Oil analysis in the real world: Part IX
Jack Poley | TLT On Condition Monitoring July 2011
Use all three oil analysis tiers for best effectiveness with marine applications.
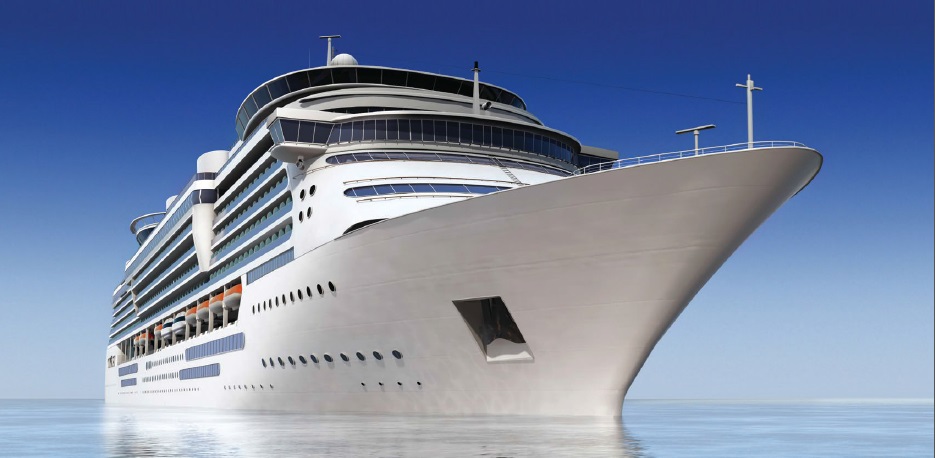
www.canstockphoto.com
Last column I discussed the three-tiered oil analysis strategy for mobile equipment (trucking and off-highway). This issue I’ll talk about using the three oil analysis tiers for marine applications (offshore drilling platforms and vessels).
Oil analysis for marine activity exhibits special needs, just like off-highway. Unlike off-highway, however, abrasives contamination is usually not near the top of the list of concerns. Of special concern in the marine environment is:
•
Water contamination. Water is a common contaminant in the marine environment, however, it must be differentiated when detected as to whether it’s fresh or salt. Sodium (Na) is the primary key for such differentiation, with possible support in the form of lower levels of magnesium (Mg) or calcium Ca). Accordingly routine spectrometric metals will include these elements. There are two basic premises:
1.
If water and Na (via significant increase) exist, it is saltwater.
2.
If water exists but Na doesn’t move, the water is fresh. The maintenance team should know what to do thereafter.
•
Lube mixing. Viscosity (VIS) is a critical consideration with respect to lube mixing, as there are numerous sumps scattered throughout the vessel or platform and it is not uncommon to have sumps with mixtures of similar or like fluids with respect to purpose and additives but of the wrong viscosity, owing to carelessness in topping off or refilling sumps. VIS testing is thus especially critical and needs to be observed for consistency with respect to the required grade. When VIS changes significantly but there are no other indications in the test results such as oxidation, acid number (AN) or fuel dilution (for diesel engines), lube mixing should be considered as a potential problem.
When lube mixing is suspected, based on exceptional VIS readings without the suggestion of known causes via supporting test results, there are some rules of thumb:
A.
VIS reading is within, say, -12%+16% of the grade required:
•
If the metallic additive package (Mg, Ca, P, Zn)* shows little deviation and no significant wear metal accumulation is noted, the situation is acceptable. One would surmise that similar fluid with a different VIS was added but not in sufficient quantity to create issues with the lubricating function.
•
If the additive metals have changed significantly (any of them more than, say, 50%), there is a possibility that incompatible fluid was added, which is unacceptable risk-taking. Drain the lube.
B.
VIS reading is more than 20% off: Drain the lube. There is too much deviation in such a case. Performing a partial drain (sweetening) with replacement of a proper grade should be discounted unless the sump is very large (possible economic issue), additive metals are showing virtually the same pattern as previous samples and wear metals are completely stable.
SUMMARY
Tier 3 primarily provides full emission spectroscopy metals analysis to monitor other than iron (Fe). As well, best instrumentation is usually available where precision is deemed critical.
Minimum Tier 3 (offsite) testing for OTR:
•
Spectrometric metals analysis (all compartments), minimum Na and the Big 4 wear metals (Fe, Al, Cu, Pb) and the primary additives found in the preponderance of lubes (P, Zn, Mg, Ca). Additional metals such as Si, Sn, Ni, Ba, etc., are usually also available to help shape the advisory commentary.
•
Viscosity (all compartments).
•
Infrared Spectroscopy (FTIR).
1.
Fuel Soot (four-cycle diesel)
2.
Oxidation (all compartments)
3.
Glycol (diesel)
4.
Water (if not employing a crackle test; all compartments).
•
Fuel Dilution (diesel)—FTIR is not recommended unless you have very good control over the fuel source and valid reference samples. A direct test such as gas chromatography is the preferred approach, correlated with viscosity.
•
Particle Count (hydraulic circuits, top drives, thrusters, certain precision gearsets, seal compartments).
Tier 2 (onsite) testing, perhaps optional basic testing:
•
Kits are available with smart testing vessel simplicity of use:
1.
Fe—ppm to vet anomalies detected via sensor or other onsite tests or Tier 1 (sensors). Portable instrumentation is available for this task.
2.
Infrared Analysis, including FTIR (Fourier Transforms IR)
a.
Water
b.
Fuel Soot (diesels)
c.
Oxidation
d.
Nitration
e.
Glycol (diesels)
f.
Possible lube mixing (if referencing is employed)
g.
Other, dependent on instrument and onsite needs.
3.
Viscosity (ambient or heated, the latter more accurate)
4.
Acid Number
5.
Base Number
6.
Insolubles (if infrared analysis is not available)
7.
Particle Count (portable kits are available)
8.
Patch Testing to vet composite findings or increased Fe levels
9.
Other, as deemed appropriate for the component.
Tier 2 (onsite) Test: Water-in-Oil Test Kit. (Courtesy of Kittiwake Developments Ltd.)
Tier 2 (onsite) Test: Electronic Viscosity test. (Courtesy of Kittiwake Developments Ltd.)
Tier 1 (online) testing (optional):
•
Oil condition sensors are very useful for monitoring relatively large sumps (100 gallons upward) in an effort to extract maximum drain intervals in a safe manner.
•
VIS is still the most fundamental property of a lube and should be routinely monitored. As the asset value increases, the test needs to be closer to the machine in remote situations such as marine implies.
•
High value assets can be protected with ferrous particle monitoring. Diesels, hydraulics, top drives/ other critical gearsets and thrusters have applicability for ferrous particle monitoring. The advantage of online testing is to spot wear development at the outset, as well as bridge the time gap between samples taken just prior to the onset of such trauma. If that time gap is more than two months, a ferrous particle sensor may have particularly strong merit.
While the above notes are entirely appropriate for marine activity, other remote, unattended installations such as wind turbines or pipeline stations can benefit from roughly the same testing and monitoring strategy. Sodium, perhaps, would not figure as prominently, nor would water, generally, but the approach is nonetheless similar.
It is the advent of Tier 1 testing that has shined a light on the remote component with respect to condition monitoring strategies, and any operation of that ilk is a highly likely candidate for Tier 1 testing, with Tier 2 and Tier 3 as supporting and vetting activities.
Tier 1 (online): Ferrous Particle Counter – sensitivity to 40 μ diameter. (Courtesy of Kittiwake Developments Ltd.)
Tier 1 (online): fdMplus instrument for determination of Fe ppm in Tier 3 laboratories or Tier 2 onsite installations. (Courtesy of Kittiwake Developments Ltd.)
*Recall that additive metals detected and quantified via UV emission spectroscopy (the predominant metals analysis used) yield no indication of the form in which the element exists. Measuring zinc (Zn), e.g., provides a value but does not reveal anything regarding that element’s efficacy as an additive, except when new and a reasonable assumption can be made that all Zn detected is active.
Jack Poley is managing partner of Condition Monitoring International (CMI), Miami, consultants in fluid analysis. You can reach him at jpoley@conditionmonitoringintl.com.
For more information about CMI, visit www.conditionmonitoringintl.com.