What are the most common mistakes people make when selecting the wrong lubricant or additive package?
TLT Sounding Board May 2012
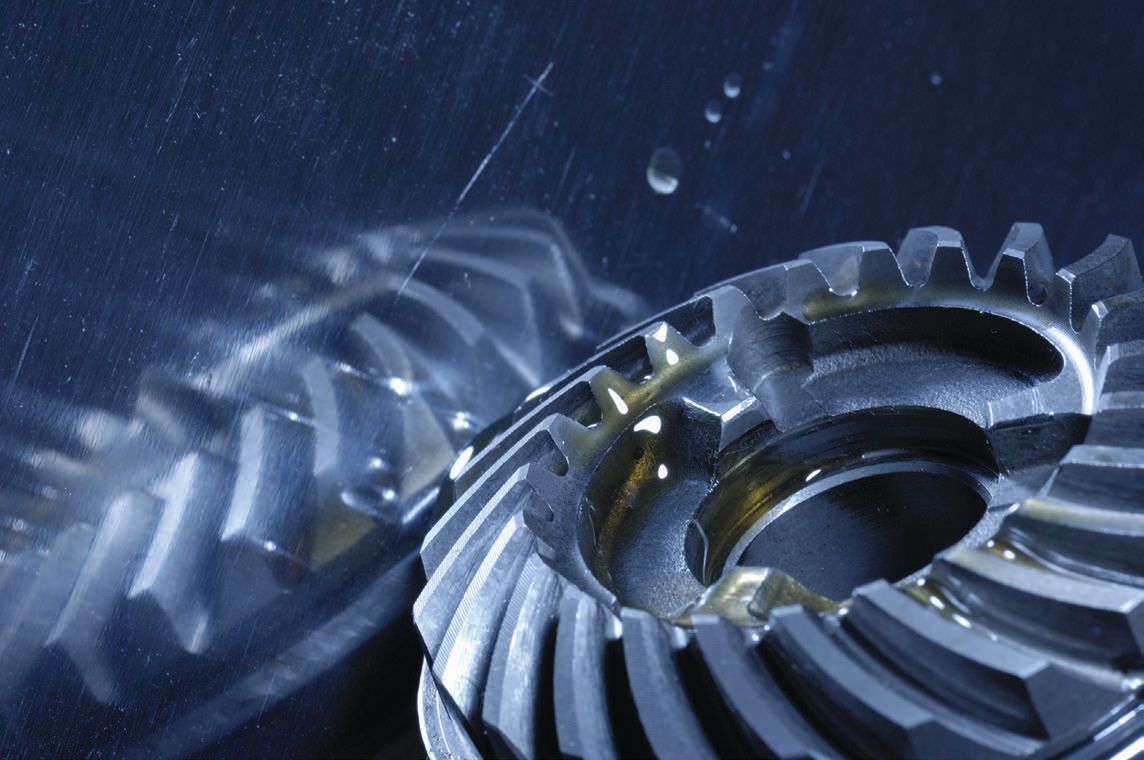
www.canstockphoto.com
You could create a best practices manual of sorts by taking the everyday mistakes lubricant end-users make and reversing them. Instead of ignoring the OEM’s recommendations, read them. Make your decision based on lubricant performance, not price. Check instead of assuming that the lubricant currently being used is the correct one for the job. Unfortunately, too many TLT readers say their customers are clueless as to why what they’re doing isn’t working. STLE and its members will continue to spread the word—when dealing with situations that could put expensive machinery at risk, compromise safety or cause profit-killing downtime, the smart choice is always a qualified lubrication professional. Accept no substitutes.
Selecting the wrong viscosity, usually too thin in gearboxes and hydraulics and too thick in engines.
Assuming the same viscosity is equivalent to the same type of oil: an ISO VG 68 turbine oil is the same as an ISO VG 68 antiwear hydraulic oil.
Assuming there is no differentiation between grease or not understanding where to use solid lubricants rather than liquid-based lubricants.
Looking at the price or what the sales rep recommends versus looking at equipment lube specs.
They look at price instead of performance. Higher performers usually trump price when it comes to longevity of use and fewer recharges.
Incorrect viscosity.
Not following the OEM’s recommendations.
Not checking the background of lubricants used and working conditions.
Not understanding what their equipment needs are for the type of lubricant and schedule.
One of the most common mistakes people make when selecting a lubricant would be not reading the owner’s manual or the OEM information. Another problem arises when the OEM calls for a type of lubricant but the users cannot locate it and then tries to figure out which is the most similar or what would be the next best alternative. Also they make the mistake of settling for a lower grade lubricant because they can’t afford or can’t find the correct one, which can wind up being a costly mistake. Finally, the, “I’m set in my ways and back in the day this is what we used” attitude can be a huge mistake with newer vehicles and the accompanying changes in additive package chemistry.
One of the more common mistakes is assuming that the product in use is the appropriate product for the application.
The most common mistake is not determining compatibility first.
Failure to consider the interactions of different additive functionalities within a given additive package and the coincidental effects of one on the others.
Lubricant consolidation is a good practice since it reduces the number of products in a plant and lessens the chance of putting the wrong lubricant into the equipment. However, in some applications only a specialty product provides the required performance, and the specialty product must be used.
Lack of understanding.
People think all greases with the same grade NLGI are compatible.
Not matching the existing product via cross reference.
Always assuming that the gearbox axle contains 80w90.
Looking at price versus application.
I often hear maintenance people (who are not stupid) say “oil is oil,” “grease is grease” or “just put something on it, some lubrication is better than no lubrication.”
Not knowing what type of gear lube they may need, R&O, EP, worm gear lube, etc.
Sometimes grease information is scarce.
Misinterpretation of performance specifications and improper application.
Topping off with the wrong lubricant occurs frequently due to poor labeling of the fluid containers and the lubrication points on the equipment.
They only look at the limited specification of the product that they used before in the same or similar application.
When changing from one lubricant supplier to another, the new supplier often takes the list of products currently in use and makes recommendations based on that list. If the previous supplier, or the one before that, did not have the right product but substituted something close from their product line, and that is done on multiple occasions, the product in use may not be the best product for the application. It is always best to go back to OEM recommendations or the basics of the applications (speed, load, operating temperature, bearing type) to determine the proper lubricants.
They think the higher the viscosity, the better. They think the more EP additives, the better. They think that if it is meant for race track use, it should be good for their street car. They think that lubricants that performed well in TV stunts would work well on their equipment.
Going too long between lubricant changes.
Purchasing lubricants according to cost and not according to what is needed lubricant-wise.
Making a decision based on how much it will cost for the purchase, not for overall cost down the road.
Editor’s Note: Sounding Board is based on an e-mail survey of 13,000 TLT readers. Views expressed are those of the respondents and do not reflect the opinions of the Society of Tribologists and Lubrication Engineers. STLE does not vouch for the technical accuracy of opinions expressed in Sounding Board, nor does inclusion of a comment represent an endorsement of the technology by STLE.