What direction do you see condition monitoring/oil analysis heading in the next 10-20 years?
TLT Sounding Board June 2011
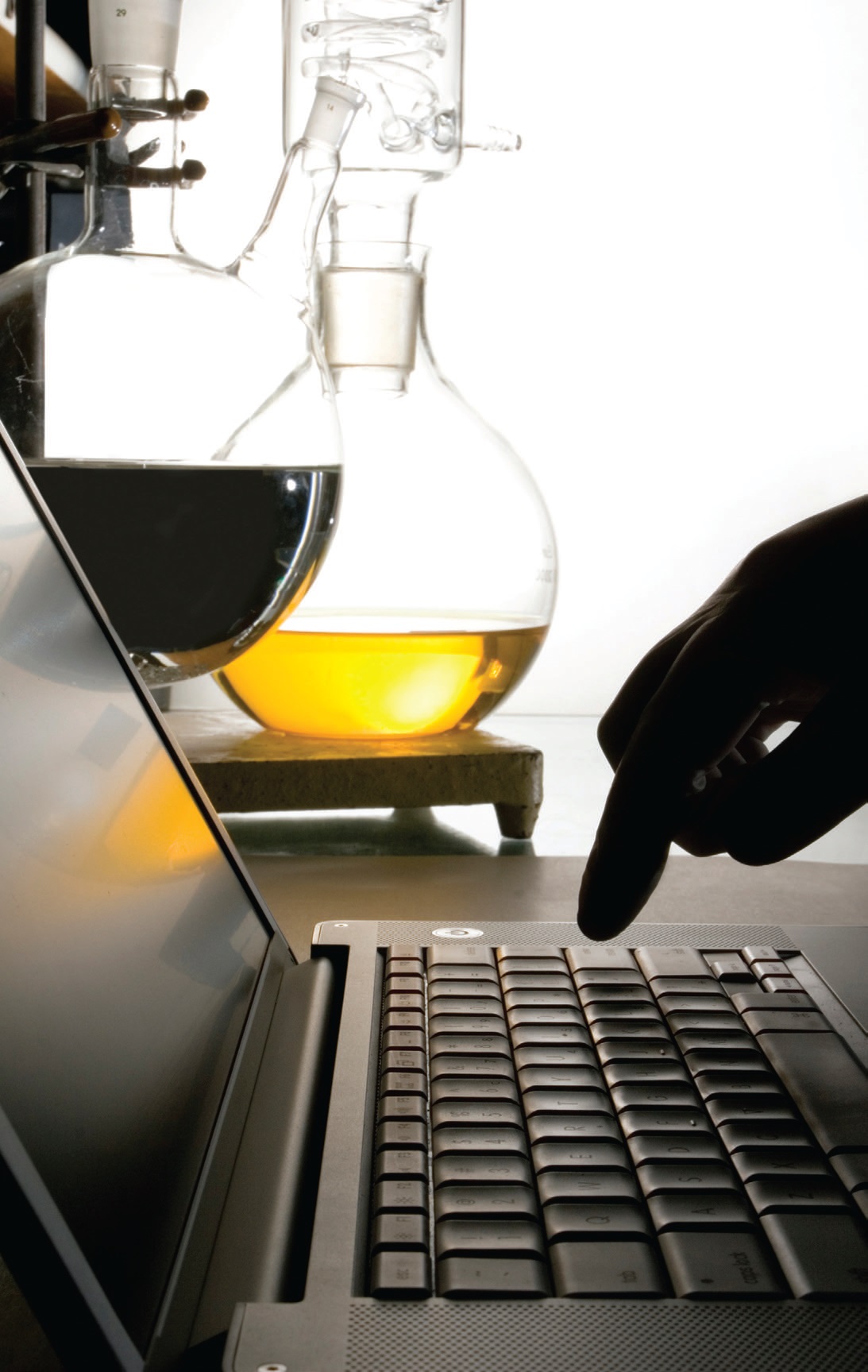
www.canstockphoto.com
TLT readers produced a long list of reasons why they believe the use of condition monitoring and oil analysis will expand in the future. The cost of oil and lubricants is increasing, machines are undergoing more demanding applications, and plants need to reduce costs across the board. But for TLT readers, that last point is a sticky one. Educating senior management that investing in higher quality lubricants and condition monitoring actually reduces costs long-term continues to be a daunting task. Similarly, readers believe more training on proper lubricant practices for floor personnel and machine operators is essential. Many readers believe the use of sensors and online data monitoring will grow. One respondent stated it simply: “The longer the fluid stays in the tank, the less it costs!”
I see the need for it increasing as well as the understanding of why it is important.
Increased monitoring and analysis due to increased cost of lubricants to reach maximum use. New technologies in lubricants to extend usage.
Online analysis with real-time updates.
With the continued push toward lean management, I see a push for preventive maintenance routines that are driven from equipment condition monitoring.
You will see more and more in-line field analysis tools become available. Not that the analysis lab will go away, but the concept of immediate data in this instant-gratitude society seems very likely, and new technologies are becoming available that make it very practical and accurate.
I see more emphasis placed on condition monitoring primarily as a cost-reduction practice. Lubricant suppliers will have to cover the cost of oil analysis, and results will be used more efficiently to help reduce cost in terms of failures and maintenance. I also see a lot of the bigger industries switching from oil-lubricated equipment to newer oil mist technology, which will have a major impact on lubricant suppliers worldwide. Presently, newer technology is very expensive, but we all know that as time passes the cost goes down and companies will jump on board.
End-users are becoming more aware that clean oil is critical.
Real-time feedback control of lubrication and MWF systems is the future.
More intelligent and embedded systems in expensive equipment. Possibly nice opportunities for experts/consultancies.
In the future on-board sensors that use algorithms to account for changes in operating conditions will migrate from engines to other applications.
Oil condition monitoring needs to be focused on developing sensors that provide indicators of oil quality and particle size distribution with a higher degree of accuracy.
It will be even more important in the future to have 100% equipment availability. Lube oil analysis will be required to assure us that equipment condition is good and that scheduled maintenance is done only when needed.
We’ll need to be more sensitive to varnish formation detection.
It will become more important to insure that lubricants and parts are doing their job under tougher conditions.
In-line and online sensors will play a major role in routine condition monitoring. Laboratories will play a more conditional role, performing advanced analysis.
Funding will be a key issue, as well as the moving of production overseas.
I see oil analysis monitoring being more an integral part of an overall plant maintenance strategy and also an effective tool to limit and reduce overall machinery breakdown/downtime. However, customers and plant maintenance managers need further education on the benefits of oil analysis. Lack of oil analysis understanding seems to be the major problem that faces oil analysis technology to advance and be widely implemented.
Condition monitoring will be a
must. Prices of lubricants and the use of synthetic lubes will dictate the use of oil monitoring.
Predictive analysis is the direction for all to go.
In the next 10-20 years, condition monitoring should be the baseline for all maintenance. More work is needed to assess the best practices involving this type of monitoring. Laboratory methods must readily match online condition monitoring methods in order to confirm the best maintenance decision. This will in the end allow predictive maintenance, reducing the possibility of unexpected failures.
Longer-term use of oils, pushing their useful life to the limit. This requires lubrication formulations that extend the life of oils.
Real-time monitoring of oil is the key to the future.
Oil analysis is still not used to its capacity. I would like to think that this will change, but I do not see it progressing much beyond where it is now.
With the cost of online sensor technology reducing, I see a move to more online monitoring systems for more equipment, even some equipment deemed less critical and which used to have offline monitoring carried out.
Competition will drive industries to increase uptime production. This will lead industries to utilize oil analysis to minimize downtime for maintenance.
Utilizing less manpower with the impetus to achieve desired results will mean that we must use new or used proven technologies to monitor our machinery.
The real issues are price/cost and accuracy.
I see more condition monitoring on equipment that historically has not had it. The cost to add is significantly reduced and, compared to unexpected machine downtime, worth it.
Condition-based maintenance (only replace lubricant when needed), identification of issues early, predictive estimates on amount of safe operation until service is needed to allow scheduling of service when it is most convenient.
Demands for manufacturers to become or remain lean and mean will be the greatest in industrially developed regions with higher labor costs than developing industrial regions. Survival will favor those who fully embrace, adopt and continually advance long-term proactive maintenance practices. These include total lifecycle analyses of new and upgraded equipment and processes, effective, proactive condition monitoring and best practices for lubricants and lubrication. Some maintenance, manufacturing and marketing niche-related publications increasingly indicate that ongoing global economic conditions has taken its toll on long-term initiatives, including implementing or strengthening proactive maintenance practices in favor of focusing on short-term profitability. The outlook for condition monitoring/lubricant analysis will probably remain flat and quite possibly decline modestly as long as the global economic environment remains depressed. The long-term benefits achieved through sound proactive maintenance practices may extend this timeline before new and advanced growth occurs in these areas, possibly by 3-5 years. Past and existing indicators suggest that significant expansion of proactive maintenance practices, including condition monitoring/lubricant analysis, will again occur but only after the global economy revives and stabilizes in a controlled inflationary growth mode.
Improved lubricant formulations and advances in sensor technology are key issues.
Filter improvements and offline filtration has provided the biggest bang for the buck.
New methods of analysis might need to be developed to enable users to detect the earliest signs of equipment fatigue.
Primary issue is providing a quick turnaround!
More focus on conservation and synthetics.
Increased use by industry with growing expertise at the industrial user level.
Condition monitoring and oil analysis will be a top priority in the near future. But it may be a hard thing to convince managers of that because of the cost and their lack of knowledge about lubrication.
I think it will gain wider acceptance as a necessary tool for proper operation of any critical, lubricated asset.
Data analysis will utilize more electronics and computer technology. Used oil sampling may be completely automated.
It will most definitely have a direct correlation between the availability of crude oil supplies and the conservation of lubricants in use. It will therefore be a necessity rather than a “nice thing to have.”
As equipment continues to get smaller and easier to use, I see condition monitoring in the field being used more and more with accuracy improving. This will increase its use, making it more reliable.
If end-users aren’t using this technology, they will be. Why? To save money. If they’re already using this technology, they will become more proficient. Why? To save even more money.
All oil analysis labs should be ISO 17025 accredited to assure high quality service.
What will have the biggest impact on oil analysis in the next 10 years?
Sensor technology
47%
Computer Data Analysis/Automated Analysis and Data Reporting
49%
On-site laboratories
26%
Other
12%
Based on results from some 15,000 TLT readers. Total exceeds 100% because some respondents voted for more than one category.
What are the biggest challenges in the next 10 years for end-users looking to maintain strong lubrication practices?
The biggest challenge will be to continue minimizing equipment downtime without excessive lubrication system cleanouts and flushes. Condition monitoring helps by detecting harmful build-up of foreign substances and degradation byproducts. If a company has a control plan which specifies actions in response to certain troublesome data being obtained, including changing filters so that lubricant can flow unimpeded through the machinery, this will help maintain machine uptime.
Everyone wants to save money. Some people might think that new technology and constant monitoring is too expensive and may even go back to primitive thinking and preventive or even run-to-failure maintenance.
It will be a must to have best practice procedures in place, and oil monitoring is again critical.
The challenge will be running under more demanding conditions with less environmental impact. Monitoring actual lubricant conditions requires increased sensitivity to permit accurate life assessment.
Difficulty hiring and retaining competent staff.
Highly efficient filtration technologies will reduce the diagnostic power of oil analysis.
90% of oil rigs have no baseline to compare, no historic data.
Although it seems obvious, the best way of saving cost is having reliable indicators of what happens within machine components. Therefore, I consider sensor technology must be improved to indicate earlier fault detection. We need better data. If the data is noise, does it matter how much intelligence you put in the next stage?
Knowing the condition of the lubricants in the equipment is paramount. Timeliness will be critical. There is some need to have on-site capability, but the costs remain relatively high and capital expenditures may be limited in this area. Having local qualified laboratories with good data reports will help.
Pursuing extended service intervals while extending equipment life as quality and performance of lubricants continue to improve.
Internal champions within companies. Fostering the mentality that condition monitoring can actually help.
The issue will be making maintenance a priority. Coolants/fluids are often “out of sight, out of mind,” and as long as production is running/meeting specifications it is not looked at.
Education of true equipment condition monitoring techniques and not just standard oil sampling. Most professionals don’t understand the difference between monitoring the condition of the oil and the condition of the equipment.
I would say educating the end-user about lubricants. The lack thereof will be the stumbling block. Educating the end-user about lubricants together with condition monitoring is the way to go.
I have seen the routine shutdown periods for machine maintenance be removed from production schedules—this means that condition monitoring of all machinery must be incorporated for critical machine lubrication and monitored much more closely. Failure to do so can (and will) result in more machine maintenance issues if problems are not identified and rectified in a timely manner.
Lack of technical expertise.
Obtaining the budget to conduct condition monitoring. It is very difficult to convince management to fix something that is not broken.
Constant education and understanding on how mechanical systems/components are affected by various lubrication conditions/situations. An educated end-user will make better use of condition monitoring technology.
Good and reliable maintenance managers who know how to maintain a lubrication program and who do not give in to an analyst trying to lower cost in the short-term.
Penny-pinching led by the bean counters will be the biggest challenge. Condition monitoring can be used in ROI calculations to convince bean counters otherwise.
Loss of skill and knowledge as experienced lubricant professionals exit the work force.
I feel that there is a lack of lubrication knowledge from the ground up. Condition monitoring can allow end-users to show maintainers what a specific piece of machinery is doing and how it is performing. This will allow the maintainer to have a better understanding as to why they must have strong lubrication practices.
The biggest challenge is making a right decision without stopping the machine. Condition monitoring can provide online results.
To what extent do you think changes in lubricant formulation will have an impact on condition monitoring/oil analysis?
A major impact
40%
Some impact
53%
No impact
7%
Based on results from some 15,000 TLT readers.
Editor’s Note: Sounding Board is based on an e-mail survey of 13,000 TLT readers. Views expressed are those of the respondents and do not reflect the opinions of the Society of Tribologists and Lubrication Engineers. STLE does not vouch for the technical accuracy of opinions expressed in Sounding Board, nor does inclusion of a comment represent an endorsement of the technology by STLE.