Please describe an incident where used oil analysis averted a potentially serious problem.
TLT Sounding Board August 2011
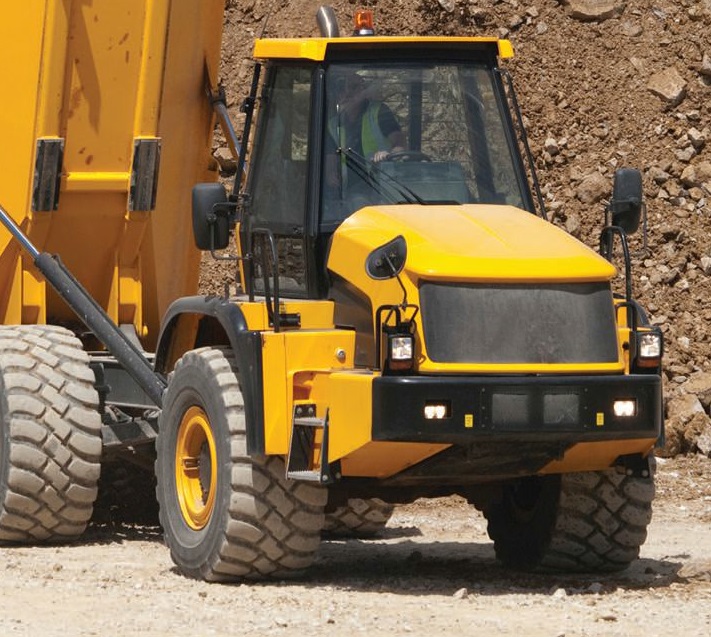
www.canstockphoto.com
Unsurprisingly, STLE members are huge fans of used oil analysis—and with good reason. This month’s questions elicited specific instances where the process prevented machine failures and complete breakdowns, saving millions of dollars. Averted downtime, lost productivity, waste and shipping costs saved millions of dollars more in additional expense. But the benefits aren’t always monetary—several members noted that potentially explosive situations were avoided through used oil analysis. The system also can assist in selecting a more appropriate lubricant for an application. As one reader said, “Oil analysis allows for trending of equipment and lubricant condition. It is an early indicator of problems before they become critical.”
Used oil analysis caught fuel in a specific make/model across our fleet at 5,000 hours. We were able to work with the OEM to fix this issue and averted more than $2 million dollars in repairs and lost production.
Many—that is why we do regularly scheduled analysis.
Numerous examples where oil analysis found a serious problem.
Finding high brass content in the sampling revealed bearing cage damage. Also found high water content.
On countless occasions detection of glycol and fuel in engine oil has averted premature engine failure.
An elevated Ferrous Index on a test slate alerted us to a thrust bearing problem. Replacing the bearing ($30,000) avoided a complete rebuild of the gearbox ($475,000).
Every day you can find examples of used oil analysis reports that give you information about potentially serious problems, including wear metals trends, viscosity increasing or decreasing, AN or BN abnormal data, abnormal cleanliness ISO code, water contamination, soot level, fuel dilution, oxidation, nitration, abnormal PQI values, wear debris particulate, etc.
High fuel dilution in a truck that previously would have gone undetected.
Found failing oil cooler in a bus application (antifreeze contamination in the oil).
This was a grease issue where the customer experienced some premature wear issues. Testing the used grease did show a great deal of contamination, and the sample of the fresh grease revealed no performance issue.
A newly overhauled, high-speed air compressor requires turbine oil lubrication with no more than trace quantities of various elements. Oil analysis revealed higher quantities than are allowed per OEM requirements. Review of analysis data showed high levels of certain elements, which happened to be additives in another lubricant used in an adjacent air compressor. Wrong lubricant added to the overhauled machine was the likely cause. System was flushed two times and follow-up sampling and analysis was conducted. Element levels were then within OEM specs.
High glycol was found in a diesel engine oil sample. The equipment was taken out of service and the leaking oil cooler replaced prior to major engine damage and failure.
Of course, many instances. Oil analysis fills an important function in modern maintenance strategy.
Do you review the used oil analysis lab report in detail only if it has flagged results?
Yes
29%
No
71%
Based on results from some 15,000 TLT readers.
A heat exchanger constantly leaked into the reservoir and caused a lower viscosity and PH of a water-based hydraulic fluid. We alerted the customer who said, no, this couldn’t be the problem. So we asked them to open the reservoir and look at the top. There was a calcium mass on the top of the reservoir confirming our results!
We detected abnormal levels of chlorine and sulfur in the oil. The customer wanted to kick us out since their machine was gumming up, but we identified that foreign and incompatible oil was added by an operator and saved the business.
Many cases where analysis detected wrong oil type with additive identification. Additives were corrosive to soft metals in the machines.
High fuel dilution on a diesel engine due to faulty injection pump. Potential for explosion due to high fuel content in engine crankcase.
A routine oil analysis showed that a unit had developed a coolant leak. The dispatcher called the unit back to the yard instead of picking up a full load. As soon as the truck pulled up to the garage, the exhaust belched a huge plume of white smoke, an indication of water vapor and probable serious leak. This averted a towing bill and serious damage to the engine.
A personal vehicle I owned showed coolant leak shortly after purchase. I got rid of it shortly after.
Water content and varnish existence in turbine oil analysis.
Contrary to manufacturers’ recommendations, we switched from an EP gear oil to a higher viscosity AW oil, which works better. This was due to results shown to us through analysis.
EGR coolers almost certain to fail over time. Catching the initial slight weep prevents corrosive wear and allows our customers to schedule OEM shop time when it is cost effective. Usually when caught early it is a warranty issue.
Ferrography results on two consecutive grease samples six weeks apart indicated particles 100 microns and larger. The bearing was replaced before shaft damage occurred. Shipping one way for this roll is $5,000.
Coolant leaks or fuel dilution in engines is the most common occurrence we see.
Do you change the oil immediately if a used oil analysis result has a flagged value?
Yes
27%
No
73%
Based on results from some 15,000 TLT readers.
Used oil analysis results have flagged many potentially serious problems such as coolant contamination and fuel dilution of engine oil, high silicon (dirt) contamination and accompanying accelerated wear metal levels in gearboxes and many other circumstances.
Mainly engine oil sample results easily determine glycol contamination.
There have been numerous instances where used oil analysis determined coolant leaks and prevented future breakdowns from a blown head gasket. I have also seen several times where we have caught engines that had mechanical problems that were indicated by used oil analysis. Result were minor repairs vs. majors.
Bearing wear in a critical gearbox—evidence of the occurrence prevented a long-term shutdown and potential damage to the gears.
We watch our oil analysis data daily and have many good saves. We typically run all mobile equipment components to max life using oil analysis to make solid decisions. We extend component life and have an estimated savings in a four-year time period of over $5 million.
High ferrous count led to retesting of pump pressure lines that found a pump in stages of failure.
Dozens of examples: A school bus fleet identified coolant dilution and head gaskets were replaced instead of the engine. Construction and trucking companies—the list goes on.
Finding high Fe content in the results raised our awareness of a serious wear and load capacity in the equipment.
Rapid evolution of water content in an oil-lubricated stone crusher subjected to versatile weather conditions in southern countries showed that it was absolutely necessary to make an intervention on the machine and control the sealing.
The most important test method for BN (Base Number) that indicates engine condition is:
ASTM D2896
35%
ASTM D4739
38%
Neither is important
31%
Based on results from some 15,000 TLT readers.
Several times gear reducer failures have been averted because of oil analysis reports.
In the infancy of our used oil analysis program, we sampled a set of motors that are crucial for production and found the results quite troubling. These motors were on an annual oil change frequency, and the sample was taken six months after the latest oil change. The RULER results showed the antioxidant package was nearly depleted and AN was well above the condemn limit. Through consultation with the lubricant supplier and the motor manufacturer, we were able to change the lubricant from a Group I to a Group IV lubricant and avoided downtime. The economic benefit was over $1 million in lost production!
In an engine oil sample, finding above-normal glycol levels helped us show a new customer the importance of sampling and help avert an engine failure.
In some industrial plain bearings that can’t be in contact with Zn additives, the early detection of common hydraulic oil contamination avoided bearing corrosion and break. The assay is so easy and the equipment and time out of work is very expensive.
Used oil analysis identified contaminant product within the existing fluid, thereby absolving the existing fluid manufacturer of product liability claims.
We find water in oil all the time. We have found a mixing of products which left the oil in service at the wrong viscosity.
Yes, absolutely. We have a 99% confidence level when we use a good laboratory and conduct a standard procedure to take the sample.
In one case we found the incorrect viscosity oil used in a gearbox requiring an AGMA 4 (ISO 150). An ISO 32 hydraulic oil had been used. Unfortunately some gear damage had been done before the testing program had been started, but I believe it did prevent a total failure.
Editor’s Note: Sounding Board is based on an e-mail survey of 15,000 TLT readers. Views expressed are those of the respondents and do not reflect the opinions of the Society of Tribologists and Lubrication Engineers. STLE does not vouch for the technical accuracy of opinions expressed in Sounding Board, nor does inclusion of a comment represent an endorsement of the technology by STLE.