The Lubrizol Corporation
Clean and Keep Clean
Productivity Enhancements Using Lubrizol Clean Hydraulic Oil Technology
By Dave Oesterle, Product Manager, Hydraulics, The Lubrizol Corporation | TLT CMF Plus November 2011
It’s a common theme in today’s industry: systems are becoming smaller and more compact, but productivity is expected to increase. The hydraulic equipment market is no different. Equipment reservoirs are small and contain less oil, which means that fluid is circulating through the system much more rapidly. The impact on the fluid is significant since these new shorter cycle times don’t allow for cooling or the settling of contaminants. Harsher environments also can result in higher temperatures and higher pressures, which in turn, contribute to the rapid formation of varnish. Varnish plates onto system parts – like valves – reducing tolerances and resulting in valve sticking and equipment related downtime. According to reports from original equipment manufacturers, the tougher operating environment is leading to more frequent problems in higher performance systems.
Lubrizol’s research showed that off-the-shelf hydraulic packages were not addressing the varnish issue in modern hydraulic equipment. Our goal was to develop technologies that could clean up varnish in the first place and keep it clean in the long run. But, as a first step, we listened to the voice of the end user.
End User Research
To get a sense of the issues that matter most to hydraulic equipment operators, Lubrizol surveyed end users across a wide range of applications regarding their primary concerns. We talked with engineers, managers, vice presidents and owners and solicited their thoughts and ideas on how to improve hydraulic operations. Extending equipment life and reducing downtime were identified as major needs by end users.
See Chart 1.
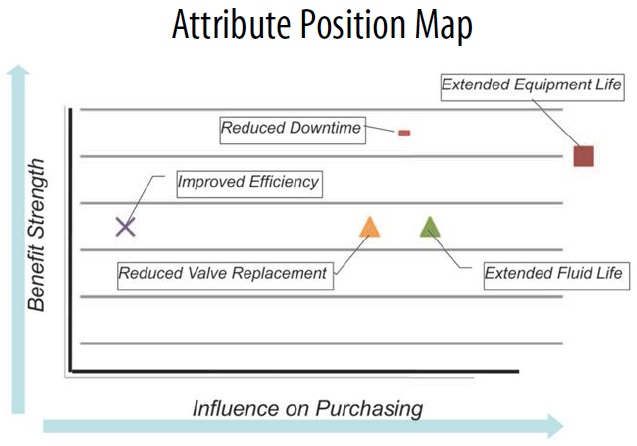
Chart 1. The attributes position map illustrates equipment users’ most significant needs as identified by our survey respondents. Respondents included users of both stationary and mobile equipment.
Using the results from the survey as a guide, Lubrizol was able to tailor a cleaning technology designed to meet the demands of modern hydraulic equipment.
Clean Up: Introducing Lubrizol® 6786
Today’s equipment end users face a dilemma. Their equipment is coated with varnish and contaminants, which can gradually increase the cycle time necessary to make a part, resulting in a loss of productivity. However, the downtime to clean machines can be costly, and existing cleaners can present health and safety issues. The solution: Lubrizol® 6786 Industrial System Cleaner. This new cleaner can be added to equipment
while it is running, at concentrations of up to 20%. Lubrizol 6786 works to remove varnish while the machine works to produce parts, eliminating downtime typically associated with cleaning. Alternately, the cleaner can also be used in a static bath. And, because it is not solvent-based, health and safety concerns are greatly reduced.
To test the efficacy of Lubrizol 6786, we conducted a lab test using an Eaton-Vickers 35VQ25 vane pump. The test was run for 1000 hours to allow for the formation of varnish precursors in a typical mineral-based hydraulic fluid. The initial varnish rating on a valve (that was taken from a field application) was 5.5 (on a scale of 1 to 10, where 1 is the dirtiest and 10 is the cleanest). We then added 20% by volume Lubrizol 6786 to the used fluid (from the 1000 hour pump test) and circulated this mixture at 140ºF over that spool. The mixture of the used hydraulic fluid with the cleaner added to it was allowed to circulate across the spool for a period of seven hours. After seven hours, the spool received a near pristine rating of 9.5.
See Figure 1.
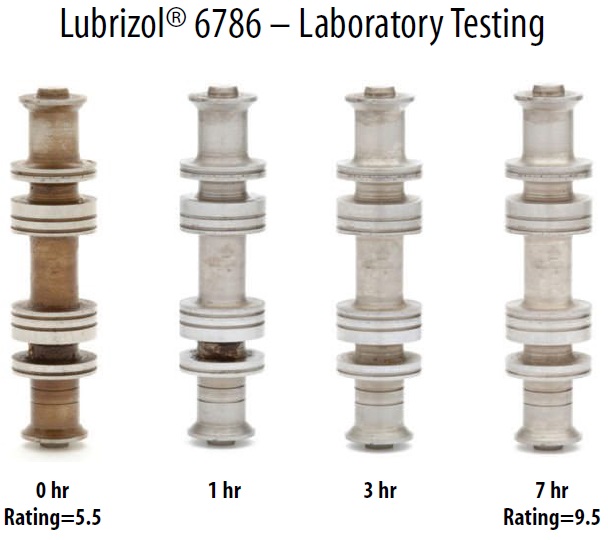
Figure 1. Spool cleaned with Lubrizol 6786, rated at 0, 1, 3 and 7 hours.
Some equipment end users prefer to pull parts out of the equipment for cleaning and may discard valves considered too damaged by varnish to save. To determine Lubrizol 6786’s effectiveness in this scenario, spools were taken from a piece of hydraulic equipment. The spools pulled from the valves were rated as “heavily varnished” by a valve refurbishing company. The spools were then submerged in Lubrizol 6786 fluid at room temperature, with no fluid circulation, over a 48 hour period. As illustrated in
Figure 2, the spools cleaned up beautifully, eliminating the need to purchase new valves, which can represent a significant cost savings.
Figure 2. Valve spools immersed in Lubrizol 6786 Industrial System Cleaner for a total of 48 hours. Samples of Lubrizol 6786 are available for you to try this test on your varnished and contaminated valves. Contact your Lubrizol sales representative for more details.
The Next Step: Field Testing
Lubrizol 6786 delivered outstanding performance in lab testing. Our field testing took place in an injection molding machine shop. As molten plastic is poured into molds, these systems can get hot. They operate under extreme conditions, making them the perfect test subject for Lubrizol 6786.
In preparation for the test, we gathered operating system data, selected specific parts to observe, took oil samples and established the right concentration of Lubrizol 6786 for use. Prior to treatment, photos were taken of parts selected for observation. To install the cleaner, some of the hydraulic fluid was removed from the machine, and the cleaner was introduced into the system under turbulent conditions as the machine continued to make parts. Oil samples were taken at prescribed intervals. The test ran for 48 hours. At that time, oil samples were analyzed, system parts were removed, rated and photographed and pre and post cleaning parts were compared. The results speak for themselves.
See Figures 3, 4 and 5.
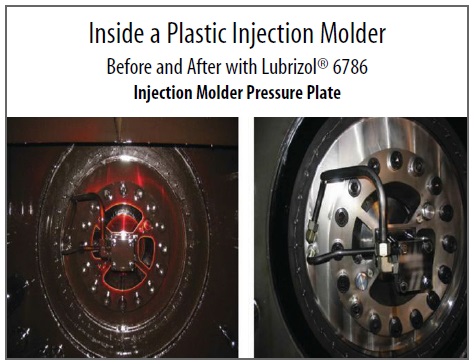
Figure 3. Injection molder main ram pressure plate, before and after test.
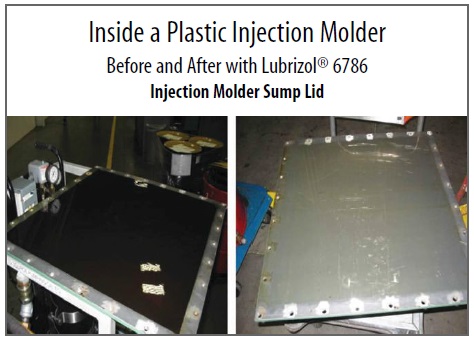
Figure 4. Injection molder tank hatch door, before and after tests.
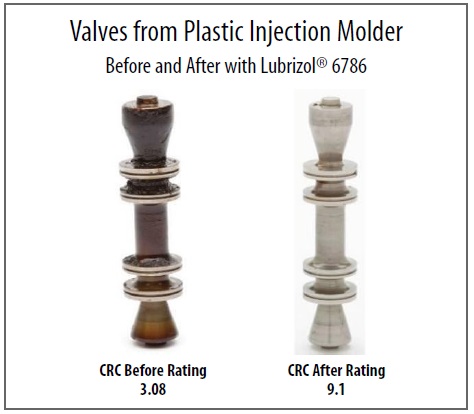
Figure 5. Valve spools, before and after test.
Performance testing has shown that Lubrizol 6786 removes varnish build up and sludge (which can decrease productivity) and helps eliminate valve sticking due to the presence of varnish. It also significantly reduces equipment downtime when compared to manual cleaning. Lubrizol 6786 is compatible with mineral-based oils and common seal materials. Lubrizol 6786 will also help reduce filter changes over the long term. However, end users should be aware that filters may need to be changed after the initial treatment due to the amount of dirt and contaminants removed from the parts.
Clean and Keep Clean: Lubrizol® 6776A
Once end users have removed varnish from their equipment, they will want to prevent varnish from building up again. Along with Lubrizol 6786, Lubrizol is introducing the second part of the equation, Lubrizol 6776A, an antiwear additive package designed to keep the system clean and free of varnish. Suitable for Group I and Group II basestocks, Lubrizol 6776A delivers high oxidation life to protect components, as demonstrated by performance in the ASTM D943 test:
Group I ExxonMobil AC
4500 hours in ASTM D943
Group I CEPSA (high sulfur)
3024 hours in ASTM D943
Group II Chevron RLOP
7050 hours in ASTM D943
The new additive package also delivers excellent wear, rust and corrosion protection and outstanding filtration in the presence of water. Extended duration pump testing demonstrates the keep-clean performance of Lubrizol 6776A.
Demonstrated Performance
To prove the effectiveness of Lubrizol 6776A, Lubrizol again ran an Eaton-Vickers 35VQ25 vane pump test for an extended 1000-hour interval in a pre-cleaned system. Conventional hydraulic oils start to show tenacious varnish at 500 hours, with varnish observed in both zinc and ashless oils. Comparisons between the performance of standard fluid technology and Lubrizol 6776A can be seen in
Figure 6.
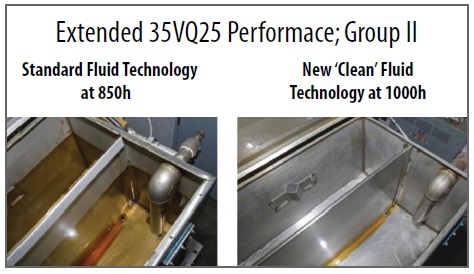
Figure 6. 1000-hour Eaton-Vickers 35VQ25 vane pump results demonstrate that varnish can be mitigated by using Lubrizol 6776A clean technology in a Group II base oil.
In the standard 35VQ25 vane pump test, which runs 150 hours (50 hours each for three different cartridges), Eaton will allow a total weight loss of 90 mg on vanes and rings. Beyond that, the test fails. In the test run with Lubrizol 6776A, over a 1000-hour period, vane loss measured 14 mg and ring loss an impressive 28 mg (a total of 42 mg).
See Figure 7.
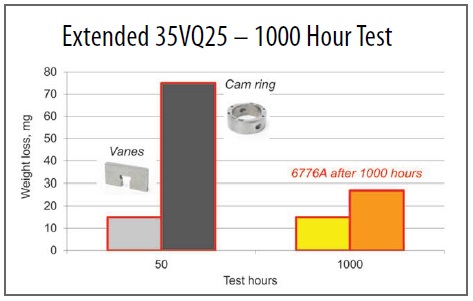
Figure 7. Lubrizol 6776A exceeds OEM requirements after extending the test 20 times longer than normal limits.
By using Lubrizol 6776A, the hard-to-clean varnish that typically occurs at 500 hours was not present, even after 1000 hours.
Clean and Keep Clean – The Right Combination
Together and separately, Lubrizol 6786 and Lubrizol 6776A, accomplish the goal of delivering the performance attributes requested by end users and identified in Chart 1. Using these clean and keep clean technologies can provide extended fluid life, reduced valve replacement, better efficiency, extended equipment life and reduced downtime.