Evonik Oil Additives
Pour Point Depressants in Food Applications
By Jen-Lung Wang, Global Business Manager, Wax Modifiers, Evonik Oil Additives | TLT CMF Plus November 2012
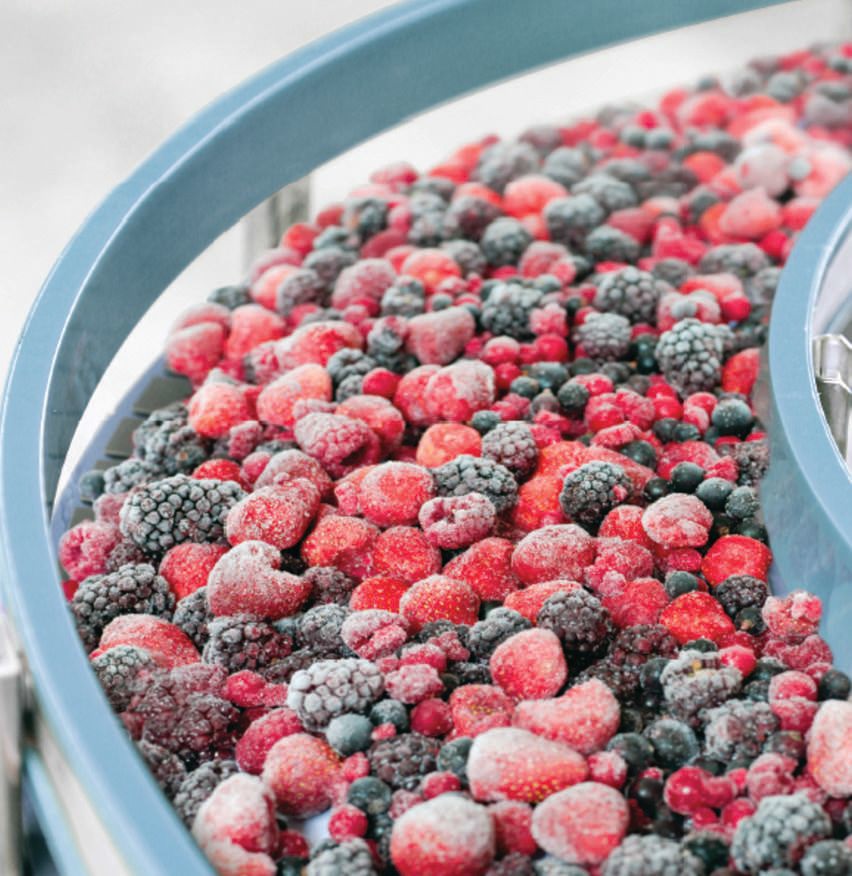
Lubricants are vital in many areas of the food-processing industry: in processing meat, poultry, and fish; in bottling, brewing, and distilling; in baking, frying, and canning; and in coating, packaging, and freezing fruit and vegetables. Without lubricants, commercial food processing would be impossible. A good food-industry lubricant needs to reduce friction and wear, prevent corrosion, rust, and oxidation, enable “no-loss” food processing, and maintain its fluidity at both high and very low temperatures. Additionally, a good lubricant should be easy to handle, anti-fungal, anti-bacterial, and of course, cost-effective. Responsible food processors are careful to use only lubricants registered with the National Sanitary Foundation (NSF®) International, to ensure food safety and to maintain NSF certification.
In 1999, based on the original USDA guidelines, NSF launched the food grade lubricants and additives registration program, which authorizes registration of products processed in accordance with its standards. NSF registration requires the use of lubricants designated H-1 for all applications where there is any chance of incidental contact with food. No additives may be used in H-1 lubricants unless they are designated HX-1 by the NSF. H-2 lubricants are approved for use in the food industry only in applications where there is no possibility of contact with food.
Most NSF H-1 food-grade lubricants that are commonly used have synthetic base stocks such as poly-alpha-ole fins (PAOs) and polyalkylene glycols (PAGs). These synthetic lubricants are favored because of their comparatively high viscosity index, good cold-temperature fluidity, low toxicity, and other characteristics. However, such synthetic food grade lubricants tend to be expensive, leading to overall high formulation cost. Consequently, formulators are faced with the challenge of developing cost-effective H-1 food grade lubricants with all of these highly desirable properties.
Two alternative base stock categories for H-1 food-grade lubricants are the paraffinic white oils and the Group III oils, both of which are extremely low in toxicity and are reasonably priced. While white oils and Group III oils have good low temperature properties, there is still room for improvement in accommodating the broad operating temperature range encountered in food processing applications. Consequently, Evonik Oil Additives has developed a cost-effective and highly efficient solution to the challenge of improving low temperature performance in H-1 food grade lubricants – a food-grade, NSF-certified pour point depressant identified as VISCOPLEX® 1-135.
All paraffinic mineral oil, including white oils and Group III base stocks, contain small amounts (normally a few percent) of waxy materials. As the temperature of oil decreases, some of the waxy components come out of the solution as tiny crystals, and the solution begins to appear hazy to the naked eye. As additional wax precipitates, the crystals grow in to plates, and the plates will grow together to form a three-dimensional network if the temperature is sufficiently low for an ex tended period of time. This solidification process is sometimes referred to as gelation. While the wax matrix resulting from gelation is quite fragile and can easily be destroyed by shaking or stirring, if not treated, the entrapped oil in a stagnant environment, such as an oil sump or reservoir, can very well restrict pumpability and filterability, thereby placing a lower temperature limit on the utility of the lubricant.
Pour point, defined as the lowest temperature at which the oil mixture will still flow, is a simple method to predict oil low temperature fluidity. Materials that depress pour point of the oil are designated pour point depressants. Over the years, a wide variety of synthetic materials has been introduced commercially as pour point depressants, including poly alkylmethacrylates (PAMA), polyacrylates, acrylatestyrene copolymers, esterified olefin- or styrene maleic anhydride copolymers, alkylated polystyrene, and vinyl acetate-fumarate copolymers. Among all the chemistries, polyalkylmethacrylates were the first of the polymeric pour point depressants to be developed, and they remain, by far, the best chemistry available today, with a worldwide market share that far outstrips the alternatives. The reasons for this predominance focus on the molecular structure of the polymers and the tremendous flexibility available in its chemical composition. Polyalkyl methacrylate (PAMA) pour point depressants prevent the build-up of paraffin crystals in lubricants at cold temperatures by providing seeds for wax crystallization. The protruding saturated alkyl branches that recur along the length of the PAMA polymer are similar to the wax structure in the oil and can co-crystallize with the wax instead of forming a three-dimensional agglomerate. These mini-crystals or crystallites, as they are called, are attached to the PAMA chain and thus are unable to coalesce into a three-dimensional network. As a result, they have much less effect on the flow or lubricity of the oil, so that it can flow at temperatures much lower than that at which untreated oil would be practically solid.
With its VISCOPLEX® PPDs, Evonik Oil Additives is recognized as both a pioneer and the leader in PAMA-based pour point depressant technology. Its 70-plus years of research and development experience in lubricant cold-temperature rheology and product application have produced an impressive level of expertise and know-how.
VISCOPLEX® 1-135 pour-point depressant is the latest PPD product developed by Evonik Oil Additives specifically for use in food-grade lubricants formulated with white oil and Group III base stocks. VISCOPLEX® 1-135 pour-point depressant is certified by NSF as an HX-1 additive for H-1 food-grade lubricants and is produced according to good manufacturing practices (GMP) at Evonik Oil Additives’ manufacturing site in Lauterbourg, France. It is also both Kosher-approved and Halal-certified, to ensure its applicability across a broad range of food processing lubricants. VISCOPLEX® 1-135 pour point depressant is particularly active in white oils and in Group III oils, with treat rate levels of up to 1.75 wt%, but more typically in the range of 0.2- 0.5 wt%. VISCOPLEX® 1-135 pour-point depressant can lower pour points by as much as 12-27°C for white oils and as much as 12-15°C for Group III base stocks, which usually have lower pour points. It can even lower the pour points of vegetable oils, such as sunflower and soybean oil, by as much as 3-9°C. Because of its powerful ability to deter the agglomeration of paraffinic wax crystals, VISCOPLEX® 1-135 pour point depressant also dramatically reduces the Brookfield Viscosity of white oils at very low temperatures.
Evonik Oil Additives VISCOPLEX® 1-135 pour point depressant extends the low temperature operating range in white oils and Group III oils based H-1 food grade lubricants, enabling these base oils as cost-effective, non-toxic alternative to synthetic base oils for food processing lubrication. The combination of NSF-certified H-1 paraffinic base stocks with the VISCOPLEX® 1-135 pour point depressant yields a clean, high-performance food-grade lubricant that keeps food processes in motion around the world.
More information on the benefits of the VISCOPLEX® 1-135 pour point depressant can be found at evonik.com/oil-additives.