Grease life in ball bearings: The effect of temperatures
Drs. E. Richard Booser and Michael M. Khonsari | TLT Technical Analysis October 2010
Limiting factors define grease life in four distinct temperature zones.
KEY CONCEPTS
•
Defining potential grease life is required for less maintenance and lubricated-for-life bearings in electric motors, industrial, transportation and marine applications.
•
At elevated temperatures grease life is limited by oxidation and oil loss from evaporation and creep.
•
Increased grease stiffness and decreased mobility of oil content can lead to a shortened life span at low temperatures.
Greases are used in millions of ball and roller bearings that normally contain the same type and viscosity of oil. The gelling agent is selected for its ease in compounding the grease, stability over a wide temperature range, water resistance and mechanical stability under shear action of the rotating ball complement. Operating temperature plays a critical role on grease usefulness. This temperature dependency makes it difficult for the engineer to select an appropriate grease for the job and for maintenance personnel to set up an effective regreasing schedule.
While OEM recommendations and past experiences should be used as the primary source, useful guidelines can be obtained by examining limiting factors that define grease life in four distinctive temperature zones.
Petroleum mineral oils are used in over 98% of current greases. The low evaporation rate needed for long life combined with low temperature utility dictates that these oils are usually in the SAE 20-30 viscosity range with 40 C viscosities of about 100 to 300 cSt. Higher viscosities up to 900 cSt employed for some slow speeds and heavily loaded bearings commonly result in noisy operation, high torque and a restricted low temperature range. Synthetic oils, primarily synthetic hydrocarbons (PAOs) and esters are used in 1%-2% of greases for unusual temperatures or other demands not readily met with conventional mineral oils.
COMMON AGENTS
Common agents used to gel the mineral-oil phase are fatty acid soaps of lithium, calcium, sodium and aluminum at 6%-20% concentration. Since 1942, lithium soap grease use has expanded to make up about 75% of the market. They are water resistant, and their original temperature limit (in the 110 C-125 C (230 F-257 F) range) has been raised to 150 C-175 C (302 F-347 F) by use of low-molecular-weight organic acid as a complexing agent in making the soap.
For high-temperature service, polyurea non-melting powders are finding increasing use in electric motors, industrial, transportation and marine applications up to about 175 C (347 F). Fine bentonite clay particles also find use in mineral oil and synthetic hydrocarbon greases for the Navy, nuclear power plants and other demanding applications.
Oxidation-inhibiting additives at 0.1%-1.0% concentration are commonly used to extend shelf and operating life many fold along with a rust inhibitor for enhanced water and salt spray protection. While extreme-pressure additives are necessary in some greases to minimize wear at low speeds with shock and oscillating loads, their decreased thermal stability may undesirably shorten grease life by 50% or more in applications for which their extreme-pressure and antiwear properties are not required.
The following sections in this analysis review operating grease life that may be expected before encountering 10% of failures in an application. These individual lifetime factors for the four temperature zones shown in Figure 1 involve primarily: (1.) Oxidation to bring about drying of grease at high bearing temperatures above 150 C, (2.) Oil loss by evaporation, creep and other physical dissipation in a warm range from 70 C to 150 C, (3.) Limitations characterized by bearing suppliers in the common operating range of 40 C-70 C and (4.) Grease hardening and high oil viscosity effects at lower temperatures. These are given in terms of usual speed and load conditions in industrial service with single-row ball bearings.
Figure 1. Bearing temperature vs. life plot for premium mineral oil grease.
Lastly, we’ll review life correction factors for more demanding conditions.
HIGH TEMPERATURE ZONE (ABOVE 160 C)
In this range, oxidation is commonly the primary life factor that causes hardening and drying of the grease. As typical with mineral oils and hydrocarbon liquids, the rate of oxidation doubles for each 10 C temperature rise. This pattern is reflected in the following Arrhenius equation with log of grease life L (hr) related to the reciprocal of absolute temperature [273 + C]:
log L = A + B/(273+ C ) (1)
where B = 6,000 for grease life dropping in half for 10 C rise in this temperature range. A = 10.75 to reflect life of the order of 300 hr at 180 C encountered in ASTM D3527 wheel-bearing tests with premium petroleum greases (
1).
WARM ZONE (70 C TO 160 C)
Greases in this next cooler range typically fail when 50% of their oil content is lost by evaporation, bleeding and other primarily physical processes. With the lower activation energy for these physical oil life factors, life drops by a factor of 1.5 per 10 C temperature rise (
2). The Arrhenius equation then becomes:

(2)
Activation energy term E = 2,450 corresponds to 1.5 per 10 C. Life term D is -2.60 for a number of premium mineral oil and synthetic greases using various thickeners such as lithium hydroxystearate, complex metal soaps and non-melting polyurea powders (
3). With silicone oils and their low surface tension leading to higher oil loss by creep and bleeding, D is commonly on the order of -2.8. Low temperature greases compounded with diester oil display significant evaporation loss with D = -3.5. Representative values of Equations 1 and 2 life factors for a number of grease types is shown in Table 1.
Table 1. Representative grease life factors in Equations 1 and 2 for elevated temperatures (a).
NORMAL INDUSTRIAL TEMPERATURE RANGE (40 C TO 70 C)
This temperature range is encountered by a large portion of ball and roller bearings in electric motors and a wide variety of industrial machinery. Bearing manufacturers such as SKF and FAG commonly give a relubrication life period of about 40,000 hours under mild speed, load and service conditions.
When temperature drops below roughly 70 C, (i.e., the lower limit of the warm zone), the rate of oil loss from the grease is balanced by the relative increase in the oil viscosity compared to the warm zone.
LOW TEMPERATURE LIFE ZONE (BELOW 40 C)
Dropping below this usual industrial operating range brings a distinctive drop in grease life (
see Table 2). This drop in life L can be judged from past observations in 25,000 rpm fractional horsepower motors (
4) to follow as the square of increased viscosity of the oil v in the grease.
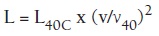
(3)
Table 2. Life with representative greases in low temperature zone.
Two life-reduction factors are likely involved with the viscosity increase at low temperature: (1.) Grease becomes harder and its ability to feed to bearing surfaces becomes less effective and (2.) With less bleeding, the oil mobility decreases for reaching the ball cage pockets (
5) and for refeeding loaded ball-raceway contacts (
6).
This low temperature relation is complex. In one experience with midwinter ball bearing failures in suburban railway cars, stiffened NLGI Grade 2 mineral oil grease was found to be the culprit for immobilizing the ball assembly in the bearing cage pockets. The rotating shaft and inner bearing ring merely skidded at full speed within the static ball assembly and caused premature bearing failures. The grease oil viscosity at ambient temperature was in the 15,000 cSt range. With this viscosity level, however, frictional heating from initial bearing rotation, combined with heating from an electric motor or other machine elements, often may gradually raise grease temperature into a more normal temperature range with satisfactory grease life.
As an extreme, maximum oil viscosity in grease for starting and running ball bearings in medium torque equipment is approximately 100,000 cSt (
7). The grease becomes so immobilized that impossibly high torque is required to start rotation in most electric motors and related industrial machines.
LIFE CORRECTION FACTORS FOR DEMANDING CONDITIONS
High DN Operation. Reduction in grease life with higher surface speeds can be approximated by applying a reduction term of 9.6×10
-7 kDN to log L values for each of the four temperature zones for mild running conditions in open, single-row, deep groove ball bearings. This decrease in life with increasing DN values (mm bearing bore × rpm) reflects greater demands for lubricant feed rate at higher surface speeds.
While this kDN velocity term reflects experience with premium Grade 2 greases in open ball and roller bearings in electric motors and related equipment, the pattern of decreasing life with increasing DN varies greatly. Greater sensitivity to high DN values may be encountered, for instance, with stiffer greases used to accommodate close confinement in sealed bearings and high temperatures.
Limiting DN values are eventually reached at about 270,000 for medium cross-section (300 series) single-row ball bearings of standard ABEC-1 precision. Above this limit, a rapid drop in grease life should be expected in the absence of specific performance trials. Increased lubrication needs for other bearing types are reflected in the k speed factors of Table 3.
Table 3. Speed factor coefficients for various bearing types (a).
Centrifugal Grease Throw-off. Centrifugal throw-off of grease from bearing surfaces with increasing speed is believed to eventually reduce lubricant film thickness below the surface roughness in loaded contact films to set this DN limit. With lubricant availability from oil-soaked phenolic cages, the higher speed limit in Table 4 may correspond to lubricant throw-off from the balls and cage. Finer surface finish with precision ABEC-5 and -7 bearings also provide a higher DN limit with their need for lower ball-raceway lubricant film thickness. Conversely, 35% lower speed limit values observed with silicone greases may result from easier throw-off of the lower surface-tension silicone oil in the grease (
2).
Table 4. Approximate speed limits for grease lubrication.
Outer Ring Rotation and Cage Effect. Interestingly, outer ring rotation is found to reduce grease life to 42% of that with usual inner ring rotation. The effect corresponds to obtaining the same life with the same cage speed for rotation of either the inner or outer bearing ring (
9). This would imply that lubricant throw-off from cage and ball surfaces is a major life and speed limiting factor.
Although difficult to quantify, high bearing loads also decrease expected grease life only to a minor extent for C/P ratios 4, where C is the basic dynamic load rating and P is the equivalent bearing load (
10). Theoretically, load does not much affect either load-carrying film thickness in a ball bearing or film thickness on cage surfaces. Increased thermal heating becomes significant for high loads with C/P > 4.
ILLUSTRATIVE EXAMPLE
Following is the estimated life expectancy of premium mineral-oil ball bearing grease at 900 rpm in a 6210 ball bearing (bore diameter D = 50 mm) at temperatures of 180 C, 120 C, 60 C and 10 C:
(a.) At 180 C in the hot zone using Equation 1:
Log L = A + B/(273+C) = -10.75 + 6000/453 = 2.455
L = 312 hr
(b.) At 120 C in the warm zone using Equation 2:
Log L = D + E/(273+C) = -2.60 + 2450/393 = 3.63
L = 4,266 hr
(c.) At 60 C in the usual industrial range (
see Figure 1)
L = 40,000 hr
(d.) At 10 C in the cool range using Equation 3 with viscosity of the oil in the grease being 125 cSt at 40 C and 750 at 10 C, Equation 3 yields:
L = L
40C × (v/v
40)
2 = 40,000 x (125/750)
2
L = 1110 hr
(e.) Attributing life reduction for the kDN speed factor at 120 C, for the case b with log L = 3.63:
9. 6 ×10
-7(kDN) = 9.6 × 10
-7(1.0)(50)(900) = 0.0432
Log L = 3.63–0.0432 = 3.587
L = 3864 hr, a 9% reduction from the predicted 4266 hr using Equation 2.
CONCLUSIONS
Considering the commonly poor reproducibility and generalization of grease test results, the most reliable use of grease-life relations is likely in extrapolations from established operating conditions. If bearing temperature drops from 90 C to 80 C, for instance, life would be expected from Equation 2 to increase by 50%. Corresponding adjustments in regreasing schedules might follow the life factors related to changes in types of bearings and their size and speed.
In considering any new grease for a given application, life might first be calculated from laboratory spindle results. This might involve simply comparing bench life test results for the new grease with those for a grease now in use. Many laboratory test data, however, are for relatively small diameter ball bearings at speeds and temperatures above those in industrial applications. As such, comparative test results may have limited significance for a specific application at more usual operating conditions.
Any grease that shows promise should then be subjected to an operating trial under the most severe conditions to be expected. This allows observations for noise, any temperature peak with overgreasing, slumping, leakage, water washout and related in-service demands expected.
REFERENCES
1.
Rhee, In-Sik, “Decomposition Kinetics of Greases by Thermal Analysis,”
NLGI Spokesman, June 2007.
2.
Booser, E.R. (1974), “Grease Life Forecast for Ball Bearings,”
Lubrication Engineering,
30 (11), pp. 530-540.
3.
Khonsari, M.M. and Booser, E.R. (2008),
Applied Tribology – Bearing Design and Lubrication, John Wiley & Sons, West Sussex, UK.
4.
Smith, R.L. and Wilson, D.S. (1980), “Reliability of Grease-Packed Ball Bearings for Fractional Horsepower Motors,”
Lubrication Engineering,
36 (7), pp. 411-416.
5.
Cann, P.M., Donner, J.P., Webster, M.N. and Wikstrom, V. (2001), “Grease Degradation in Rolling Element Bearings,”
Tribology Transactions,
44 (3), pp. 399-402.
6.
Cann, P.M. (1999), “Starved Grease Lubrication of Rolling Contacts,”
Tribology Transactions,
42 (4), pp. 867-873.
7.
Baker, A.E., Jackson, E.G. and Booser, E.R. (1953), “The Significance of Grease Testing,”
Lubrication Engineering,
9 (5), pp. 249-253.
8.
FAG Bearings Corp. (1995), “FAG Rolling Bearings,” Catalog WL 41 520 ED, Danbury, Conn.
9.
Kawamura, T., Minami, M. and Hirata, M. (2001), “Grease Life Prediction for Sealed Bearings,”
Tribology Transactions,
44 (2), pp. 256-262.
10.
SKF Products (2009), Interactive Engineering Catalogue/R.
Richard Booser is a consultant in Vero Beach, Fla. He served as 1956-57 STLE president and was the editor of the highly-acclaimed STLE/CRC Press Tribology Handbook series published from 1983 to 1997. You can reach him at ERBooser@aol.com.
Mike Khonsari is the Dow Chemical Endowed Chair in Rotating Machinery and professor of mechanical engineering at Louisiana State University in Baton Rouge, La. He is an STLE fellow and also serves as associate editor of Tribology Transactions. You can reach him at khonsari@me.lsu.edu.