Lubricating Titanium Alloys
Jean Van Rensselar, Contributing Editor | TLT Feature Article November 2012
Resolving lubrication issues is the last step in widespread commercialization of this material, which has many desirable qualities.
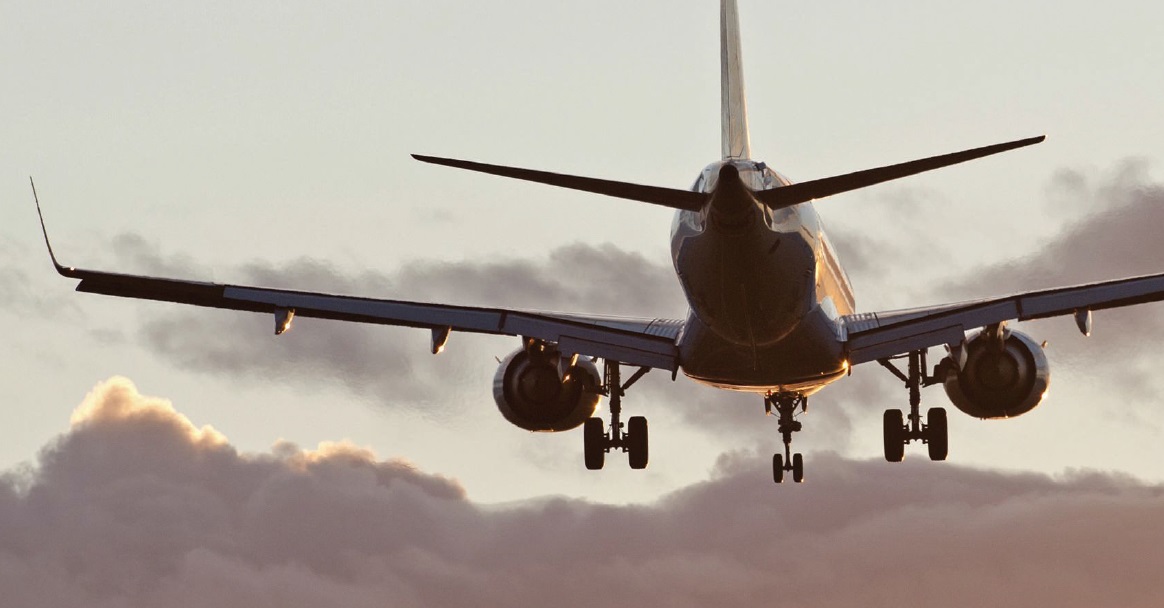
www.canstockphoto.com
KEY CONCEPTS
•
Titanium has the highest strength-to-weight ratio of any metal.
•
New processing technologies are dramatically lowering the price of titanium.
•
Lubrication is the last issue to be resolved before titanium alloys explode into the marketplace.
The keypad on your bank’s drive-thru ATM. Your alarm clock. Graduation day. A fleeing family pet—all these things can be frustratingly out of reach. This is how aerospace, truck and automotive manufacturers have felt for decades about titanium alloys—so perfect for so many applications but too expensive to harvest and too difficult to lubricate. This is all changing.
STLE-member Jun Qu, senior R&D staff scientist, Materials Science and Technology Division, Oak Ridge National Laboratory, in Oak Ridge, Tenn., explains: “Recent developments in titanium processing forecast the availability of lower-cost titanium, and that has prompted further interest in exploring the tribological behavior of titanium alloys as bearing materials.”
Since titanium is not easily corroded by saltwater, it is ideal for boat parts subject to that environment. In applications where high strength-to-weight and high-temperature resistance are important, such as aircraft, spacecraft and missiles, titanium is also the material of choice for some parts. Titanium has the advantage of a very low rejection rate in human tissue, so it is used for permanent and semipermanent replacement parts such as artificial hips. It’s common in dental implants and fillings. Titanium is also currently used in the following applications:
•
Chemical and petrochemical production
•
Hydrocarbon production and processing
•
Power generation
•
Nuclear waste storage
•
Ore leaching and metal recovery
•
Armor plate applications
•
Food and pharmaceutical processing
•
Recreation and sports equipment.
About 95% of extracted titanium ore is refined into titanium dioxide (TiO
2), which is used to produce a super-white pigment for products such as paints, business paper, toothpaste and cosmetics.
CLASSES AND GRADES
Titanium alloys are classified four ways:
•
Alpha alloys. These contain only neutral alloying elements such as tin and/or alpha stabilizers like oxygen. Alpha alloys are not heat treatable. Nearly all titanium has a significant amount of dissolved oxygen and can be considered a TiO alloy.
•
Near-alpha alloys. These contain alpha stabilizers and up to 2% beta stabilizers such as silicon and/or molybdenum.
•
Alpha and beta alloys. These are metastable (capable of existing in a state of equilibrium but are also capable of changing to a more stable state). They usually include a combination of alpha and beta stabilizers that can be heat-treated.
•
Beta alloys. These are also metastable and contain enough beta stabilizer to maintain the beta phase when rapidly cooled. They can also be treated with solutions and aged in order to improve strength.
ASTM categorizes titanium alloys by grades, ranging from 1 (essentially pure) to 38. The most commonly used alloy is Grade 5 (also referred to as Ti6Al4V, Ti-6Al-4V or simply Ti 6-4). It has a chemical composition of 89%-90% titanium, 6% aluminum, 4% vanadium, a maximum of 0.2% oxygen and a maximum of 0.25% iron. It is used extensively in aerospace (strong, lightweight), medical (no rejection issues) and marine (low corrosivity) applications.
Grade 5 is significantly stronger than commercially pure titanium (Grade 1) while having the same rigidity and thermal properties. Thermal conductivity, however, is about 60% less in Grade 5 than in Grade 1. Grade 5 offers a commercially appealing combination of strength, corrosion resistance and ease of fabrication.
ADVANTAGES AND DISADVANTAGES
Pure titanium has the highest strength-to-weight ratio of any metal—as strong as some steels and 45% lighter; twice as strong as aluminum but only 60% heavier. It is also highly corrosion resistant and can withstand extreme temperatures. Beneficial properties of titanium and its alloys include:
•
Low weight and high strength-to-weight ratio
•
Exceptional corrosion resistance
•
Excellent high temperature stability
•
Low expansivity
•
Low or non-magnetic
•
Extremely short radioactive half-life
•
An extremely thin, conductive oxide surface film
•
A hard, smooth, difficult-to-adhere-to surface
•
Compatibility with human tissue.
While titanium is very plentiful (the seventh most abundant metal) it has historically been very difficult and costly to recover; the reason being that it must always be extracted from other ores (the star in a star sapphire is actually a titanium dioxide impurity). Less desirable characteristics include:
•
Difficult and expensive to extract
•
Difficult to machine and cast
•
Difficult to lubricate.
STLE-member Carl Hager, tribology specialist for the Timken Co. in Canton, Ohio, explains, “With titanium, adhesive wear is a big issue because the material is very soft and reactive. In aerospace turbine engines, compressor blades are often made from titanium alloys. During operation, the roots of the blades experience low amplitude oscillations that lead to fretting wear damage. This damage is often initiated as adhesive wear between the mated titanium alloy components.”
The Kroll Process (1)
Titanium has traditionally been produced by the Kroll process, a costly method made even more expensive by the fact that it wastes magnesium during the procedure. Steps include extraction, purification, sponge production, alloy creation and forming and shaping—with these steps usually carried out by different processors in different locations.
Extraction. The manufacturer receives titanium concentrates from mines. The iron is removed until the product contains about 85% titanium dioxide. The material is heated to 1,652 F and reduced to impure titanium tetrachloride (TiCl4) and carbon monoxide.
Purification. The reacted metal is put into large distillation tanks and heated. Impurities are separated using fractional distillation and precipitation. This action removes metal chlorides that include iron, vanadium, zirconium, silicon and magnesium.
Sponge production. The purified titanium tetrachloride is transferred as a liquid to a stainless steel reactor vessel. Magnesium is added and the container is heated to about 2,012 F. Argon is then pumped into the container. This removes the air and prevents contamination with oxygen or nitrogen. The magnesium reacts with the chlorine to produce liquid magnesium chloride. Since the melting point of titanium is higher than that of the reaction, this leaves a pure titanium solid.
The titanium solid is removed by boring from the reactor and treated with water and hydrochloric acid to remove excess magnesium and magnesium chloride. The resulting solid is a porous metal called sponge.
Alloy creation. The sponge is mixed with alloys and scrap metal with the exact proportion of sponge-to-alloy material formulated prior to production. The mass is then pressed into compacts and welded together. The result is a sponge electrode that is placed in a vacuum arc furnace for melting and ingot formation. In order to produce a commercially acceptable ingot, it is usually remelted 1-2 additional times. In the U.S., most ingots produced by the Kroll method weigh about 9,000 lbs (4,082 kg) and are 30 inches in diameter.
When the ingot is finished, it is inspected for defects and the surface may be conditioned per customer specifications. From there, the ingot will be shipped to a finished goods manufacturer where it is milled and fabricated.
BREAKTHROUGH EXTRACTION METHODS
Most titanium is extracted using the complex, cumbersome and costly Kroll process (
see sidebar above). But newer, less costly methods are being developed. One of these is the FFC Cambridge process, which uses titanium dioxide powder (a refined form of rutile (
2)) as feedstock for the end product. When mixed oxide powders are used, the end product is an alloy that is manufactured for a significantly lower cost than the Kroll process. The FFC Cambridge process and other processes being researched have the potential to make titanium alloys much more common in commercial products— especially those involving motor vehicles (
3).
MACHINING DIFFICULTY (4)
Why is titanium difficult to machine? The answer boils down to the physical, chemical and mechanical properties of titanium and its alloys:
•
Titanium conducts heat poorly. Heat generated by the cutting action does not dissipate quickly. Most of the heat is concentrated on the cutting edge and the tool face, which can result in cutting tool deformation, reduced tool life and potential workpiece damage.
•
Titanium can alloy and react with cutting tools. The result is galling, welding and smearing, as well as rapid deterioration of the cutting tool.
•
Titanium is more elastic than steel. Workpieces have a tendency to move away from the cutting tool unless heavy cuts are maintained. Also intricate parts can become unstable under tool pressure.
•
Titanium has poor surface integrity. The surface integrity can be compromised by certain machining techniques, including grinding.
•
Titanium’s poor work-hardening characteristics. Alloys have no stationary metal mass (built-up edge). This creates a high shearing angle that causes a thin chip to contact a relatively small area on the cutting tool face, resulting in high bearing force. This generates heat and ultimately cutting tool damage.
Then there’s the lubrication issue.
The oxygen diffusion process
The oxygen diffusion (OD) process creates dramatic improvements in the hardness and tribological performance for a variety of titanium alloys. The process consists of heat-treating titanium alloys in air or an oxygen-nitrogen binary gas at a temperature ranging between 1,022 F and 1,652 F (550 C–900 C) for anywhere from a few minutes to hundreds of hours. This is followed by air or furnace cooling. OD produces a top oxide layer and a near-surface hard, wear-resistant oxygen-diffusion zone (1–300 μm). The oxide layer is then intentionally polished off to expose the diffused surface. Advantages include:
•
The process is easy to conduct
•
The process is inexpensive
•
Efficiency increases due to friction reduction
•
Reliability and durability improve due to wear reduction
•
There are no part size and geometry restrictions.
LUBRICANT/FLUID CONSIDERATIONS
Referring to a series of tests conducted at the Oak Ridge National Laboratory, Qu says, “In one case when rubbed against a Cr-coated diesel engine piston ring and lubricated by an engine oil, the Ti-6Al-4V alloy suffered a wear rate 2,000 times higher than gray cast iron. This is primarily caused by the incompatibility with the lubricant that was designed for ferrous alloys.”
Like many other metallic alloys, titanium alloys do not respond well to traditional organic lubricants. During contact, titanium transfers to the opposing surface, causing a number of problems including premature wear. Titanium in contact with itself or other metals has a greater tendency to gall than other metals. This means that sliding contact with tooling surfaces necessitates the use of lubricants. But then titanium alloys cause many lubricants to degrade.
“A titanium surface when rubbed and slid against other hard materials (metallic or ceramic) has a strong tendency toward adhesion and material transfer,” Qu says. “Therefore the failure mode is generally dominated by galling in dry conditions and by scuffing in lubricated conditions. Conventional antiwear additives such as ZDDP are designed for ferrous alloys to reduce wear by forming a protective tribofilm at the contact regions. For Ti alloys, first their compatibility with these antiwear additives is less than optimum and, second and more important, the wear rate is so high that a tribofilm, even being formed, is not sustainable.”
Figure 1. Cross section TEM image and EDS spectrum of an OD-Ti64 worn surface, suggesting the presence of an antiwear tribofilm as a result of the tribochemical reactions between the OD-Ti64 surface and the engine lubricant.
Figure 2. No tribofilm on an untreated Ti64 worn surface.
LUBRICATING TITANIUM ALLOYS
The coefficient of friction for titanium-on-titanium rubbing contact is up to three times the value for steel-on-steel and four times the value for bronze and other bearing metals (
5). Two factors combine to give titanium its poor tribological performance.
1.
The atomic/crystal structure. Titanium is classified as a transition metal; it has two electrons in the third shell and two in the fourth shell. The electron arrangement is responsible for the undesirable tribological properties of titanium. The atomic structure (and surface hardness) can be ameliorated by bulk or surface alloying.
2.
The titanium oxide film. This film has a relatively low tensile and shear strength. When adhesive bonding occurs in rubbing contact with adjacent titanium or other metal surfaces, the fracture occurs in the oxide rather than at the interface, resulting in large amounts of corrosion/material transfer and galling. As with the atomic structure, improvement of hardness through alloying offers some improvement, but this problem can also be overcome by coating the surface with another material.
During machining, standard hydrocarbon lubricants reduce the friction between moving titanium surfaces somewhat. Lubricants and barriers such as high-pressure oils, graphite or molybdenum disulphide greases may be adequate. Other solutions include semi-permanent and permanent (glassy) coatings. Because titanium has low thermal conductivity and machining equipment can easily become overheated, there also needs to be special consideration for coolants and cutting fluids.
An Alloy Solution—NITINOL 60 (6)
Attacking the lubrication problem from the alloy side is a nickel-titanium alloy, NITINOL 60 (60NiTi). Its alloy was developed in the early 1950s by Dr. William Buehler, a Naval Ordnance Laboratory Researcher working on non-corrosive, non-magnetic alloys for aerospace, energy production and medical devices. It contains, by weight, 60% nickel and 40% titanium and holds promise for oil-lubricated rolling and sliding contact applications such as bearings and gears.
NiTi alloys are known for their shape memory. When properly processed, however, NITINOL 60 also exhibits excellent dimensional stability and useful structural properties. NITINOL 60 is hard, electrically conductive, highly corrosion resistant, less dense than steel, readily machined prior to final heat treatment, non-galling and non-magnetic. Importantly, NITINOL 60 has shown remarkable tribological performance when compared to other aerospace bearing alloys under oil-lubricated conditions.
Products made from NITINOL 60 have the following properties:
•
Better lubrication: Oils without corrosion inhibitors can be used.
•
Lower friction: The coefficient of friction is substantially reduced.
•
High hardness: Hardness from 56 to 62 RC can be achieved (
7).
•
Wear-resistance: Low friction and high hardness lead to long life.
•
Non-magnetic: Beneficial in a range of applications.
•
Non-corrosive: Salt spray tests show no signs of corrosion.
•
Reduced weight: Parts weigh 15% to 20% less than steel.
•
Higher speeds: Lighter weight reduces centrifugal forces.
•
Tighter tolerances: Super-fine grain structure achieves closer tolerances.
•
Greater efficiency: Lower weight and friction mean reduced power consumption.
Figure 3. Ion-sputtering aided XPS analysis revealed the composition-depth profile of the tribofilm on the OD-Ti64 worn surface.
LUBRICANT OBSERVATIONS
The Titanium Information Group offers the following titanium lubrication observations (
8):
1.
Spray-on Film Lubricants. A number of proprietary dip or spray-on dry film lubricants based on molybdenum disulphide or PTFE are available that provide lubricity for severe forming operations. Some of these temporary coatings are very stable and may be left on titanium until all processing is completed. Those based on molybdenum disulphide and applied at the start of a manufacturing cycle may be retained for the service life of components.
2.
Thermally Unstable Lubricants. Thermally unstable lubricants such as oil, grease and plastics must be fully removed before any intermediate or final heat treatment is carried out.
3.
Dry Film Lubricants and Surface Treatments. The combination of dry film lubricants with anodized and other surface treatments frequently provides the best longer-term solution to titanium’s adhesive wear.
IONIC LIQUIDS
The corrosion resistance of titanium is due to the formation of the oxide film. But this film is very vulnerable to acidic material such as some ionic liquid lubricants (ILs). For example, tetrafluoroborate imidazolium IL lubricants break down at the metal-to-metal contact, producing severe corrosion and forming metallic fluorides, boron carbide and boron oxide. But researchers are finding that some IL lubricants work well.
In one study, at room temperature, the best performance was obtained for 1-methyl-3-benzylimidazolium chloride ([BzMIM]Cl), while at 100 C (212 F), the lowest friction and wear values were obtained for 1-hexyl-3-methyl-imidazolium hexafluorophosphate ([HMIM]PF6). The [HMIM]PF6 lubricant forms adsorbed layers on the titanium surface and a phosphate- containing protective layer on the steel counterface (
9).
ORNL STUDIES
A series of studies were conducted between 2003 and 2010 at the Oak Ridge National Laboratory that drew many useful conclusions and made a significant contribution to the body of knowledge on titanium lubrication. These studies were led by Drs. Peter Blau and Jun Qu and sponsored by the Vehicle Technologies Program of the U.S. Department of Energy.
“We have conducted a series of fundamental studies to address the sliding friction, wear and lubrication issues of Ti alloys for potential ground transportation applications,” Qu says. “Our laboratory tribological tests on various Ti alloys have shown poor friction and wear performance in both dry and lubricated sliding, all substantially worse than baseline ferrous bearing alloys.”
Following is a summary of the five ORNL tests.
1. Friction and wear of titanium alloys sliding against metal (10). In order to establish a baseline for further studies on the tribology of titanium against various classes of counterface materials, a 2005 study looked at the effect of pin-on-disk sliding friction and wear on two different titanium alloys (Ti–64 and Ti–6Al–2Sn–4Zr–2Mo) against bearing balls composed of 440 C stainless steel, silicon nitride, alumina and PTFE.
Ceramic sliders suffered unexpectedly higher wear than the steel slider. The wear rates from the highest to lowest were: alumina, silicon nitride and steel. This trend was inversely related to their hardness but corresponded to their relative fracture toughness.
Energy dispersive spectroscopy (EDS) and X-ray diffraction (XRD) analyses confirmed the tendency of Ti alloys to transfer material to their counterfaces and suggested possible tribochemical reactions between the ceramic sliders and Ti alloy disks. The study concluded the following: A titanium alloy rotor can weigh approximately 37% less than a conventional cast iron rotor with the same dimensions while offering good high-temperature strength and much better resistance to corrosion from road-deicing salts.
2. Tribological investigation of titanium-based materials for brakes (11). In a 2007 study, friction coefficients and temperature rise data were obtained for two commercial Ti alloys, four experimental Ti-based hard particle composites and a thermally spray-coated Ti alloy. Several commercially produced lining materials were used as counterfaces. Using a flat block pressed against a rotating disc, the tests consisted of repetitive on-and-off drags at sliding speeds from 2 to 15 m/s, using nominal contact pressures of 1.0 or 2.0 MPa. The following conclusions were drawn from the results:
1.
Two Ti structural alloys, Ti64 and Ti6242, behaved similarly with decreasing friction coefficient as the sliding speed and temperature increased.
2.
Gray cast iron discs had better wear resistance than those made of Ti alloys and composites.
3.
The highest thermal heating parameters (the degree that friction is converted to heat) were observed for the Ti with thermally sprayed coating and the lowest for cast iron. The thermal heating parameter for composite materials fell in between.
4.
Relative to the Ti-containing material combinations tested, the Ti alloy discs coated by a proprietary thermal spray coating and run against a highly metallic lining material had the most promising combination of good elevated-temperature frictional response and very low wear.
3. Oxygen-diffused titanium as a candidate engine material (12). A 2009 study explored the effectiveness of oxygen diffusion (OD) case hardening on titanium surfaces that were subsequently exposed to a ZDDP-containing engine lubricant. The study reported a friction reduction of 70% and a wear reduction of up to six orders of magnitude for an OD-treated Ti64 alloy. It concluded that the OD zone was critical to the antiwear tribofilm formation as a result of the interactions between the titanium surface and the lubricant. There were two reasons:
1.
It creates a surplus of oxygen, which forms a renewable oxide interlayer believed to have higher reactivity than base metal—allowing the metal to interact with lubricant additives.
2.
The hardened oxide layer can provide a strong backing for an effective ZDDP-based tribofilm.
Figure 4. The SR-71 Blackbird was the first all-titanium military airplane. This photo was taken at NASA’s Dryden Flight Research Center. (Courtesy of NASA)
4. Oxygen-Diffused Titanium as a Candidate Brake Rotor Material (12). Another 2009 study looked at the effect of OD specifically on titanium truck brake rotors. The study was prompted by the fact that despite the advantages of light weight, good strength and corrosion resistance, titanium alloys are otherwise not satisfactory brake rotor materials because of poor friction and wear behavior relative to cast iron.
In this study, OD was applied to titanium rotors. The resulting OD-Ti64 was tested on a subscale brake tester against a flat block of commercial brake lining material and benchmarked against several other Ti-based materials, including untreated Ti64, Ti-based-metal matrix composites (Macs) and a thermal spray-coated Ti alloy. The lining material used in the tests was neither designed nor optimized for OD-Ti64.
The OD-Ti64 disk produced an appropriate friction coefficient level (0.35–0.50) with excellent fade-resistance. It had the best braking performance among the tested Ti-based materials. These tests showed that the OD process improved the wear resistance of titanium by 40 times. The OD-Ti64 disk had a lower wear rate compared with Ti MMCs.
5. Surface engineering for improved durability and lubricity of Ti–6Al–4V alloy. As mentioned earlier, titanium alloys have a tendency to fail by galling and often exhibit high and unstable friction coefficients. In a 2011 study, selected surface engineering techniques were compared to determine which best enhance the tribological performance of a Ti64 alloy and a 60Ni–40Ti alloy (
13). Test treatments included diffusion, hard coatings (TiN and CrN), a soft coating (Cu–Ni–In), titanium- matrix TiB2 in situ-formed composite and shot peening with AISI 52100 bearing steel (
14).
Diffusion treatments included oxygen diffusion, nitriding and carburizing. In addition to studying the effects of individual surface engineering approaches, some were combined in an attempt to maximize their effects but at the same time retain the mechanical properties of the titanium alloy resulting from proper heat treatment. Both dry and lubricated friction and wear tests were conducted. Lubricated tests were performed in engine-conditioned diesel engine oil and the following conclusions were drawn:
1.
The difference between passing and failing was distinct— the materials and surface treatments clearly fell into a specific category. The successful treatments yielded friction coefficients less than 0.15 while the treatments that failed had friction coefficients greater than 0.26.
2.
CrN-coated Ti64 specimens had the least amount of wear, followed closely by DLC-coated Ti64 specimens.
3.
Nitrided and OD-treated specimens yielded the lowest friction coefficients and their wear was also comparable to those of CrN and DLC-coated specimens.
4.
For some treatments (such as the carburized surfaces) test-to-test repeatability was an issue. Transitions to severe wear were not repeatable, and the issue of consistent behavior was a cause for rejection of that particular treatment.
5.
Various wear modes were exhibited by the materials tested with three-body abrasive wear, pitting or coating fracture and adhesive wear being the most common.
6.
The ratio of the wear of the ball specimen to the flat specimen differed from one material couple to another, and must be considered in the context of the tribosystem.
7.
Tests in lubricants of other types may produce different rankings, since the lubricant used in lubricated tests contained soot, acids and possible engine debris.
Titanium alloys are currently used and successfully lubricated in limited aerospace applications—one proven methodology is a mitigation strategy for fretting wear. Hager explains, “Typically the surfaces are thermal sprayed with a soft metallic coating and then a bonded solid lubricant is applied on the surface of the thermal sprayed coating. The metallic coating is often an aluminum bronze alloy or a copper nickel indium alloy. The surface solid lubricants are often molybdenum disulfide in an epoxy binder or graphite in a silicate binder.”
Figure 5. Researchers at NASA’s Jet Propulsion Laboratory and the California Institute of Technology developed an amplifier for boosting electrical signals from space. It is made of a superconducting niobium titanium nitride coiled into a double spiral 16 millimeters in diameter. (Courtesy of NASA/JPL-Caltech)
CONCLUSION
With the processing issue largely under control, attention continues to turn toward solving the remaining lubrication issue. The ORNL studies and other studies have proven that effective lubricants for titanium alloys do exist. The challenge is translating these findings into mainstream engineering and manufacturing processes that will enable titanium alloys to transform the trucking, automotive and many other industries.
“There is no universal surface treatment or coating that fits in all systems,” Qu says. “Each system has to be tested and analyzed case-by-case.”
REFERENCES
1.
From
here.
2.
Rutile is a titanium and oxygen mineral.
3.
Porsche and Ferrari currently use titanium alloys in some engine components because of its ability to withstand high stress performance.
4.
From
here.
5.
From
here.
6.
From
here and
here.
7.
RC = Rockwell Hardness, a hardness scale based on the indentation hardness of a material.
8.
Ibid
9.
From
here.
10.
J. Qu, P.J. Blau, T.R. Watkins, O.B. Cavin and N.S. Kulkarni (2005), “Friction and Wear of Titanium Alloys Sliding Against Metal, Polymer, and Ceramic Counterfaces,”
Wear,
258(9), pp. 1348-1356.
11.
P.J. Blau, B.C. Jolly, J. Qu, W.H. Peter and C.A. Blue (2007), “Tribological Investigation of Titanium-Based Materials for Brakes,”
Wear,
263(7-12), pp. 1202-1211.
12.
J. Qu, P.J. Blau and B.C. Jolly (2009), “Oxygen-Diffused Titanium as a Candidate Brake Rotor Material,”
Wear,
267(5-8), pp. 818-822.
13.
D.G. Bansal, O.L. Eryilmaz and P.J. Blau (2011), “Surface Engineering to Improve the Durability and Lubricity of Ti–6Al–4V Alloy,”
Wear,
271(9-10) pp. 2006-2015.
14.
Shot peening is a cold-working process that entails bombarding a surface with shot pellets at a force sufficient to create deformation.
Jean Van Rensselar heads her own communication/public relations firm, Smart PR Communications, in Naperville, Ill. You can reach her at jean@smartprcommunications.com.