Oil analysis in the real world: Part VIII
Jack Poley | TLT On Condition Monitoring May 2011
Use all three oil analysis tiers for best effectiveness with off-highway machinery.
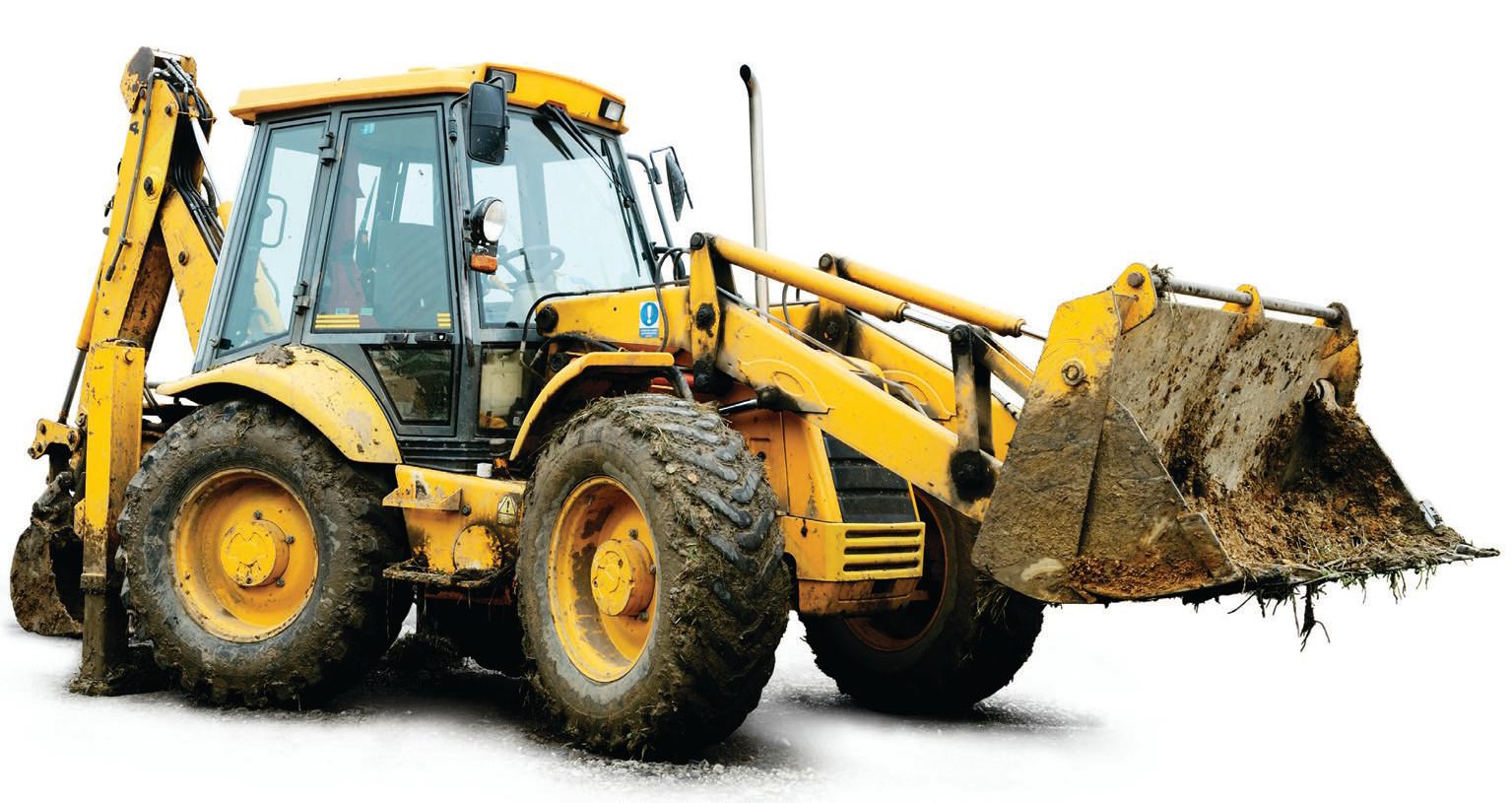
www.canstockphoto.com
Last column I discussed the three-tiered oil analysis strategy for over-the-road (OTR) truck applications. This issue I’ll talk about OTR’s more difficult mobile cousin, off-highway (OH).
It is likely that OH oil analysis is practiced on a greater percentage of equipment than any other application. The reason is obvious: abrasives or “dirt,” a commonly used term, is ever-present given the types of environments OH equipment finds itself. The need to identify and deal with abrasive contamination is the reason that oil analysis usage is so dominant in OH applications.
Breaking it down to tests, here’s what you will want to see with every sample to monitor abrasives:
•
Iron (Fe) ppm–the most common wear element
•
Silicon (Si) ppm–the most common dirt or abrasive component element.
Of course, routine spectrometric analysis (SP) covers these two elements and numbers more, but Fe and Si are the absolutely essential elements. Again, dirt is the primary enemy in OH venues. Because Si has a number of possible sources, e.g. seal material, some of which are not abrasive, additional elements from SP analysis are needed in order to clarify the situation.
Special monitoring for hydraulics and power-shift transmissions include particle count (PC).
Why aren’t Fe & Si enough protection? Because hydraulics and powershift transmissions (the latter a hydraulic with gears and wet clutches, essentially) have very tight clearances in their oil circuits, including spool valves and pistons. Further, while Si is the dominant component in most abrasives, almost any reasonably hard particle can raise havoc with tightly fit parts. In a contaminant-laden operating area, PC is the one test you want over all others in these types of systems. Yes, water is worth an inspection, too, but oftentimes it’s readily visible in the sample. PC discloses potential abrasives in oils that look clean to the eye, thereby providing a worthy insurance policy for the compartment.
Why not perform PC on engines and other compartments, too? In fact some equipment maintainers do request PC values on final drives with good effect, though not all such components are amenable for PC testing. However, reciprocating engines, particularly diesel engines, are not conducive to PC owing to interference from combustion byproducts and the fact that they do not require oils with the same oil cleanliness in order to be effectively lubricated. Here the measurement for Si is sufficient and can be correlated with Fe (or Cu or Al or Pb, etc.) to assess abrasives exposure.
Here are some useful points to consider in selecting tests:
•
Operating conditions are always under abrasives pressure. Si levels are particularly critical to monitor with Fe the key as a potential wear indicator.
•
Extended drains are usually not a practical consideration in OH venues, primarily due to Si and more frequent instances of water contamination from operating conditions.
•
All compartments must be monitored (engines, transmissions, final drives, hydraulics). Abrasives or water can strike anywhere. A crippled piece of machinery isn’t going to produce any revenue.
•
There are three primary contaminants from issues in the (engine):
1.
Fuel from a leak: pump, injector, jumper line
2.
Fuel soot (
see below)
3.
Coolant leakage into the crankcase: oil cooler pinhole, injector seal, gasket.
•
Fuel soot and oxidation are indicators that, when limits are reached, suggest an oil drain. If the limits are reached too fast, there may be operating issues.
A.
Fuel Soot (diesels only)
1.
Fuel mixture too rich
2.
Worn rings
3.
Excessive engine idling or lugging
4.
Dribbling injectors, internal jumper lines or seal leaks (injector or pump).
B.
Oxidation (all compartments)
1.
Oil has reached drain limit in normal fashion
2.
Oil has reached drain limit too rapidly, suggesting problems from higher-than-normal temperatures
a.
Clogged breather (final drive, transmission)
b.
Engine overload (excessive payload)
c.
Wrong viscosity oil added
d.
Wrong oil for the application.
•
Water: of concern when present.
Water-in-oil Test Kit for Tier 2 (onsite). (Courtesy of Kittiwake Developments LTD.)
Electronic Viscosity test for Tier 2 (onsite) Test. (Courtesy of Kittiwake Developments LTD.)
Ferrous particle counter for Tier 1 (online) test. counter sensitivity to 40μ diameter. (Courtesy of Kittiwake Developments LTD.)
SUMMARY
Tier 3 is virtually mandatory, unless a UV metals spectrometer is situated on-site, because there currently is no simple, single test for Si. Other testing tiers are optional, depending on the particular component and its operating venue.
Minimum Tier 3 (off-site) testing for OTR:
•
Spectrometric metals analysis (all compartments), with emphasis on Si detection for abrasives monitoring, along with Fe to help vet the Si value.
•
Viscosity (all compartments).
•
Infrared Spectroscopy (FTIR).
1.
Fuel Soot (diesel)
2.
Oxidation (all compartments)
3.
Glycol (diesel, powershift transmission)
4.
Water (if not employing a crackle test; all compartments).
•
Fuel dilution (diesel)–FTIR is not recommended unless you have very good control over the fuel source and valid reference samples. A direct test such as gas chromatography is the preferred approach, correlated with viscosity.
•
Particle Count (hydraulic circuit, auto-power-shift transmission).
Tier 2 (on-site) testing, perhaps optional basic testing:
•
Kits are available with smart testing vessel simplicity of use
1.
Water
2.
Viscosity (ambient or heated, the latter more accurate).
Tier 1 (online) testing (optional):
•
Because oil drain extension is not often achievable (or advised due to Si prevalence), oil condition sensors are not likely to be practical for OH use.
•
High value assets such as large horsepower engines, hydraulics and power-shift transmissions may have applicability for ferrous particle monitoring. The advantage of online testing is to spot wear development at the outset, as well as bridge the time gap between samples taken just prior to the onset of such trauma. If that time gap is more than two months, a ferrous particle sensor may have strong merit.
Jack Poley is managing partner of Condition Monitoring International (CMI), Miami, consultants in fluid analysis. You can reach him at jpoley@conditionmonitoringintl.com.
For more information about CMI, visit www.conditionmonitoringintl.com.