Operating life of a lubricant
R. David Whitby | TLT Worldwide November 2011
To achieve optimum machine productivity, select the correct lubricant to use, monitor and maintain.
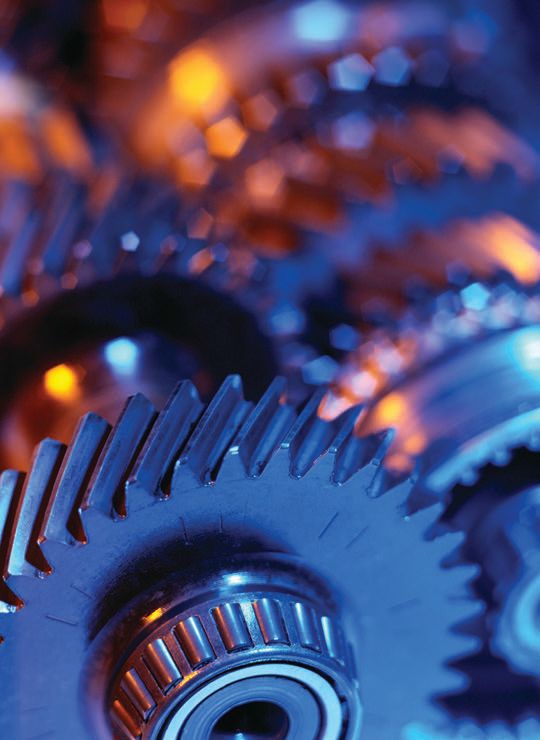
In many lubricants, rapid separation of water from the oil is very desirable such as in gear oils.
www.canstockphoto.com
THERE ARE SIX FACTORS THAT AFFECT the operating life a lubricant: (1.) oxidation, (2.) thermal degradation, (3.) contamination, (4.) foaming, (5.) air release and (6.) demulsibility. Of these oxidation is the factor that most often limits the lubricant’s useful life. However, all of them affect the ability of a lubricant to lubricate.
Oil or grease-oxidation products are volatile and non-volatile acids and polymerized products (sludge and varnish). Severely oxidized oils tend to become very viscous at low temperatures and may gel. As a result, they are not pumpable, so lubricated surfaces will be starved of lubricant, causing severe wear and eventually seizure.
Volatile and non-volatile acids attack white-metal bearings, can be water-soluble and are more aggressive when the lubricant is wet. They also promote the generation of sludge, varnish and emulsification and inhibit air release. In addition, they can interfere with the action of antiwear, antirust and corrosion-inhibiting additives. Varnish and sludge increase oil viscosity, decrease viscosity index, reduce heat transfer abilities, block oil ways and promote foaming and emulsification.
Oils can crack at high temperatures in the absence of oxygen. Thermally degraded oils form carbonaceous residues and volatile gases. Volatile products lower the flash point of the oil and are a safety hazard. Residues can deposit on hot surfaces and insulate them, causing heat build-up in other locations. The tendency to form deposits can increase rapidly. In general, these deposits on metal surfaces are not able to function as lubricants.
Contamination is probably the most common cause of oil failure or rejection. Some contaminants can have a major influence on the properties and performance of the lubricant, affecting aeration, foaming, air release and demulsibility. The most common contaminants of oils or greases are water, fluid-soluble materials, fluid-insoluble materials, erroneous fluid additions and fluid degradation.
With aeration, entrained bubbles of air in oils can cause reduced compressibility of hydraulic fluids, reduced volumetric efficiency of hydraulic system pumps and loss of power transmission efficiency due to the amounts of energy absorbed by compression. Aeration also can cause cavitation damage in pump suctions and servo-valves, inadequate response times for turbine over-speed systems, localized oil oxidation in highly loaded regions such as thrust bearing pads and white-metal bearings and interference to oil flow through filters. Excessive air entrainment and poor air release also can contribute to oil foaming.
Air release is significantly affected by oil viscosity and temperature. Air release values for oils are increased by high oil viscosity, low oil temperature, contamination by diesel engine oils, greases and corrosion preventives, the presence of rust particles and contact with very hard water.
Foam is not a particularly good lubricant. Air/oil foam can accumulate in the headspace of reservoirs, gearboxes, crankcases, sumps and other components with vapor spaces. Excessive foam may be forced out of the reservoir through the breather cap or may be ingested into the circulation pump, as well as interfere with the effective lubrication of gears and bearings.
In many lubricants, rapid separation of water from the oil is very desirable, particularly for turbine oils, gear oils and hydraulic fluids. Water tends to separate from most types of oils due to the differences in density. The separation of small droplets of water can be assisted using centrifuges or coalescers. However, poor oil or grease demulsibility can cause corrosion of ferrous metals, significant reduction in the fatigue life of ball bearings, roller bearings and gears and the removal of rust inhibitors and some antiwear and lubricity additives from oils.
The lubricants used in a machine are just as important as any other component of the machine. Ensuring that the correctly selected lubricant is used, monitored and maintained properly is very important to optimum machine productivity.
David Whitby is chief executive of Pathmaster Marketing Ltd. in Surrey, England. You can reach him at pathmaster.marketing@yahoo.co.uk.