The diesel dilemma
Drs. Wilfred T. Tysoe & Nicholas D. Spencer | TLT Cutting Edge December 2011
Studying soot on the nanometer scale helps us understand its role in engine wear.
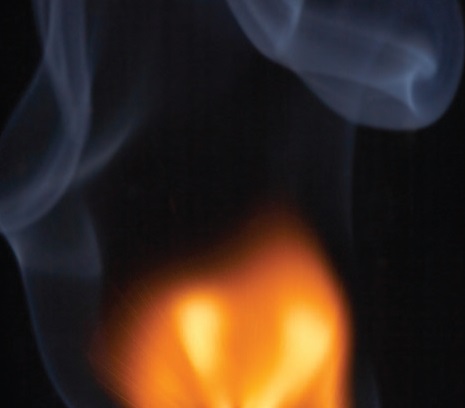
Flame temperature, in particular, seems to play an important role in tribological behavior of the soot.
REDUCING HARMFUL EMISSIONS from automobile engines always involves tradeoffs. In diesel engines, there is the choice between soot production and the formation of nitrogen oxides (NO
x). In the diffusion flame that characterizes the diesel combustion process, increasing the amount of oxygen leads to soot reduction and greater NO
x emission, while reducing oxygen consumption reduces NO
x emission but increases soot. This is sometimes known as the “diesel dilemma.”
Since NO
x and soot emissions from automobiles are both highly regulated, it is almost inevitable that there will be some degree of soot produced by modern diesel engines. Of course soot does not only end up in the tailpipe; a significant fraction enters the lubricating oil, and that is where our tribological story begins.
There is considerable literature on the effects of lubricant soot content on engine wear, and the field is complex. On the one hand, there may be simple abrasion of some engine components by hard soot particles. On the other hand, soot has been reported to interact chemically with antiwear additives, either by adsorbing them, reducing their availability to the wearing surfaces, or by removing them from the contact regions.
Simultaneously, soot can even have a beneficial effect on wear, increasing oil viscosity and, therefore, film thickness. The latest efforts to understand the behavior of soot (
1) have been reported in the STLE affiliated journal
Tribology Letters by Hiralal Bhowmick and professor Sanjay Biswas of the Indian Institute of Science in Bangalore, India.
Bhowmick and Biswas have created a model soot by burning ethylene, but what makes their study unusual is that they have extracted individual soot particles from different parts of the flame and measured their sizes and crystallinity by high-resolution transmission electron microscopy, hardness by nanoindentation and tribological properties by lateral force microscopy in an atomic force microscope (AFM). In order to correlate these properties with behavior in other flames and with other reports in the literature, the researchers also carried out careful temperature measurements at different parts of the flame.
The particles appeared to be around 21 nm in diameter and slightly larger in the cooler parts of the flame. However, the morphology varied significantly from completely amorphous at the root of the flame (1,665 K) to amorphous but surrounded by a columnar crystalline shell (which was graphitic with long-range order) in the hottest part of the flame (1,689 K). As the particles move into the cooler part of the flame (1,657 K), the amorphous core gradually shrinks, and the majority of the particle consists of small crystallites embedded in an amorphous phase.
Nanoindentation measurements, which were carried out by holding the particles in position on a silicon wafer with a 10 nm PMMA layer, revealed that the hardness of the particles increases significantly (from 3 to 4.5 GPa) upon going from the hottest to the coolest part of the flame, while the friction coefficient (as measured by a DLC-coated AFM tip) appears to increase concomitantly. By repeated scanning of the AFM tip over individual particles, the amount of removed material as a function of applied load could be determined. While this measurement was only semiquantitative, it was found that the particles taken from the hottest part of the flame, i.e., those with the graphitic shell, were most prone to material removal, presumably due to the weak interlayer bonding.
The hardness of the hardest soot particles formed in these model experiments (3 to 5 GPa) was not so far away from that of cast-iron engine liners (5 to 7 GPa), meaning that abrasive wear of the liners is a possibility and wear of the additive-produced layers even more likely. Clearly these careful experiments indicate that soot particles can span such a relatively wide range of morphologies—and therefore different mechanical and tribological properties—that there is not one single answer to the question of how soot affects engine wear.
Flame temperature, in particular, seems to play an important role in tribological behavior of the soot. Further experiments involving soot-additive interactions are now clearly needed.
FOR FURTHER READING:
1.
Bhowmick, H. and Biswas, S.K. (2011), “Relationship Between Physical Structure and Tribology of Single Soot Particles Generated by Burning Ethylene,”
Tribology Letters,
44 (2), pp. 139-149.
Eddy Tysoe is a Distinguished Professor of Physical Chemistry at the University of Wisconsin-Milwaukee. You can reach him at wtt@uwm.edu.
Nic Spencer is professor of surface science and technology at the ETH Zurich, Switzerland. Both serve as editors-in-chief of STLE-affiliated Tribology Letters journal. You can reach him at nspencer@ethz.ch.