Online condition monitoring of greases
R. David Whitby | TLT Worldwide May 2012
Researchers develop sensor for detecting grease quality in bearings.
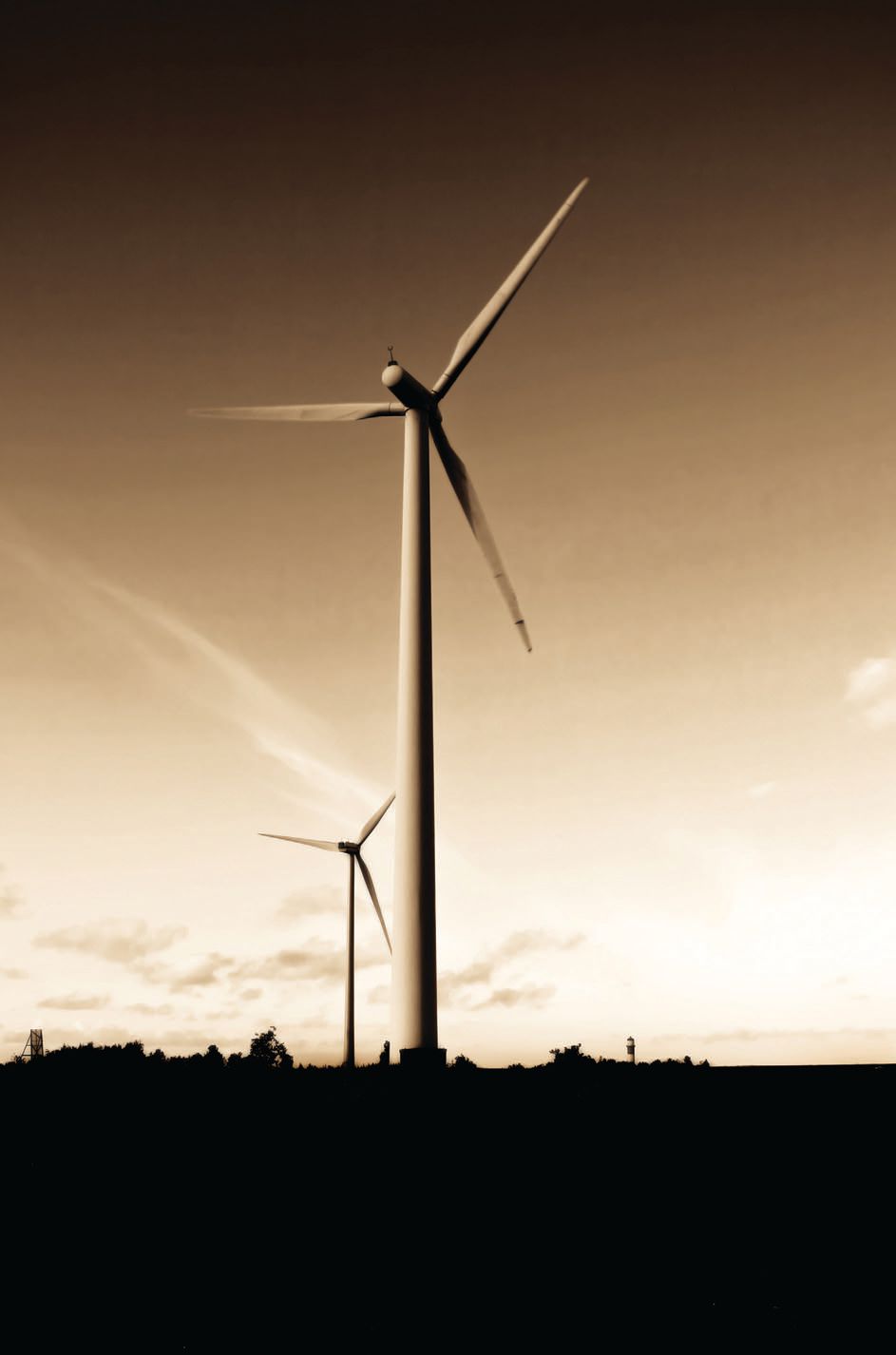
The sensor is ideal for monitoring critical plant and machinery in difficult-to-access areas such as wind turbines.
www.canstockphoto.com
AN INNOVATIVE SENSOR HAS BEEN DEVELOPED THAT ENABLES ONLINE CONDITION MONITORING OF GREASES IN ROLLING BEARINGS. The sensor is ideal for monitoring critical plant and machinery in difficult-to- access areas such as wind turbines and automated assembly lines.
The sensor, developed jointly by The Schaeffler Group, Freudenberg Dichtungsund Schwingungstechnik and Klüber Lubrication, incorporates what is claimed to be a unique electronic evaluation system that enables grease condition monitoring while the bearings are operating. The sensor is positioned directly in the grease in the bearing.
This is a significant breakthrough, as the schedule for replacing rolling-bearing grease can be planned into maintenance schedules precisely. Any changes in the condition of the grease can be detected early before any damage might be caused to the bearings. With preventive maintenance regimes, the operating life of the grease is critical, particularly if it is less than the expected life of the bearing (
Note: Check out the April feature article on key trends in bearing lubrication available digitally at www.stle.org).
Grease-lubricated bearings are normally regreased midway through the grease’s operating life. The disadvantage is that the grease is replaced without knowing anything about its actual condition. Now, however, it may be possible to continue using the grease for a longer time without affecting the performance of the bearing. Conversely, bearing damage might already have occurred due to ingress of water or high temperatures if the grease wasn’t replaced earlier.
Until now, users could only gather information about the condition of the grease inside a bearing by taking a sample and conducting costly, time-consuming laboratory analysis. Schaeffler claims the new grease sensor enables grease to be replaced according to the actual operating requirements of the bearing and not according to any predefined time period. This demand-based (rather than time-based) relubrication results in a reduction in grease, replacement parts and maintenance costs. It also benefits the environment in terms of the volume of lubricant used. Meanwhile, operational downtime of plant and machinery is reduced, while process efficiencies and machine utilization are improved.
The sensor, which measures 5 mm x 40 mm, is able to detect four parameters of the grease: water content, cloudiness (opacity), wear (thermal or mechanical) and temperature. From these parameters, the sensor’s electronic evaluation system uses complex software algorithms to generate an analog signal (4-20mA), which displays the condition of the grease. By setting alarm thresholds (limit values), digital signal outputs also can be generated, indicating whether the grease quality is poor or good, ranging from 100% for as-new to a theoretical 0% for an unusable grease. A user can decide at which point grease relubrication or replacement should be conducted.
The sensor operates by using the optical, near-infrared reflection principle. This method, developed in conjunction with the Fraunhofer Institut for Electronic Nano Systems (ENAS) in Germany, is based on an infrared process used by laboratories to measure the quality of grease. It also has been adapted for online measurements in rolling bearings. The know-how involves both the setup of the sensor and how the measurements are evaluated.
Evaluating the measurements involves rotationally symmetrical irradiation of the grease by the sensor at an angle of 45 degrees using specific wavelengths within the infrared spectrum. The sensor head is embedded directly into the grease during this procedure. The reflected light is measured perpendicular to the grease, which enables any shadow effects or surface anomalies to be excluded completely. The reflected light is then evaluated in terms of the quality of the grease.
In terms of sensor setup, the optimum measurement point varies, depending on the application.
Schaeffler, Freudenberg and Klüber have validated the measurement method for 95% of greases currently available, while a further solution is currently being developed for integration of the sensor in rolling bearing seals.
David Whitby is chief executive of Pathmaster Marketing Ltd. in Surrey, England. You can reach him at pathmaster.marketing@yahoo.co.uk.