The regulatory future of antimicrobial pesticides
Dr. Neil Canter, Contributing Editor | TLT Cover Story 2012
While suppliers seek to increase performance, the pressure is on to eliminate key actives.
KEY CONCEPTS
• Antimicrobial pesticides control the growth of microbes that can degrade MWFs and cause both premature fluid failure and health and safety issues.
• Regulatory issues could lead to a reduction in the number of antimicrobial pesticide options available to the MWF formulator.
• The MWF industry is looking to find combinations of antimicrobial pesticides with synergistic materials to more effectively control the growth of microbes.
ONE OF THE CHALLENGES TO ENSURING THAT METALWORKING FLUIDS WILL OPERATE AT AN OPTIMUM LEVEL OVER A LONG PERIOD IS MINIMIZING contamination from bacteria and fungus. Both of these microbes are well known to literally “eat” the components used to formulate a MWF. Examples include emulsifiers, extreme pressure additives and lubricity additives.
The result is that the fluid becomes destabilized and cannot provide the needed functions of cooling, corrosion protection, lubricity and flushing metal chips. Also of concern are the byproducts released by microbes that can lead to a reduction of the pH of the MWF, further causing fluid instability and corrosion. These byproducts can cause problems from a health and safety standpoint to workers exposed to the MWF.
One of the component classes used by MWF formulators to handle the issues created by microbes is antimicrobial pesticides—also known as biocides. But there are challenges faced by the MWF industry in working with antimicrobial pesticides in a safe and proper manner.
To provide their perspective on working with antimicrobial pesticides, TLT interviewed the following seven industry experts:
• Dr. Fred Passman, president, BCA Associates, Inc.
• Andy Krey, microbiologist, Castrol Industrial North America.
• Dr. Terry Williams, principal microbiologist, Dow Microbial Control.
• Uwe Falk, global commercial manager, The Lubrizol Corp.
• Phil Miller, global compliance manager, metalworking fluids, The Lubrizol Corp.
• Eric Coenen, international key account manager, Schuelke & Mayr GmbH
• Richard Rotherham, director global MWF business unit, Troy Corp.
FUNCTIONS
STLE Fellow Dr. Fred Passman, president of BCA Associates, Inc., in Princeton, N.J., says, “Antimicrobial pesticides perform three primary functions: (1.) They are used as in-drum preservatives to prevent microbes from proliferating in the MWF during storage. (2.) Antimicrobial pesticides are used in application (by either formulation into the MWF or as tankside additives) to prevent uncontrolled microbial proliferation (reproduction) and activity (metabolism) in recirculating MWF and MWF systems. And (3.) To disinfect system surfaces (MWF compounding equipment and MWF systems.”
STLE-member Dr. Terry Williams, principal microbiologist for Dow Microbial Control in Spring House, Pa., says, “Bacteria and fungi will grow in aqueous systems that provide a balance of nutrients (carbon, nitrogen, phosphorus and sulfur) and suitable environmental conditions (pH, temperature, salinity). Antimicrobial pesticides are used to prevent the growth of microbes in the end-use fluids and eradicate or control microbial growth when population levels get too high and must be reduced.”
The impact microbes can have on MWFs is shown in Figure 1 where three of the four emulsified fluids have split due to microbial contamination during a one-week period. When properly treated with an antimicrobial pesticide, the second fluid from the right remains stable.
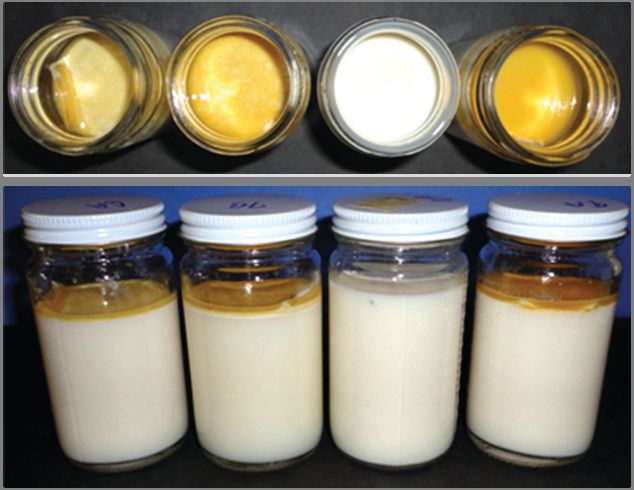
Figure 1. Microbial growth can degrade MWFs in a short period of time, as shown when three of the four emulsified fluids split in one week. The fourth fluid (second from the right) was properly treated with an antimicrobial pesticide and remained stable during the same period. (Courtesy of Dow Microbial Control)
Eric Coenen, international key account manager for Schuelke & Mayr GmbH in Norderstedt, Germany, says, “The function of antimicrobial pesticides is to destroy bacteria and fungi to prevent these microbes from spoiling or destroying (e.g., industrial products and processes).”
STLE-member Richard Rotherham, director global MWF business unit for Troy Corp. in Concord, Ontario, Canada, says, “The use of antimicrobial pesticides reduces the overall bioburden in the system by killing or inhibiting organisms with a corresponding reduction in biomass.”
REASONS FOR USE
STLE Fellow Phil Miller, global compliance manager, metalworking fluids for The Lubrizol Corp. in Spartanburg, S.C., says, “While most people are aware of the toxic nature of the antimicrobial agents used, they tend to overlook the fact that they are also intended to protect the machining industry workers from harmful microbes that can grow in the MWFs if not treated. Even regulatory agencies that do thorough risk assessments tend not to factor this into the equation.”
Uwe Falk, global commercial manager for The Lubrizol Corp. in Hamburg, Germany, adds, “If not controlled at low levels, microbes themselves (like mycobacteria) along with the products from their metabolism may be harmful.”
Rotherham points out that without antimicrobial pesticides, microbes will proliferate, leading to potential worker health and safety issues and poor MWF performance. “One of the most dramatic indicators of microbial attack is the foul odor due to the formation of hydrogen sulfide or other biodeterioration products. When the fluid in a system or a machine sits idle for any length of time, such as in a shutdown period or over a weekend, hydrogen sulfide can be generated through growth of sulfate-reducing bacteria,” Rotherham says. “When circulation is restarted, aeration of the system releases the sulfide odor, an effect which has been dubbed as Monday Morning Odor. This occurrence is not only unpleasant but also potentially toxic [Time Weighted Average Exposure Value (TWAEV) of 10 ppm and Short-Term Exposure Value (STEV) of 15 ppm].”
Rotherham adds, “Other odors that can be experienced due to microbial attack include ammonia and musty off-odors. Ammonia production is normally associated with fluids that have been highly contaminated for prolonged periods and have a large biomass, often through degradation of amine-containing components such as monoethanolamine.”
The protection afforded by antimicrobial pesticides is essential to prevent specific components in the MWF from being broken down by microbes. Rotherham explains, “Typically, fluid components are attacked oxidatively. This is a gradual process in which unsaturated bonds become saturated, side chains are removed from complex molecules and chain lengths are reduced. The components of a MWF are not all equally degradable, and some will be attacked at a more rapid rate than others. Amongst the components that are often the first to be attacked are the corrosion inhibitors and emulsifiers. In ferrous systems, rusting of parts may be the tell-tale indicator of microbial attack.”
Rotherham also indicates that complicating the problem is that the byproducts of microbial attack by a specific microbe may become a food source for another microbe.
Williams mentions that one other source of offensive odors comes from short-chain fatty acids (butyric, propionic and valeric). He adds, “Antimicrobial pesticides are also needed to minimize potential health risks from hypersensitivity pneumonitis and endotoxins (gram-negative-bacterial cell walls).”
Coenen believes that antimicrobial pesticides are essential because bacteria and fungus have ideal conditions to grow in a MWF. He says, “The MWF environment provides the following favorable circumstances for microbial growth: moderate temperature which is perfect to grow microbes, sufficient organic nutrients for microbes to exploit and, of course, the presence of water in high amounts. These three perfect parameters for microbial growth will enhance the spoilage of the MWF because the microbes will digest specific components such as emulsifiers.”
Figure 2 shows an image of MWF spoiled due to microbial contamination. Passman states that protection of the components used in MWFs can translate into positive benefits for the MWF end-user and formulator. He says, “Good control of microbial contamination can translate into 5% to 15% annualized savings on overall fluid/fluid management costs. The impact on the health and safety of the MWF environment is substantial. Healthy, focused workers are invariably more productive than those who are suffering from respiratory disease.”
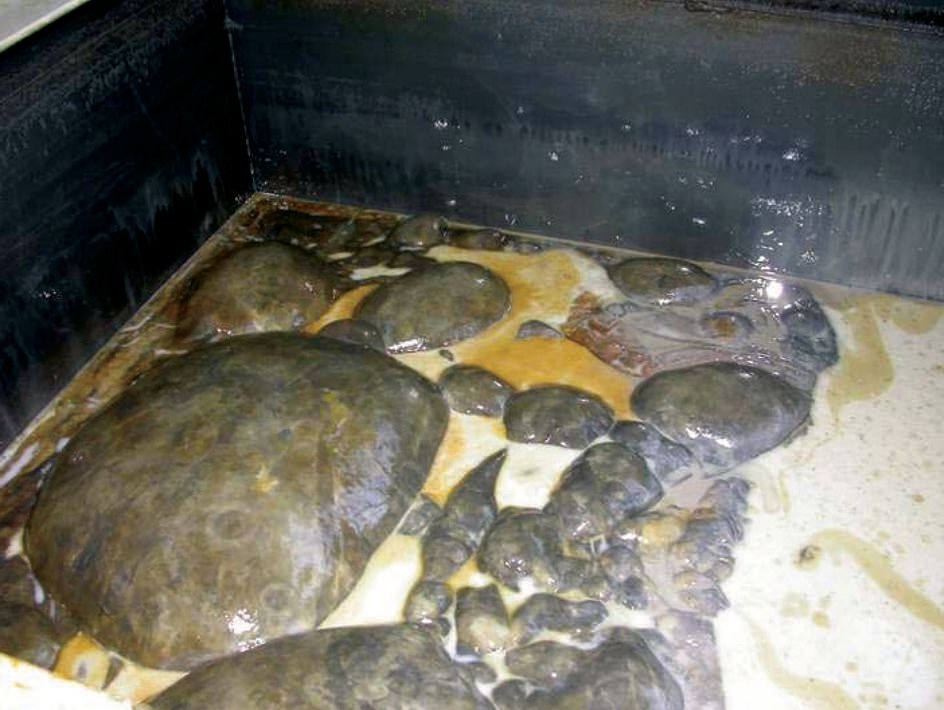
Figure 2. Premature failure will occur with microbially contaminated MWFs such as the fluid shown. (Courtesy of Schuelke & Mayr GmbH)
STLE-member Andrew Krey, microbiologist with Castrol Industrial North America, Inc. in Naperville, Ill., gives a formulator’s perspective on the reasons for using and the benefits from antimicrobial pesticides: “Among the reasons for using antimicrobial benefits are protection of MWF functional chemistries from biological attack, extension of product emulsion/dilution stability, maintenance of product performance, reduction in odor generation potential and minimization of health and safety concerns.”
Krey continues, “Improved MWF dilution/emulsion stability can result in extended product changeout intervals. From our standpoint, product sump life extension is always a goal.”
TYPES OF ANTIMICROBIAL PESTICIDES
Coenen differentiates how microbial growth is controlled between those antimicrobial pesticides that release formaldehyde and those that do not. He says, “Antimicrobial pesticides control the growth of microbes by chemical interaction in the physiology of the microbial cell. This interaction hinders the multiplication of the microbes (biostatic effect) or even kills the cells (biocidal effect). Some of the antimicrobial pesticides release formaldehyde, which interferes with the microbial cell. Others are formaldehyde-free and utilize another chemical interaction to destroy the microbial cell.”
There are a large number of antimicrobial pesticides that can be used in MWF applications. Passman and Rotherham cite ASTM E2169 (Practice for Selecting Antimicrobial Pesticides for use in Water-Miscible Metalworking Fluids) as an ideal source for reviewing the specific types (1). Passman says, “In the ASTM method, there is a table that currently lists approximately 50 molecules that are approved either individually or in formulated blends as antimicrobial pesticides for use in MWFs.”
Rotherham broadly classifies them as either bactericides or fungicides. Passman states that four of the antimicrobial pesticides are used exclusively as fungicides and the others are used primarily as bactericides.
One of the most widely used classes of antimicrobials is the formaldehyde-condensates. Passman says, “This class of antimicrobial pesticides represents greater than 80% of the total volume of MWF-treatment microbicides used today. Examples include hydantoins, morpholines, oxazolidines and triazines. The mechanism of how they control bacteria is to crosslink proteins, thereby inhibiting enzyme or cell membrane activity.”.
Rotherham believes the ways antimicrobial pesticides control microbial growth are very complex. He says, “The mechanisms and sites of action can vary from molecule to molecule and will also vary with the organism being targeted. Some antimicrobial pesticides act as simple poisons, while others cause physical disruption of cell structures.”
Williams provides his perspective on the types of antimicrobial pesticides and how they control microbial growth: “Antimicrobial pesticides include products that primarily control bacteria (triazines, chloromethylisothiazolone, methylisothiazolone, benzisothiazolone oxazolidines, dimorpholines, phenolics, glutaraldehyde, quaternary amines, bromopol and dibromonitrilopropionamide) and fungi (octylisothiazolones, butylbenzisothiazolone, pyrithione and carbamate). Most biocides function by inhibiting cellular metabolism through disrupting enzymes or proteins. Certain biocides directly affect cell wall membranes and cause cells to burst in a process known as lyse (quaternary and phenolics). Other antimicrobial pesticides specifically affect energy generation (pyrithiones).”
ADVANTAGES AND DISADVANTAGES
Rotherham lists a number of criteria that MWF formulators must take into consideration in selecting one type of antimicrobial pesticide over another type. He says, “Formulators have been trending now to non-formaldehyde releasing chemistries based on customer demand. Compatibility with other components in the fluid is very important, which limits the use of cationic antimicrobial pesticides because anionics can be used in formulations. Formulation stability is a key criterion because some antimicrobial pesticides are not compatible with other components in the MWF concentrate and are used almost exclusively tankside. Other factors that need to be considered are cost effectiveness, ease of incorporation, targeted organisms, workplace safety and environmental acceptability.”
In the latter case, Rotherham is referring to restrictions placed on the discharge of phenolics in wastewaters.
Each of the antimicrobial pesticides available for use in MWFs has advantages and disadvantages. Most of the parameters used evaluate their performance on specific microbes and their stability in MWF concentrates.
Williams looked at a number of the key antimicrobial pesticides and said, “Chloromethylisothiazolone is an excellent bactericide and fungicide with effectiveness against biofi lms. It does not release formaldehyde, but its use is limited to tankside treatment. Benzisothiazolone is a good bactericide that is very stable and compatible in MWF concentrates and also does not release formaldehyde. Ethylbicylooxazolidine and dimethyloxazolidine are good bactericides, very stable and compatible in concentrates and provide pH buffering.”
The spectrum of antimicrobial activity varies among the chemistries, according to Passman. He says, “Determining what antimicrobial to use can be complicated because characteristics (for example, chemical stability in MWF formulations) that are an advantage for some applications can become disadvantageous under other conditions (the stable microbicide can accumulate through MWF cycles of concentration) and potentially exceed permissible concentrations.”
Coenen gives some general advantages and disadvantages amongst antimicrobial pesticides: “In general, advantages can include quick biocidal effect, less odor than other actives, less legislative pressure and long-lasting efficacy. Among the disadvantages are discoloration with some actives and strong labeling (toxic, etc.).”
Krey believes that most compatibility issues with antimicrobial pesticides can be taken care of through proper formulating. But regulatory issues can make it a disadvantage to work with a specific antimicrobial pesticide as compared to other options. He says, “Challenges do arise when biocidal actives are not globally registered or listed on each of the primary country chemical inventories. Registration gaps can restrict the transfer of products from one region to another. This is especially troublesome for global MWF formulators.”
SUPPLIER ISSUES
The most important issues facing antimicrobial pesticides are based on regulatory factors. Williams says, “Antimicrobial pesticides must be registered with the EPA, Canada Health Ministry (PMRA) and the European Biocidal Products Directive (BPD). These agencies require detailed information on product chemistry, environmental fate and health hazard testing.”
Williams continues, “This requires long-term testing with approval times often 6-12 months for simple changes and years for detailed changes. Test costs are significant. REACH is another regulatory requirement, which affects all chemical suppliers who must provide detailed information as well.”
At the crux of this issue is the matter of how formaldehyde-releasing biocides will be handled and how MWF formulators are reacting to fewer antimicrobial pesticide options that are becoming more expensive. Passman says, “The unclear regulatory climate has led to much speculation about the fate of formaldehyde condensates. EPA’s Office of Pesticides Programs (OPP) has yet to make any final decisions. There is a chance that chronic (lifecycle) data will be required. These studies take more than two years to complete and can cost between half a million and $1 million. Only products that have been approved for use in high-volume markets that are large enough to justify the cost of the toxicological testing are likely to be introduced into the MWF industry.”
Passman continues, “Besides being effective and EPA registered, microbicides must be chemically compatible with MWF formulations. No one is going to formulate a product around the antimicrobial pesticide chemistry. Given the current economy, cost pressure continues to be enormous. Increasingly, formulators are looking to use chemicals that are not registered as microbicides. Some of these chemistries have well-documented performance properties other than antimicrobial activity. I fully support their use. Others, however, only have documentation of their biocidal performance. All other performance claims reflect the manufacturer’s ‘we have reason to believe’ arguments (this is an amine, therefore it is expected to do what other amines do—provide corrosion inhibition, emulsion coupling, etc.).”
Miller says, “The most prevalent issue is regulation based on emotional response rather than scientific fact. Formaldehyde is the prime example. One scientific body of experts classified formaldehyde as a known leukemia agent based primarily on an epidemiology study that reported the effects of exposure to formaldehyde were remarkably similar to benzene, only to find out later that the plant where the study was done has elevated amounts of benzene in it. Confounding information in other studies has also been discarded in order to classify formaldehyde more severely.”
Falk adds, “Customers’ opinions about antimicrobial pesticides are often steered only by harmful labeling of a product, which often does not reflect the real low-risk when handled at the levels and manner recommended by the supplier.”
A similar view is expressed by Coenen who says, “Key topics affecting antimicrobial pesticides are mainly the Biocidal Products Directive in Europe and FIFRA approval for the U.S. The support of the chemical antimicrobial pesticides under such legislation requires a large amount of money, time and knowledge. A general risk is the prohibition of certain chemicals or a strong negative labeling of such chemicals.”
Rotherham discusses the irony that antimicrobial pesticides are the most tested components used in MWFs, yet they are also under the most regulatory and customer pressure. He says, “There is a definite perception by the worker that antimicrobial pesticides are dangerous and, therefore, undesirable without a real understanding of their benefits. This has resulted in an increased use of so-called biocide-free products that do not readily support microbial growth. However, the components of these fluids that are providing microbial control generally have less supporting data in terms of both performance and safety.”
Rotherham warns that additional mandated testing will lead to a reduction in the number of antimicrobial pesticide options available to the MWF formulator. He says, “In the next phase of EPA reregistration, antimicrobial pesticides used in open MWF systems will require both cancer and multigeneration reproductive toxicology studies. This will add at least $3 million in additional regulatory support costs for each supported antimicrobial pesticide (an exception to this requirement is if the antimicrobial pesticide labeling includes a statement that it is only to be used in closed systems). As a consequence, we expect to see a further reduction in the number of product types available to formulators, as has already happened in other pesticide use areas.”
Krey maintains that concentrate stability is an important parameter that can increase the effectiveness of antimicrobial pesticides. He says, “There is room for improvement in the stability of antimicrobial active ingredients in MWF concentrates.”
HHT
Hexahydro-1,3,5-tris-(2-hydroxyethyl)-s-triazine (HHT) is one of the most widely used antimicrobial pesticides and functions by releasing formaldehyde. Currently, the recommended treat rate for using this antimicrobial pesticide in MWF is 1,500 ppm. In April 2010, EPA recommended that the treat rate be dropped to 500 ppm, which would render this antimicrobial ineffective in treating MWFs. EPA has since decided to review its position and not enforce a treat rate of 500 ppm.
Falk says, “I think HHT will be available for some time. If EPA regulates the dosage down to 500 ppm maximum, this antimicrobial pesticide will need to be replaced or supplemented. I think the avenue taken will be to supplement HHT since EPA has very recently made a decision for registration of a new active, methylenebis-morpholine that is also a formaldehyde release antimicrobial.”
Falk continues, “The difference is that methylene-bis-morpholine has a slower rate of release and low levels of released formaldehyde. The bottom line is the market has to be educated not to make knee jerk emotional decisions in using antimicrobial pesticides.”
Rotherham comments on the EPA review of HHT. He says, “HHT was the subject of a 2008 EPA Reregistration Eligibility Decision. One part of that decision was a risk-mitigation requirement that would see the use level reduced in MWFs. At this time, label changes have not been implemented, and we are hopeful that based on National Academy of Science review and criticisms of EPA’s Draft IRIS Assessment of Formaldehyde, EPA will reconsider the risk-assessment criteria and not proceed with the proposed reduction in use levels.”
Rotherham continues, “We do not anticipate any changes in the market availability of this active or any other similar amine-formaldehyde-condensate antimicrobial pesticides in the foreseeable future.”
Coenen offers a European perspective on HHT. He says, “It carries the labeling Toxic by Inhalation for use in Europe. This labeling makes it a less attractive active compared to other options. However, with the overall regulatory environment leading to more strict labeling/legislation for antimicrobial pesticides, some users will continue to use HHT for its advantages since other alternatives might also receive stricter labeling in the future.”
Passman warns, “If HHT is eliminated as a possible antimicrobial pesticide, then it is likely that other formaldehyde- condensates will follow in its wake. Only the aldehyde microbicides have been shown to denature endotoxin. Endotoxin’s role as a respiratory allergen is well documented. Elimination of formaldehyde-condensate microbicides could well translate to increased incidence of allergenic respiratory disease among machinists.”
Krey reveals that his company has formulated away from HHT so that its possible removal from the marketplace will not be an issue. He says, “We made the decision not to use HHT back in the 1990s when rumblings about health and safety issues first surfaced. Our product line is virtually HHT-free.”
BIOFILMS
An initial impression about microbes may suggest that they are microscopic and cause difficulties to MWF systems on a molecular level. In actuality, microbes prefer to form macroscopic biofilms that can facilitate their growth and protect them from their enemies. Biofilms can cause physical problems such as trapping metal fines and literally plugging up piping and sluice surfaces to limit MWF flow.
Coenen explains, “Biofilms are chemical structures built by microbes where they can hide and multiply. The biofilm is made of different building blocks such as sugars, proteins, nucleic acids, lipids, dead and living microbial cells.”
Figure 3 shows a biofilm growing in a MWF system. Rotherham suggests reviewing a primer on biofilms available from the University of Montana’s Center for Biofilm Engineering (2). He says, “Microbes exist in two forms: free-living/planktonic or attached to surfaces/sessile. We now know that the sessile form is the normal state. Biofilms in MWF systems are typically composed of mixtures of different organisms embedded in a polymer matrix (EPS) and form as a result from the growth of the organisms on the surfaces in the system. Biofilm includes both organic and inorganic debris. They have discrete structures with features more analogous to higher organisms than to the single-celled organisms of their planktonic state.”
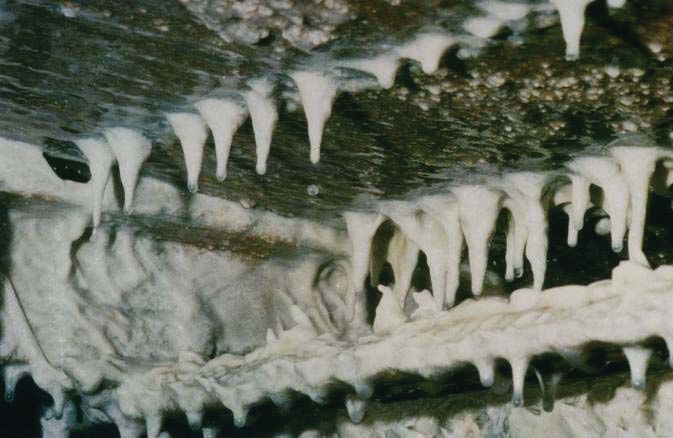
Figure 3. Biofilms are communities of one or more types of microbes that are embedded in a polymer matrix and are difficult to remove. (Courtesy of Schuelke & Mayr GmbH)
Williams maintains that biofilm formation has been found to be quite complex with specific chemical compounds being used for communication purposes. He says, “Biofilms are populations of cells that attach and ‘stick’ to surfaces. They form under dynamic conditions of fluid flow and are found in machine parts, basin walls and pipework, fluid distribution lines and sluiceways, weirs, filters and swarf. Microbes initially stick to the surface by secreting extracellular polymeric substances (EPS), which are composed primarily of polysaccharides and proteins and form a strong adhesion to the solid substrate.”
Williams continues, “Recent studies have shown that cells within biofilms can communicate via signaling compounds from the family of acylated homoserine lactones. These compounds influence cellular attachment, growth and detachment (dispersal) from biofilms.”
Figure 4 shows biofilm taken from a model recirculating MWF system that was not treated with antimicrobial pesticides. When an antimicrobial pesticide was used, no biofilm was observed.
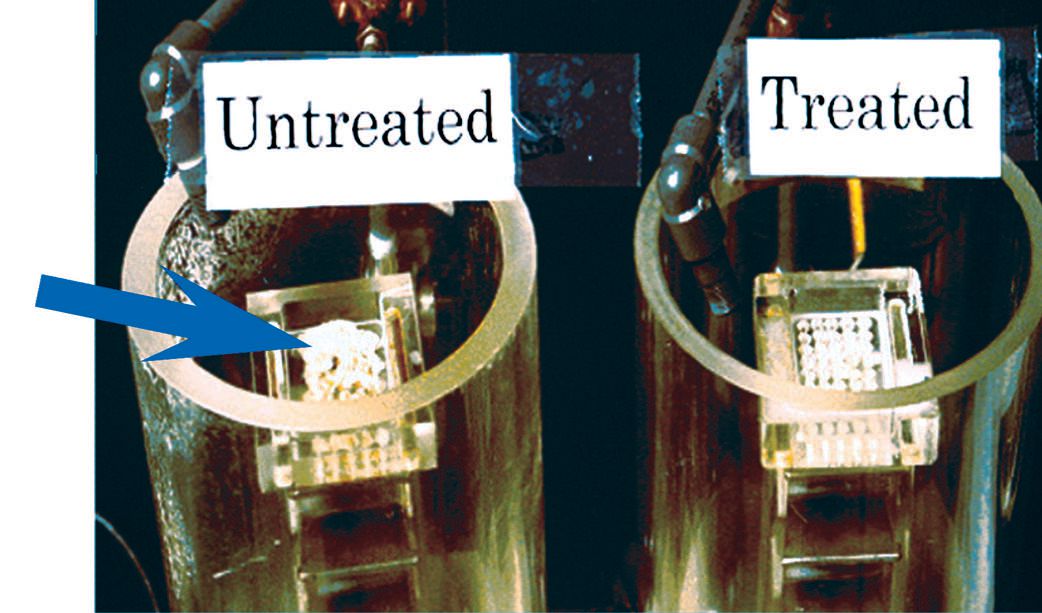
Figure 4. Treatment of MWFs with antimicrobial pesticides is very important in minimizing the formation of biofilms. The model MWF system on the right did not contain any biofilms due to proper treatment with an antimicrobial pesticide. But biofilm grew in the same MWF system on the left, which was not treated with antimicrobial pesticides. (Courtesy of Dow Microbial Control)
Passman equates a biofilm to a simple, multicellular organism. He says, “Biofilms are communities of one or more types of microbes that live embedded within a polymeric matrix. Cells within the biofilm differentiate to carry out specific functions that are essential to the biofilm community’s health and well-being. Microbes are quite promiscuous, so there is considerable genetic and non-genetic chemical communication among cells within the biofilm. Typically, polymer-producing cells settle onto a surface. As they proliferate, they trap other cells that are floating by. A mature biofilm community can establish itself within 24 to 48 hours after the first cell settles onto a pristine surface.”
Krey indicates that biofilms are a major concern for MWF formulators. He says, “Virtually every aqueous environment can support a biofilm of some form. Diluted MWFs are often the perfect environment for biofilm development. Once entrenched in a MWF system, they become a constant microbe reinoculation source.”
Removal of biofilms can be a big problem for those maintaining MWF systems. Krey comments about the use of biofilm penetrant chemistries and antimicrobial pesticides in dealing with this issue. He says, “Biofilm penetrant chemistries are available in the marketplace. Some antimicrobial pesticide manufacturers also make biofilm penetration claims about their products. I have not conducted controlled laboratory evaluation of penetrant or biofilm removal efficacy. However, in several limited field trials, biofilm penetrant chemistries do appear to loosen organic/biofilm residues from MWF system surfaces. It was difficult to gauge the actual effectiveness of the additive because the extent of biofilm development within the systems was not known.”
Krey continues, “The same can be said for antimicrobial pesticide efficacy upon biofilms. There are those instances where system residues are dislodged directly after an antimicrobial pesticide addition is made. Yes, antimicrobial pesticides are the likely cause, but it is not known if they are truly effective. More industry-specific research in biofilm development and removal could be beneficial.”
Chemical cleaning is recommended as an important option for removing biofilm, specifically when charging a new MWF. During the discharge of the old fluid, system cleaners can be added to the flow of the old MWF and circulated for eight to 24 hours before this fluid is discarded and the new fluid is charged. Coenen says, “When biofilms are present in high loads, the chemical measure should be combined with mechanical cleaning through the use of high-pressure washers.”
Passman maintains that initially a machine cleaner should be introduced and recirculated in the MWF system followed by use of a biocide-treated fluid. He says, “Once the machine cleaner has been used, it is a good time to shock dose the system with the maximum permissible concentration of the selected microbicide. Optimally, the biocide-treated fluid will recirculate for 24 hours or longer, but in the real-world four hours will suffice. At this point, the system should be drained and cleaned. Repeated flushings with dilute MWF are needed until the system is found to be clean.”
Passman warns, “If a contaminated system is recharged before a clean flush has been achieved, the residual contamination will shorten the system’s performance life. It is similar to adding air to your tires and hitting the road when the tires have 70% of the recommended pressure. A bit of time may be saved, but you will not make it far down the road before you encounter more problems.”
Rotherham indicates that prevention is the best course of action. He says, “Some of the ways that biofilms can be dealt with or disrupted in other environments (chlorine, pH shock) are highly detrimental to the MWF. So-called biodispersants have very limited efficacy, and biofilms can quickly adapt to overcome their limited control. Effective microbial control of the fresh fluid introduced into a clean system using antimicrobial pesticides and an effective monitoring system are important to limit uncontrolled biofilm development.”
Williams points out that antimicrobial treatment must be modified to get the organisms in a biofilm under control. He says, “Microbes become less susceptible to antimicrobial pesticide when growing in biofilms due to decreased permeability of the antimicrobial pesticide, slower rate of growth by biofilm cells and deactivation of the antimicrobial pesticide within the EPS matrix. For heavy biofilms, antimicrobial pesticides are still effective, but they may need to be dosed at the maximum EPA label use rate and dosed frequently to assure effective killing of cells in the biofilm and removal of the EPS matrix.”
DETERMINATION OF MICROBE CONCENTRATION
The long-established test method used to evaluate the concentration of microbes in MWF systems is the dipslide test. In this procedure, a paddle coated with an agar medium designed specifically to grow bacteria on one side and fungi on the other side is dipped into a MWF sample for a few seconds. The paddle is then placed in its container and allowed to incubate at 30 C for 24 to 36 hours for bacteria and three days for fungi (see Figure 5).
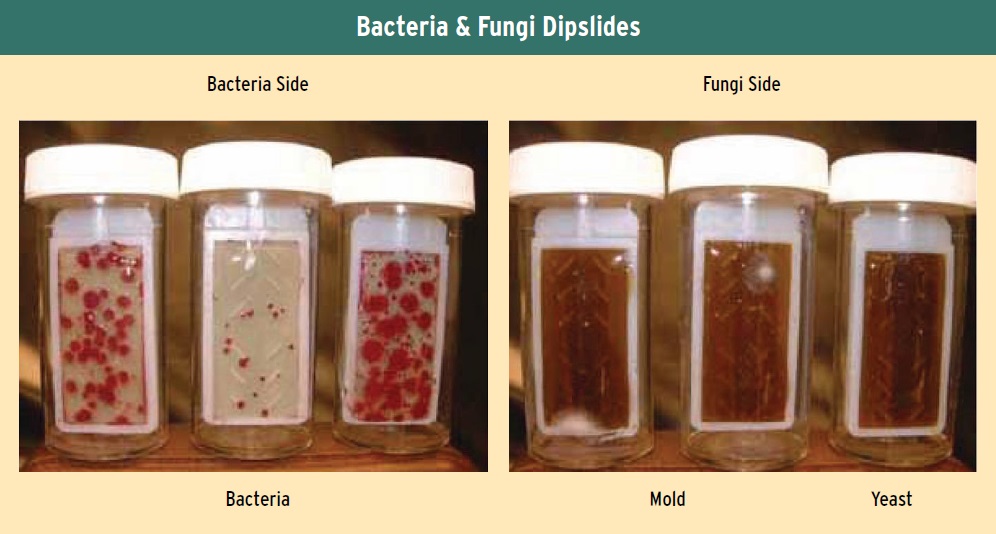
Figure 5. The dip-slide test has been the long established method for evaluating the concentration of MWF systems. Agar medium on the left are used to grow bacteria, while agar medium on the right are used to grow fungi. (Courtesy of STLE)
This test does take time to produce results. Our industry experts were asked for their opinions on the dip-slide test and other options available.
Williams says, “Dip slides are an effective method to provide a simple, inexpensive monitoring of microbial growth in water-based industrial systems. They are suitable for bacteria and fungi and require minimal technical skills. An alternative called Petrifilm ™ (from 3M) is a plating method that requires a one-milliliter pipette to dispense the sample onto an agar-covered paper film using the same concept as dip slides to estimate microbial growth. While this technique is more quantitative, it requires more equipment and skill but still has the same time constraints.”
Williams continues, “Other methods such as measurement of oxygen levels (indicative of the metabolic state of the microbes) can be adapted to real- time and online monitoring. Measurement of ATP is a very fast method but does not distinguish between living and dead organisms. ATP is good for trend analysis and gross changes.”
Krey says, “Dip slides do provide a decent estimation of relative bacterial and fungal contamination in a sample. The results generated from dip slides are most similar to those that can be generated by the microbiology industry standard plate count method. Interpretation of results is not typically an issue. Among the problems found in using the dip-slide test are media-specific growth limitations, the inability to detect static but viable populations and the time needed to generate data and interpret final results.”
Krey continues, “Indirect, quick methods such as hydrogen-peroxide reaction, dissolved oxygen depletion and ATP quantification all have their benefits and limitations. The primary benefit is the fast response time. Quick detection can led to faster correction in the MWF sump. However, these methods have limitations such as they cannot differentiate between bacteria and fungi, the results do not directly correlate to plate count results and MWF chemical interferences can lead to false positive/negative results. As long as the limitations are known and results are interpreted correctly, any one or a combination of direct and indirect detection methods can be used to trend microbial content within MWFs.”
Passman says, “There is no perfect method, and in many applications, the dip-slide test is adequate. The real problem is that only a small percentage (estimated to be 0.01% to 0.1%) of the microbes active in a MWF will form colonies on the dip slide in the time allotted for the test. While all other condition monitoring methods require only a few minutes to perform, culture tests have that incubation period. By the time you have data, it is likely that conditions in the system will be very different from what they were when you started the test.”
Passman continues, “I typically rely on data from three rapid methods: the 15-minute catalase test, a twohour oxygen demand test and the ATP test (ASTM E2694). If I only have time for one of these tests, then I go with the ATP test (3). It is an ASTM standard method that has been vetted through both extensive field evaluations and an interlaboratory study in which 10 companies participated (4). The ATP test detects all metabolically active cells in the sample, but it does miss dormant cells and does not differentiate between bacteria and fungi. As a 10-minute test, it provides useful data in about the time it takes to run an alkalinity test.”
Rotherham agrees that the dip-slide test works well, though suffers from the time needed to deliver test results. He says, “Dip-slide tests have the benefits of being quick and simple to use by relatively unskilled operators.”
Rotherham acknowledges that there is a trend toward the use of more rapid test methods in microbiology. He says, “One weakness of these methods is that there is an initial capital cost, but, more important, they are not simple and a degree of skill/experience is necessary for the operator. While they have the benefit of providing virtual real-time results, their use and data interpretation requires a skilled operator.”
Rotherham points out that a new technique under development and known as the electronic nose shows promise as a means to online monitor the microbial concentration of MWFs (5). He says, “Although the project is still in the early stages and not yet close to commercialization, this is an interesting approach. Once installed in a MWF system, there would be significant benefits.”
Coenen indicates that the dip-slide test is the most efficient way to determine the presence of microbes when price, time and ease of use are considered. He adds, “A more sensitive way could be the ATP analysis, which is a very quick procedure but does not differentiate between bacteria and fungi and also between living and dead cells.”
FUTURE OPTIONS
Continuing regulatory pressures on antimicrobial pesticides, combined with the higher costs needed to ensure they are validated for use commercially, leads to the feeling that fewer actives will be available in the future. Our industry experts were asked about how the MWF industry will handle this issue in the future.
Miller says, “As EPA reregistration becomes due, many suppliers may opt not to reregister for metalworking use in the face of the huge costs involved. We have seen this scenario play out recently, and I expect it will occur many more times.”
Falk says, “I think we will see continued pressure to use fewer antimicrobial agents, which will lead to improvements in fluid management techniques. Synergists will likely contribute to this trend, but nobody wants to address the health and safety profile of the combination of an antimicrobial pesticide with a synergist with actual data. If the efficacy of an antimicrobial is significantly enhanced using a synergistic material, then would not one reasonably expect a higher level of toxicity from the combination?”
Coenen predicts that such a synergistic effect will place more regulatory scrutiny on those chemicals that exhibit biocidal/biostatic effect as an additional benefit, particularly in Europe. He says, “There is a trend toward antimicrobial pesticide-free MWFs, which usually means that the hindrance of microbial growth is performed by chemicals that perform other functions in the fluid. It needs to be seen when legislation hits on those chemicals since they still fall under the scope of the BPD in Europe because such chemicals fall under the definition of an antimicrobial pesticide.”
Coenen indicates that antimicrobial use will be minimized to as little as possible and as much as technically necessary.
Rotherham also sees future product development focused on finding combinations of antimicrobial pesticides with synergistic materials. He says, “If EPA risk assessments mandate lower use levels of some actives, there will be a trend toward using combinations of actives, especially where the actives are synergistic. Both suppliers and formulators also will continue to look for true synergists—materials that are clearly not antimicrobial pesticides themselves but which, when used in conjunction with antimicrobial pesticides, boost the efficacy of the latter.”
Krey believes that more biostable additives also will be incorporated into MWFs if future trends for fewer antimicrobial pesticide options are realized. He says, “As the number of antimicrobial pesticide actives drops, the use of biostable materials will likely increase. Stable, bio-resistant MWF emulsions and solutions will always be needed.”
Williams feels that the use of more than one antimicrobial pesticide (combination treatments) will grow in the search for more effective microbial control. On the matter of synergists, he says, “Other treatments involve the addition of various MWF additives such as certain classes of amines that enhance the efficacy of antimicrobial pesticides without having antimicrobial pesticide properties themselves.”
For the future, Williams predicts a number of improvements that will facilitate the monitoring of microbes, including the possibility of online, real- time systems that will automatically trigger the dosing of antimicrobial pesticides. He says, “New dosing systems for tankside treatments may evolve with improved safety and handling features to reduce antimicrobial pesticide exposure to workers. Solid biocides also might become popular if appropriate dosing and handling systems are available. New methods in measuring antimicrobial pesticide levels may also be developed to optimize dosing and treatment.”
Passman feels that a balance between product cost and waste treatability is needed in formulating MWFs. He says, “Increased use of recalcitrant (bioresistant but not biocidal) molecules is inevitable. If the finished MWF formulation is not sufficiently biodegradable, then end-users will be wary of using it. If it has a poor toxicity profile—reflecting the inclusion of toxic unregistered microbicides—that too will limit the applicability of the formulation.”
As for the future, Passman sees the inevitability of fewer antimicrobial pesticides being available to the MWF formulator. He says, “Invariably, antimicrobial pesticides enter the MWF market only after they have become commercially successful in other greater volume demand markets. I suspect that pressure on formaldehyde-condensates will continue to wax and wane, but these products will remain the mainstay of the industry. More formulators are finding means for achieving bioresistance without resorting to registered antimicrobial pesticides. As the costs of sustaining registration increase, I anticipate that the length of the product list in Table 1 of ASTM E2169 will shrink substantially.”
The continuing threat that microbes have in creating major problems for MWF systems means that antimicrobial pesticides will remain an integral additive to be used, both in the MWF concentrate and tankside. Suppliers and formulators will need to find more effective approaches for using antimicrobial pesticides in a manner that enhances their performance while minimizing their treat rate.
Further information on antimicrobial pesticides can be found in the Jerry Byers book, Metalworking Fluids, Second Edition (6), and in a recent TLT feature article (7).
Food grade lubricants: Need for antimicrobial pesticides?
WHILE MUCH OF THE ATTENTION on the use of antimicrobial pesticides is with MWFs, the increased concern with contamination of the food supply means that questions about whether food grade lubricants are a good medium for microbial growth need to be asked.
STLE-member Douglas A. Wallace, president of Wallace & Associates Inc. in Mount Prospect, Ill., provides his perspective on the use of antimicrobial pesticides in food grade lubricants. He says, “Initial interest in the use of antimicrobial pesticides in food grade lubricants came from major food retail brand names. The interest was driven as brand name insurance and not by problems associated with microbes in lubricants. This project was initiated as a proactive process to prevent any possible contamination of food products by the lubricants used in the operation.”
Wallace continues, “The food-processing environment contains lubricants, water and food byproducts (see Figure 6). This can be an ideal growth media for microbes. The addition of an antimicrobial pesticide will ensure that the lubricant itself will not add to any pre-existing contamination or become a medium for growth. This added insurance is considered a benefit to those marketing food products to consumers in a highly regulated market that has been hit with many deadly contamination issues.”
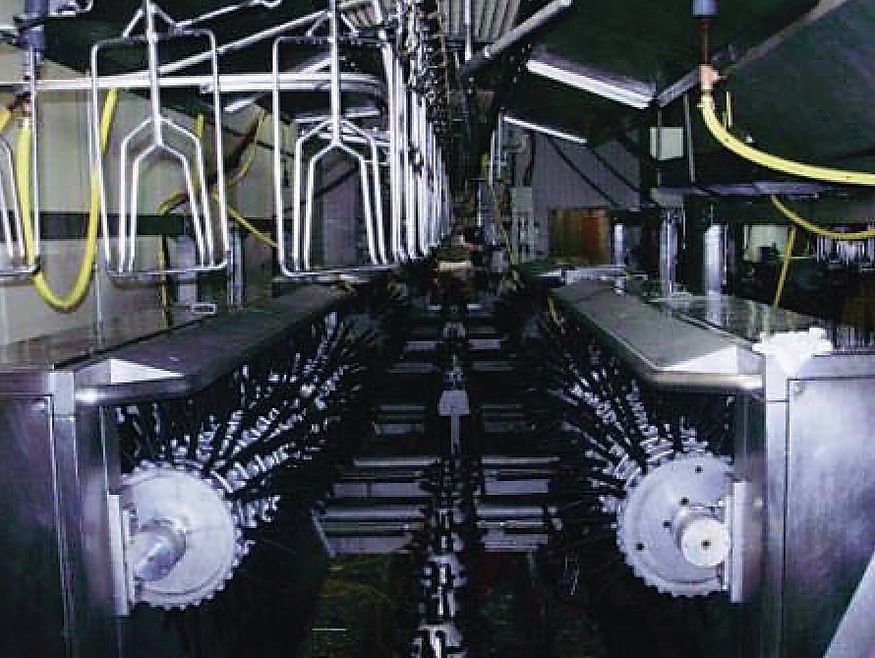
Figure 6. Food processing plants such as this turkey processing plant that contains a counter-rotating primary picker can be an ideal growth environment for microbes. (Courtesy of Wallace & Associates, Inc.)
Adding to the confusion is drawing the distinction between an antimicrobial pesticide and a preservative. Wallace explains, “An antimicrobial pesticide is designed and added to the lubricant for the express purpose of killing microbes. This chemical must proceed through a very rigorous registration process. Initial registration must be with EPA under FIFRA followed by a third-party registration with an organization such as NSF® through a classification such as HX1 in which the additive can be used in situations where incidental food contact is possible. Once registered, the antimicrobial pesticide will be incorporated into a finished food grade lubricant and registered in a category such as H1.”
A preservative fulfills a different function in just protecting the lubricant from decomposition. Wallace says, “The sole purpose of a preservative is to prevent the lubricant from degrading due to water, oxygen, microbes or any other known contaminant or threat. This type of product makes no claims to function as an antimicrobial pesticide.”
Two products are registered as antimicrobial pesticides that are eligible for use under HX1. One of the compounds is para-chloro-meta-cresol, while the other is proprietary. Several preservatives such as sodium benzoate are on the GRAS (Generally Regarded as Safe) list, which makes them eligible for use in food grade lubricants. Some of these components are designated as Edible Food Additives, which are used to preserve food itself.
Wallace adds, “Research is underway to determine if such natural ingredients such as clovers, oregano, thyme, paprika, garlic and cinnamon are under consideration for use as antimicrobial pesticides. The lauric ester of the amino acid l-arginine is also under evaluation.”
The biggest issue raised in using an antimicrobial pesticide in a food grade lubricant is whether it is necessary. Wallace says, “The primary advantage to the end-user of lubricants intentionally treated for antimicrobial registration is the knowledge that his lubricant and his brand are not endangered by microbes at the lubricant machine interface. The greatest disadvantage is the extra costs associated with the process of inoculating the lubricant, if it does not inherently have an antimicrobial property. There has never been a documented case of a lubricant failure due to the absence of an antimicrobial pesticide.”
Additional questions then need to be answered by the food industry and suppliers of food grade lubricants. Wallace says, “If the antimicrobial pesticide is not necessary, is it allowed in the lubricant? Does the inherent antimicrobial activity of the lubricant make the claim of antimicrobial properties unnecessary? Should it really be an actionable circumstance to claim an efficacy that may exist naturally in the food grade lubricant?”
There are no easy answers to these questions as suppliers of food grade lubricants continue to struggle with determining if there is need for using antimicrobial pesticides.
REFERENCES
1. ASTM E2169-01 (2007). Can be obtained at the ASTM Web site: www.astm.org.
2. The primer on biofilms can be found here.
3. Canter, N. (2009), “New Test Method for Detecting Microbes in MWFs,” TLT, 65 (8), pp. 8-9.
4. Passman, F., Whalen, P. and Stachell, D., “Quantifying Adenosine Triphosphate (ATP) in Water-Miscible Metalworking Fluids – ASTM E 2694 Interlaboratory Study to Determine Test Method’s Precision,” To be presented at the 2012 STLE Annual Meeting & Exhibition, St. Louis, Mo., May 6-10.
5. Meyer, D. (2011), “Online Monitoring of the Chemical and Microbial Properties of Metalworking Fluids – The Electronic Nose,” Presented at the 4th Symposium on Metal Removal Fluids: Global Challenges, Barcelona, Spain, September 2011.
6. Passman, F. (2006), “Microbiology of Metalworking Fluids,” in Byers, J. ed., Metalworking Fluids, Second Edition, CRC Press, Boca Raton, Fla., pp. 195-229.
7. Passman, F. (2010), “Current Trends in MWF Microbicides,” TLT, 66 (5), pp. 30-38.
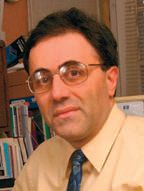
Neil Canter heads his own consulting company, Chemical Solutions, in Willow Grove, Pa. Ideas for Tech Beat can be submitted to him at neilcanter@comcast.net.