Teach, don’t punish
Peter A. Oglevie | TLT Shop Floor October 2012
When it comes to safety training, personnel must understand the reasons why you have established policies and procedures.
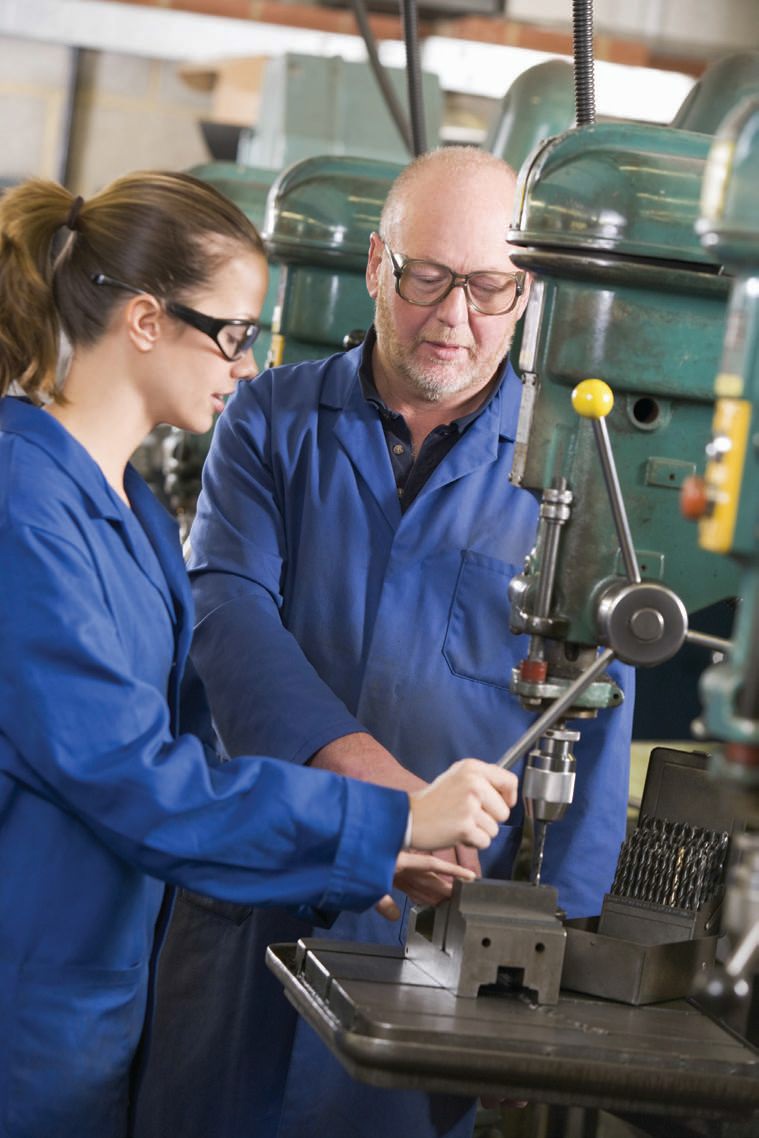
Be prepared to adapt your training methods to the student’s learning style.
www.canstockphoto.com
I have lots on my mind this month. I spent time wondering about the sailboat race my team just finished, watching the Coast Guard look for a body in the lake and contemplating what it all means. My thoughts turn to the family of the young man lost in the lake. I’m sure this young man had swum in this spot many times, and no one expected the tragic outcome. However, this particular spot should have been posted as a No Swimming area due to conditions that occur after strong northeast winds.
So what does this have to do with the shop floor?
This month I want to go back to basics. The shop floor is not a place we should take lightly. Much like the lake I sail on and people swim in, what we do on the shop floor affects the health of shop floor operators, profitability of companies and the well being of the end-users of the products being produced. With all this at stake, shouldn’t we spend the little time it takes to train shop floor personnel basic procedures?
Let’s start with what we want a training program to accomplish. Do we want to teach proper use or punish shop floor operators? The goal should be to teach, not punish. If an operator doesn’t get the lesson, teach him again.
A good training program is ongoing and non-punitive. While you need to offer a platform for learning, recognize that not all people learn the same way. Be prepared to adapt the training methods to the learning style of the student.
I like to explain the purpose for the training session up front. I still remember asking my first foreman why something had to be done that way and getting the response, “Because I said so.” That kind of a response never sets well with me. If he had said, “We need to keep this concentration level to avoid that ugly smell in the machinery,” I would have followed the procedure with pleasure.
Next, remember the KISS rule (keep it simple stupid). Do not baffle the shop floor operators with your brilliance; that’s not the goal. Simply teach the lesson at hand. For instance, if you want to teach how to control concentration on a coolant, have titration kits or refractometers in the classroom. Show them how to use the equipment properly.
Measure your progress. At the end of a training session, give students a quiz on the subject matter. Grade the quiz with the students and make sure to go over each question that was answered improperly. Explain the mistake. Remember the goal is to teach, not punish.
Keep the quiz on file. If down the road the problem comes up on the shop floor, note this in the file and require another training session. This will usually take care of the problem. However, not all people are cut out for shop floor work and may never get it. If nothing else, following these steps gives you a sound legal basis for dismissal.
Finally, post signs or progress reports for inspection. For instance, if we are taking the time to measure the concentration of a product, we should have a chart visible showing these readings. Call this the warning sign. If I walk up to a machine and check the chart, I know where we are. If I check the machine concentration and find a discrepancy, I need to work on training. You can learn a lot about what is happening simply by having a sign.
On the sailboat we race, we do not have a sign saying we must wear a life vest. However, sailing association rules require all personnel on board to wear a life vest, and everyone on the team wears them. The reason is that sailboats have a part called a boom that can cause a head injury. If you are unconscious, you cannot swim.
The beach where we lost the young man will get a new No Swimming sign soon, I’m sure. I guess a higher authority forgot the lesson I am trying to make: teach, don’t punish. Explain why. Keep it simple. Measure your progress. This young man just might have saved future tragedies from occurring.
Pete Oglevie is president of International Production Technologies in Port Washington, Wis. You can reach him at poglevie@wi.rr.com.