Nickel (Ni). Nickel is not really uncommon, but neither is it presented routinely because, although it’s a player in stainless steel and construction of copper-lead sleeve bearings and a variety of other places, its concentration is usually too low to be seen from sample-to-sample. In a way trace metals are good flags when they do show because it probably means that other metals are presented at significantly higher levels of concentrations beyond typical, thus escalating the urgency and severity of the evaluator’s comments.
The non-hydrocarbon effect of trace metals appearances. Unfortunately with today’s plethora of synthetic oils, Ni (and other elements) is presented regularly with many formulations. Is there Ni present in these fluids? I doubt it, and no one’s ever contradicted me in that regard. I believe it is an interference phenomenon based on the spectrometer’s calibration/standardization with hydrocarbon fluids rather than the synthetic fluid under examination. Most spectrometers are set up and calibrated using hydrocarbon standards. They are commercially available and have served their purpose properly for decades.
Synthetic lubes are not hydrocarbons by definition. Most of them do not combust as readily as hydrocarbons, but in any case they combust and react differently when fed into the analytical gap of the spectrometer, particularly with rotating disc electrode systems where the samples are analyzed neat. Still, even ICP (inductively coupled plasma spectrometer) results have demonstrated artifacts (false presenting is perhaps better phrasing on my part) of certain elements due to light emission wavelengths that register on detectors that are positioned in discrete locations where Ni and other elements always appear, based on the wavelengths emitted for those particular elements after recapturing electrons upon being ionized (2).
For our purposes here, the point is that we may see false readings for the likes of a number of metals, e.g., Si, Mo, Cr, Sb (antimony), Sn, Ni, Co, Ti or others when certain synthetics are being analyzed using a hydrocarbon calibration for the spectrometer. Since some of the listed metals (and the list is not necessarily confined to these) are also wear or contaminant or additive metals, it is at times difficult to speculate about their source. The method I utilize is to look at the unlikeliness of a metal’s presence in the situation. Ti, of course, comes to mind in this type of case unless the sample is from, say, a gas turbine!
Why don’t labs calibrate for this? I expect that some do, particularly private labs that confine their analyses to only a few fluid types. In a commercial operation, however, it would be a significant task to sort out which samples need such treatment (ahead of the actual analysis) and to toggle between hydrocarbon and hydrocarbon base-stocks. This is especially true if several synthetics were involved in the daily workload, as one would need standards for each major chemistry type of synthetic received for analysis in order to truly address the artifacts that may be presented.
There is also the fact that prepared synthetic standards, to my knowledge, are not commercially available in the marketplace. Even should there be, the expense of maintaining several sets of standards, coupled with the logistical challenge of knowing when to invoke the hydrocarbon calibration substitution (many fluids are not sufficiently identified when submitted). Thus a laboratory would have to blend its own standards and deal with often insufficient information in the main.
This is a painstaking, expensive undertaking. In truth, many experienced evaluators are likely aware of the false presentations of various elements that exist for samples routinely analyzed at their facilities and can probably finesse the situation adequately most of the time, e.g., seeing 50 ppm Sb and 0 ppm Fe, Al, Cu or Pb or even levels at 25 ppm (half the Sb) is simply not reasonable given the composition of most components’ lubricated parts (3). By the same token, however, Sb is greatly diminished, if not disqualified, as a wear metal indicator due to the high amount of subtraction necessary due to the baseline readings: if there is 5 ppm or less Sb from wear (not untypical in a Cu/Pb or Babbitt bearing wear scenario when it might present), and 50-plus ppm from baseline readings, this is a lot of noise in the normalization calculation.
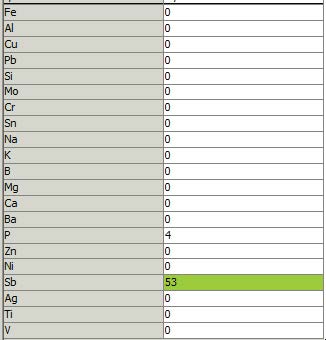
As shown in the figure, here is an example of false presenting for Sb in a new synthetic compressor lubricant (I was not provided with fluid chemistry). Yes, the Sb could be an additive, but in such a low quantity it would seem ineffectual. There are Sb additives around, but all those instances I’ve seen are for EP (extreme pressure) agents, which are generally in a thicker medium, not compressor lubes, such as the example data shown. Even the relatively low P (phosphorus) value is likely not there—for that matter detecting P much below 50-100 ppm is marginal with most P spectral lines available.
Again, I’d welcome additional input from an informed reader on this elusive area.
REFERENCES
1. Here we are beginning to enter the lowest credible range of most spectrometers, though I then had the advantage of a three-meter spectrometer as opposed to today’s more compact spectrometer. The extra length provided somewhat greater resolution for many elements such that we could consistently see tenths of ppm in trace metals like Co, Ni and Ag (silver). While most of the time this wasn’t particularly necessary, I was able to use Ag’s resolution to some advantage when evaluating samples from Packard engine bearings utilized in U.S. Navy minesweepers. Aluminum and other non-magnetic metals were employed as much as possible to minimize magnetic effects and interference with the minesweeping operation, the boat’s sole purpose. Even the hull was wooden.
2. It is not within the purview of this article to fully explain the spectrometric process. Many resources are available on the Web to learn about this process more fully.
3. False readings are not necessarily confined to metals analysis and the UV spectrometer. Infrared spectroscopy is highly dependent on proper referencing. Failure to have a reasonably close reference for a synthetic will virtually always result in questionable readings (e.g., the oxidation band, a staple of FTIR output, is hugely influenced by certain types of synthetics, especially those whose chemistry is significantly oxygenated). If proper referencing is not applied, the result is usually hugely false positives for oxidation, negating any useful assessment of oxidation. The lucky aspect of this is that synthetics, for the most part, are far more resistive to oxidation than hydrocarbons. Therefore the odds of a masked oxidation condition are rather low. Still, that’s not good chemistry and certainly not good oil analysis, do you think?
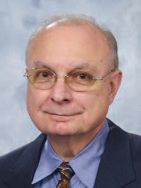
Jack Poley is managing partner of Condition Monitoring International (CMI), Miami, consultants in fluid analysis. You can reach him at jpoley@conditionmonitoringintl.com. For more information about CMI, visit www.conditionmonitoringintl.com.