Small sources, significant savings
Peter A. Oglevie | TLT Shop Floor August 2012
Something as simple as running an air compressor efficiently can pay big dividends on the bottom line.
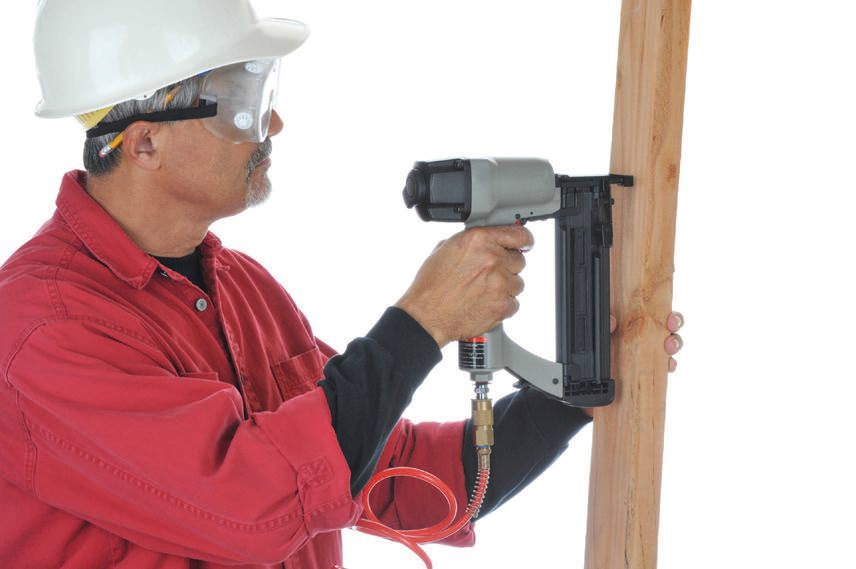
Air compressors serve all sorts of functions at home and on the shop floor, but a 1/16-inch line leak costs about $600 per year.
www.canstockphoto.com
IT’S SUMMER, AND I AM BREAKING OUT the construction equipment for the house projects. Drills, hammers, sledge hammers, jack hammers, Sawzall, mudding tools and the always-present coal shovel to clean up. As the destruction phase finishes, things start to get fun. I get to put the pieces back together. This means getting my air compressor and air storage tank out of the basement and attaching it to my finish nail gun. The other day I was walking around the new living room shooting nails into the baseboard trim to the sound of “Sweet Home Alabama.”
So what does this have to do with the shop floor? My answer is simple: compressed air. Several articles in this issue of TLT focus on energy savings and condition monitoring. I can think of no better area to apply what we do to the shop floor than the air compressor.
First, let’s set the background for just how important compressed air is for operations on the shop floor. Compressed air is used to eject parts from machinery, run air tools, operate brakes to stop machines, run press feeders, power clutches to start machines and countless other ways. So air is as necessary to a shop floor as it is for the tires we drive on. If you want to get into trouble in a shop, shut down the compressed air system. Problems like moisture and contaminants in the oil will keep you on your toes. Sound like a great application for condition monitoring.
Second, let’s look at the cost of compressed air. Even air is not free. The cost of running a 100-hp air compressor, for the sake of argument, is roughly $56,000 per year at .08 per kWh. Of this 12% would be for maintenance, 12% for the equipment and 76% for energy consumption. When you consider that compressed air is only about 40% efficient in the first place, you start to wonder why we use it. Unfortunately, we just do not have a better alternative. My nail gun, for instance, runs on air and saves me time and personal energy. I can do the trim work in a day; using the old hammer and punch would take me a week. My costs run about two drops of good airline oil a day and one dollar in electricity.
On the shop floor, air drives are used for the same reason. It saves time and improves efficiency. However, you must watch for leaks and inappropriate uses. I worked with a maintenance director once who used to bring in a small crew on Saturday when none of the machines were running. He turned on the air and found leaks in the system. He fixed them and was able to pay the overtime out of the savings. He also did not have to buy another compressor. So fix the leaks. A 1/16-inch leak costs about $600 per year.
In another instance, I was called on the carpet for a die lubricant that was not performing up to expectations. When I examined the operation, I found an airline attached to the press to eject parts. It was about an eighth-inch in diameter and blowing a constant stream of air. As the press feeder moved the steel into the die, the air blew the lubricant off. This produced what I call the double whammy: poor toll life and the cost of the air. We installed a pulse system on the press to eject the part. Problem solved, and it paid for itself in six months.
Now back to my little air compressor. It is about 1 hp and costs about 10 cents an hour to run. It not only saves me time on house projects, I also find it handy for other things around the house like blowing up bike, motorcycle and car tires. All of these applications save energy. Proper inflation of tires saves an estimated 3% on a car.
So here is a proposal. The first major oil company that goes back to free air at the retail outlets gets my business. It would save me the energy of hauling the equipment out of the basement. What a great public relations coup for an industry that has a public perception problem.
Pete Oglevie is president of International Production Technologies in Port Washington, Wis. You can reach him at poglevie@wi.rr.com.