Complexity in oil analysis information: Part II
Jack Poley | TLT On Condition Monitoring January 2012
We now come to the crux of oil sampling—the evaluation.
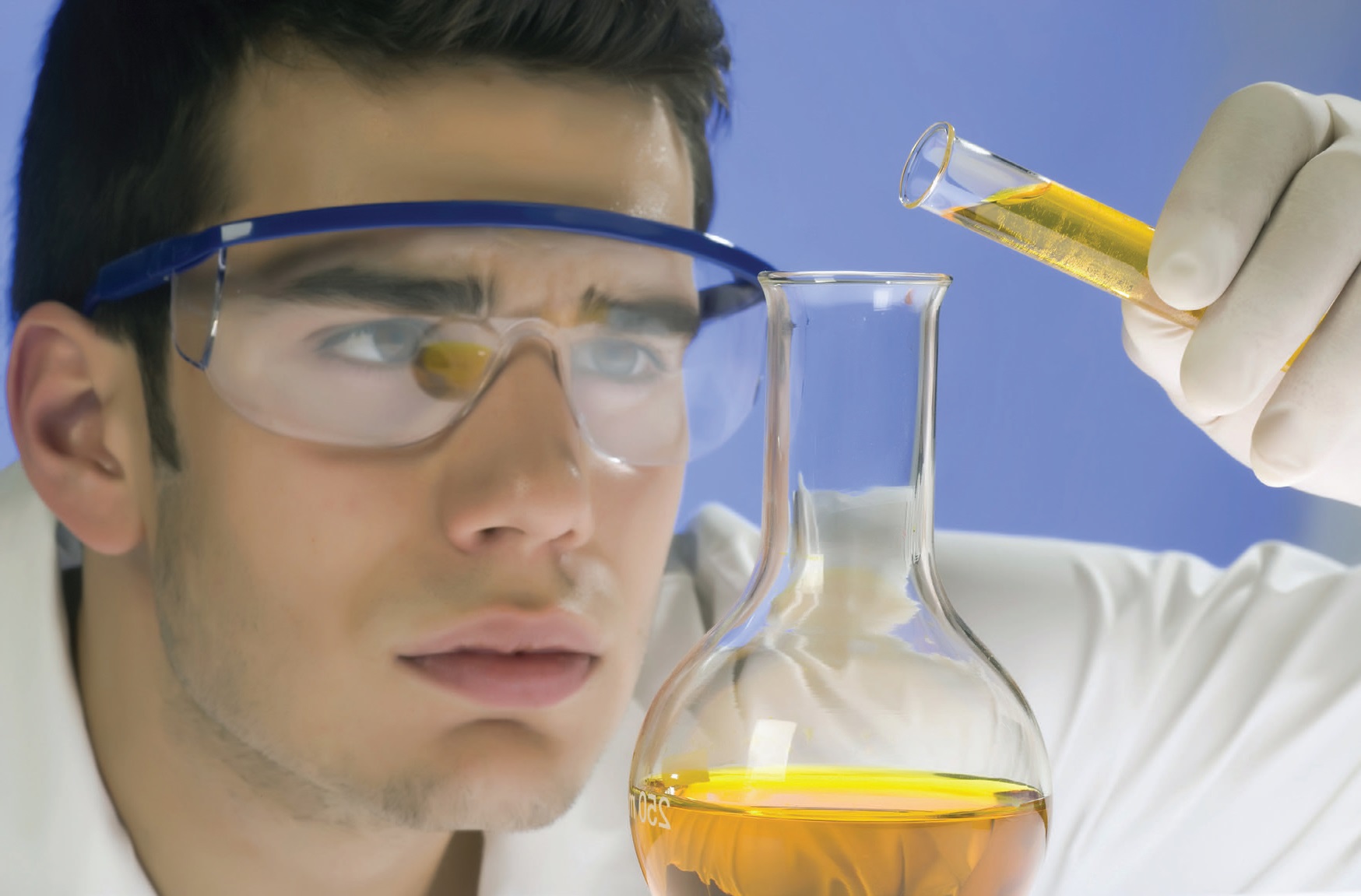
www.canstockphoto.com
DURING THE EARLY 1960s I was interviewed by a writer for
Popular Science magazine. It was when I first became involved in oil analysis (OA) working for the first commercial lab that used a UV spectrometer for measuring wear, contaminant and additive metals. This was the beginning of commercial OA as we currently know it, where the machine took precedence over the oil, and condition monitoring began— though it didn’t have a name then. That would come 25 years later.
In the interview I simply explained what we did, how we did it and why it worked. The writer cleverly suggested the analogy of going to a physician, for example, submitting to a blood sample and then discussing the results with the doctor to arrive at a decision as to possible treatment. Indeed, the medical analogy was perfect, if a bit haughty. OA in those days had very little sophistication except for the multielement, semiautomated UV spectrometer invented by Walter Baird that enabled cost-effective testing for most oil-wetted systems. The interview was indelible because that same analogy was in the text of the article—with the quote attributed to me!
TESTING PROCEDURES
So is OA (including fuels and coolants) now sophisticated enough to be compared to the blood work analogy? With some leeway, yes. The rub, however, is that the physician is, and has always been, in last position in this arbitrary scenario.
OA has been around as a commercial offering for more than six decades. Millions upon millions of samples are submitted for analysis these days. Contracts are based on testing to be performed. Nowhere is it stipulated that an evaluation (interpretation, data analysis, etc.) of any kind will be performed. It is unfortunate that the most critical aspect of OA (what to do?) is taken for granted and otherwise shunted off to the side. Admittedly, in captive private systems, the needed (and usually effective) evaluation may be available via personnel onsite. Based on my experience, this is exceptional and not the norm.
The
correct analogy for OA and medicine, therefore, is that the component’s ‘blood sample’ is tested and a comment may or may not be included and may or may not be relevant or complete. OA is sold by the test, not the opinion. So opinions are free and, in a lot of cases, that’s what they’re worth.
Times are, in fact, changing, but old habits and procedures don’t simply disappear or get replaced with better habits and procedures overnight. In the case of testing itself, procedures are constantly being changed and improved (some of that depends on how well these procedures are followed), but evaluation has lagged until fairly recently. What’s changed? Computerization and purpose-specific software.
We rely increasingly more on computers to perform tasks better than we do. Sometimes the computer is misapplied, but the point is valid. OA Evaluation (OAE) is one of the tasks that can now be relegated to software. What has emerged is the development of Expert Systems (exsys) and Intelligent Agents (a more sophisticated exsys that likely includes pattern recognition) that can perform qualified OAE with relentless consistency. Isn’t consistency what we need in any OAE? Certainly, as long as it’s not consistently incorrect (but when it is, we can correct it system-wide, resulting in a permanent fix). An intelligent agent that is properly managed can constantly be improved as fresh knowledge and experience are appropriately injected to and absorbed by the software trampling valid algorithms already in place.
Following are three primary areas in the rendering of an OA report:
1.
Rating data for severity and rate of change (trend)
2.
Assessing the data ratings ensemble and providing an opinion for:
a.
Machine Condition (wear, primarily)
b.
Lube Condition (degradation, contamination, incorrect product, etc.)
c.
Follow-up Action or not (lube/filter maintenance, accelerated sampling, diagnostics, teardown/inspection, etc.)
3.
Rendering a report that is easy to understand for people not directly involved in the OA process—
the report recipient (there could be a CMMS in the middle).
RATING DATA
This is actually not a difficult task on the surface, but there are caveats and nuances to consider. Given one has a sufficient statistical quantity of like or similar data, a statistical algorithm can be applied to yield data thresholds for notable, abnormal, high and severe ratings. Here are some of those nuances:
•
Component type and parameters. “Like data” can have several levels of conformity. If we say “hydraulic,” what does that really mean? It means any machine that performs a (mostly) hydraulic function. In a large plant, there could be numbers of hydraulic systems, but they could have vastly different mechanical characteristics. Consider types of hydraulic pumps: vane, gear, axial-piston, centrifugal, e.g. Each is a specific type of pump that has parameters not related to its neighbor. It would be foolish to lump all these types of hydraulic pumps into a single statistical analysis, then expect good data ranges to work with.
•
Manufacturers and models. Given that we are meticulous in isolating each differing component type (the first key and essential information in performing an evaluation), we should now look to see if we have different manufacturers involved with each component type. If so, and there are sufficient samples (usually, at minimum, 30-50 samples from at least 4-10 unique components), we can carry our statistical process down to the manufacturer level. Logically, we can go the model level, as well, given the data are available in sufficient quantity.
In the next column, we’ll continue our discussion on application considerations, along with comment rendering and report delivery.
Jack Poley is managing partner of Condition Monitoring International (CMI), Miami, consultants in fluid analysis. You can reach him at jpoley@conditionmonitoringintl.com.
For more information about CMI, visit www.conditionmonitoringintl.com.