Providing Solutions for Sporting Gear Protection
RealWorld Proof of Performance – It was tough but someone had to do it.
Designing chemical solutions for the practical challenges of gear lubrication has become a specialty science involving high tech chemistry, tribology and physics. To the average motorist, gear lubrication may not be something that concerns us. How many even know if the vehicle we drive even has a rear axle which needs lubricating? To the gear formulation team at Afton Chemical, designing solutions to meet gear and transmission lubrication challenges has been an objective for over half a century. Occasionally during that time, we have been invited to help in areas quite different to the world of heavy duty trucks and SUVs. Examples include racing gear oils and marine gear oils.
The world of marine gear presents some interesting challenges, not least of which is brought on by the presence of water. The very nature of the application means that water contamination of the lower unit or outdrive transmission is not just possible but highly likely. Conversely, most gear lubricant technology is developed with only small levels of water contamination in mind. One of the most fundamental decisions that must first be made, therefore, is how to deal with the water when it gets into the system. Generally, there are three possible design strategies:
1.
Ignore the water and assume that it is either low enough in concentration not to matter, or that the application will run hot enough to evaporate it before it becomes a problem.
2.
Separate the water and establish a maintenance practice that includes draining the water periodically.
3.
Emulsify the water and formulate the lubricant to function well in this emulsified state.
Strategy 1 is probably the most common and is adopted with most automotive and commercial axles today. Typically these oils will pass rust tests so that small water contamination will not cause any corrosion issues. These tests include the CRC L-33 rust test which forms part of the API GL-5 and SAE J 2360 specifications.
Strategy 2 is very common in the industrial sector, where the sump may be drained periodically. Not only do these industrial fluids have to meet rust inhibition standards, but must also separate contaminant water. Tests adopted by the industry which measure this water separation include the ASTM D1401 and the ASTM D2711 tests.
Strategy 3 is the least common and may be adopted in certain applications, including some mining gear, rock drill and marine applications. It is also interesting that tractor hydraulic oils (THF), while not meeting the API GL-5 specification, often will be used to lubricate the gears and the power take off units in the tractor. OEMs typically require that THF absorb at least a portion of any water that gets into the system.
Given the potency of many modern rust inhibition technologies, one may ask the question what is the big deal with water contamination? Generally, the OEMs regard water as a serious challenge to their equipment. In cold weather it may freeze and actually cause physical damage. Water is a very poor lubricant; with high levels of water there is a risk that it will displace the oil in bearings, between the gear teeth and in other places. Catastrophic wear could then ensue. There is little doubt that choosing the right strategy is a critical part of any lubrication design.
For marine gear applications a clear strategy of emulsification has been adopted in the industry. The oils which will emulsify both fresh water and sea water and provide stable emulsions are considered superior for this application to oils which either separate water or form only weak emulsions. Water emulsifying characteristics may be measured using a variety of different tests including the ASTM D1401 and D2711, though many others exist.
Figure 1 shows the difference between a emulsifying gear oil and a demulsifying gear oil in one of these tests. To best simulate likely water intrusion in the lower unit, Afton found it best to test using high speed shear and incremental water addition to reach full test level contamination.
Figure 1. Superior emulsion characteristics provide superior lubrication protection in wet gear environments such as marine applications.
Many industry rust tests were developed to screen oils for fairly mild water contamination. For example, the ASTM D665 test has been used for many years to evaluation hydraulic oils which typically will only see some 1% water contamination or less. Indeed, marine gear oils will tend to pass these tests without difficulty. Much more sensitive is the ASTM D1748 humidity cabinet test which enables formulators to evaluate superior marine gear oils (see
Figure 2).
Figure 2. ASTM D1478 humidity cabinet test run in 100% humidity for 10 days clearly shows the advantage of modern technology designed to cope with prolonged water contamination.
While very important performance criteria, emulsion stability and corrosion protection are not the biggest challenge brought by the marine gear environment. This relatively small gear box transmits sufficient power to bring rapid acceleration which leads to very high contact stress on the gearset. Protecting the gears and the bearings from wear, pitting and breakage is a key challenge. Many lubricant tests have been designed over the years to simulate high torque and variable speed conditions experienced in gear applications. Some of these include the L-37 ASTM D6121, L-42 ASTM D7452, 4 ball tests, Timken tests, FZG and many others. While very useful, passing these tests provide only a portion of the reassurance needed that marine gear boxes will be adequately protected. To be more confident, some of these tests must be run on the lubricant which is deliberately contaminated with levels of water. Typically these levels may be as high as 10%, though in some circumstances, levels as high as 20% have been evaluated. See
Figure 3 and
Figure 4 for examples of wear and EP tests conducted on marine gear oil where water was added. (A word of caution, some of these standard industry tests run at temperatures above the boiling point of water. There is a danger that boiling may cause the contents of the reservoir to spray out of the test, which may risk injury to the operator. It is advisable to take extra precautions during these tests or modify the procedure to accommodate the water present).
Figure 3.
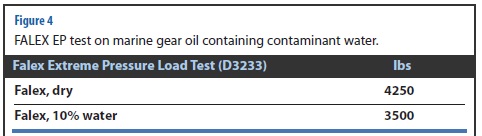
Figure 4.
Field Testing
In order to prove the performance in the field (or should we say ocean?), the technology was tested under extreme conditions. Twin Yamaha 225 hp lower units were installed on a 33 foot 15,000 lb sport fishing boat. To evaluate under worst case conditions, no 20-hour break-in was performed. One lower unit was filled with a test lubricant, while the other was filled with a reference product. The testing lasted 300 hours, with lube inspections every 100 hours. It should be noted that the factory recommended maintenance is to change the gear lubricant every 100 hours, but for this evaluation the lubricant was left in the sump for three times this recommendation. The lower unit transmissions were then torn down and inspected.
The route was conducted on the East Coast of the United States in the Chesapeake Bay area. This included salt water and fresh water environments. Included were Ocean fishing, Bay scenic tours, and river tours.
Figure 5 shows the planned 10 hour daily cycle, which describes the typical stress placed on the lower units throughout the day. Sea state and weather conditions, as well as waterway traffic prevented exactly following the test cycle, but these speeds and loads were maintained as best as possible.
Figure 5.
Conclusion
Providing technology for gear applications involves many areas and environments. Adapting the chemistry to cope with high levels of water contamination provided a significant challenge for Afton’s gear team to rise to. After exhaustive laboratory and real world field testing, the latest technology, Afton’s HiTEC® 372G marine gear oil additive, is enhancing lubricant protection in the field.