Oil Misting: A solid choice for lubrication
Dr. Betty Rostro-Kohanloo | TLT Feature Article April 2011
State-of-the-art technologies have made these systems a viable option for industries beyond petrochemical.
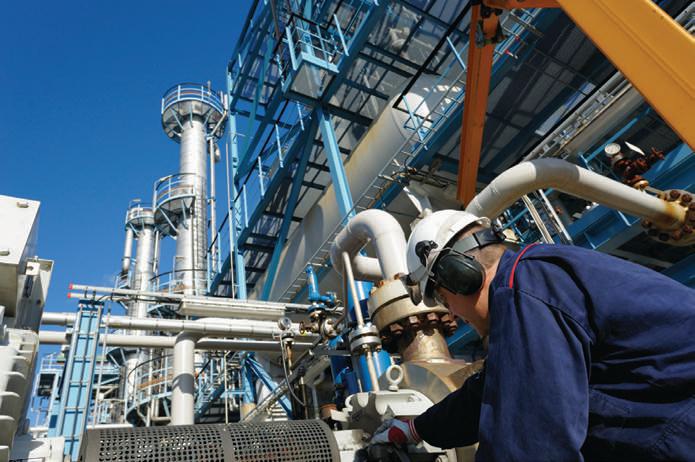
www.canstockphoto.com
KEY CONCEPTS
•
Oil misting is becoming more popular for companies looking to reduce power consumption and lubrication costs.
•
Oil mist systems use a pressurized oil-air feed system that is introduced into vortex-like orifices, yielding 1-3-micron-sized droplets.
•
Emerging technologies mean oil misting systems might soon be a viable choice for consumers.
At the same time that companies are demanding a serious reduction of power consumption, they also are looking to cut their lubricant costs. Most are requiring more high-speed bearing, gear and engine performance with high- to low-speed functioning.
In seeking alternatives to grease and circulating-oil lubrication, a system that can reduce costs, fire, health and environmental liabilities would be a good solution. Oil mist lubrication is perfectly suited to match the job, as it supplies a limited oil feed to ensure adequate cooling, while avoiding lubricant starvation in high-speed, high-temperature equipments.
Oil mist lubrication systems use a centrally located pressurized oil-air feed system that is introduced into vortex-like orifices, yielding 1-3-micron-sized droplets. By being freely suspended in air and filtered away from wear and debris particulates, the micron-sized oil mist is endowed with a natural filtration property. This filtered mist, in turn, provides machinery with cleaner and lower temperature functioning due to reduced friction. Industrial equipment, high-speed machine spindles and some aerospace applications already are using oil-mist lubrication systems.
Typical older-generation misting equipment employ compressed air, oil mist generators and a centralized pump system to provide an atomized, microscopic oil feed (1-3 microns in size). In these centralized setups, a low-velocity (<7 feet per second) and low-pressure (<1 psi) distribution system allows passage through reclassifier nozzles. The nozzles then atomize the oil into a rectifier area, which delivers a mist, spray or condensate to the lubrication point. The working motion of the multiple machine elements to be lubricated then further circulates the misted oil. A schematic of a typical petrochemical oil misting system is shown in Figures 1 and 2.
Figure 1. Basic Oil Misting System
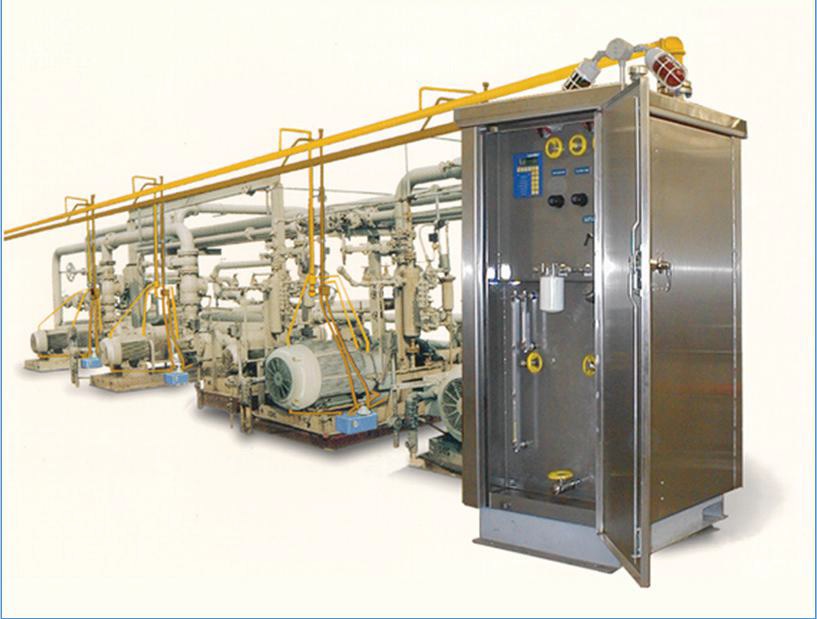
Figure 2. Typical Enclosed Misting System (Courtesy of Colfax Corp.)
In the petrochemical industry alone, closed-loop misting systems are desirable due to their negligible emission behavior. Oil misting systems have been more readily introduced into equipment whose speed has matched the oil misting velocity.
According to Heinz P. Bloch, P.E., from Process Machinery Consulting in West Des Moines, Iowa, “For the over 60,000 equipment items on plant-wide oil mist systems in the U.S., annual volume is estimated in the vicinity of 300,000 gallons. Electric motors also can be easily converted to dry sump oil-mist lubrication, as it is able to extend the functioning of internal motor bearings. The annual usage would decline if plants would convert to closed oil mist systems.” Careful control of equipment pressure also can decrease the introduction of oil contaminants allowing for decreased friction and cooler machinery operation.
Oil misting systems are already quite common to industrial applications such as refineries, where they are used in conjunction with sump lubrication. Most are familiar with the dry sump lubrication methods that are used in large engines and utilize a reservoir and external oil supply. Wet oil sump techniques, which are common to smaller equipment, use an internal oil pool system and splash-spray methods. Combined dry sump-oil misting systems typically spray a directed oil mist into the bearing housing, which then drains the liquid oil. Wet sump-oil misting or purge lubrication, in turn, transfers the oil mist above the oil level of a bearing housing in order to lubricate and replenish the oil in the sump.
Companies often fear implementing such combined sump-mist techniques since they think of complicated machinery design and costly upgrades. Yet combined sump-oil mist lubrication systems can be easily implemented into existing industrial machinery through the use of piped oil-mist inlet, vent and overflow drain valves. The combined sump-oil mist methods provide machinery with lower operating temperatures and use much less lubricant stock.
More companies are now looking into whether implementing industrial oil misting systems into their existing or newer machinery can further reduce maintenance and lubricant costs. “Oil mist reduces lubrication-related bearing failures by up to 90% by providing a cool, continuous stream of fresh oil to the bearing,” says Chris Berthiaume, products and marketing manager at Colfax Corp. in Houston. “The low positive pressure generated by oil mist keeps moisture and contaminants from entering the bearing frame.”
Industrial type misting systems are known to reduce 90% of bearing, 75% of gearbox and 35% of seal failures and allow for a 15 C-20 C reduction in temperature, thereby reducing manpower (maintenance) by 47%. Furthermore, avoidance of lubricant starvation and variable speed functioning is now possible using newer coatings, sealants and improved oil-additive formulation.
However, newer oil-air misting systems in emerging compact equipment differ than the older generation systems with the main difference stemming from decreased size. The reduced dimensions of these compact internalized misting systems use compressed air, nozzles, oil scoops and spacers in an inclined geometry. This allows equipment to better exploit the centrifugal force, causing the oil mist to flow into the bearings at much greater velocity and speed. The use of spacers also allow for a steady supply of lubricant and sufficient cooling, which can greatly increase the speed of the bearing or equipment. These more compact oil misting systems differ vastly from the established industrial oil mist lubrication systems that have been commonly used in petrochemical plants.
While technology demands are changing industrial perceptions of oil misting, discrimination against its implementation in indoor equipment still remains. This is understandable, as high-speed functioning of turbomachinery often led to stray mist streams. Human exposure of this stray mist often presented complications, due to the irritating nature of the oil additives.
According to Bloch, “When plant-wide oil mist systems were first installed in the early 1960s, they were open systems. In an open system, the oil mist is introduced into a bearing housing (
see Figure 3) and allowed to envelop the bearings. Much of the mist then escapes along the equipment shaft into the atmosphere.”
Figure 3. Open System Pump Cooling Tower (Courtesy of Heinz P. Bloch, P.E. — Process Machinery Consulting)
“In modern systems, the mist is applied (
see Figure 4), between a modern bearing protector seal and the adjacent bearing,” Bloch continues. “The mist then migrates to the bottom- center of the bearing housing where it is ‘pulled off’ into a return header that operates at a very slight vacuum.”
Figure 4. Pure Mist pump (Courtesy of Heinz P. Bloch, P.E. — Process Machinery Consulting)
Berthiaume adds, “Stray mist is often mentioned on open loop systems with regard to permissible limits. On these open systems, stray mist in workplace areas is much below the permissible level of 5 mg/cm
3. on closed-loop systems, 95% of the oil used can be reclaimed.”
Oil separator or electrostatic precipitator and/or lube-oil reservoirs that can recirculate stray mists in closed systems can be applied if human exposure is problematic. Newer compact oil misting systems can, in fact, totally avoid these issues. More modern mist systems, such as that housed in the Honda GX25 and GX35 4-stroke engines, are enclosed to avoid leakage of the mist into the environment and/or can burn any stray mist with fuel in the engine.
At this juncture the end-user might wonder whether they will rely on mineral-based stock, polyalphaolefins or high-end synthetic esters. According to STLE-member Ray Thibault, an industry consultant in Cypress, Texas, “The lubricant used must be very low in wax content to prevent plugging of the reclassifier, especially at cold temperatures. Previously naphthenic oils were used because of low wax content. They have been replaced by low wax ISO 100 paraffinic mineral oils. Many people have switched to synthetics, especially in cold-temperature environments. The most common synthetics used are ISO 68 PAOs and ISO 68 or 100 diesters.”
Basic mineral oils can, however, be implemented for equipment that needs minimal maintenance, i.e., that which houses similar-sized bearings that operate under constant velocity where low temperature operation is not an issue.
When choosing oil misting lubricants, viscosity-temperature profiles often are the key to proper selection. Says Bloch: “Being aware of the relative unreliability of conventional lubricant application methods involving risky oil rings and constant level lubricators, knowledgeable reliability professionals can attest to the utility and overall advantages of properly engineered dry sump oil mist systems. The known advantages of properly engineered oil mist systems far outweigh the actual or perceived disadvantages. It is unfortunate that much information to the contrary is either anecdotal or pertains to systems that were either not correctly designed, installed, maintained or upgraded as new technology became available.”
Colfax’s Berthiaume adds, “High-quality synthetic oils have the best misting properties, however, low-paraffin oils are used quite extensively.” Dibasic ester synthetics, which fail to exhibit waxing, often are valued for their decreased maintenance and servicing and are commonly used in misting applications. However, dibasic esters incompatibilities with various metals, paints, plastics and seals can arise.
In spite of their efficiency, some claim that costs, implementation changes and environmental adaptations are simply not worth the trouble. “Oil mist systems are usually purchased as capital equipment,” states Berthiaume. “While initially more expensive than conventional means (flooded bath) of lubrication, ROIs on oil mist systems is typically less than two years.” Yet, oil misting systems are becoming routine in high-speed machine spindles, aerospace and more common in small and electric motors, enclosed bearings and gears, chains and rolling element bearings.
Compact machinery designs also are using higher output rotor and precision bearings that are more thermally robust in order to prevent seizure and cope with changes to rotational speed and heat generation. Carburized nitrided steel parts and specialized coatings also can avoid the lubricant starvation that can occur in high-speed oil misting applications, leading to problem-free operation. Such changes have allowed compact oil misting designs to be implemented into car engines, providing consumers with higher horsepower, reduced CO
2 emissions and much lower oil and fuel consumption.
Newer compact oil misting systems are also available for smaller electric motors and engines, and some are now being implemented in the newer high-performance diesel engines. For example, Schaeffler Group, a Bavarian company with 180 locations worldwide, has begun to manufacture the Mercedes-Benz om651, 2.2-liter, four-cylinder diesel engine using their INA lightweight balancer shaft and rolling bearing assembly, which increases torque and power. Their new lightweight balancer shaft improves engine efficiency and fuel consumption and reduces CO
2 emissions by using a narrower design. This improves the oil mist supply to the bearings and allows for a smaller oil pump and much lower oil feed.
ProCharger supercharger kits, which use a gear-driven centrifugal supercharger, aeration-based oil pump and an oil mist lubrication system, also are now available for Gm, Ford, Chrysler, trucks/SUVs, carbureted cars, marine, motorcycle and sport compact cars. Already available at local dealerships, these supercharger kits are designed to increase horsepower, torque and engine longevity by using high-quality synthetic oils and an adapted oil mist lubrication system. This provides machinery with muscle car performance that boasts lower oil, fuel and reduced CO
2 emissions.
Overall, the future looks bright for oil mist lubrication as state-of-the art capabilities enable these systems to provide equipment with reduced oil consumption, higher speeds, heavier work loads, increased precision and longer machinery life. This is now paving the way for their implementation and use outside of the petrochemical industry, making oil mist systems more readily available to the everyday consumer.
Betty Rostro-Kohanloo is a free-lance writer based in Houston. You can reach her at bkohanloo@gmail.com.