STLE’s Certified Metalworking Fluids Specialist
Dr. Robert M. Gresham, Contributing Editor | TLT Commentary March 2012
This certification isn’t easy to get—which is why it’s worth so much.
KEY CONCEPTS
• While plant managers remain under pressure to cut costs, the quality of fluid management cannot be compromised.
• To receive STLE’s CMFS certification, an individual must demonstrate both knowledge and experience.
• CMFS holders use a multidisciplinary approach to solving problems, maintaining quality and protecting plant workers.
THE LAST FEW YEARS HAVE BEEN PRETTY ROUGH ON PEOPLE IN MANUFACTURING INDUSTRIES IN THE U.S. The bedrock of much of manufacturing in this country is the metalworking industry, which is responsible for fabricating many of the metallic components found in products familiar to us all. Despite the typical recessionary pressures to cut costs and increase market share, quality from design to final assembly cannot suffer. Indeed, the recent recall problems experienced by some of the major automotive manufacturers further highlight the necessity for maintaining high quality standards.
Manufacturers for such OEM industries as automotive, agricultural, military, engine (gasoline, diesel and gas turbine), aerospace, as well as the parts suppliers to these industries, must assure that the chemical managers they hire have the best, most qualified, people on site—and back in the laboratory supporting their work. How do MWF users know their employee or supplier is really competent to do the job correctly? Worse yet, how many mistakes (sometimes very costly mistakes) have to be made before a manager knows who should be hired as the MWF problem- solver or which coolant company should be hired as a MWF manager?
The answer is much easier if the in-house problem solver or the supplier has earned STLE’s Certified Metalworking Fluids Specialist™ (CMFS) certification.
What is this certification? The CMFS process is different from many certificate programs where an individual takes a classroom or online course and then takes a test on the material presented. This is not a certification. A true certification seeks to measure whether the individual has both the experience and factual knowledge to solve real-world problems. Thus, certified individuals usually have not only taken several courses and read many books on MWF management but also have spent a number of years in a manufacturing operation gaining experience and honing problem-solving skills in a real-world environment. Thus, in a true certification program, an individual demonstrates this needed experience and proves his knowledge and problem-solving capability through a rigorous examination process. This describes STLE’s CMFS certification.
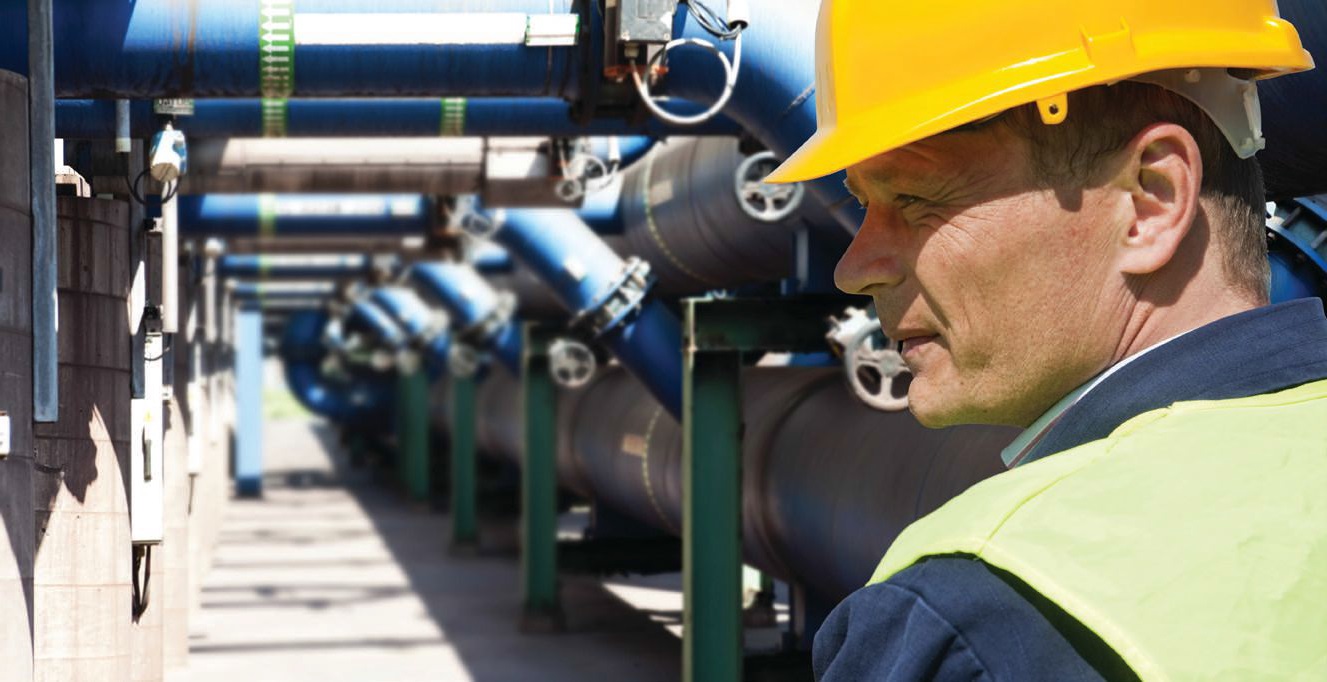
A true certification measures whether the individual has both the experience and factual knowledge to solve real-world problems.
THE PROCESS
Typically, a CMFS is the individual who evaluates and selects the proper MWFs to use, as well as the appropriate fluid-control measures. This individual controls inventories, conducts surveys, trains operating personnel, recommends operating parameters and fluid-handling equipment and troubleshoots MWF applications on the shop floor. Facilitating effective communication between fluid suppliers, end-users, peers and other stakeholders is an essential function of a CMFS-certified individual. This person has broad knowledge of fluid chemistry, machining processes, tooling, filtration, metallurgy and waste treatment.
CMFS holders are those individuals who have met a rigorous set of minimum standards:
Experience
• For individuals working in a manufacturing environment such as a fluid specialist or fluid manager, the requirement is three years.
• For individuals working in a laboratory environment such as a technical support chemist or research chemist, the requirement is five years.
Knowledge
• Minimum: two-year degree in science, manufacturing technology or business; coursework, including general chemistry and biology; minimum 20 hours internal or external training in MWF applications and management.
• Recommended: four-year degree in science, engineering or business; coursework, including chemistry and biology; familiarity with inventory management.
Written Examination
• A rigorous multiple-choice examination featuring many scenario- type questions based on actual plant problems that are designed to measure the individual’s knowledge, experience and problem-solving capability.
Industry standards for the certification are established by members of STLE’s Metalworking Fluids Certification Committee. The committee is dedicated to assuring the industry that the CMFS-certified individual is qualified to provide technical consultation in the field of MWFs management. The designation isn’t easy to get, which is why it’s worth so much.
What can an employer expect a CMFS holder to bring to the operations? At the top of the list are problem- solving skills, which require knowledge of metalworking operations and processes and the attendant issues of swarf removal, mist control, employee exposure, part storage and handling. You also can expect your CMFS employee to understand control of fluid chemistry, contamination control and waste treatment, all key components in fluid management. Not to be forgotten, the fluid manager also must be able to help develop methods for controlling and reducing costs while maintaining production quality and productivity.
Here’s a true example of how CMFS can help your operations:
An OEM powertrain engine plant typically uses a large (20,000 gallons and up) central coolant system to handle multiple operations on a particular part. Several years ago, an engine plant that machines aluminum blocks experienced operational difficulties with a soluble (emulsifiable) oil coolant being utilized in a 120,000-gallon central system. These difficulties included plugging of nozzles, filters and a layer of a greasy material on the surface of the sump. Production management was upset with the chemical manager, who had made several unsuccessful attempts to rectify the problem.
A CMFS-certified individual was brought in to help solve the problem. Using a multidisciplinary approach (including observing similar operations in the plant, utilizing available laboratory data and communicating with numerous persons such as plant personnel and supplier R&D personnel) he recommended several solutions, including modifying the coolant formula. Result: problem solved.
This type of approach, including being on the plant floor and not relying solely on single-point sources of information and data, is encouraged in the suggested reading material and training courses offered by STLE.
Now is the time to act. With recessionary pressures continuing, maintaining a competitive edge is critical not just for maintaining profitability but for survival itself. Further, the regulatory environment continues to tighten restrictions on the metalworking industry. Beyond employee health and safety issues, which have been at the fore in recent years, we are now addressing the impact of operations on air pollution as evidenced by the recent activity on VOCs of MWFs by the South Coast Air Quality Management.
How is a company to survive under these pressures? That’s a good question. The answer? Employ Certified Metalworking Fluid Specialists.
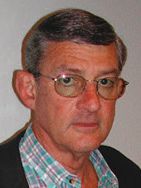
Bob Gresham is STLE’s director of professional development. You can reach him at rgresham@stle.org.