Using oil analysis data to make lubricant upgrades
Mike Johnson | TLT Best Practices August 2012
This case study shows how developing high-performance products for multiple applications can offer superior economic value.
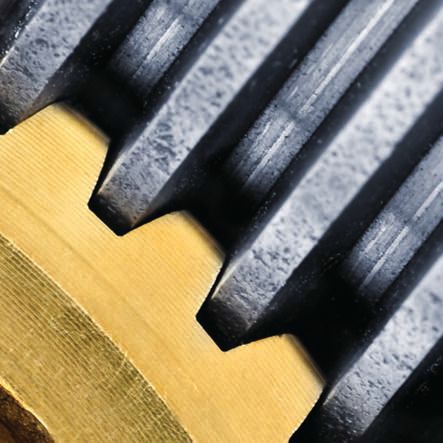
www.canstockphoto.com
KEY CONCEPTS
•
A North American wire manufacturer implemented a machine condition-monitoring plan to improve plant productivity.
•
A decision was made to convert worm gear sumps from the standing mineral oil-based gear lubrication to a PAG-based product.
•
Four sample cycles have occurred since the upgrade to the PAG product type, resulting in a sharp and permanent decline in iron and copper.
THERE IS A VARIETY OF WAYS IN WHICH LUBRICANT ANALYSIS can be a powerful tool to support long-term machine health and productivity. By choosing to focus on machine health, as well as paying attention to the early symptoms of pending failure, one can make corrective decisions to prevent failure and lost productivity.
In Part II of this three-part series (
see the April TLT, available at www.stle.org, for Part I), we will review a case study involving a gear drive that illustrates how a properly executed lubricant-based machine analysis routine led to a decision to upgrade lubricant selection for a critical drive system that, to date, has improved surface protection evidenced by appreciably reduced wear debris.
OPERATING STATE
A North American wire manufacturer operated a multidrive, wire-drawing machine set. The drives used a combination of worm and helical gear sets, with the low-speed, high-load conditions provided by worm gear drives.
In 2009 the manufacturer implemented an inspection and machine condition- monitoring plan (including oil analysis) to improve plant productivity. Permanently installed sample ports were put on the machines that were determined to be process critical, and repeatable sampling was initiated.
A sample routine was executed on a quarterly basis, and specific expectations for wear contamination and fluid property limits were set based on machine types and criticality. A new sample of each lubricant was processed, and the additive metal levels were used to establish a chemical and elemental fingerprint to represent a normal state.
GEAR WEAR CONDITION
At the time of the second sample, multiple worm gear sets were flagged for rising wear and placed in an “alert” state, due to high levels of copper and tin wear debris, indicative of bronze metal wear. The drive systems were reviewed for components that might contain copper, tin and iron, as well as other common metals. The drive did not contain bearings with brass cages, so the obvious single choice for bronze wear was the worm gear itself.
Through ensuing analyses of multiple drives in the plant, they continued to show elevated copper, tin and iron, as these elements generally rise and fall together with product grade changes.
Reliability management recognized that while the wear rate could be perceived as low for a gearbox in general, it indicated a problem for long-term reliability. A periodic filtration plan was put into place to minimize the effect of contamination, but the wear rate persisted.
The drives were evaluated for proper viscosity, and it was determined that the operating conditions justified the use of an ISO 460, which was in use at the time. Following a spike in wear conditions, a decision was made to convert worm gear sumps on one production line from the standing mineral oil-based gear lubricant to a PAG-based product at the equivalent (ISO 460) viscosity grade.
Both products were provided by different high-performance lubricant suppliers. The price differential was, therefore, not as sharp (2:1) as the initial move from an initial commodity product (15:1) would otherwise be. The price differential between the commodity grade and the synthetic PAG was still enormous and would become a stopping point if management was stuck on differences in purchase price alone. Planning ensued for change during a scheduled outage, but the change did not come quickly.
The wear values for all analysis results for the test machine are shown in Figure 1, with the data points noted below the trend lines. The lubricant type change occurred following the March 2011 sample date shown with the red vertical line.
Figure 1. Extended wear debris tracking on a worm type gear drive.
The machine was placed back into service and continued to operate under routine production conditions. Ensuing samples suggest that the wear conditions that occurred with the mineral oil-based worm gear lubricant were alleviated.
IMPROVEMENTS
Four sample cycles have occurred since the upgrade to the PAG product type. The data consistently demonstrates a sharp and permanent decline in iron and copper, which infers a greatly reduced surface wear state.
Figure 2 provides a trend line for both copper and iron. Tin and an element of bronze was present at a proportion around 10 parts copper to 1 part Tin (a traditional proportion for bronze metal) and, accordingly, was never more than a confirming trace metal. The trend line provides evidence that the PAG lubricant improved gear surface conditions. At the current wear metal levels, it is reasonable to expect that the test case gear drive lifecycle has been extended. Based on early indications of success, additional drives have been upgraded.
Figure 2. Wear debris trending: Green = Iron; Blue = Copper.
Interestingly, the lifecycle extension of the bronze gear, which produces lower long-term cost of maintenance, is irrelevant. Likewise, the immediately elevated cost of the lubricant purchases is irrelevant.
SUMMARY
The core value of implementing a condition-monitoring program is not cost reduction. The added cost of analysis and lubricant price increase alone would seemingly increase the cost of production. Further, the value of making a decision to upgrade from one lubricant performance level to another in pursuit of similar results, as noted in this article, is of only marginal value.
The objective was achieved (dramatically lower wear rate, suggesting longer component life and reduced cost of care), but the value is that the plant was able to produce more from the existing capital investment than would otherwise be possible.
When supported by effective machine condition monitoring (proper sample collection, sample interval and review of data for proactive improvements) management can make shrewd, constructive decisions to spend more money on high-performance products for a multitude of applications that collectively accrue enormous value to the company.
Author’s note: There is an ongoing debate that product performance differences exist between brands, and even between products within a brand. This is, of course, just as useful as debating whether there are differences between the qualities of automobiles or whether there are differences in the qualities of suits of clothing. Fortunately, the differences are as clear as night and day, if one knows what to look for.
For those responsible for lubricant purchases, the existence of high-performance lubricants is seemingly held in the same high regard as the practice of Voodoo. However, the real question is not of lubricant performance but whether high performance equates to superior use-cost. A product may provide superior results, but when used to lubricate the plant floor it provides no value over a commodity option.
Gear lubrication is a big challenge for molecule blenders who labor over recipes that balance cost of materials with in-use performance. Raw material selection plays a major role in both ends of the balanced equation, particularly as it pertains to worm gears. There is a distinguished option that has both higher cost (per gallon) and irrefutable opportunity to improve machine operating performance.
Polyalkylene glycol (PAG)-based lubricants are the right choice for worm gears. They bring a price multiple of 10 to 15 versus mineral oils, but they provide unmistakable improvement in wear protection. The lubricant used initially in this case study was a high-performance, mineral-oil worm gear lubricant that was replaced by a PAG of similar viscosity. The change in Cu, Sn and Fe wear debris speaks for itself.
Mike Johnson, CLS, CMRP, MLT II, MLA III, is the principal consultant for Advanced Machine Reliability Resources, in Franklin, Tenn. You can reach him at mike.johnson@precisionlubrication.com.