Describe a problem you solved using a synthetic lubricant instead of a mineral-based product.
TLT Sounding Board March 2011
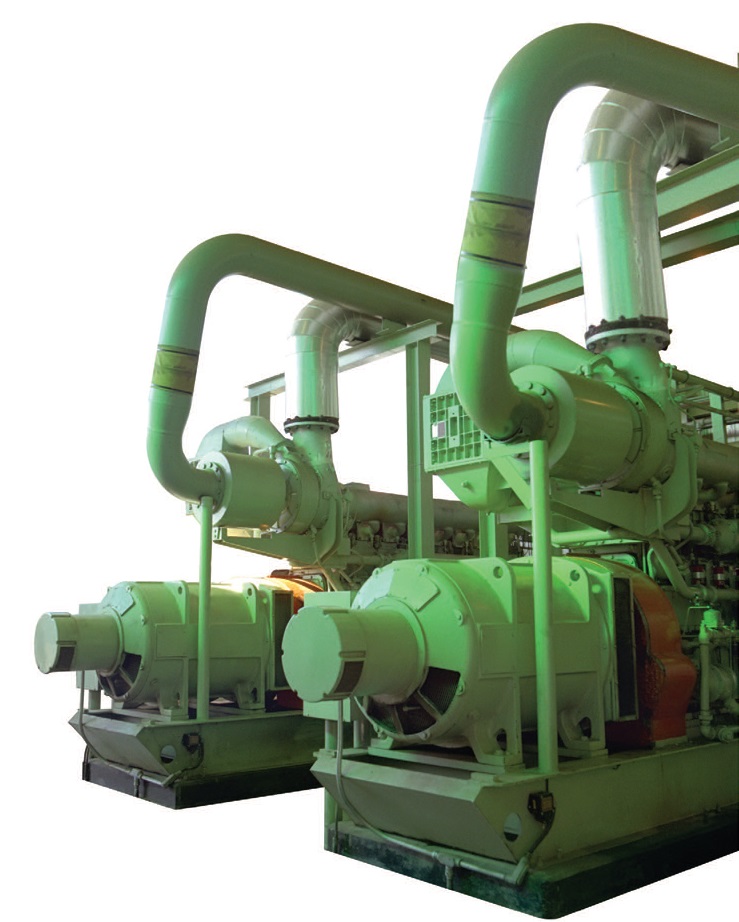
www.canstockphoto.com
How do you weigh higher product cost vs. performance vs. operational savings vs. environmental benefits? That is the decision STLE members face when considering synthetic lubricants as an option for their customers’ machinery. In many cases, the operational savings exceeded the increased product cost, with some readers reported savings between $40,000-$100,000 annually. In other situations they didn’t, and the customer, after an initial test period with the synthetic, reverted back to the mineral-based product. In many applications, the synthetic performed a job the mineral product simply couldn’t, often because of severe operating temps. Most frequently cited applications were air-screw compressors, gearboxes, pulverizers and chains. Overall, TLT readers are sold on the benefits of synthetics. Said one: “They simply work.”
Mineral oil-based product would not pump at customer operating temperatures. Ambient temperatures were subzero.
We moved the change period from six months to three years.
We use synthetic gear oil for specialized applications.
Our site discontinued the use of all compounded gear oils due to their limited life expectancy. We replaced them with synthetic R&O oils, therefore greatly reducing the need for oil changes.
No bacteria in a metalworking fluid.
Low temperature pumpability for greases.
The synthetic gear oil provided extended gear life to cooling tower gearboxes.
We are using a synthetic in our hot-service circulating pump. We have extended the run by several months. I also have been using a synthetic lubricant in all of my mixer gearboxes since 1992. I have not seen the wear metal increasing as fast as I did with mineral oil-based products.
We manufacture synthetic lubricants. We followed six screw air compressors over a three-year timeframe and allowed them to run to their maximum life. The synthetic lubricants averaged 3-4 times the life of the mineral oil, and when the compressors were inspected they were much cleaner.
Use synthetics for a pulverizer gearbox running at 190 F-210 F.
I get measurably better fuel economy in my vehicles using synthetic motor oil. I am also able to shift more smoothly using synthetic manual transmission fluid.
Large screw pumps operating too hot for conventional lube. Switched to a PAO and one-grade lower viscosity.
Automobile plants typically do not have effective PM schedules. Filling all gearboxes with synthetics at the start has gotten us very long gearbox life without routine oil changes.
Hot service reboiler pumps. Process temps range from 140 C up to 180 C degrees.
True synthetics have aided in solving a unique gear lubrication problem where wide temperature ranges were experienced. Another application was in a grease formulation where freezing temperatures were present.
Cold starting a vehicle that didn’t have access to electricity for the block heater. The vehicle did start at -41 C with a full synthetic 0W30 engine oil.
Low coking, high-temperature chain applications.
Extended bearing life on a highly overworked centrifugal pump. We got approximately two times the bearing life and significantly lowered pump temp.
I work for a company that sells a lot of synthetic lubricants. One of the main reasons is because PAOs perform much better at low temperatures in our customers’ mechanisms. I have run into more examples of this situation than I have been able to track. It goes beyond pattern or results. It is established in my mind as fact.
Extended drain intervals in haul trucks.
A gearbox on a vibratory shaker was running too hot. Switching the oil to a PAO of 1 ISO grade lower viscosity dropped the temperature by 20 degrees.
We operate a variety of equipment in harsh conditions and in most cases have chosen to use the synthetic product up front to prevent problems rather than wait for problems to appear and then try to solve them.
Open gears on kilns. High-viscosity, synthetic lubricants, improved gear life and reduced lubricant consumption made gear inspection easier.
Blast freezer at -50 F requires low pour NSF H-1 food grade.
We’ve never had a scenario where we changed to a synthetic because of a problem. In the few instances where this was done, the equipment could not be down for any reason and plant engineers recommended changing to a synthetic as part of the effort to reduce downtime on that particular equipment.
Do you feel you have a good understanding of the nature and benefits of synthetic lubricants?
Yes
86%
No
14%
Based on results from some 166 TLT readers.
A synthetic solved a lubrication problem in some coal pulverizers. The synthetic was able to handle the higher temperatures and contamination that the mineral oil was unable to deal with.
High-temperature chain lubricants based on an ester.
On a hot product charge pump running in a very hot ambient temperature (140 F), mineral oil viscosity was borderline. We changed to a PAO synthetic of the same viscosity. The higher VI of the synthetic ran well within the viscosity requirements of this pump at these running temps and extended bearing life.
Light truck transmission noise.
Synthetics reduced the operating temperature of a gearbox at a customer’s location.
Glycol-based lubricant resisted dilution by process gas, saving more than $100,000 a year in oil costs.
Open gear lubricants, durability and surface protection.
Our cold weather plays havoc on gear lubes (engines can have real issues, too, but are often plugged in). Synthetic lubes are the only ones that will fl ow in the dead of winter out here.
A synthetic oil extended oil drain intervals in rotary screw compressors to 8,000 hours.
A pulp and paper mill was operating at more than twice the maximum recommended SFPM. The supporting splash-fed Dodge and Falk gearboxes were experiencing excessively high temperatures, increased wear and shortened lubricant life with the ISO 320 mineral gear oil in service. They were unwilling to convert to mist or spray lubrication, so I switched them to an ISO 150 PAG fluid (the correct viscosity when compensated for a 227 VI and for the higher elevated operating temperature due to the higher SFPM). As a consequence, the gearbox temperatures and wear were reduced and ODIs were extended back to the original period prior to the speed increases.
Synthetic products improved the low-temperature performance of an axle lubricant to meet the performance specification. The mineral oil could not.
Extended pump life and reduced the maintenance expense of change-outs. Cost savings exceeded $40,000.
Changing from a standard automatic transmission fluid to a synthetic automatic transmission fluid dropped the operating temperature by 75 degrees and prevented the oil from burning.
Helped with skirt varnish build-up.
Have used synthetic lubricants to eliminate varnish problems in compressors. Synthetic lubricant provided no varnish and increased time between oil changes.
Needed a higher density fluid and used a POE.
Synthetics help us maintain our environmental stewardship by reducing the frequency of lubricant changes and disposals. Operating improvements are an additional benefit.
Silicon-based fluid makes a much longer lasting constant temperature bath fluid in terms of visibility.
We have had great luck in moving food grade gearboxes over to NSF-approved polyglycol lubricants. They have allowed many of our customers to extend the life of their gearboxes used in food grade applications.
Some of our vertical motor antifriction bearings run at about 200 F-205 F. Just a bit on the high side for our mineral base oil without adding alternative cooling. We have switched to synthetic and now run at these temperature levels.
300,000 miles on my personal truck with Mobil 1 5w-30.
A gear unit under severe conditions ran cooler and with greater reliability with synthetic lube.
The definition of a synthetic lubricant may vary from one industry or application to another. For MWFs, a synthetic is defined as any product that does not contain mineral oil. A customer was using petroleum-based grinding oil but had problems with occasional fires and the high cost of fire insurance. We developed a water-based synthetic product for them that gave comparable grinding performance but without the fire risk. It was more expensive but saved on fire insurance costs.
I replaced a mineral oil with a synthetic to fix a foaming issue. At another customer, they needed more lubrication and didn’t want chlorine or sulfur in their shop, so a polymer-based synthetic took over.
Need for hard vacuum pump (10^-5 Torr) used perfluorinated ether because of extremely low vapor pressure.
The use of synthetics in compressors and blowers has become the starting point to improve service life. This starting point provides immediate results to those responsible for equipment upkeep. Due to the cost, a change to synthetic lubricants can reveal the level of commitment people have to maintaining and protecting the service life of equipment.
Synthetics reduced the operating temp in a speed increaser. This allowed the operation to continue in higher ambient conditions.
I work in the food production industry. Most all our lubricants are USDA H1 Food Grade Synthetic. Better performance and longer change intervals.
A synthetic lowered the gear unit’s temperature from a delta of 110 F to 90 F. Also, at high temperatures synthetics last longer.
Customer requested an alternative to their mineral-based lubricant with the purpose of extending drain intervals to twice their existing hour interval in their natural gas engine fleet in gas compression. They used a synthetic instead of their conventional mineral-based NGEO and did get double the drain interval. However, it was not enough to offset the additional cost, and they reverted to the original mineral-based lubricant.
If a synthetic lubricant and a mineral-based product both solved a problem but the synthetic offered environmental benefits, would you pay more to use the synthetic?
Yes—that’s the price you pay for helping the environment.
34%
No—budgets are tight and I have to offer my customers the best economic solution.
20%
Only if it was mandated by regulation.
29%
Other.
22%
Based on results from some 166 TLT readers. Total exceeds 100% because some members chose more than one answer.
The synthetic formulation performed well on form-tapping aluminum. The customer wanted a synthetic but pricing was too high.
Mineral oil could not handle the extreme temperatures in the gearboxes along the line of a hot bar steel rolling mill. Replaced with synthetic and now we change oil every three years instead of every three months.
Parts from machine were cleaner and product less likely to split due to higher ability to reject tramp oil.
Hitachi Ex1800 shovel pump drives operating at a coal mine were oxidizing the oil and leading to frequent oil changes. Switched to a synthetic, lowering the temperature and extending drain interval five times over mineral oil.
We are experiencing a wonderfully appropriate Montana/Western North Dakota winter. We are also in the middle of the most recent energy development boom cycle. There is no time to wait or postpone projects. Synthetic TO-4 fluids, gear oils and hydraulics are weathering the storm and keeping construction projects on schedule. Three feet of snow, a refreshingly brisk 20-mph breeze and balmy -30 F temperatures eliminate much of the whining associated with the increase price of the synthetics. They simply work.
Any rotary flooded screw compressor using a mineral oil rapidly oxidating due to high operating temps.
A low/no out-gassing requirement for a bearing used in a fan in a guidance system.
Military applications for hydraulic fluids in aircraft show a large difference in the ability to propagate a flame. The synthetic being used is far superior to the mineral-based.
Using barrier fluid in a dual mechanical seal at -80 C.
Replaced conventional gear oil with synthetic on the gear drives on the paper machine floor. Using conventional oil, the gear drives had to be changed every three months. We were able to extend that to once a year with synthetic, saving a lot of money and also providing better gear protection.
I reduced my overall cost of lubricant purchases by utilizing the extended drain capabilities of synthetics.
Editor’s Note: Sounding Board is based on an e-mail survey of 13,000 TLT readers. Views expressed are those of the respondents and do not reflect the opinions of the Society of Tribologists and Lubrication Engineers. STLE does not vouch for the technical accuracy of opinions expressed in Sounding Board, nor does inclusion of a comment represent an endorsement of the technology by STLE.