Oil analysis in the real world: Part V
Jack Poley | TLT On Condition Monitoring September 2010
Diesel engine oil analysis requires a comprehensive test package.
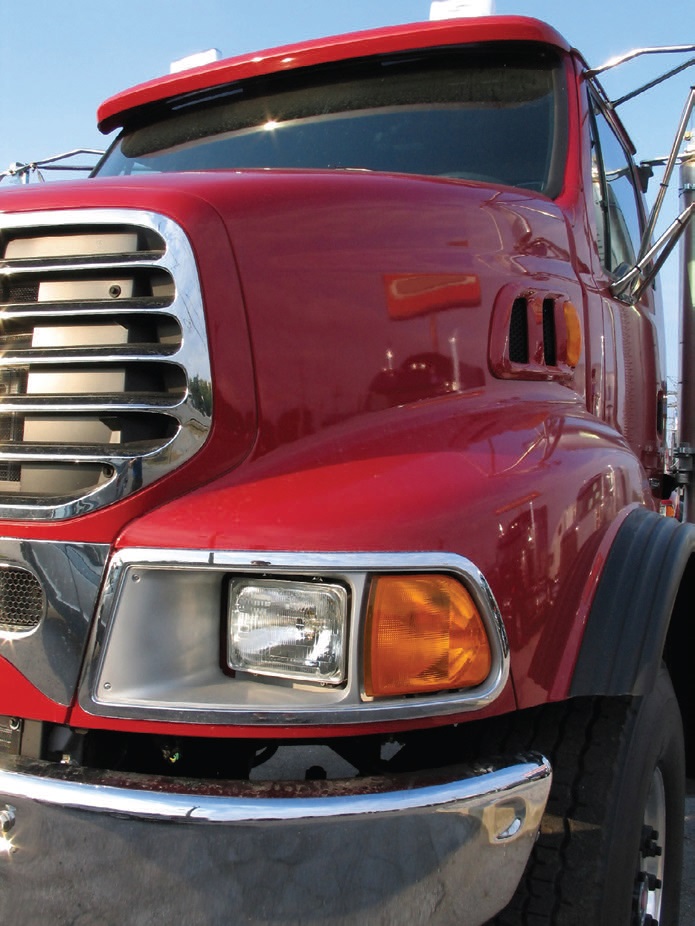
www.canstockphoto.com
Let's pick up from our discussion from the July TLT with our choice of tests for a diesel engine. We assessed the things that can go wrong with oil analysis. Here's how we might go about monitoring those possibilities.
WEAR METALS MONITORING, PARTS-PER-MILLION
Major wear metals - mandatory tests are the Big 4:
1.
Iron (Fe)
2.
Aluminum (Al)
3.
Copper (Cu)
4.
Lead (Pb)
Minor wear metals: Certain tests offer value as wear-point differentiators. Tests that are often useful and recommended are: chromium (Cr), nickel (Ni), tin (Sn), molybdenum (Mo) and antimony (Sb). Tests that offer very occasional value include vanadium (V) and manganese (Mn).
Discussion: Major metals are non-negotiable and always should be in the wear metals package. The recommended Metals also are close to vital. The occasional metals are only needed when there is knowledge that they'll be useful, owing to a particular manufacturer's inclusion of that metal in sufficient amounts that it could be detectable in a wear situation. Some manufacturers are not as forthcoming as others in this regard.
CONTAMINANT METALS MONITORING, PARTS-PER-MILLION
Abrasives: Major is silicon (Si). Minor is aluminum (Al). Others could be included if specifically. Coolant Additives: Potassium (K), boron (B), sodium (Na) and silicon (Si).
Discussion: Silicon is by far the most common and effective indicator of abrasives or 'dirt,' as the slang goes. New engine oils may have 5-14 ppm of antifoaming additive (silicon basestock synthetics not withstanding and, luckily, not found in diesel engine oils).
This amount becomes the baseline or zero-point for assessing possible abrasives contamination. Aluminum (and others) may be a factor as an abrasive, too, but it is usually in less concentration than Si. Of course, Al is also a wear metal and, thus, tricky to isolate. Nevertheless, a capable evaluator can logically assess it in proper context.
ADDITIVE METALS MONITORING, PARTS-PER-MILLION
Very Common: Magnesium (Mg), calcium (Ca), phosphorus (P), zinc (Zn) and Silicon (Si). Common: Molybdenum (Mo) and Barium (Ba). Occasional: Boron (B), sodium (Na) and potassium (K).
Discussion: The primary purpose of analyzing for additive metals in a used oil is to (you hope) gain assurance that the correct product is likely in the crankcase. Simply noting that the additive metal(s) concentration remains roughly the same from sample to sample in a given component does this. Spectrometric metals analysis
does not qualify the nature of the additive metals in terms of their continued effectiveness. While the spectrometer can determine the concentration of, say, Mo, it has no ability to distinguish the chemical form the Mo represents.
Molybdenum as an additive is frequently found in gear oils nowadays but is also seen in diesel engine oils with regularity. When present, it is at levels of at least 50 ppm, precluding any value of detecting Mo as a wear metal where the concentration would be too low to effectively differentiate wear from additive. This kind of masking occurs whenever an element can exist in more than one category or chemistry (wear vs. contaminant vs. additive), as noted with Si and Al earlier.
Recommendation: There are three types of spectrometric techniques routinely employed for wear metals monitoring:
•
Emission Spectroscopy (RDE): Rotating disc electrode
•
Emission Spectroscopy (ICP): Inductively coupled plasma
•
Absorption Spectroscopy (AA): Atomic absorption.
AA is perfectly effective but obsolete in terms of the number of elements it can practically address, as only one element at a time can be analyzed. This makes AA practical for only small-throughput labs or where only a few metals (say 5-6) are required. Emission spectrometers, on the other hand, can analyze for 20 or more elements in one pass, so the time to analyze is geometrically less than that of AA.
RDE and ICP are both acceptable methods, so either one should be suitable. My own choice for diesel monitoring would be RDE, but ICP will certainly work. Which method one chooses is not as critical as how well maintained, calibrated and standardized the instrument is within its lab environment and, of course, assurance that the suite of metals the lab offers meets the minimum needs per above.
Finally, the metals listed above are not necessarily the last word. The person(s) evaluating your data should know what metals are expected, and those metals should be a part of the testing suite. You have a right to ask if that is the case provided you also are forthcoming with information about the manufacturer and model of the component, the application, duty cycle and environment of the engine and the oil brand in use, including furnishing reference samples periodically. If you do your part, you should expect the quid pro quo of a qualified, knowledgeable evaluation.
CONTAMINATION, NON-METALLIC
Fuel: Fuel dilution is a major concern in diesel engines and quite common. It's important to have a dependable means of assessing this contaminant. Two testing components, kinematic viscosity and a percent measurement of fuel to a tolerance of not more than plus/minus 1%, enables a good assessment of fuel dilution. One value corroborates the other to yield excellent confidence.
Viscosity must be at 100 C (not 40 C) for diesel engine oils. Viscosity alone is not sufficient to assess fuel dilution. Other mechanisms such as shearing or the addition of the wrong oil can affect viscosity.
Fuel measurement is accomplished primarily by three methods:
•
Gas chromatography (GC): the gold standard.
•
Flash test: not as sensitive as GC but better than nothing.
•
Infrared (FTIR/IR): requires a fuel reference-difficult to calibrate to a percentage result-often reported in non-standard scalar units. Least recommended.
Recommendation: GC is simply superior to the other methods, but FTIR is very popular because it can accomplish a variety of tests, giving labs a more competitive position. GC only does fuel dilution, so its slightly more costly. It's your engine...
Water: It is not easy to collect, let alone test an oil sample for water, given oil and water's normal immiscibility. Many labs use a hot plate "crackle" test to establish the presence of water, then follow with a Karl Fischer (KF) test, yielding ppm water. While not at all a guarantee of the true water content of the sump, it is a least-of-evils approach. FTIR also offers a result but still has the caveat of proper referencing to consider. Most of the time any significant water found in diesel engine oils is emblematic of a cold, invalid sample.
Glycol: The purpose of detecting glycol is to identify a coolant leak into the crankcase via a head gasket breach, oil cooler pinhole or other cooling system failure. While measuring glycol directly, a colorimetric kit is usually effective, and the detection of coolant additive metals via metals spectroscopy, as described above, is quite a bit more sensitive and often more dependable. This is particularly the case when K is present, since it rarely has any other source possibility other than as a coolant additive metal. Direct glycol measurement, therefore, is considered optional for most diesel engine applications.
FTIR can be programmed to determine glycol with precision approaching the colorimetric test, but again careful attention must be paid to proper referencing. Coolant additive metals offer better assurance most times.
Soot: Carbonaceous residue from incomplete combustion. Only one method, FTIR, is commonly in use because it is quick and usually good enough. There are some site-adapted non-FTIR test kits that also do a workman-like job. The reference method is thermogravimetric analysis (TGA), but it is far too tedious and expensive to employ TGA routinely.
Fuel soot results from FTIR involves a light scattering method based on the Tyndall effect. As such a reference is not nearly as critical as for other data derived from FTIR.
LUBE DEGRADATION
Oxidation: When reacting with oxygen, oil begins to thicken and provide less effective lubrication. There are bench tests that provide very good oxidation indication, but the default test is FTIR, once again owing to its cost and efficiency. FTIR does a very good job for oxidation, provided a reference is in place. Synthetics may mask the results with this method.
Base Number: Base number isn't nearly as important as it was before the advent of desulfurization of diesel fuel. The correct (best) method for base number is one of two titration methods provided by ASTM. However, a reasonable estimate (remember to get a reference) is available via FTIR and is easily good enough, certainly in the North American environment. Oxidation and fuel soot build up much before a base number begins to reflect a problem.
Acid number: Acid number has never been a popular test for diesel engines and has even less merit now owing to desulfurized Fuels. It is not a recommended test for diesel engine oils at this time, except if significant sulfur is present in the fuel consumed.
OPTIONAL: FERROUS PARTICULATES
It is well understood that standard spectrometric wear metals testing does not detect particles much greater than five micrometers; thus evidence of fatigue wear may be present but missed. There are screening tests that help fill this gap and they should be considered for high value assets such as large, slow-speed diesels. For the record, high-speed, four-cycle engine oils don't usually show high quantities of fatigue-oriented ferrous particles. Put another way, routine spectrometric Fe analysis usually identifies the possible onset of such wear trauma.
PQ or other large ferrous particle screening: Ferrous particle screening is done with magnetic technology. The PQ is, perhaps, the simplest and easiest method available for this purpose. When considered with other test results, a more informed opinion can be rendered, particularly for decision making as to a tear down inspection for wear.
Laser Net Fines: This is a unique instrument that differentiates and counts several particle shapes, beginning at 20 micrometers, although the composition of the particles is not addressed. Because the instrument also can estimate water with reasonable precision and provide a particle count (dubious value in a diesel engine but certainly valuable in hydraulics), it has multifarious contributions.
For diesel engines, I'd opt for the PQ analysis if ferrous particle screening is deemed appropriate. Again, consider the value of the asset.
COMPOSITE TESTING PACKAGE
•
Spectrometric Metals: The minimum with no influencing information.
•
Major Wear: Fe, Al, Cu, Pb.
•
Minor Wear: Cr, Ni, Sn, Sb.
•
Contaminant: Si, K, B, Na.
•
Additives: Mg, Ca, P, Zn (Mo).
•
FTIR: More data will likely be available from this test, but these are key.
o
Oxidation.
o
Fuel Soot.
o
Cursory Water (or Hot Plate Crackle alternative), with KF vetting if positive.
•
Gas Chromatography: Fuel contamination to nearest percent.
•
Viscosity: Not debatable.
•
PQ or similar: Optional.
Jack Poley is managing partner of Condition Monitoring International (CMI), Miami, consultants in fluid analysis. You can reach him at jpoley@conditionmonitoringintl.com.
For more information about CMI, visit www.conditionmonitoringintl.com.