Complexity in oil analysis information: Part V
Jack Poley | TLT On Condition Monitoring July 2012
Your job is to offer an as-accurate-as-possible evaluation—even if it is ignored.
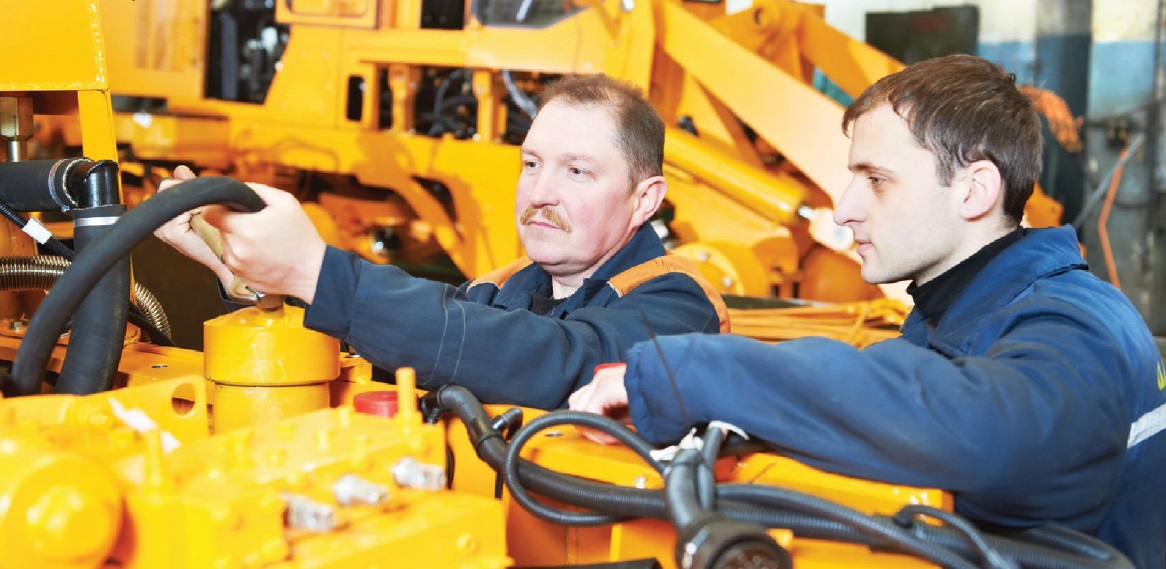
www.canstockphoto.com
LET’S EXPLORE REAL-WORLD REPORTS AND THEIR DATA, along with observations and reasoning from the standpoint of an intelligent agent (IA), a sophisticated expert system designed to address condition monitoring data, with primary emphasis on oil analysis. Several domain experts and practitioners have informed it in order for the IA to render advisories, supported by observations and reasoning. This process is specifically referred to herein as the evaluation, as opposed to data rating, as previously covered.
Certain constants and treatments are in play:
•
Assumption is made that data rating and coloration (Severity 0-4: 0.White, 1.Green, 2.Yellow, 3.Orange, 4.Red) is based on sound statistical data previously generated and applied for a given sample’s component type, whether generic or highly specific, leaving us with only the evaluation to complete and present. The evaluation results in a specific rating for the component, separate from the data ratings, based on the severity of the comment.
•
We can assume that the laboratory rechecked suspicious data, if any. If we don’t trust the data, we must assume the sample is invalid and comment accordingly.
•
Any discussions about data are (now) in the context of what they might or might not mean in terms of arriving at the rendered commentary for the sample at hand. Again, how the data was acquired is moot; the IA is at the evaluation stage where it would have already prompted and dealt with any questions or anomalies in that regard.
•
Insufficient data, particularly as to the sample information or metadata, might at times be the rule. The IA is expected to make the best of it, demurring just like a good evaluator should—
there’s no sin in withholding an ill-advised opinion born of guesswork and assumptions! (I wish I had been so ingrained early in my career).
•
These exercises require that you have better than rudimentary understanding of OA and know, e.g., which elements are wear metals or contaminant metals or additive metals or combinations thereof (chameleon elements). As well you should have a feeling for typical values in given situations. Likewise you should have fundamental knowledge of machinery and its interaction with its lube.
•
It does not matter if a comment is ideal or even correct, only that it can be fired by a specific set of conditions that a domain expert can specify. If feedback is appropriately provided, the comment can be vetted and edited accordingly.
ADDITIVE CHEMISTRY, MIXING AND INVALID SAMPLES
This is actually a very important area in terms of identification and consequence, and some evaluators have difficulty with it because it can involve a lot of reasoning and explanation, and it’s not always a black-or-white decision.
These samples are from a typical 4-cycle diesel engine. Mo is frequently found as an additive in a number of motor oil brands and can be a troublesome element to evaluate effectively. Why? Because most samples are evaluated without benefit of an analysis of a fresh lube for baseline values. Our IA is ready to subtract the average baseline of Mo or B in this lube, provided the value is known. No reference, no subtraction and a precautionary set of flags is issued, instead. So what should we say, knowing what we don’t know?
In this example, the B is flagged because it also has the potential to represent a coolant additive (therefore, a coolant leak). But that usually requires companion elements in excess, such as Na (sodium) or K (potassium). Since those values are normal or low, the B is more likely to be indicative of a lube additive and, therefore beneficial, or at least neutral to the evaluation. All we can do is admonish the user/viewer that a new lube reference would be useful. Of course, in this case, we have at least four episodes where the comment requesting the new lube reference was fired but not heeded. Sadly, this is a typical response.
Example 1. Persistence of Mo (molybdenum) and B (boron) in a diesel engine oil.
Dealing with the Mo, it is clearly not a wear metal, because Fe (iron) is not at all corroborating the Mo. There is no wear scenario that is remotely possible where Mo equals or exceeds Fe, so the Mo cannot be a wear metal at the level shown. In the previous paragraph, we didn’t have to consider Fe in relation to B because B is not found in Fe alloys, whereas Mo is, at times.
Finally we have to admonish the user/viewer to again furnish a new lube reference. Note: we don’t want to nag about a new lube reference twice in the same report, so our first global rule for our IA is not to repeat the same comment in a given report. Simple enough.
So you read all this and you say, “Big deal, I know all this, so why do I need the IA?” Well, even if you know this you’ve got to say it so that your customer can be warned to provide a new oil reference. And you say, “Well, he never does, so it doesn’t matter.”
In real-world OA that’s true more often than not, but that’s not really your privilege since you’re paid to provide a useful opinion, whether it’s availed or not. The truth is you’re mad at the customer for not caring about his program sufficiently or the fact that you tried to advise him to no avail, and you’ve got better fish to fry. I agree with you. That’s why I use an IA—because I get tired of saying the same thing over and over with no result. But the IA doesn’t, and it doesn’t inject any emotion into it. And you still say, “Big deal!” Nice idea but there’s no game change. Yes, I agree with that, too, until…
A coolant possibly materializes: Na or K rises a suspicious bit, getting to a green or yellow severity color, but the B (that you now believe may partially represent coolant additive chemistry) doesn’t change color or seem to move much. Why doesn’t the B change color? Because it’s so large in concentration, relatively speaking, that a few extra ppm (few might be 30 ppm in this case) will not move it to the next severity color (orange). A new lube reference would have put the B in proper perspective by subtracting the baseline, leaving the difference as a possible indicator, along with Na or K.
To your disappointment, because you’re robbed of a possible tell-tale sign, Fe and other primary wear metals, like Cu (copper) or Pb (lead) or Al (aluminum) didn’t rise when the Na or K began to. Why? Because they don’t have to. There’s no law that says wear metals must necessarily occur when a coolant leak appears to exist. It is our fate as evaluators that not all the patterns speak in unison. At times things get rather fragmented, so the B is important if you’re going to make a decision to recommend a pre-emptive pressure test of the cooling system with no wear metals basis. Downtime and labor expense, the very things OA tries to minimize, is being suggested here—no time to get frivolous!
And if/when your customer calls up mad about the failed engine due to a coolant leak, you can point out that, had he provided the new lube reference you requested each and every sample for the last 10, you could have had a better chance of identifying the problem.
The IA algorithms for dealing with these particular types of situations, where lube references are concerned, is complex in that it involves numbers of elements and the physical/ chemical tests additional to the spectrometric data. The exception for Fe and the math relationship of Fe/Mo must be included, among numbers of other considerations.
However once written and applied, you needn’t worry about being bored (or careless), and your customer is properly warned, repeatedly if need be. Perhaps now, with the IA’s help with the repetitive aspect of your job, you may find the time to call him and ask for a new lube reference directly—that should be an opportunity to make a positive contribution to the overall relationship while you’re at it.
Lube mixing is very common, particularly in industrial settings where numbers of machines are in service and a dozen or more oil brands might be in play. While this example is yet another case of not having a new lube reference, one doesn’t need the reference to know that lube mixing has clearly occurred.
Example 2. Lube mixing (or invalid sample?) – Steam Turbine
Hold on! What if this isn’t a sample from this steam turbine but is, instead, a sample from something else that is labelled incorrectly. Or perhaps the lab has logged the sample incorrectly. Recall what I stated earlier as to guessing. Right—it’s a pity to recommend a bearing inspection (not that you necessarily should based on one suspicious sample) when there’s been a possible sample mix-up, irrespective of who’s at fault.
Our best play is to distance ourselves with a comment that addresses all possibilities but refuses to make a commitment until another sample is sent or the lab retests or checks to see if a logging error occurred.
And what about the Sb (antimony) in the previous three samples? Did I mention we don’t have a new lube reference for this product, either (which explains the green flags on the phosphorus). There is probably no antimony in the oil, though we cannot prove this without a new lube reference. Phosphate esters, which may be present in this lube, seem to emit varied traces of other elements’ wavelengths, such that minor registrations unwittingly take place. Sb is not the only element that presents falsely with synthetic-based products. Inasmuch as it is a low-percentage component of some Babbitts, among its other possible alloying sources, levels as shown would be considered serious if coupled with, say, Sn (tin).
This is akin to the previous argument in Example 1, where Mo and Fe didn’t correlate appropriately for Mo to be considered a wear metal. Here, Sn would likely need to be dominant before the Sb value would possibly be considered to be credible. This correlation failure is another piece of evidence that the Sb is not as reported. There are a couple of other considerations that could be made, but you get the idea.
Again we’ve got to construct a semi-complex algorithm to ferret this type of reasoning out, with the hope of eventually securing a new lube reference while defending ourselves in the event something goes wrong in the interim.
Note: The algorithm for this particular set of findings in the example report has been modified to be more specific to the verbiage in the narrative, and it also includes the notion of “false” Sb when synthetics are in use. We have this benefit because a new lube reference was, in fact, furnished shortly after this report was issued. There is hope, and this is the notion and spirit of the IA: a flexible, teachable agent that can be adjusted and tweaked as new, trustworthy information and knowledge is made available, regardless of the source.
We’ll explore another aspect of IA usage in real-world evaluation in the September TLT.
Jack Poley is managing partner of Condition Monitoring International (CMI), Miami, consultants in fluid analysis. You can reach him at jpoley@conditionmonitoringintl.com.
For more information about CMI, visit www.conditionmonitoringintl.com.