The Human Element: Labor and skills management
Mike Johnson, Contributing Editor | TLT Best Practices November 2011
Why it’s well worth the investment to hire dedicated lubrication personnel.
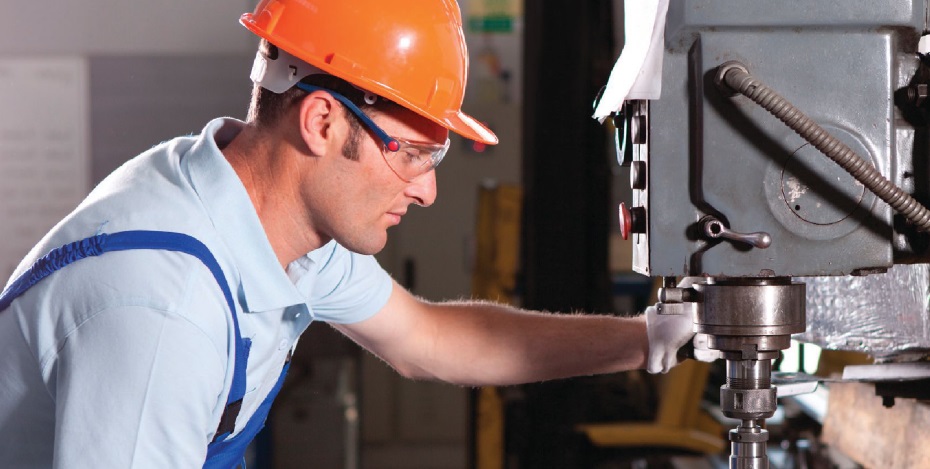
www.canstockphoto.com
KEY CONCEPTS
•
Too often plant labor divides its time between working part-time on mechanical repairs/inspections and part-time on lubrication activities.
•
In this scenario, the tyranny of the urgent supplants the value of the important, and lubrication tasks go unattended.
•
The solution is hiring a full-time lube tech with the right combination of general business and communication skills plus an aptitude to develop lubrication-specific knowledge.
HOW MANY TIMES HAVE YOU SEEN A COMPANY MISSION STATEMENT proclaiming that its most important asset is its people? Of course, that’s not entirely true. A manufacturing company’s most important asset is its productive capacity. That derives from a combination of people, machines and infrastructure. People are a part but only a part. That notwithstanding, certainly people are important. In the machine reliability world, one of the most important groups of people is also one of the most overlooked.
Carl P. Owens, Jr., a former boss and exceptional mentor, used to tell his audience during training activities that the most important person in the manufacturing plant was the oiler, now referred to as the lube tech. Not the mechanic. Not the maintenance manager (who was typically paying for the training). Not the production manager. Carl understood this from the inside out. He spent the first half of his highly productive career doing maintenance and process engineering, then engineering management, then site management for a large electrical parts manufacturing company. His final role in the manufacturing plant, held for several years, was that of the plant manager.
Figure 1. LUBE TECH JOB DESCRIPTION AND ACTIVITIES
The machine lubrication tech position is responsible for routine machine relubrication using both oil- and grease-based lubricants, as well as several other contributing activities, including lubricant contamination control practices, machine inspections and troubleshooting, automatic lubrication systems inspection and troubleshooting and oil analysis (sample collection and handling, analysis, resolution of issues) for select lubricated mechanical components and systems.
Activities include:
•
Grease relubrication with manual and automatic dispensing equipment.
•
Fill and top-off oil tanks and reservoirs.
•
Change filters and breathers on reservoirs.
•
Drain and clean select reservoirs.
•
Operate filtration equipment.
•
Operate dehydration equipment.
•
Periodically clean and seal reservoirs and oil tanks.
•
Perform maintenance on dispensing equipment and automatic systems.
•
Perform field-level oil analysis, including crackle, viscosity and blotter test.
•
Schedule, collect, label and mail samples for analysis.
•
Perform basic evaluation of oil analysis results and recommend current and future maintenance actions.
•
Make mechanical modification of systems as directed to facilitate sampling and filtration and other proactive improvements.
•
Label and tag reservoirs, equipment, inventory and delivery containers.
•
Print out (or sync-out/sync-in), log and perform planned lubrication activities.
•
Update scheduling systems, including adding notes to computer-based systems as required.
•
Request work orders for maintenance repairs and activities as required.
•
Troubleshoot common lubrication-related equipment problems.
•
Troubleshoot/evaluate work practices and offer suggestions for improvement.
•
Conduct department-specific inventory and routine ordering of products.
•
Stock inventory locations.
•
Safely use hand tools and lubrication equipment for routine and non-routine lubrication functions.
•
Report in writing any discrepancies or conditions that require corrective, predictive or planned maintenance for production systems.
His logic was simple: the rest of those positions can be vacant for a significant amount of time with little change in production. However, eliminate the person(s) responsible for machine lubrication, and machines fairly quickly begin to lose lubricated components. Lost capacity and productivity soon follow.
I have subscribed to this logic throughout my career, offering this anecdotal advice to audiences as well. When reflecting on the importance of this job task with engineers and managers, there is uniform agreement that the job of machine lubrication is indeed vital. No questions asked. Our instincts tell us that the machine won’t run without oil and grease.
Unfortunately, most organizations fail to live up to their declared conviction by failing to either allocate or dedicate smart, motivated people to the task. Further, where labor is provided, in most instances it is either an entry-level (no skills required) or retirement-level (no energy required) position.
This article introduces an argument for dedicated (versus allocated) technicians, and suggest a job description and skills requirement that is appropriate for the job.
Dedicated lubrication labor occurs when management decides that all lubrication program tasks will be completed.
www.canstockphoto.com
DEDICATED OR ALLOCATED?
Each time I provide a lubrication program effectiveness assessment for a plant site, I spend a fair amount of time digging into the actual means of how lubrication man-hours are managed. I find two types of approaches: either allocated or dedicated labor. These seem like trivial differences, perhaps no difference at all, until one digs into how the difference in management approach impacts daily functions.
Let’s define the terms:
•
Dedicated lubrication labor. Technicians working exclusively on clearly defined lubrication tasks and responsibilities and reporting to a centralized program manager.
•
Allocated lubrication labor. Technicians dedicating time to both mechanical repairs/inspection activity and machine lubrication activity and reporting to an area or department supervisor.
Department-level management prefers allocated labor. This is a tactical management level in the production facility. Decisions revolve around fulfilling operations, maintenance and reliability priorities. The job is to keep production flowing, and anything that interrupts department production must be
immediately addressed! In this environment, there is no doubt that an allocated labor person assigned to lubrication (especially a skilled mechanic) who can be drawn off of routine activities and placed on the urgent matter of machine repair is an appealing option. Appealing on a daily basis.
TYRANNY OF THE URGENT
Having this ready resource increases the likelihood that production management will grow comfortable with, perhaps even confident in, the maintenance department’s ability to address urgent matters that arise. The lube tech justifiably becomes a standard fixture in a run-to-failure maintenance plan.
As management becomes normalized to the idea that the hours dedicated to routine lubrication become hours available for urgent needs, urgent needs grow to fill the available time. If there is no strict accountability to assure the lubrication tasks are always covered, in relatively short order the lubrication tasks will not be done and machine failures will increase as will time required for urgent work. The allocated labor approach chosen with good intentions creates a self-fulfilling reality. The tyranny of the urgent supplants the value of the important.
I am not aware of any objective research that validates this position, but I consistently witness this tendency with distributed lubrication management programs. Management’s failure is in a lack of awareness of the role that sporadic lubrication care plays in component failure. This soon translates into a lack of commitment to completing all lubrication-related tasks.
There is uniform agreement that the job of machine lubrication is indeed vital. No questions asked.
www.canstockphoto.com
DEDICATED: A HARD BUT CORRECT CHOICE
Alternately, if management chooses to fulfill the net requirement for all reliability-enhancing lubrication activities and allocates this time with rigid expectation for completion, then lubricated component failures will decline (this can be proven easily enough), along with all of the direct and indirect labor burden.
Dedicated lubrication labor occurs when management decides that all lubrication program tasks will be completed, measures the size of the task and supplies labor accordingly. Task measurement occurs as follows:
1.
All production machines are cataloged.
2.
All machine components are cataloged and identified as “to be” or “not to be” lubricated.
3.
Those components requiring lubrication are assigned an interval.
4.
Each type of lubrication task is time stamped.
5.
The time per task is multiplied by the frequency for the task and then multiplied by the number of times that the task is assigned. The entire task should be incorporated into this estimate. For example, three minutes per bearing regreasing event instead of 10 seconds. Obviously it doesn’t take three minutes once the technician is at the fitting. The overage allows for time to get there, discover that the fitting is broken, replace it and then fulfill the regrease task.
6.
The total hours required for lubrication management is divided by man-hours per year.
7.
Determine how many hours per year per man are available. A senior mechanic has regular holidays (10 days +/-), plus 4-5 weeks of vacation time to subtract from availability.
8.
Apply a labor factor (fudge factor) as deemed necessary.
Once the scope of the entire job is known, management can dedicate labor accordingly with an expectation of complete/near complete weekly fulfillment of scheduled tasks. If the labor is strictly dedicated to lubrication, and from the top down there is agreement that this is the case, then instances where technicians are pulled off their routes to address other urgent matters will truly be the exception.
Again, I have no examples of studies documenting whether dedicated labor is more consistently left alone to fulfill routine tasks, but I do have firsthand experience with program managers demonstrating that their dedicated labor is able to complete assigned weekly work requirements.
www.canstockphoto.com
Figure 2. LUBE TECH GENERAL SKILLS AND APTITUDES
For the dedicated lube tech, these should include:
A.
Basic computer literacy, including the capability to operate standard e-mail, spreadsheet, word processing and moderately complex software. Also employ Web-based programs, including those used for lubrication scheduling and oil analysis functions.
B.
Good oral and written communication skills and good team-building skills.
C.
Capability to work in an unsupervised position effectively.
D.
Capability to read and interpret such technical documents as:
•
OEM maintenance plans
•
Blueprints
•
Software system instructions.
E.
Capability to perform basic mathematical functions (addition, subtraction, multiplication, division, percentages) for the purpose of interpreting alarms, calculating lubricant inventory and calculating relubrication quantity considerations.
F.
Certified to operate lifting equipment (fork truck, skip hoist, etc.)
G.
Certified to perform lockout-tag out procedures.
H.
Demonstrated initiative and strong work habits.
Lastly, as quickly as possible, the new employer should seek to transfer job-specific knowledge that cannot realistically be expected to exist, even for a journeyman mechanic. This pertains to generic lubricant weights and grades, product-specific names, weights and grades, generic terminology associated with machine-specific lubricant specifications, terminology associated with lubricant analysis and condition control, terminology associated with machine components and component operation, etc. This final level of knowledge development is depicted in Figure 3.
LUBE TECH SKILLS AND KNOWLEDGE
Assuming that a sufficient amount of labor is dedicated to the work to enable 95% first-run completion of lubrication tasks, what type of skill set and/or general knowledge level is appropriate for the lube tech sent to complete the job?
In practice, company requirements for skills/knowledge range from none to journeyman mechanic. The dominant influence seems to be whether the job classification is considered an entry-level or a seniority-based position.
Seniority-based positions are more likely to have journeymen mechanics, millwrights or other skilled tradesmen than those programs where the lube tech is an entry-level position. For either circumstance, a company would benefit from having a job description and skills requirement clearly defined in its work policy manual.
The work of the lube tech is rarely so physically intensive that it should be exclusively a male work role, but it is certainly a job that requires fitness for the sake of endurance performing hard work in harsh conditions. Accordingly, this is not a man’s or woman’s job, but one that requires strength, energy and physical fitness.
There is a set of definable skills and knowledge that should become part of the job-bid or new hire process. The job description and activities are depicted in Figure 1.
This job task covers the lubrication-specific work needed for a typical manufacturing environment. Operation-specific tasks (such as operating an idle machine before beginning lubrication practices) may be added if they are known to be required in advance. None of these job tasks require highly detailed knowledge to perform. In fact, with some classroom training/education and routine on-the-job (OTJ) training, knowledge to perform these tasks can be readily transferred.
Machine-specific knowledge and information may be transferred during OTJ tutelage if a person is in place who has the specific knowledge. Otherwise, it will have to accumulate over time with experience. This could include things such as: the XYZ conveyor drive should be checked only while idle. If checked while it’s operating, the drive oil gauge level will appear to be low. If it is then filled to the normal level while the drive is operating, it will become too full, overheat and produce significant foam.
A minimum amount of walk-around knowledge should be expected for any plant position. This includes basic computer literacy and application knowledge, reading and writing skills, shop math skills and a demonstrated ability to learn—demonstrated by completion of any kind of technical skills training, such as a two-year technical school certificate. A high school diploma may not be enough, but if that is all that exists for an otherwise qualified candidate then a judgment call needs to be made. This walking-around knowledge could be characterized as general skills and aptitudes, as noted in Figure 2. In addition, the position requires the specific set of skills, knowledge and aptitudes depicted in Figure 3.
Figure 3. LUBRICATION-SPECIFIC SKILLS, KNOWLEDGE AND APTITUDES
•
Understand fundamental lubrication concepts as defined by a recognized independent organization (STLE, ISO, API, ICML) fulfilling a recognized independent knowledge certification (CLS, 18436-4, MLT, MLA).
•
Hold or obtain a Level I certification within three months of hire.
•
Hold or obtain a Level II certification within 18 months of hire.
•
Demonstrate by hands-on review basic problem-solving skills.
•
Demonstrate by hands-on review basic understanding of the function of mechanical systems.
•
Demonstrate by hands-on review basic understanding of hydraulic and circulating systems operation.
•
Demonstrate by hands-on review basic contamination control practices.
•
Demonstrate by hands-on review basic machine inspection functions.
www.canstockphoto.com
SUMMARY
In the absence of a clearly defined job description and a matching skills and knowledge requirement set, it is difficult for management to select personnel, either new or existing employees, who represent the best fit for one of the most important but overlooked roles in the plant. Labor should be dedicated to continuous coverage of lubrication tasks. If labor is providing double-duty between mechanical repairs and lubrication tasks, then the site must work purposely to assure that all the lubrication tasks are given time to be accomplished.
The company would do well to define the job of the lube tech to the maximum extent it is willing to support and hire general knowledge and specific skills needed to achieve the intended end result. Certification through an independent industry organization adds credence to the technician’s role.
Mike Johnson, CLS, CMRP, MLT II, MLA III, is the principal consultant for Advanced Machine Reliability Resources, in Franklin, Tenn. You can reach him at mike.johnson@precisionlubrication.com.