Spell it out
Peter A. Oglevie | TLT Shop Floor April 2012
Committing that lube procedure to writing will eliminate a host of problems.
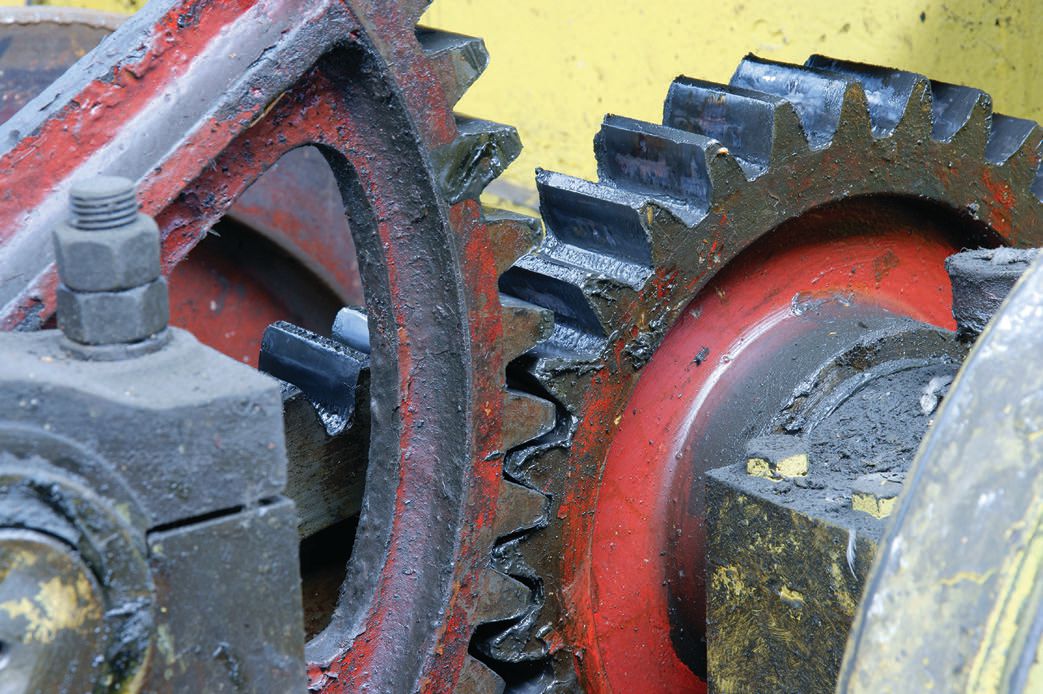
Performing preventive maintenance on old machines might not be glamorous, but it is a necessity.
www.canstockphoto.com
SOMETIME WE LET THINGS GO WHEN WE SHOULDN’T. It’s not for lack of desire; we just don’t get around to doing them. My last van was the victim of bad timing. I was busy with other projects and did not grease my front end, change the oil and do my usual visual inspections. Instead I took it to a shop and relied on others to do it for me. For me, there was no glamour in it anymore. But the shop did a poor job. I never realized how much I depended on that van until it broke down.
The shop floor is very similar. Performing preventive maintenance on old machines might not be glamorous, but it is necessary. Much like I found I could not haul my drywall, boards and tools when my van was down, the shop floor can’t make the parts that keep operators working if the machine is down.
This issue’s
Sounding Board on improper lube selection includes several examples pertaining to grease. On the shop floor, grease is not glamorous, but it certainly is necessary. It is also one of the most abused lubricants on the shop floor, and the reason is lack of knowledge.
I remember walking through a shop floor with Norm, the foreman. As we walked past a punch press, I noticed the crown was being taken out. I asked why. Norm said the bearing lubricator meter plugged and starved the bearing. My follow-up question was why. He did not know. I asked if I could take a look at the problem and was given his blessing.
I checked the grease and found it was not specified for pressurized applications and would separate under pressure. The grease supplier had made a mistake in specifying the grease for the system. If I had simply replaced the old grease with my equivalent, the problem would have occurred again. So I specified grease designed for pressurized systems. Problem solved, and I never saw the crown of the press again.
As a supplier, make sure the grease you recommend is the proper grease. Do not supply greases based on the previous grease used. Go to the manuals and check the specifications.
Another experience that has stuck with me also relates to grease. I had worked with Brad, maintaining his machines. We were talking about failure modes in his electric motors. I asked what he felt was the main cause, and he said fire. I was shocked and asked why. Brad’s answer: “too much grease.”
I have always opposed using too much grease. So naturally I asked how he was handling this problem. He outlined his successful procedure.
With their smaller horsepower motors, Brad applied a loving squirt of grease at Christmas. On larger horsepower motors, he gave me a chart that
spelled out how much grease to use. He also gave me the procedure his crew followed to lubricate motors.
Brad’s procedure called for locking and tagging out the machine and then removing and cleaning the drain plug and drain lines. Clean the motor gaps of excess grease and dirt. Wipe the fitting and add the required amount of grease at a rate not to exceed 33 strokes per minute. Unlock the machine, start the motor and run for 20 minutes. Stop the motor, lock out the main switch and wipe away excess grease. Replace the drain plugs. Remove the lock and tag from the starter switch.
Brad’s procedure spelled out exactly how to lubricate the electrical motor. Result: no more fires.
Many of the front-end steering problems on my van related to poor greasing procedures. I have yet to hear “zerks cleaned” from the crew that worked on my van. How much road grime was pushed into the van’s ball joints, tie rod and pitman arms? I would have wiped the zerks, but I don’t know if they did. The next time I take my van in for maintenance, I will ask to see the grease specifications and procedure sheet.
Pete Oglevie is president of International Production Technologies in Port Washington, Wis. You can reach him at poglevie@wi.rr.com.