Static Discharge
Jean Van Rensselar, Contributing Editor | TLT Feature Article September 2012
It’s an old problem with a highly effective new solution.
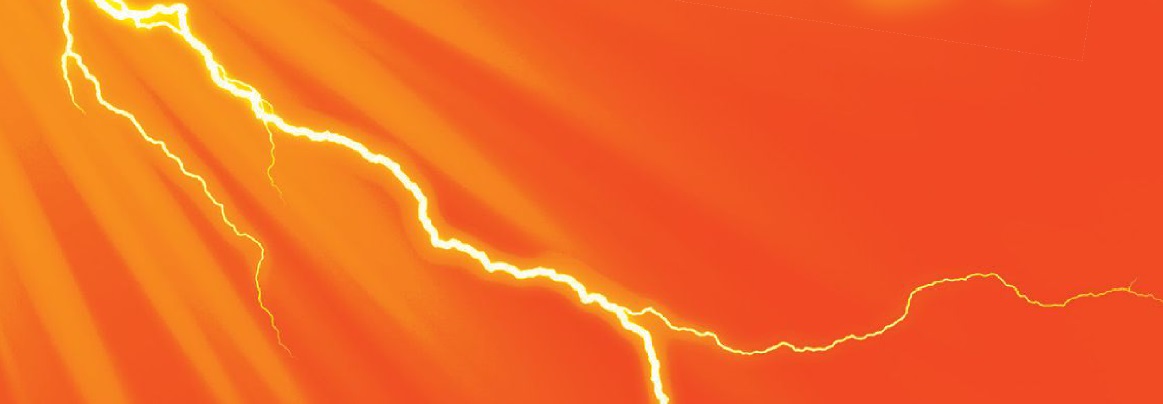
www.canstockphoto.com
KEY CONCEPTS
•
Static discharge can cause damage such as surface etching.
•
The oil filtration process is one of the prime catalysts of static.
•
Filter advances promise a solution.
Charge generation is the result of the triboelectric effect or static electricity—the friction that occurs when certain surfaces come in contact with each other. The power and
polarity of the charge depends on the types and properties of materials involved and also properties such as the temperature or humidity of the surrounding environment.
When static discharge occurs in oil, it leads to thermal breakdown, which leads to oxidation, which leads to polymerization. The oil often becomes more acidic and visibly darkens. In addition, it can cause metal particles to flake off and deposit in the oil. If the charge is strong enough, it will pit surrounding metal. None of this is good.
The oil filtration process is one of the prime catalysts of static electricity. Equipment operators know it’s taking place because of the clicking sound they hear when the fluid passes through the filter. If the electricity discharges to a grounded surface, it damages not only the filter but also more costly system components. Static discharge is also dangerous—the cause of electrical explosions, fatalities and injuries.
STLE-member John Duchowski, director of technology development for HYDAC, says, “In very simple terms, the fluids charge because they are exposed to a surface of dissimilar material, such as the filter cartridge, and surfaces of system components such as pipes and hoses. However, because the filter element presents the largest surface area, most of the charging occurs at the filter element.”
Researchers have looked at several methods for reducing static discharge and preventing the damage it causes. These methods include antistatic additives and modifications to the filter. The goal is to eliminate damage to the filter and prevent (or significantly reduce) charge migration into the fluid.
Oils that are highly refined and have few additives (more likely industrial than hydraulic oils) are less conductive; oils with a prevalence of metal-based additives will be highly conductive.
Because most industrial operations involve separation processes that induce a charge, electrostatic charge is common for solids and especially liquids, which are also charged during stirring, spraying and atomization.
STATIC DISCHARGE CAUSES
Electrostatic charge is produced when two surfaces move in relation to each other—this usually means they must come in contact with each other but not always. Akira Sasaki, a founding member and former managing director of KLEENTEK Corp., current principal of Maintek Consultant and an STLE Fellow, says, “It is generally considered that triboelectricity is generated by friction caused when oil comes in contact with a metal surface. But the facts show that the generation of triboelectricity with oil is not by friction but by electrical double layer (
1).”
When a fluid flows on the surface of a solid, the charge will be separated and the different charges will appear on the fluid and the solid, respectively, at the place where the different materials meet. The positive or negative charge that is generated by the moving fluid will migrate from the fluid to the surface it comes in contact with—the charge separation appears just when the two materials are separated. The charge is generated when two materials contact but will not appear as long as they are not separated. Causes of electrostatic charge in a system include one or more of the following:
•
Fluids passing through filters.
•
Fluids that travel through systems at high speeds and/or are highly agitated.
•
Fluids that are kept at lower temperatures.
•
Fluids that become aerated.
STLE-member Gerald Munson, chief technology officer at Fluid Assets, LLC, adds that the double-layer phenomenon and induced charging also exist for metal fluid paths in machinery that is lined with an insulating coating (e.g., paint or Teflon™).
Kal Farooq, senior staff engineer with the Scientific & Laboratory Services Group of Pall Corp., explains, “Static discharge is a common problem in fluid pumping/handling systems due to the presence of a moving liquid surface against other surfaces such as the pipes, tubing and fibers of the filter element. The build-up of the charge to levels that cause the discharge (sparks) and the associated damage is influenced by the conductivity of the fluid and the surface it is in contact with, along with the magnitude of the surface area in contact, fluid temperature, its velocity, cleanliness and viscosity.”
If the surfaces are either not capable of conducting electricity or grounded, the charge will build up and discharge. This generates an electrostatic discharge to a surface of lower voltage. If the resulting spark occurs outside the system, it is both visible (sometimes spectacularly) and potentially dangerous.
Figure 1. Burned Breather Filter. (Courtesy of HYDAC)
FILTRATION-CREATED STATIC
One of the primary causes of static discharge in lubricants is filtration. Because most lubricants are not highly conductive, the charges run downstream without depositing along the surface walls and accumulate. If enough charge accumulates, the fluid will discharge to a conductive part of the filtration system and either damage it or discharge into the ground. The extent of damage depends on a number of factors including the materials involved.
“Since filter cartridges have a large surface area and typical filter media made with glass fibers or other non-conductive fibers tend to generate a high charge, the problem of static discharge is common in filtration systems,” Farooq says. “The charge is generated at the fluid/filter interface. This results in a net positive or negative charge at the filter and an opposite charge imparted to the fluid. The charge carried by the fluid can accumulate on downstream surfaces.”
If the filter is made of nonconductive material, the charge cannot dissipate into the filtration system. Then the filter will charge until the voltage reaches a certain point and discharge to conductive parts such as the metal components of the filter housing—where significant damage can occur. In addition, the filter’s constant charging/discharging along with constant fluid flow can severely damage the filter fibers. While grounding the filter system prevents sparking, it does not prevent either the filter or fluid passing through it from charging and causing damage.
“This problem occurs mostly where large surfaces of two dissimilar materials come into contact with each other,” Duchowski says. “Because in hydraulic and lubricating systems, the filter elements represent the components with the largest surface area, most of the charging occurs there. Both the filter element and the fluid acquire charge. With the usual hydrocarbon-based fluids found in most hydraulic and lubricating systems, the filter element acquires a positive charge whereas the fluid acquires a negative charge.”
STATIC DISCHARGE EFFECTS
Electrostatic discharge usually produces a clicking sound as the charge repeatedly increases and discharges to surfaces of lower voltage through sparking. The clicking frequency depends on the charging rate—the louder and more frequent the clicking, the bigger the problem. The discharge can result in etching of the surface to which it discharges. This may cause microscopic particles to flake off and it may also leave surface carbon deposits. Discharge that results from lubricated surfaces with high air content tends to cause pitting. If the discharge occurs in a flammable environment, it can be hazardous.
Farooq explains, “Sparks generated by the discharge generate very high localized temperatures, on the order of 10,000 C, which literally burns the fluid, cracking the molecules and forming free radicals that further promote fluid degradation through additive depletion and oxidation. The end result is accelerated fluid degradation, elevated levels of oil-insoluble materials such as carbonaceous particles and varnish-forming, resinous material.”
Figure 2. Electrostatic Discharges in the Filter Element. (Courtesy of HYDAC)
DANGEROUS IGNITIONS
“When spark discharges occur in oil, it will not directly cause a hazardous fire because the oxygen in the oil is negligible,” Sasaki says. “However, those spark discharges will crack oil molecules and produce free radicals. The free radicals will then initiate a chain reaction of oil oxidation. When spark discharges crack oil molecules, hydrogen gas and low molecular weight hydrocarbon gas will be produced. If they are mixed with oxygen in the air in an oil tank and spark discharges were caused in the mixed gases, an explosion can occur. This is because static electricity may be stored on the surface of oil in an oil tank.”
He adds, “However, there is usually no risk of explosion, as the charge of the oil in the oil tank is released to the metal surfaces adjacent to the oil from time to time or it is relaxed before it accumulates to the level of causing spark discharges.”
The crucial factor in determining the level of danger from an electrostatic charge is the probability that an explosive atmosphere and a high charge will occur at the same time and place. Dangerously high charges can occur while processing nonconductive, combustible fluids such as hydrocarbons and other nonpolar solvents. But conductive substances also can accumulate dangerously high charges if they are processed in nonconductive machinery.
During the manufacturing process, both the lubricant and the machinery are capable of becoming charged and retaining the charge. While the amount of electricity produced by static electricity is relatively small, under extreme conditions (such as high processing speeds) dangerously high currents capable of producing an ignition can occur.
Either some or all of the energy stored in the accumulated charge can be released during a discharge. In the latter case, a high-energy discharge can ignite a potentially explosive atmosphere. Charged, insulated, conductive substances can be ignited by spark discharges and are responsible for most of the ignitions of potentially explosive atmospheres by static electricity in industrial environments.
“For the static discharge-generated spark to be a fire hazard requires the presence of the right mix of fluid vapors and air and enough energy in the spark to initiate and sustain the ignition,” Farooq says. “Discharge activity (sparks) within the fluid phase such as inside the filter housing or under the fluid surface inside the reservoir is not considered a fire hazard. Lube system design should prevent the build-up of oil mist to critical levels and eliminate the possibility of severe sparking in the reservoir. Depending on the application, a non- or low-flammability lubricant may be required.”
Duchowski says, “The issue of flammability is a very important, even critical one. Already in several instances, we have observed either explosions or fires that occur as a result of electrostatic discharge within hydraulic and lubricating systems. This can occur for different reasons and under different circumstances.”
Duchowski uses this example: If the lubricating oil is used in an application where it comes in contact with flammable gas (which ends up being dissolved in the oil due to diffusion such as in natural gas compressors) and if enough charge remains in the oil where it can cause arcing in the reservoir, there is a very high probability of explosion. This is especially true if a combustible mixture is present in the reservoir air space above the fluid (as it usually is since the natural gas effusing from the oil in the tank ends up mixing with air above the oil surface).
“Sometimes flammable gas is not even required; it is enough for the finely dispersed oil mist to be present in the reservoir airspace for fires and explosions to occur,” he adds. “However, in most of these applications, the use of nonflammable lubricants is not the answer, because these are often water glycols or phosphate esters that are incompatible with system components such as pumps and seals and are often not suitable from the point of view of operational system requirements. The answer lies in the choice of a suitable filter element.”
Figure 3. HYDAC Electrostatic Test Bench. (Courtesy of HYDAC)
PREVENTING, REDUCING, ELIMINATING STATIC
Environmental concerns have resulted in the increased use of oils with nonmetallic antiwear additives. While these oils may have lower conductivity, the lower conductivity means that the charge generated is more likely to accumulate and discharge destructively.
Because the majority of filters are made with the supporting core contained within the housing, not the element (for easy disposal), there is an increased use of charge-inducing polymers. The combination of lower conductivity and higher accumulated charge results in greater static discharge. This increased static discharge prompted Pall Corp. to investigate the subject and research filter materials that would yield a lower charge.
While using a grounded filtration system will prevent the system from sparking to nearby conductors, grounding the system will not keep the filter material or fluid from charging, nor will it accelerate discharge. Past attempts to reduce the potential of static charge accumulation included:
•
Adding an antistatic additive to the fluid. The additive raises the conductivity of the fluid and accelerates the rate of charge dissipation but is usually added to fuels, not lubricants. Antistatic additives have not been approved for use in hydraulic and lubrication systems.
•
Reducing the charge exiting the filter. This was accomplished by using a static charge reducer (SCR)—a passive device that injects a charge of the opposite polarity into the charged fluid during flow. This was a less-than-ideal solution because of the lag time before the effects kick in and the fact that the SCR became contaminated by conductive layers, making it ineffective.
•
Reducing the filter’s flow volume. This was accomplished by increasing the filter size. While this is a simple and effective solution, engineering considerations make it impractical in many cases.
•
Creating more time for the charge to dissipate. This was also an effective but impractical (and costly) solution since it required re-engineering the system to increase the distance of the fluid route and/or adding a reservoir.
•
Adding a grounded conducting surface. While this creates better conditions for discharge and seems to reduce or eliminate surface damage to materials, it doesn’t solve the basic problem of fluid charging.
The only practical way to effectively keep the filter and fluid from charging is to reduce the charge generation at its source (during filtration). Experts say this means altering the filter components.
Farooq explains, “Factors that affect static charge generation and dissipation can be manipulated to address the problem. One of the most effective and easily implemented solutions is the use of filters made with media that generate a lower charge and dissipate the charge effectively and rapidly before it builds up to high enough levels to cause discharge.”
“It is important to note that these (or any other) filter elements do not filter out or neutralize charge that might be formed by other system components,” says Duchowski, whose company, HYDAC, is one of a handful that offer a charge-reducing filter. “What they do is minimize the charge separation behavior that occurs at the interface between the filter element and the oil.”
Figure 4. Thermal image of the Local Hotspot in the Hydraulic System Oil. (Courtesy of HYDAC)
THE PALL STUDY (2)
The Pall Corp., developers and manufacturers of filters and filtration systems, wanted to investigate the effects that different filter materials would have on hydrocarbon fluid charge generation.
In order to test these effects, Pall technicians created two test setups. They built the first with a nonconductive housing to isolate the filter material from the rest of the system and built the second to test the charge generated by filter cartridges—in order to more closely mimic in-field working conditions.
Using both test stands, they tested different filter materials in several different oils to determine the difference in charge generation and material damage. They selected oil that represented the largest possible sample of available oils with characteristics believed to affect the rate of charging.
The main oil used in testing was a Group I, R & O turbine lube oil (due to its high dielectric strength and low conductivity). They also used a synthetic POA-based oil (MIL H-83282).
The first test set used flat sheets of three different types of filtration materials in the isolated filter housing. The first material was the standard glass-fiber-based (GF) filtration material, which is similar to glass-fiber-based filters used for lubrication oil.
The second material was surface-modified glass-fiber- based material, and the third was a proprietary electrostatic dissipative (ESD) material developed by Pall laboratories. They conducted the analysis using five different oils, measuring the charge generated on the filter material.
For the first test set, only Group I turbine lube oil was used (because of its representative characteristics). The results showed that the standard GF material generated a current more than double the charge generated by the surface-modified GF material. The new ESD material generated a current that was significantly lower than both.
Pall study field tests (3)
•
Field Trial 1: This measured the downstream charge on a hydraulic system at a transformer radiator manufacturing plant. The cartridge charge collector setup was connected to a port on the filter housing downstream of the filter media. Visual and auditory tests were also conducted in the reservoir because plant workers had complained about sparking in the reservoir that they believed was caused by electrostatic discharge at the filter/fluid interface. Both the ESD and the standard glass filters were tested. Tests showed that the ESD material reduced the downstream oil charge to a negligible amount and completely eliminated the noticeable discharge within the reservoir.
•
Field Trial 2: This set of tests was conducted on an injection-molding machine hydraulic system involving three separate styles of filter media: standard glass material, standard glass material with a conductive mesh and the new ESD material. The tests were performed with the cartridge charge collector connected to the downstream port of the filter housing. The testing also included visual examinations for possible effects of electrostatic discharge, as well as auditory tests.
Both the visual and auditory tests checked for phenomena caused by discharge from the filter element to the grounded housing. The standard glass filters were the only ones that exhibited either clicking sounds from the filter housing, and/or visible burn marks on the plastic end caps of the filters.
In addition, the standard glass filter showed a downstream potential of 12V-14V. The new ESD material was the only one that showed lower voltages than the standard glass fiber with 4V-5V measured, while the glass filter with conductive mesh was measured at 14V-16V under the same conditions.
•
Field Trial 3: Testing was arranged at a paper mill on a hydraulic system. Tests were run using both the glass filter material with conductive mesh and the ESD filter material. The cartridge charge collector was used, and the downstream voltages were measured at different flow-rates through the collector at the same system flow. At the maximum flow measured, the ESD filter showed a 98% reduction in the voltage measured downstream. The data taken was commensurate with data obtained in earlier lab testing under similar conditions.
•
Field Trial 4: The fourth set of tests was run at a power plant on a power generation lube system. Testing was done on a different type of glass filter than previously tested (supplied by a different manufacturer). This new glass filter had a metal gas-plasma-treated glass fiber mesh downstream of the filter material. Two different grades of the filter were used: β15 ≥ 200 and β41 ≥ 200. Both of these are much coarser then the ESD filter tested previously, β3 ≥ 200, per ISO 16889.
The current generated by the ESD material was not affected by heat treatment, while the current generated by the other two samples was significantly increased by the heat treatment. The test was then run again using different oils to determine how they would compare to the Group I turbine lube oil, and if the new ESD material would follow the same charging patterns.
The results from testing the filter material in the isolated system were the basis for the testing that was started using pleated elements in the practical grounded system.
With the grounded cartridge filter test stand, two different types of filter setups were tested: (1.) the flow either started outside the filter and worked its way into the grounded metal core (out-to-in) or (2.) the flow started inside the filter and worked its way out to the grounded metal support sleeve (in-to-out). The tests studied the effect of flow rate on the charge generated downstream of the filter media. A different type of filter housing was then used to measure the charge generated in the downstream oil by out-to-in type filters.
Cutting-Edge Electrostatic Testing
HYDAC has developed an in-house testing methodology that measures electrostatic charging, both at the filter element and in the oil downstream of the element. This technology also allows for better, although not yet exact, comparison against laboratory-derived data.
The sensor (used for field measurements) is an in-house developed, engineered and manufactured voltage transducer based on HYDAC’s proprietary design. It is easily adaptable to fit into nearly all fittings and, consequently, allows for direct voltage measurements in close proximity to the oil’s filter element. This provides the most accurate readout—before the charge has any possibility of dissipating.
In addition, HYDAC’s Stat-Stick® easily interfaces with the company’s portable data acquisition unit. For more detailed investigations, Stat-Stick also can be connected via a high-voltage probe to an oscilloscope where the electrostatic signal can be stored and analyzed for more complete characterization of the charging behavior.
Pall personnel conducted field performance trials at four different locations, each having different systems, utilizing different flow conditions and different oil types with different additive packages. They tested with various combinations of filter materials in order to rate them in terms of their charge generation value and compare their performance to the ESD material. The materials selected were glass fiber material from several manufacturers: glass filter material with a fine conductive mesh, and two grades of standard glass filter material with a metal mesh. The study concluded the following:
1.
Due to the potential for discharging, electrostatic charge may be a problem in the filtration process whenever hydrocarbon or other nonconductive fluids pass by nonconductive filtration material.
2.
Using grounded filter housings and pipelines is a preventive safety measure that can reduce the external discharging, but it does not stop either fluid charge generation or internal damage to the filter or other system components caused by sparking.
3.
According to study results, experimental analysis of electrostatic charging in glass-fiber-based material filtration with different types of lubrication oil suggests the following:
a.
All standard glass fiber filters exhibited electrostatic charging characteristics, regardless of the manufacturer.
b.
Mineral oils generate positive charge on the filtration materials and a negative charge is carried downstream by the oil. Synthetic oils showed the opposite, negative charge on the filtration material and positive charge in the downstream oil.
c.
In the practical filtration system with grounded piping and filter housing, a significantly higher downstream oil charge was observed. This occurred in the filtration of lubricating oils with a high dielectric strength and very low conductivity (10-40 pS/m).
d.
The filter materials that showed a higher charge generation in the isolated system also showed higher charge and material damage in the practical filtration system with grounded filter housings and pipelines.
e.
Surface-modified conventional glass fiber materials showed significant charge reduction and lower potential material damage compared to the standard glass fiber filtration material. However, the surface modification alone was not enough to prevent material damage completely.
4.
The electrostatic dissipative (ESD) filter was developed to eliminate potential ESC problems in filtration of hydrocarbon fluids by preventing or significantly reducing both charge generation and its accumulation. With the ESD filter, a low conductivity fluid passing through the filter didn’t cause any material damage, and the charge measured in the downstream fluid was significantly lower than the charge generated through filtration with standard glass fiber materials.
5.
Field trials showed successful performance of the ESD filter material and correlated well to the laboratory tests.
Figure 5. Samples of Air-Free Oil and Aerated Oil. (Courtesy of Dr. Akira Sasaki, Maintek Consultant)
This study is one of several that offer irrefutable evidence of the efficacy of static-inhibiting filter materials. Because of the work of organizations such as Pall and HYDAC, the costly and dangerous effects of static discharge may be greatly diminished.
Static discharge has been a significant problem in many industrial environments for decades—damaging or destroying machinery and creating dangerous working environments. Altering the filter material to reduce static discharge is an elegantly simple and relatively inexpensive fix. All that remains is addressing a few glitches.
“The old adage ‘an ounce of prevention is worth a pound of cure’ perfectly summarizes the situation,” Duchowski says. “As a result of our research in this area, we have brought about significant decreases in the observed charging behavior. But our work isn’t over yet.”
REFERENCES
1.
“Electrical Double Layer” refers to two parallel layers of charge that exist at a surface.
2.
See full study methods, results and conclusions
here.
3.
Field trial details
here.
Jean Van Rensselar heads her own communication/public relations firm, Smart PR Communications, in Naperville, Ill. You can reach her at jean@smartprcommunications.com.