‘Metal Removal Fluids: Global Challenges’
Dr. Robert M. Gresham, Contributing Editor | TLT Lubrication Fundamentals December 2011
The fourth symposium in this series featured an all-star lineup of speakers and revealed seven industry-changing trends.
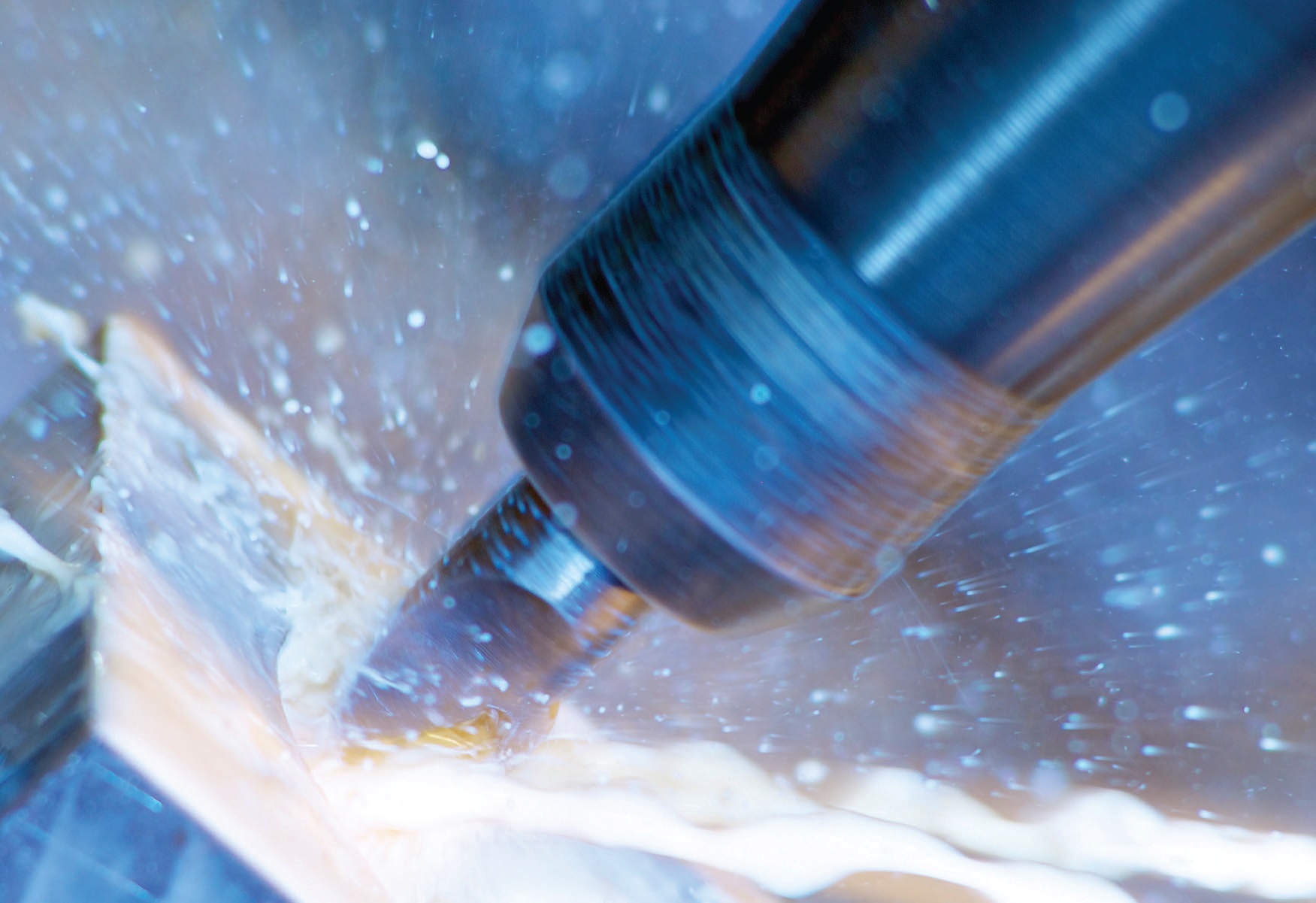
www.canstockphoto.com
KEY CONCEPTS
• The fourth metal-removing fluids symposium united government, union, industry and safety/health organizations.
• Focus was on discussing and debating current knowledge related to worker exposure in the MWF industry.
• MWF-producing companies must become leaner, more efficient and better managed with an emphasis on sustainability.
WITH THE INDEPENDENT UNION OF THE EUROPEAN LUBRICANT INDUSTRY (UEIL) as the lead organization, STLE was pleased to partner with ILMA in hosting the fourth symposium on Metal Removal Fluids: Global Challenges. This year’s event was held in beautiful Barcelona, Spain.
By way of background, the first symposium in this sequence was held in 1995 in the heart of the U.S. motor industry in Dearborn, Mich., and was sponsored by the American Automobile Manufacturers Association in cooperation with a number of U.S.-based union, industry and health and safety organizations. The emphasis was on bringing together key figures from industry, academia and government-based health and safety-orientated organizations to discuss and debate current knowledge related to worker exposure in the metalworking fluids industry.
The initial symposium was successful and relevant and swiftly followed by a second symposium in 1997. The second event featured a similar format but concentrated on issues like total system management and hypersensitivity pneumonitis, which had developed into a key issue in the two-year interval.
It was not until 2008 that ILMA, in association with UEIL and STLE, recreated the symposium in a slightly different format, again back in Dearborn. The emphasis was still on health, safety and environmental issues, but sessions on regulatory status, sustainability and future trends were added.
The fourth symposium began with a keynote presentation by Lufthansa’s Manfred Muller on building teamwork to manage risk. (Editor’s Note: For an in-depth treatment on Muller’s presentation, see Lube Fundamentals in the November TLT at www.stle.org.) The keynote session was followed by 37 presentations divided into three technical tracks: innovation, application and regulation.
While all the presentations were on point, some stood out, at least to me. From a business perspective in the application track, Boeing’s Brian Hovik and Dragos Axinte, Rolls Royce University Technology Centre of the University of Nottingham, talked about the process for getting approvals to Boeing and Rolls Royce specifications. Michael Rocker, Berufsgenossenschaft Holz und Metall, discussed the German standards that are widely used in Europe. Finally, Milind Phadke with Kline provided market information on the metal-removal fluid markets in Asia, Europe and North America.
Asia is defined in order of size primarily by China, Japan, India and South Korea followed by a rapidly growing Thailand (which we hope won’t be significantly slowed by the October floods that traumatized the country). Europe is similarly defined as Russia, Germany, France, Italy, the United Kingdom and Spain. North America is defined as the U.S., Canada and Mexico.
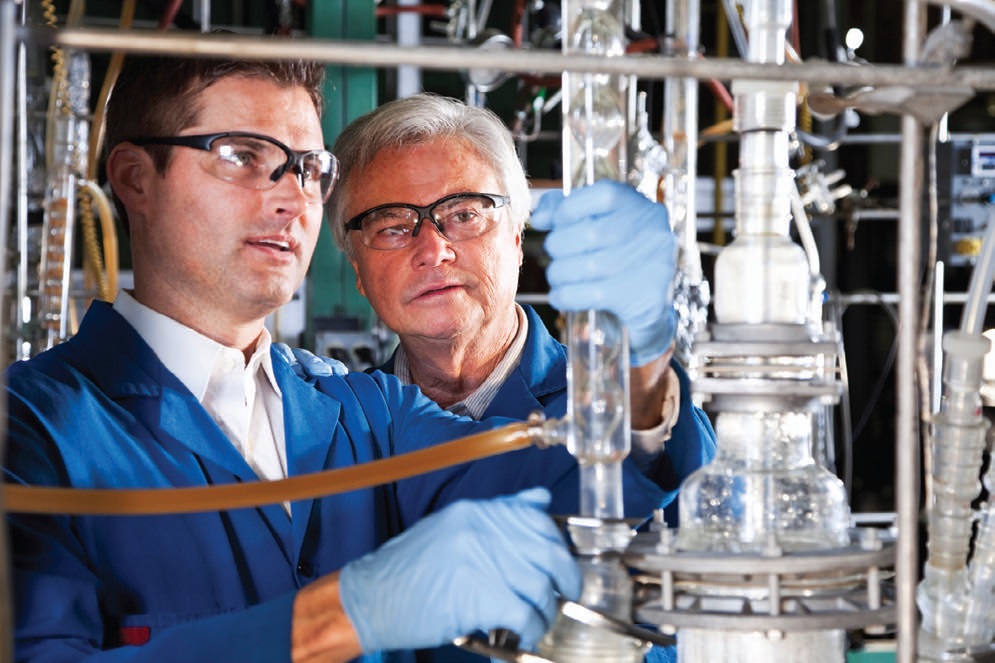
www.canstockphoto.com
Of significance has been the extraordinary growth of the Asian markets. During the last three years, the Asian marketplace has grown about 8% while the European market declined about 3% and North America about 6%. Fortunately, it appears that most suppliers enjoy a global business, allowing them to shift their sales from one area to another as market and economic forces dictate. The downside is the global market is projected to grow at a tepid 3% with Asia, Europe and North America at 5%, 2% and 1%, respectively.
The innovation track featured a number of outstanding presentations. Beginning with STLE-member John Burke with Houghton International, we took a look into the crystal ball to see how many and varied factors will affect companies in the MWF industry that are still trying to make a profit—without which survival is not possible. Of these, seven major factors emerge:
1. Operation of the factory of the future
2. Organized labor restrictions
3. Targeted chemicals
4. Government regulation
5. End-user restrictions
6. Formulator restrictions
7. Public pressure to change.
In order to manage these factors, companies will need to invest significant R&D resources in the face of an overall decline in the number of gallons of MWF used. They also will need to operate their businesses globally, and their products and processes, including waste management, must be managed sustainably. Clearly, only lean, well-managed companies will survive.
As examples of the responses to the seven factors John Burke identified, Lubrizol’s Frank Kroto discussed a new family of low-volatile organic compounds (VOCs) rust preventatives that do not contain heavy metals and are removable with aqueous cleaners. Steven Anderson with Afton Chemical in the U.K. discussed his company’s work on developing environmentally friendly EP additives for MWF applications. John Belien, Quaker Chemicals, The Netherlands, discussed studying the effects on overall performance of changing the pH buffer system in emulsifiable coolants.
I was particularly intrigued by a presentation by Daniel Meyer with the Foundation Institute of Materials Science, Bremen, Germany. He discussed work to design a gadget to detect microbial activity with an “electronic nose.” Currently, such activity is detected with slow, marginally accurate dip slides. The emerging technology essentially allows for continuous, online detection. As John Burke observed, if this works the technology conceivably could detect drugs and explosives.
Also in the application track, Stefan Fennrich, University of Tubinge, Germany, discussed a novel in vitro pyrogen test. These pyrogens (fever-inducing substances) can originate from bacteria, viruses, fungi and parasites that, in turn, can grow in MWFs and present exposure hazard to operators. The build-up of biofilms in metalworking systems also is a major problem in managing these fluids. Chuanwu Xi, University of Michigan School of Public Health, showed that microbial populations are much higher than is typically found using dip slide methods.
In the regulatory track, Mike Morris, South Coast Air Quality Management District (SCAQMD) discussed work done in part with John Burke and Primagy’s John Howell to develop a test method to measure VOCs in MWFs. This is significant, as SCAQMD will issue regulations on the amount of VOCs emitted in Southern California. Until now there was no way to measure these VOCs.
STLE-member Gene White, Cimcool Industrial Fluids, discussed the global trends in regulatory activity for metal-removal fluid products. However, regulation has tended to evolve country by country. With the growing globalization of the metal-removing fluids market and the impact of the factors expected to influence the market, as explained in Burke’s presentation, Gene has challenged the MWF community to form a “global metal-removing fluids consortium” to support proactive industry research projects aimed at developing data, test methods, etc., so intelligent regulations can be written that promote the desired outcome and keep the cost of regulation under control.
Finally, Adrian Krygsman with Troy Corp. reviewed the global regulatory perspective on formaldehyde. This is not a trivial pursuit as the situation is fluid and conclusions seemed to be based on whichever study you choose as a reference. Not good.
Overall the symposium met its objectives, the primary one being to unite industry, academia and the government under the auspices of UEIL, ILMA and STLE. The three organizations are already discussing collaborating on another event. That’s good news for us all.
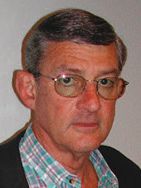
Bob Gresham is STLE’s director of professional development. You can reach him at rgresham@stle.org.