Stuck in a rut
Drs. Wilfred T. Tysoe & Nicholas D. Spencer | TLT Cutting Edge August 2011
Structuring surfaces on a mesoscopic scale leads to precise friction control.
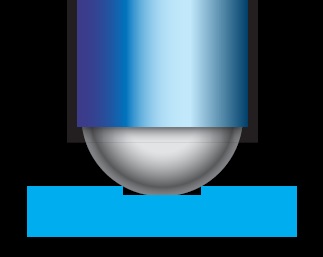
There existed a maximum friction at a groove width corresponding exactly to the width at which the sphere interlocks with the groove, simultaneously touching both walls and the base.
Over the last decade, micro- and nanoelectromechanical systems (MEMS and NEMS) have become increasingly commonplace in a wide variety of devices, with applications ranging from automobile airbag accelerometers to a host of consumer electronic products.
As we’ve previously discussed in TLT (
1), tribological problems in such devices are an issue, and controlling friction and wear remains a challenge. While our previous column on this subject dealt largely with wear, a recent paper (
2) published in
Tribology Letters deals with the control of friction on length and load scales relevant to microdevices.
At the macroscopic scale, many researchers have explored the effects of surface structure on lubrication. Structures of the appropriate dimensions have been shown to improve hydrodynamic lubrication while also serving as a sink for wear particles, thus rendering them less likely to cause wear by plowing. Structuring at the micro- and nanoscales has been explored far less, and tribological measurements involving contact sizes and loads comparable to those present in MEMS and NEMS devices (at the mesoscopic scale) have been rare. While atomic force microscopy (AFM) can achieve the loads that are relevant to MEMS, it generally involves sharp tips with contact areas on the nanometer scale.
To address the contact-area problem, Johannes Sondhauß and Harald Fuchs from the University of Münster, Germany, together with André Schirmeisen from the University of Giessen, Germany, have explored the effect of structuring on friction by using so-called “colloidal probe” AFM (
3), where the usual sharp tip is replaced by a sphere with a diameter of micrometers.
The technology that was crucial to this study was the focused-ion beam (FIB) technique, which allows the precise milling of materials with a resolution of nanometers. The authors used FIB to prepare a library of flat-bottomed groove arrays on a single silicon wafer. The groove took exactly half of the wavelength of a square-wave-like cross section, and the groove width was varied from 530 nm to 4,350 nm in 23 steps. The depth of the groove in all cases was 26 nm. The tip consisted of a titanium sphere (either 4.6 or 15.8 µm in diameter) that was glued into a hollowed-out AFM tip (FIB again!). Friction measurements were carried out in air, with the sliding direction perpendicular to the groove axis. The effective friction coefficient (calculated as the slope of the linear friction force-applied load curve) was averaged over an area of hundreds of square microns (i.e., across several grooves at many positions).
The results showed that for both sizes of tips tested against the whole range of groove spacings, there existed a maximum friction at a groove width corresponding exactly to the width at which the sphere interlocks with the groove, simultaneously touching both walls and the base. This can be calculated by simple geometry. Focusing in on the friction as the sphere traverses a particular groove, it was observed that for a groove width where interlocking occurred, a higher friction coefficient was instantaneously observed than on the neighboring terrace.
FIB is a valuable addition to our arsenal of techniques for tribological experimentation. It allows the precise sculpting of structures on the nanometer scale, and, therefore, enables us to not only mimic the roughness of engineering surfaces but also to craft new tools for the investigation of contact in a new generation of mechanical devices.
FOR FURTHER READING:
1.
Tysoe, W.T. and Spencer, N.D. (2008), “Alcohol Gets You No Wear,” TLT,
64(4), p. 64.
2.
Sondhauß, J. Fuchs, H. and Schirmeisen, A. (2011), “Frictional Properties of a Mesoscopic Contact with Engineered Surface Roughness,”
Tribology Letters,
42(3), pp. 319-324.
3.
Ducker, W.A., Senden, T.J. and Pashley, R.M. (1999), “Direct Measurement of Colloidal Forces Using An Atomic Force Microscope,”
Nature,
353, pp. 239-241.
Eddy Tysoe is a Distinguished Professor of Physical Chemistry at the University of Wisconsin-Milwaukee. You can reach him at wtt@uwm.edu.
Nic Spencer is professor of surface science and technology at the ETH Zurich, Switzerland. Both serve as editors-in-chief of STLE-affiliated Tribology Letters journal. You can reach him at nspencer@ethz.ch.