What are the most important tests that should be performed on used lubricants for routine condition monitoring?
TLT Sounding Board December 2012
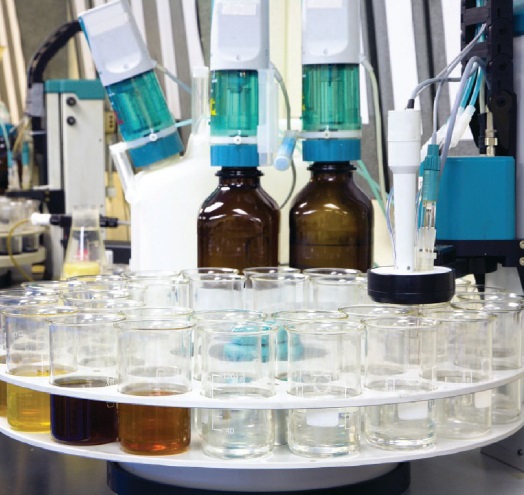
www.canstockphoto.com
Has there been talk that viscosity might no longer be the defining characteristic of a lubricant? If so, it was quickly dispelled by this month’s query. 65% of TLT readers say viscosity remains the No. 1 most critical factor to test for. As one survey respondent said, “If the viscosity is not correct, the rest of the criteria do not matter.” Also at the top of many lists were element analysis, Total Acid Number, Total Base Number, particle count and Fournier Transform Infrared Spectroscopy. When asked about the top characteristics to look for in a used-oil testing laboratory, our readers cited the combination of quality control and consistency. Several noted that manual work done by technicians was becoming passé in the industry with automated machines becoming the norm. Many readers also mentioned the need for personalized interpretation of results, not standardized commentary.
Water content, viscosity and particle count. Water content is important because the water is not a lubricant and using the wrong lubricant can affect the wear of the parts.
Viscosity, acid number.
ICP for wear metals.
(1.) Viscosity at 40 C and 100 C. (2.) Viscosity Index. (3.) Visual inspection of the oil.
ISO code, viscosity, Total Acid Number (TAN), water content.
Viscosity, because this can indicate the integrity or degradation of the lubricant.
Viscosity, because it is the most important characteristic of lubricant and indicates some pollution.
Element analysis to see whether the lubricants are contaminated.
Viscosity, TAN, Total Base Number (TBN) and ICP Metals. These tests tell you the condition of the oil.
Wear metals—this shows if anything is going wrong. Viscosity, because it effects many things.
It really depends on the application, i.e., for ball and roller bearings 0.01% water has a tremendous effect, but 1% water will hardly affect a plain bearing at all.
Elemental analysis by ICP-AES is necessary to detect and observe wear metals and other contaminants in lubricants. Fournier Transform Infrared Spectroscopy (FTIR) is necessary to monitor the degradation process of the oil (soot, nitrates, sulfates, oxidation, acid build-up, additive depletion) and to observe any contaminants (gasoline, diesel, water and glycol). Viscosity testing is necessary to ensure that the used lubricant can still meet the demands of the environment it is being used in.
Viscosity.
Viscosity and TAN to measure oxidation stability, XRF to measure remaining antiwear and EP additives.
(1.) TAN/TBN measurement: ordinary oil aging/basic reserve depletion. (2.) Viscosity measurement: most important single oil property. (3.) Other tests depending on application and base oil (water, elements, FTIR, etc.).
Viscosity and oxidation to check oil conformity. Contaminants (water, soot, dust, coolant, etc.) to check oil integrity. Element contents to check wear rate.
Water, TAN, cleanliness, oxidation stability for lubricant health and wear analysis for asset health.
Viscosity, water, contamination, wear. We need to do a trend and monitor if our machines are deteriorating or maintaining.
Dependent on the fluid being analyzed: Viscosity at 40 C and 100 C. Spectrographic analysis.
Oxidation, because it is the most frequent issue found in oil analysis.
This all depends on the component and application. Viscosity, ICP/wear metals and some type of water crackle test is common.
Particle count, water by KF, wear metals, viscosity. These tests will give the equipment owner a picture of the equipment and the lube.
Percent of metals.
Viscosity to get correct film thickness ICP. Wear and contamination trending. Particle count. If cleanliness is critical, analytical ferrography. If cost were no issue, I would add this as routine because there is nothing better than a visual on wear and contamination.
Elemental analysis, viscosity and water determination.
Spectroscopy, particle counting, viscosity, FTIR.
Is viscosity still the single most important condition monitoring test you can perform?
Yes
65%
No
35%
Results based on a survey of 13,000 TLT readers.
It depends on the application of the lubricant. However, viscosity and FTIR should always be done.
Viscosity, TAN and TBN. Particle count and load.
Dirt and particle content to detect excessive wear.
Viscosity, elements, TAN, water by KF, ISO count. You want to check for contamination and lubricant condition.
I would say viscosity and metals are both important factors of what is going on in the component.
The question is too vague. Assuming the question is on a water-soluble product, concentration of the fluid. Why: if too low, not enough lubricant for lubricity, too high could cause overheating.
Viscosity, metals, TAN and IR (and maybe water content depending on application).
Visual appearance and odor of every sample should be reported. Much information can be obtained by simply looking at the sample as received. FTIR analysis gives the most information with the least amount of sample and at a relatively low cost per test. Beyond that, the tests should be selected on the basis of what property is critical to the proper operation of the equipment in question.
The cost of an oil sample that includes spectrochemical analysis, viscosity, water (by titration), acid number and ISO particle count should be…?
$5-$10
5%
$11-$20
33%
$21-$45
44%
More than $45
20%
Results based on a survey of 13,000 TLT readers. Total exceeds 100% because some respondents chose more than one answer.
What are the three most important factors in selecting an oil-analysis testing laboratory?
Reliability, keeping their promises, certified by ASME or ISO.
(1.) Reliable/results. (2.) Good customer feedback on the testing performed. (3.) Fast service.
Quality, speed of turnaround and accuracy.
Reliability.
(1.) Dependable. (2.) Accurate data. (3.) Response time and reputation.
Trained laboratory personnel, equipment and certifications.
Number of machines, delay of result and price.
Whether the lab has ISO17025 certificate. Timing to finish tests. Location.
Consistently prompt efficiency.
Quality of the results, turnaround time and how results are reported.
(1.) Support for interpretation of results. (2.) Profound knowledge for interpretation of FTIR. (3.) Willingness to do detective work regarding causes for changes in oil properties.
Servicing time. Reliability. Expertise.
Testing equipments, experience and logistics (how fast they can send results).
Alertness on critical problems.
Time and accuracy.
It must be accredited with the ISO 9000 series, it must have quality assurance and control, and it must be able to analyze and give recommendations for both good and deteriorated oil samples.
Credentials. Accuracy. Repeatability.
(1.) Certification of the laboratory and individual personnel. (2.) Participation in industry-wide benchmarking test programs. (3.) Cost.
Quality control, quality control and quality control! Did I mention quality control?
Qualified to a standard (e.g., ISO), a program in place to monitor data integrity, training.
(1.) Accreditation—a lab must be on top of its game in all aspects to continuously pass ISO 17025. (2.) Service and knowledge. (3.) Turnaround time.
In-house capability (samples are often sent from one lab to another for tests not done in-house). ISO certification. Rapidity of results.
Good quality control practices.
(1.) Equipment. (2.) Procedures and repeatability. (3.) Cleanliness. Using automated equipment is beginning to be key in the industry. It eliminates the chance of human error. I don’t know how many labs I have toured and have been disgusted by the methodologies used. They are no better than the high school chemistry lab built back in the 1950s and still used today. The processes and tests are all manual, as measurements are done by a technician with a syringe. These methods are crude and outdated. Some of these “top of the line” labs out there need to wake up. It’s time to upgrade! Again, some of this leads into the procedures. If you are relying on a technician to measure out the same amount each time, forget it. Your procedure is horrible. Automated machines and processes today are much more accurate, and the results are repeatable. I would like to add a fourth: the analysis of the results. Many let a computer do the work for them, or use “canned” responses, something a card reader would say to anyone who comes their way. I need specific analysis and precise recommended actions. Not something that I could get from hiring a high school student. This is supposed to be a specialized field.
Understanding of our needs, professionalism of range of tests offered and knowledge of tests.
Quality/consistency of results, analysis interpretation expertise and service capability.
Quality, equipment knowledge/training aspect, software ability.
Online results.
Editor’s Note: Sounding Board is based on an e-mail survey of 13,000 TLT readers. Views expressed are those of the respondents and do not reflect the opinions of the Society of Tribologists and Lubrication Engineers. STLE does not vouch for the technical accuracy of opinions expressed in Sounding Board, nor does inclusion of a comment represent an endorsement of the technology by STLE.