Metalworking Fluids (MWF) are used in a wide range of different activities from simple grinding and metal removal to more extreme operations including honing and broaching. Additives are utilized in fully water soluble fluids and in water-free neat oil formulations. Over the years, many highly successful additives have been developed that offer formulators almost everything they require.
However, times are changing and the MWF industrial requirements are not immune to changes in usage or to changes in legislation. In recent years a number of additives have been eliminated from use in MWF applications, including nitrites and short chain chlorinated paraffins. Environmental pressures continue to mount and there is a growing desire to further eliminate additives that are suspected to be harmful to the operator or the environment. Additives such as medium chain chlorinated paraffins are under the spotlight from a number of legislative bodies and may indeed be banned from use, or have their use severely restricted in the near future.
Rather than wait for the legislation to happen, Afton Chemical’s Metal working Fluids group has been engaged in an extensive program to evaluate and benchmark chemistry that could be offered as working alternatives to additives under threat. The evaluation has been focused on existing additives currently available from the Polartech product line with a strong emphasis on renewable chemistry which has low environmental impact. These additives are already regulatory compliant which eliminates the need for lengthy and expensive registration processes.
Around forty additives, including leading industry benchmarks, were selected for evaluation in this study. These lubricant additives include antiwear and extreme pressure agents. They were examined in a broad range of applications, with testing conducted on the Micro Tap thread tapping machine, the Stanhope-Seta 4-Ball, the Reichert wear machine and the Hille Press which is used for forming and deep drawing laboratory evaluation. To further enhance the evaluation, three grades of aluminum, stainless steel, titanium and magnesium grade alloys were selected. The primary selection criteria for these alloys are for aerospace and automotive applications.
The evaluation included a range of additives in forming, cutting, wear and extreme pressure applications on a like-for-like basis. A significant amount of test protocol development was required to ensure representative data generation across materials as different as titanium and magnesium and across applications ranging from deep-drawing to metal removal. To date, over 10,000 individual tests have been carried out which has led to a substantial increase in the understanding of additives, materials and application testing.
With so many additives being tested in such a variety of ways, it is impossible to discuss all of them in this one article; however we have identified some significant conclusions in the Hille Press and the Micro Tap Tapping Torque Test. The Hille Press provides the most useful information as representative of real world applications. The Micro Tap Tapping Torque Test uses both forming and cutting modes.
Hille Press
The Hille Press is a laboratory scale deep drawing machine
(Figures 1 and 2). Test blanks are coated in a proscribed quantity of lubricant additive in carrier oil, clamped at a fixed pressure and extruded by means of a travelling punch. The performance is dependent on a number of variables, such as punch speed, diameter, and radius of curvature. For a given material, such as stainless steel, all the parameters are fixed leaving only the selection of the additive as being the prime determinant for variable performance. Additives are prepared at 0.5%, 2.5%, 7.5% and 20% in common base oil and applied to the stainless steel blank.
Figure 1. Hille Press
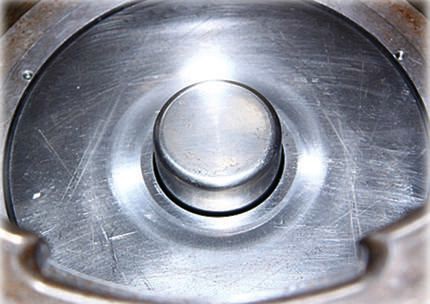
Figure 2. Hille Press Closeup
The press is instrumented and measures punch pressure or resistance to deformation verses punch displacement
(Figure 3). The punch extrudes the blank until it fails resulting in a catastrophic loss of punch pressure. Here we look for the greatest displacement for the lowest punch pressure as indicating maximum additive performance. Alternatively at a common displacement prior to failure, the average pressure can be used to rank additive performance.
Figure 3.
Our observations were quite surprising
(Figure 4). Additives 1, 2 and 3 are the industry benchmarks we selected for comparison. Additive 1 is typical medium chain chlorinated paraffin and benchmark additives 2 and 3 are leading polymeric lubricant additives known for their superior performance. The remaining additives are a selection of materials taken from a range of MWF and other lubricants. For example additive 12 is Actralube 9228, additive 14 is Actramer SYZ-3 and additive 18 is Actramer CZ6. A surprising number of additives outperformed the industry benchmarks by quite a considerable mar gin. We at tribute these results to superior boundary lubrication and interaction with the metal surfaces.
Figure 4.
Micro Tap Tapping Torque Test
The Micro Tap Tapping Torque Test
(Figure 5) is well known across the metalworking industry and has become a standard instrument for additive evaluation. Key to this program was development of test protocols appropriate to each alloy under evaluation. The requirements for magnesium, aluminum, stainless steel and titanium are each vastly different.
Under identical conditions, lower torque reflects improved lubrication and additive performance.
Figure 6 summarizes the results obtained using aluminum 7075. Here we see that additive 7, which is Actrafos SA 216, gave the best performance across the % activity range. Similarly, Polar tech® LA8005 [additive 3] gave the best performance with stainless steel 316, while for aluminum 6061 grades, MCCP and Actralube 310 [additive 17], gave the best performance for titanium grade 5.
Figure 5. Micro Tap Tapping Torque Test
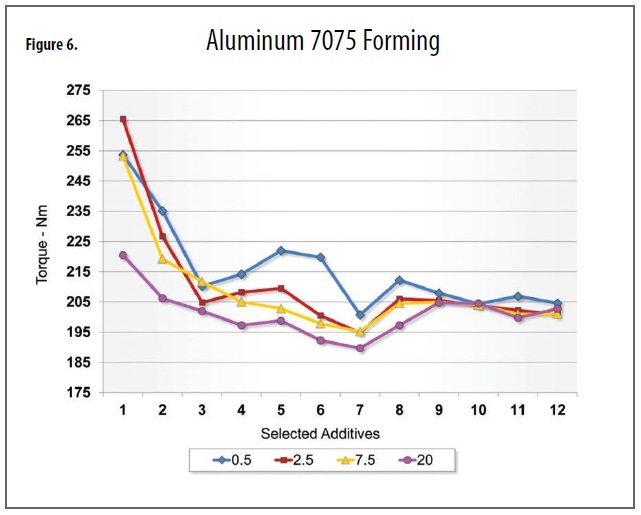
Figure 6.
The 4-Ball Weld Failure Test
(Figure 7) provided both expected and unexpected results. Additive 1 is the MCCP benchmark and gives good results, showing increasing weld load with increasing activity. As expected, additives 7, 21 and 26 (Actrafos phosphate esters) also gave very good performance. Additives 10 and 11 [TecGARD® 500 & TecGARD® 541 ZDDPs] also performed well. However, somewhat surprisingly, additive 12, Actralube 9228, gave better than expected performance, superior to the MCCP and not too dissimilar to the phosphate esters. It is interesting to note that Actralube 9228 is predominately vegetable derived.
Figure 7.
Conclusion
It is impossible in this short article to pick out examples of superior additives for each material in each application from such an extensive body of work. As expected some additives, such as the Actrafos phosphate esters work very well on stainless steel and in EP application tests. Polymeric esters such as Polartech® LA8005 and Actralube HD6000 give superior boundary lubrication in drawing and forming application tests.
The results also show that no one additive provides superior performance across all of the application areas and all the alloys tested. However, we do see additives such as Polartech® LA8005, Polartech® LA 8330 and Actrafos 216 providing superior lubrication performance across most of the tests and alloys used. A substantial number of the additives evaluated, including many of the specific additives indicated in this article are derived from renewable vegetable feedstock.
Therefore, they offer superior performance with an enhanced environmental profile over many other additives commercially available today.
We continue to make advances in understanding how additives perform and what the various application tests tell about the requirements of different materials and application regimes. Depending on the application, it is possible to recommend lubricant additives that offer both improved performance and an improved environmental profile.