Slip Slidin’ Away
Dr. Robert M. Gresham, Contributing Editor | TLT Lubrication Fundamentals November 2010
When rolling and sliding wear occur simultaneously, the result is a unique tribological phenomenon.
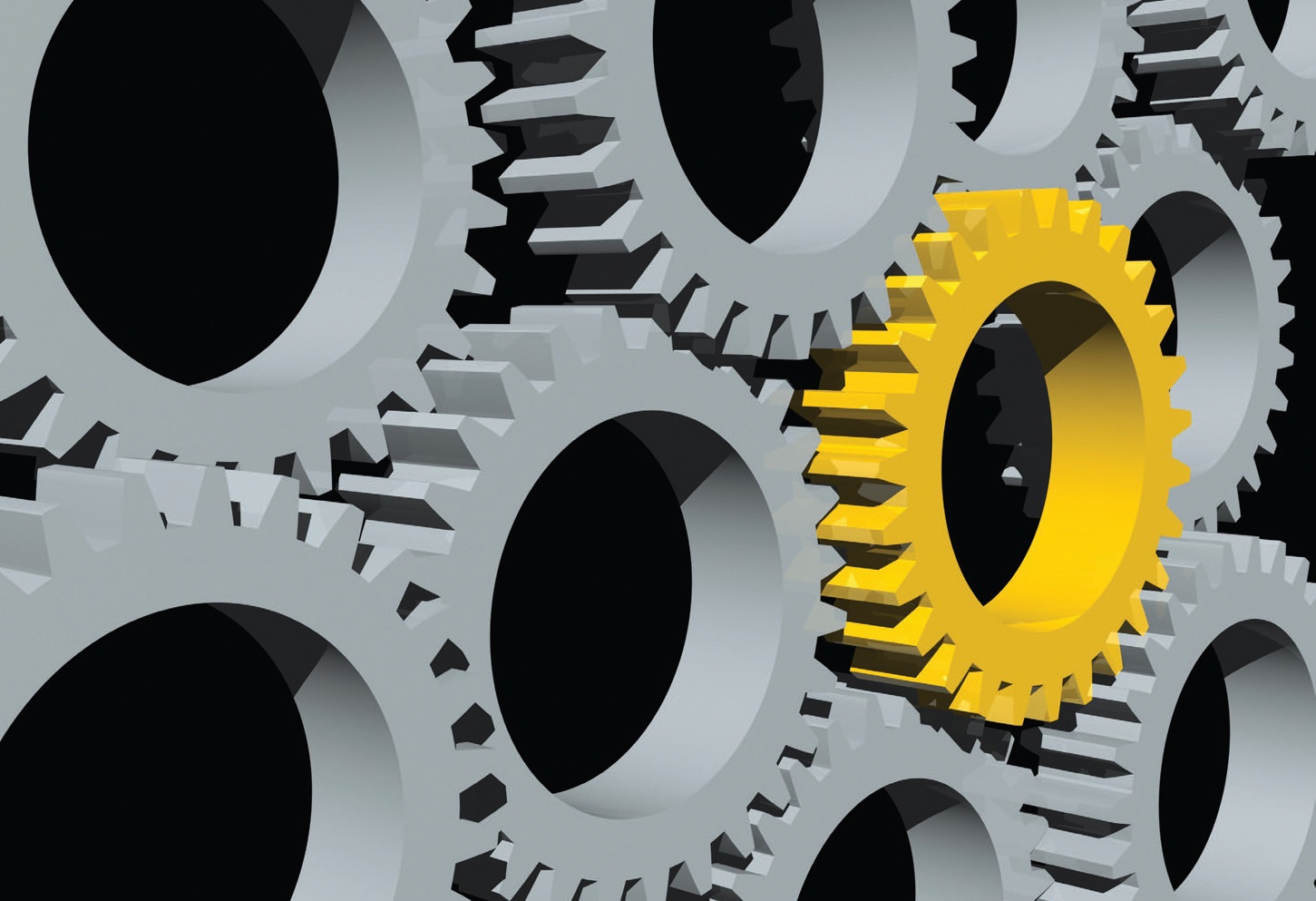
www.canstockphoto.com
Regular readers of this column know I’m constantly on the lookout for common, everyday phenomena that illustrate the principles we encounter in tribological systems. This is not always an easy task, but I think I’ve hit on a new one.
As many of you know, about 18 months ago I had my knees replaced. This resulted in a period of time, about a year before the surgery and six months after, where I wasn’t quite myself physically. I live in the country, and among the tools that I frequently use is a large garden tractor and wagon, which I use for hauling something somewhere almost every day.
Well, when the knees were hurting, I had a minor wreck because I couldn’t get the knee to get the foot on the clutch fast enough. The result was a slightly bent tie rod that caused the front wheels to skew slightly. Further, one of the wagon wheels was bent slightly out of line.
It didn’t seem to be much out of alignment, and given that it was winter and cold and the knees were aching and on fire I said to myself, “Self, not to worry. It’ll be just fine.” Of course, you readers would never make these kinds of rationalizations, right?
Fast forward to today. I’m out pruning some trees and hauling the detritus away. As I’m riding along with a wagon load, I notice that both front tires on the garden tractor are wearing quite a bit more than the rear tires (see photos). I’m thinking that is just because of the added stress of turning—I see it on cars all the time (more rationalization). But was it disproportionally more wear? Looking back at the wagon, I noticed that the right tire, the one bent slightly out of line, also had most of its tread worn down. Yet the left tire, which was in near perfect alignment, was in great shape for its age. So what’s going on?
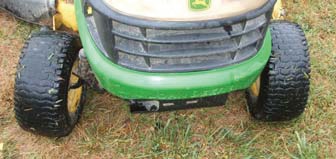
Front tires
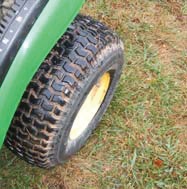
Back tires
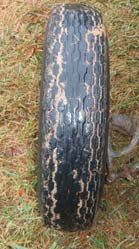
Left
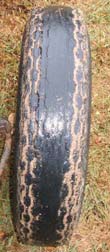
Right
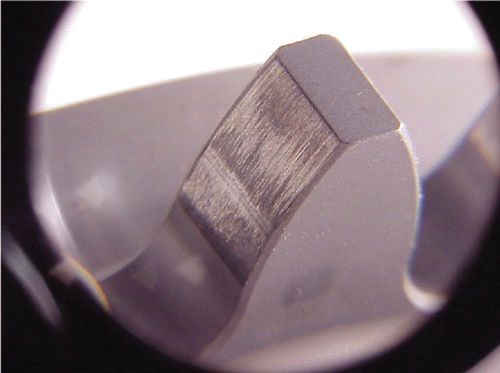
Rolling and sliding wear often is seen in gear systems.
ROLLING AND SLIDING CONTACT
Clearly this is an example of the combination of simultaneous rolling and sliding contact that tribologists talk about. This sliding component added significant scuffing and abrasive wear to the out-of-alignment tire. The front tires, in addition to the stress of turning, also are sliding and rolling when going straight. Thus, they were wearing out more rapidly that they should. They were literally “Slip Slidin’ Away.”
We see this phenomenon in mechanical systems all the time. The best example is in certain gearing systems, as shown below, which show sliding and scuffing along with rolling line contact. STLE-member Vern Wedeven of Wedeven Associates in Edgemont, Pa., designed a special test rig that precisely demonstrates and quantifies these processes.
His rig is a rolling ball-on-disk machine that allows him to vary the load and speed. It also allows him to dial in sliding motion in any desired percentage to simulate the precise combination of rolling and sliding in a given mechanical system and then measure and photograph wear scars. Pretty cool. If you want to discuss this with Vern, you can reach him at (610) 356-7161, gwedeven@wedeven.com.
So how do we prevent this kind of wear where a certain proportion of rolling and sliding contact is a necessary consequence of our mechanical system? Regarding the system’s lubricant, of course the first thing is to get the right viscosity of our base oil. The goal here is to maintain a full fluid film in the mating surfaces when at load, temperature and speed. This is the sweet spot on the Stribeck curve.
But this is not enough, as we have to manage start-up, shut down and other times where load, speed and temperature variations result in metal-to-metal contact. Formulators can use application-specific combinations of additives such as boundary lubricants, friction modifiers, EP, antiwear and antis cuff additives. Again, gear oils are good examples of such formulations.
So when you feel like your machine components are slip slidin’ away, call your lubricant supplier. He likely will have a solution for your problem.
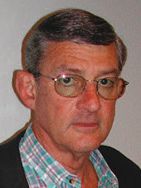
Bob Gresham is STLE’s director of professional development. You can reach him at rgresham@stle.org.