The quest for ‘fire resistance’
Jean Van Rensselar, Contributing Editor | TLT Feature Article September 2010
Researchers are hampered by inadequate test methods and an inability to even agree on the term.
KEY CONCEPTS
• The lack of an agreed-upon definition for fire resistance allows volatile lubricants to be used in high-fire-risk applications.
• Lubricants need to be tested and rated for both ignitability and combustibility.
• Fire-testing laboratories need to do a better job of replicating real-world use scenarios.
Nearly 10 years ago, on Nov. 11, 2000, 161 skiers and a conductor boarded an Austrian train for an early morning trip to the slopes. Around 9 a.m., just after the train entered a tunnel, an electric heater caught on fire. The small fire set off a chain of deadly events–igniting a slow leak of highly flammable hydraulic oil which then melted through plastic pipes carrying hydraulic brake fluid. The loss of fluid pressure kicked on the safety system, which stopped the train in the middle of the tunnel and prevented the doors from opening. The fire also burned through the main power cable, causing a blackout and loss of the communication system.
The skiers, engulfed in total darkness and rising plumes of toxic smoke, were aware of the fire but couldn’t get out. After several attempts, passengers on the back of the train broke a window. Twelve escaped and, counter intuitively but on the advice of a fellow passenger who was also a former firefighter, walked downward and deeper into the tunnel below the rising smoke.
Many of those still inside the train couldn’t escape the toxic fumes and soon lost consciousness. By the time the conductor finally unlocked the doors, the passengers who were able to, ran out but upward into the tunnel where only more toxic smoke and little oxygen awaited. In all, 155 people died in the disaster. The only survivors were the 12 skiers who, fittingly enough, traveled downhill.
An investigation confirmed that the electric heater ignited the hydraulic fluid, which then continued to combust long enough to create a dense, persistent cloud of deadly smoke. The train was eventually replaced by a gondola, but the tunnel remains closed to this day.
Had the hydraulic fluid been truly fire resistant, 155 more people probably would be alive today. But according to experts, more accidents like this are just waiting to happen-waiting until researchers can agree on a clear definition for fire resistance and until researchers develop comprehensive, uniform testing standards for ignitability and combustibility.
SMALL LEAKS, BIG CONSEQUENCES
Even though most oil-based hydraulic fluids have relatively high flash points and fire points, small leaks in a high-pressure system—such as that in the train—can create a fine spray capable of traveling a significant distance. Along the way, any ignition source will cause combustion of the spray envelope.
"Leaks can be found in all hydraulic applications, and their frequency is often dependent on the quality of the system maintenance," said STLE-member W. David Phillips, Principal of W. David Phillips & Associates and formerly with Great Lakes Chemical/Chemtura. "The frequency also will increase with system pressure, following the trend to smaller systems in the search for greater operating efficiency. Higher pressures also may mean any fluid escaping from the system as a spray or jet will travel further with increased risk of contact with an ignition source. The use of higher system and/or fluid operating temperatures compounds the problem."
BACKGROUND
One of the issues is the lack of a clear definition of "fire resistance," but experts also don't agree on the meaning of relevant terms. For example, what constitutes an ignition? Does it need to be a flame (the general consensus) or does heat not in the presence of a flame qualify?
Following are some generally accepted terms to help us work through the issue.
Ignitability. The amount of energy from an ignition source required to raise the temperature of the fluid to ignition point is usually referred to as the ignition temperature of the fluid. For the purposes of this article, an ignition source is an open flame.
Combustibility. Combustion (burning) is a vapor phase oxidation reaction resulting in the release of energy in the form of a flame. If a fluid is heated high enough, it will combust without an ignition source. For example, the standard Auto Ignition Temperature (AIT) test measures the temperature at which a material ignites without being exposed to an external spark or flame.
Flame propagation. Phillips uses this term to mean roughly what others refer to as combustion-fluid continues to burn when it is no longer in contact with the ignition source.
HISTORY
During World War II countless incidents of fire death related to large and small leaks of hydraulic fluid occurred; many involved aviators and many involved fiery tanks where soldiers either died trapped inside from the sheer heat of the fire or caught on fire as they tried to escape from the hatch. Just after the war, it happened that there were many similar incidents involving coal miners trapped in fiery mines. For example, in 1956 a hydraulic fluid fire in a Marcinelle, Belgium coal mine killed 267 people.
Military craft and coal mine fires spurred the U.S. government to team with private industry for research into less flammable and combustible fluids. They were looking for a fluid that would replace mineral hydraulic fluids without compromising performance and at a reasonable cost. One of the solutions was adding water to the fluid to act as an automatic extinguisher. Another was to create synthetic fluids without water capable of not only resisting but extinguishing flames. Some of the products that resulted are still being used, with slight moderations, today.
But none of those products yielded a perfect solution, so researchers are still continuing the quest, frustrated by what some call inadequate test procedures. The situation is also complicated by the fact that there is no common understanding of the term fire resistant.
DEFINITIONS
Fire resistant is a vague term whose meaning varies from discipline to discipline, from industry to industry and from material to material. To make the situation even more confusing, both fire resistant and fire proof are (wrongly) used as a synonym for incombustible and not ignitable. The reality is that combustion and ignition can create a fire independently of each other. A fluid can ignite without combusting; indeed this is one of the properties of water-based lubricants. But when the temperature is high enough, a fluid also can combust without igniting. Ideally the term should refer to a material that is neither ignitable nor combustible or at least the degree of ignitability and combustibility.
“A material can burn without being exposed to an ignition source,” said Eric Burkhardt, principal research chemist, ICL Industrial Products, Ardsley N.Y. “Its measured by the Auto Ignition Temperature Test. AIT is the temperature at which a material will ignite without being exposed to an external spark or flame.”
The building industry defines fire resistance as: The ability of a material, product, assembly or structure to fulfill, for a stated period of time, the required stability, integrity, thermal insulation and/or other expected duty specified in a standard fire-resistance test.
Choosing a fluid
Among the applications that benefit from fire-resistant fluids are aerospace, power generation (gas or steam turbines, aluminum and steel manufacturing) and foundry operations. These are settings that have open flames and/or surfaces hot enough to cause combustion without a flame. But any hydraulic fluid system that operates in high temperature equipment can benefit from a fire-resistant fluid.
When choosing a fire-resistant fluid, consider these four points:
1. The degree and type of fire resistance needed: Does the fluid need to reduce the chance of ignition, combustion or both?
2. Environmental compatibility (toxicity and biodegradability): Is the application in an environmentally sensitive area?
3. Feasibility of Retrofitting: It’s most often required for machinery using water-based fire-resistant fluids.
4. Expense: Some types of fire-resistant fluids are more expensive than others.
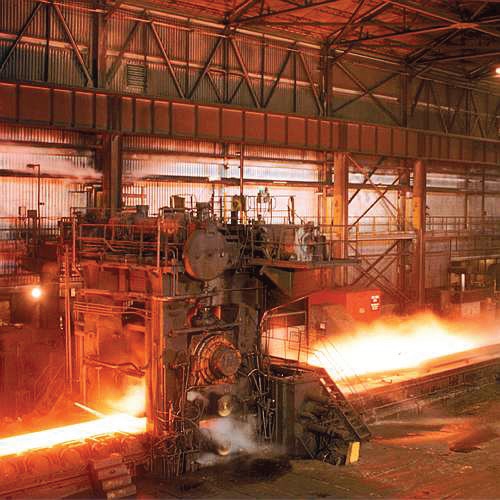
ASTM D 4175 defines a fire-resistant fluid as: Any liquid that is able to withstand fire or give protection from fire.
ISO 5598 defines a fire-resistance fluid as: fluid difficult to ignite which shows little tendency to propagate flame. This last definition does take both ignitability and combustibility into account, but the terms leave room for interpretation.
Burkhardt defines a fire-resistant lubricant as: difficult to ignite and, if ignited, will not support its own combustion (it's self-extinguishing). He points out that all fluids can be ignited if they're heated to a high enough temperature. So the real issue is whether the fluid will continue to burn once the ignition Source has been removed.
"The definition of a fire-resistant lubricant isn't uniform," Burkhardt explains. "Traditional mineral oils are used as a sort of baseline comparison and as the standard example of a fluid that is not considered to be fire resistant. Just because a fluid has better fire properties-flash and/or fire points-than a mineral oil doesn't mean that it should be referred to as being fire resistant."
The way it stands, all products with ignitability properties that surpass mineral oil can be termed fire resistant, even if they propagate flame, and lubricants with wide-ranging degrees of fire resistance can all be marketed as fire resistant.
STLE life-member Carl (Ed) Snyder, Jr., is a research materials engineer at the University of Dayton Research Institute and formerly was a materials engineer with the U.S. Air Force for 47 years. "The term itself is very ambiguous, not just regarding lubricants but for everything," Snyder says. "There is hardly anything that can be called nonflammable. That's the whole crux of the problem. It can never be an absolute term because it depends so much on the application. For example, in the Air Force it was defined as being able to sustain enemy air fire without bursting into flames."
Note, too, that the terms "flame propagating" and "combustible" are not the same.
Phillips puts it this way. "The term 'combustible' just means that the fluid will, under certain conditions, ignite," he says. "Flame propagation is the property that determines whether a fluid, on ignition, will continue to burn once it has moved away from the ignition source. If you like, flame propagation and ignitability are separate aspects of the combustion process."
None of this would be such a problem if the stakes weren't so high. Aside from the threat of injury and death, hydraulic fluid fires are responsible for enormous business losses every year. According to Factory Mutual Insurance, during a recent 15-year period, 17 large turbine building fires resulted in more than $400 million in damage. The average loss was $24 million, and the average downtime was more than 24 weeks. Some experts believe these figures are conservative since turbine fires, unless catastrophic, tend to go unreported.
Snyder, who retired from the U.S. Air Force Research Laboratory in 2009, said that before the Air Force started using the fire-resistant hydraulic fluid that he developed, noncombat hydraulic fires alone were costing about $20 million a year.
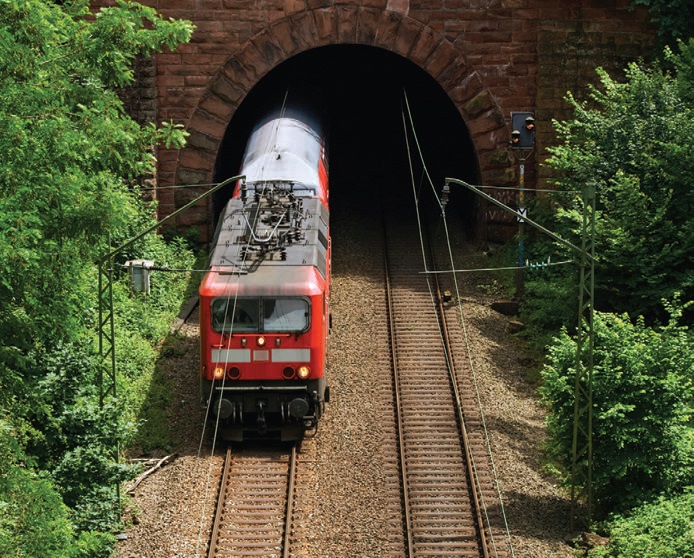
5 keys to assessing risk
Risk isn’t just about ignitability and combustibility but also potential consequences. As the train tragedy that killed 155 skiers illustrates, applications involving tunnels and mines are especially at risk. The five aspects to lubrication fire risk assessment are:
1. The likelihood that a release will occur.
2. The likely scale.
3. The likelihood that it will ignite.
4. The likelihood that it will combust.
5. The likely consequences in terms of safety, health and financial loss.
TYPES OF FIRE-RESISTANT LUBRICANTS
Although experts disagree on what constitutes a fire-resistant fluid, there are basically five types:
1. Water/glycols: mixtures of water and organic glycols. The water content in these fluids can range from 20% to 99%.
2. Phosphate esters: usually consisting of a central P-O core to which three (typically) aryl groups are attached. Aerospace phosphate esters have alkyl groups exclusively attached to the P-O core.
3. Polyol esters: typically C-18 range fatty acid esters of polyols such as trimethanol propane of neopentyl glycol.
4. Polyalkylene glycols (PAGs): moderately high-molecular-weight glycol oligomers with varying length alkyl groups.
5. Poly-alpha-olefins (PAOs): they have a chemical structure and properties similar to mineral oil but with greatly improved fire resistance.
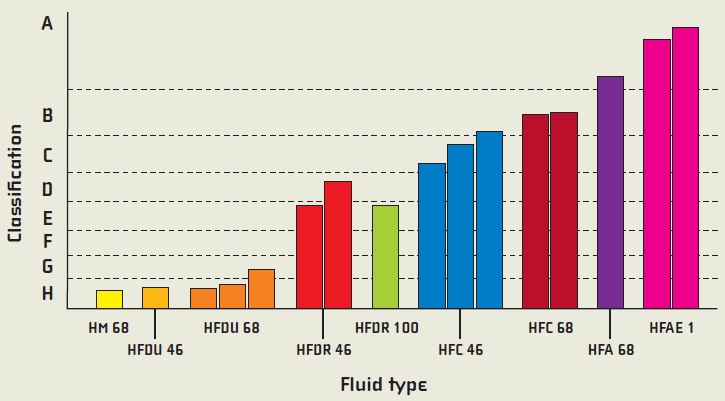
Results of the ISO/DIS 15029-2 Spray Test on a range of fire-resistant fluids.
The fire-resistant properties of high water content products usually are not measured because, as long as the water doesn’t evaporate, the water present in the fluids typically will suppress combustion. However, under conditions where contact with the ignition source is prolonged, the water will evaporate.
Water-based lubricants can have inferior performance and operating traits. They have much lower viscosity, film strength and lubricating properties than oil-based liquids. Machine components must be designed specifically for use with water-based lubricants. Then there’s the greater potential for freezing.
On the plus side, these fluids are attractive from both a cost and environmental perspective. They can be created from concentrate, and they’re less toxic than other fire-resistant fluids, although the issue of toxicity is debatable. Burkhardt says that none of the materials which are being used as hydraulic fluids are toxic.
Water/glycols, phosphate esters and polyol esters are non-aqueous HFDs. The property most relevant to fire resistance is their ease of ignition, but the behavior of the fluid if and when it combusts also is important. Phosphate esters, classified as HFDRs, are fire resistant because of their thermal/oxidative stability. Some of their vapor-phase reactions are heat absorbing, resulting in reduced flame propagation.
Polyol esters, polyalkylene glycols and poly-alpha-olefins, classified as HFDUs, have a relatively high ignition threshold (higher than mineral oil but not higher than HFDs) because of their lower volatility and higher molecular weight. They also may contain a polymeric thickener to increase the droplet size in a spray. While this makes the spray less ignitable and may improve the performance of new fluid, as the polymer shears down during use, the fire resistance begins to equate with a polymer-free fluid.
This means that, as a class, HFD fluids have a range of fire resistance that would be confusing to many users.
PAOs are less fire resistant than HFDs, but because they are so similar to mineral oils they can be used in most systems with little to no adjustment and cost only a little more. Another plus is that, unlike water-based lubricants, they degrade very little in use, and they can withstand low temperatures.
During Snyder's tenure, the U.S. Air Force, in conjunction with Mobil Oil Corp., developed fire-resistant PAOs. They were MIL-PRF-83282 and later MIL-PRF-87257, which can operate at temperatures as low as -54 C (-65 F). The fluids have been in use in almost all U.S. military aircraft since the mid-1980s and also in some regional commercial airliners.
"One of the keys to developing the fluid was that it also had to be compatible with our airplanes' hydraulic systems," Snyder says. "We wanted to avoid having to redesign the hydraulic system, particularly retrofitting thousands of seals, repainting the planes and replacing the wiring and tires to avoid incompatibility. All of these components were designed for mineral-based fluids. We figured it would cost $1 million to convert one plane to phosphate ester fluid compatibility. We wanted to develop a fire-resistant fluid that would replace mineral oil without the expense."
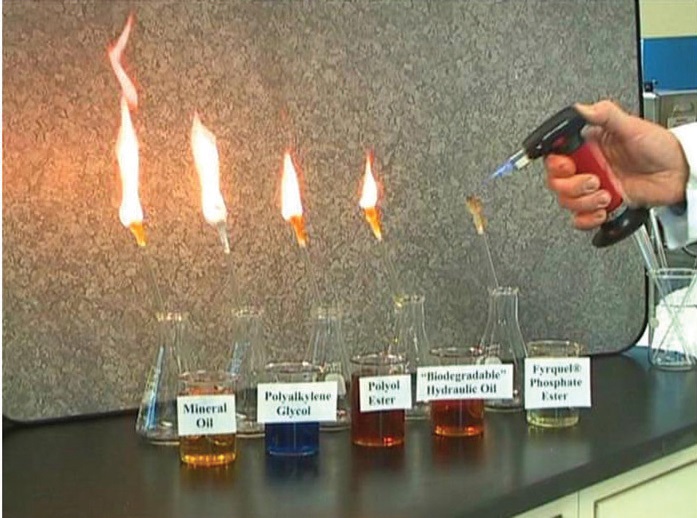
Non-phosphate ester fluids continue to burn on glass fiber wicks when ignited using a torch. Phosphate esters are not even ignited after several attempts. Photo courtesy of Eric Burkhardt.
FIRE-RESISTANT ADDITIVES?
Although researchers have tried, there are currently no additives other than droplet-sized modifiers that will make a flammable material more fire resistant.
"The only situation that would come close would be a water/glycol system in which there would be a defined minimum water content needed to impart fire resistance," Burkhardt says. "This would not be practical with other types of fluids because water is simply not miscible with most hydraulic fluid basestocks. The fire properties of a lubricant are determined by the fire properties of the basestock material, not additives."
TESTING
There are four fire tests that are most often quoted in U.S. product literature (1):
1. Flash Point
2. Fire Point
3. Auto Ignition Temperature
4. Heat of Combustion.
To prevent and limit fires, flash point, fire point and AIT numbers should be as high as possible and the heat-of-combustion number should be as low as possible. Burkhardt and Phillips agree that the most important property is whether the fluid has the ability to self-extinguish if ignited-whether it will combust.
But ignitability is important because, unless the fluid is extremely hot, it won't combust without an ignition source. Ignitability is the amount of energy from an ignition source required to raise the temperature of the lubricant to the point of ignition. Flame propagation is the amount of heat required (as the result of ignition) to maintain combustion, even when the fluid is no longer in contact with the igniter. This means a fire-resistant liquid should be difficult to ignite and quickly self-extinguish (2).
Snyder explains that the key to solving the Air Force's hydraulic fluid fires was reducing or eliminating ignition and, if ignited, combustion. "We knew once the fire got to the fuel system it would destroy the airplane," he says.
Fire-resistant tests are designed to be repeatable in a laboratory and don't necessarily mimic or predict real-world performance. Many fluids that are fire resistant when they are new will degrade fairly rapidly in use, becoming significantly more flammable.
Standard tests that are conducted on fluids to evaluate their fire properties include:
• Flash Point
• Fire Point
• AIT (ability to combust without ignition)
• Heat of Combustion
• Spray Ignition
• Soaked Cube
• Hot Manifold
• Wick
• Compression Ignition.
"One of the things that really bothers me is the AIT test," says Snyder. "If a temperature rise occurs, it's considered an ignition. I can't think of any place on an airplane where you are going to have the same static airflow conditions that you have in a lab. I think that test is way overrated. It's not designed to replicate actual conditions."
In the past, Factory Mutual (FM) used to conduct a simple pass/fail flammability test where a flame was passed through an aerosol cloud of test fluid. Some formulators added VI polymers to their fluid to create a larger aerosol droplet size. The larger droplet size resulted in lower surface area and, therefore, greater fire resistance. It was an easy way to pass the test and get FM approval. The problem is that in real-world use, the polymer undergoes shear and fire resistance is lost. Realizing this FM altered its test so that now the entire sample is burned and the heat release is measured, resulting in a Spray Flammability Parameter that must fall within FM limits.
Other manufacturers who represent their fluids as fire resistant promote a high flash point along with FM approval but ignore combustibility. Those same fluids may continue to burn even after the ignition source is removed from the fluid.
In addition to Factory Mutual, there are a number of fire-resistance testing entities. ISO 15029, ISO 20823 and ISO 14935 tests are the most widely specified. Fluids with a water content greater than 80% aren't routinely tested for fire resistance.
Factory Mutual’s real-world tests
In 2004 Factory Mutual Insurance designed a turbine mock-up complete with a turbine pedestal and lube-oil system in its West Glocester, R.I., Large Burn Laboratory.
The turbine design was sturdy enough to withstand extensive testing and later served as a demonstration unit for visitors. It was fabricated from steel, instead of the standard concrete in order to make it stronger and more portable. The design included:
• High and intermediate pressure turbine housings
• A foundation pedestal
• A grated walkway to simulate an open-floor design
• A lube oil tank and pumping unit
• A dike around the lube oil tank.
One of the main goals was duplicating a real-world environment. The representative test fire scenarios, based on actual fire loss experiences and field observations, included spray fires, pool fires and three-dimensional spill fires.
During tests, lube oil was pumped at rates up to 20 gallons per minute, a relatively low flow rate considering that a very large gas turbine could pump oil at 800 gallons per minute. But even at the low flow rate, researchers were surprised by the intensity of some of the fires. Some spray fires generated heat-release rate bursts of more than 40 mw, creating ceiling temperatures close to 816 C (1,500 F), which can cause steel deformation and roof failure.
The entire test facility was involved in the project for more than a month, with the completed tests yielding the following conclusions:
• Spray fires and three-dimensional spill fires cannot be extinguished by sprinklers alone.
• Oil flow must be cut off as quickly as possible.
• Local protection is required to control spray and three-dimensional spill fires.
• Pool fires alone can be extinguished by adequate local fire protection.
When the tests were completed, Factory Mutual conducted demonstrations for clients, risk management groups and industry experts.
ISO 15029
This expensive ranking test determines spray ignition characteristics using heat release as a measure of the ease of igniting and stabilizing the spray flame. ISO 15029:
• Can be adapted to measure heat release rates or oxygen depletion. It also can measure other combustion parameters such as smoke production.
• Does not measure radiating heat and doesn't give a total measure of heat output.
• Uses volume flow rates and doesn't take the significant density variation among fluids into consideration.
ISO 20823
This ranking test determines flammability characteristics of fluids in contact with hot surfaces, primarily assessing ignitability but also combustibility. Issues to consider:
• This is a relatively inexpensive test, typically using a manifold or tube, comparing most fluid types capable of igniting up to a temperature of about 800 C (1,427 F).
• ISO 20823 measures the propensity to propagate flame once the fluid loses contact with the ignition source.
• Since contact time is a key ignition factor for hot surface fires, the ignition temperatures wouldn't be the same for tests carried out on a rounded (tube, manifold) vs. a flat surface, although this would not affect ranking.
ISO-14935
This pass/fail test determines the wick flame persistence, which determines combustibility. ISO 14935:
• Is another relatively low-cost test capable of testing and comparing most fluids, except those with very high water contents.
• Doesn't yield precise data since it's pass/fail.
• Doesn't measure the relative tendency of the flame to propagate.
Because there is more than one testing entity, there is more than one set of specifications and standards. This opens the door for confusion. For example, while the ISO 15029-2 spray test can rank fluid performance, a similar (not identical) FM test often produces conflicting data.
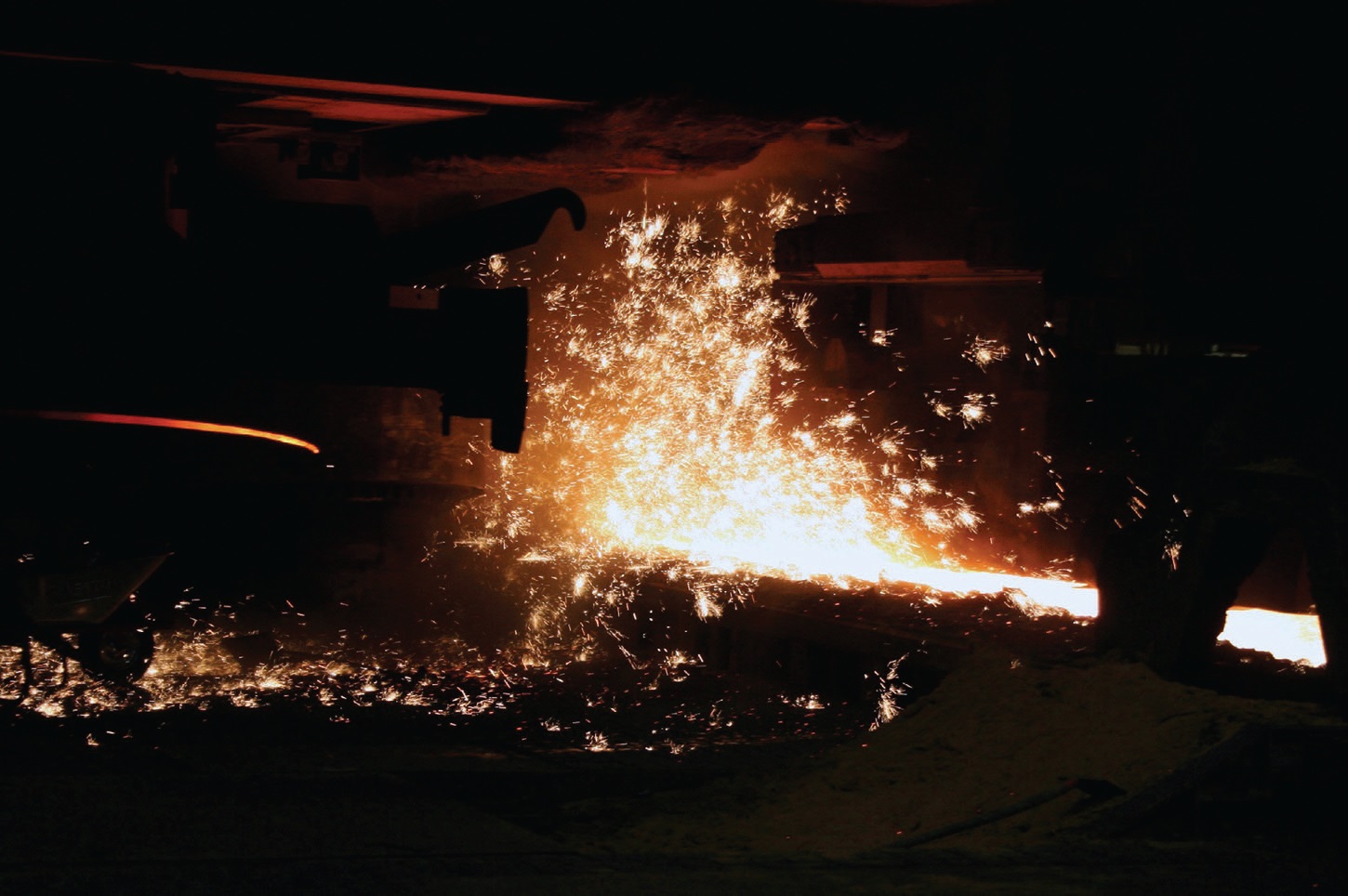
Money is wasted and lives are lost because the wrong fluid is used in the wrong application.
RESOLVING TERMINOLOGY
Phillips is concerned that the conflict between test results and standards may lead to users selecting a lubricant that doesn't have the level of fire resistance the application requires. He seriously questions the continued use of the term fire resistant to describe a broad range of fire-prevention levels and suggests segmenting fire resistance into three classes. While an improvement, Phillips acknowledges that the following definitions require further debate:
1. Fire resistant: extremely difficult or impossible to ignite and not capable of propagating flame. This definition would mainly cover fluids with water content greater than 80% (ISO classes HFAE and HFAS).
2. Fire retardant: fluids that are difficult to ignite and do not significantly propagate flame. This would cover ISO classes HFB, HFC, HFDR (phosphate esters), and HFAE/ HFAS fluids with water content less than 80%.
3. Less flammable: fluids which, under standard test conditions, are more difficult to ignite than mineral oil but readily propagate flame. This would cover HFDU fluids (polyol esters, PAOs, PAGs).
If those definitions are adopted, Phillips said it would be fairly straightforward to broadcast the changes.
"The first step would be to get agreement within ISO and ASTM on new definitions," Phillips explains. "Once this has been achieved, it would be necessary to obtain agreement on the tests to be used to assess fire behavior and the limits corresponding to the different classes. It would then be possible to publicize the changes and to start updating the use of these terms in standards and the literature. It would be the responsibility of the fluid manufacturers and suppliers to ensure the description of their products complied with the changes."
In all this, a clear legal definition for fire resistance is glaringly absent.
"To my knowledge, there is no legal definition of 'fire resistance,'" Burkhardt says. "Testing is now done based on definitions put forth by industry groups. Organizations such as the ASTM design tests in an attempt to model real-life situations found in industry.
"This is not something that is easily legislated," Burkhardt adds. "My definition, that a fire-resistant fluid should not only be difficult to ignite but, if ignited, will not support its own combustion, is derived from common sense. I would say that there are not degrees of fire resistance, but there are degrees of ignition resistance. For any given fire test, there will be a temperature value at which a given test fluid can be ignited."
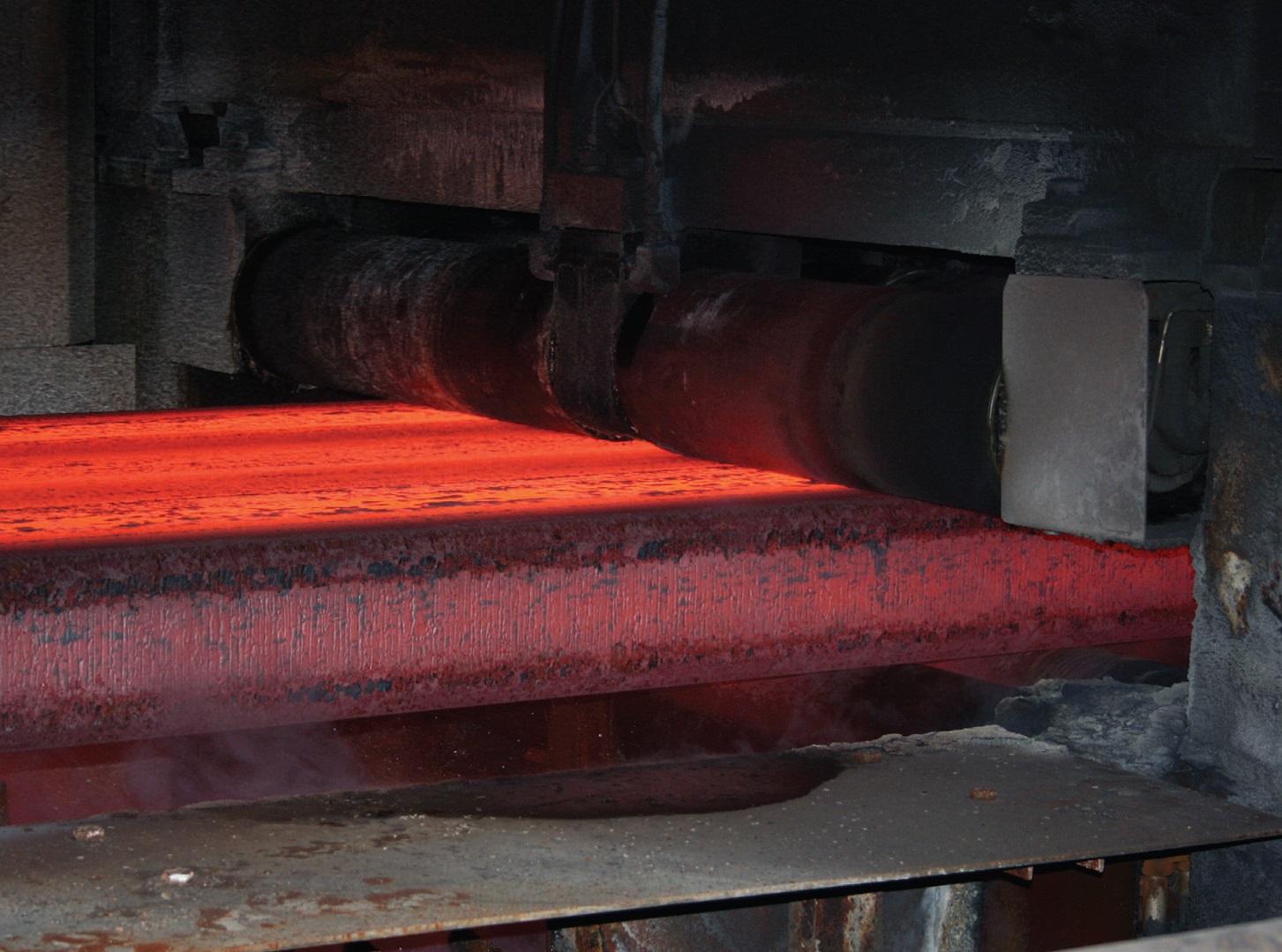
Experts agree that there needs to be a new definition as to what constitutes a fire-resistant fluid, specifically clarification and recognition of ignition and fire propagation.
RESOLVING TESTS
According to our experts interviewed for this article, to better match the level of fire resistance to the application, they agree that laboratory tests need to be improved in the following ways:
• They need to simulate real-world applications. Although it would be impossible to duplicate every possible application, certainly the most common types should be attempted.
• They need to routinely test fluids that have already degraded to a specified level or artificially degrade the fluids in the lab before testing.
• Laboratories need to agree on a common set of tests and standards.
"Entities such as the ASTM put a lot of effort into the development of what are considered to be standardized tests," Burkhardt says. "There is collaborative effort involved with representatives from industry in the development of specific tests. EPRI (Electric Power Research Institute) and some of its clients recently conducted an evaluation of a number of hydraulic fluids with respect to fire resistance using the Wick Test, Hot Channel Test, Spray Flame Test and Soaked Cube Fire Test. This report has not yet been formally released to the public."
Testing degraded fluids would be complex for a number of reasons, most notably the difficulty in ranking the level of degradation.
"Testing degraded fluids is quite possible and has been done in some instances," Phillips says. "However, it is not cheap, and there are a limited number of labs currently carrying out such tests.
"Unfortunately, I think the main reason why these tests are not often used on fluid from service is that there is rarely a limit on the fire-resistance behavior of used fluid, and any limit would vary depending on the application," Phillips adds. "It is also quite possible that the fluid would have to be replaced for other reasons-for example, an increase in TAN—before there is any significant reduction in fire resistance and these other parameters are probably easier to monitor."
Burkhardt says, "I think that for the most part they have done a pretty good job of simulating real-world applications, but fire modeling is very important here. Fire scenarios tend to be horizontal; for example pool fires. In reality, fires in industrial settings are typically 'down/up.' Due to the size of the installations-power plants are an example-that use hydraulic fluids, a leak can often travel down one or two stories, be ignited and the flames rise up to where the leak is actually occurring, thus setting off a larger fire."
THE BOTTOM LINE
Experts agree that there needs to be a new definition as to what constitutes a fire-resistant fluid, specifically clarification and recognition of ignition and fire propagation.
Of that $20 million a year the military was losing on aircraft damaged or destroyed by hydraulic fluid fires, Snyder says: "After we were able to develop and implement a fire-resistant hydraulic fluid, the cost of non-combat hydraulic fluid fires dropped to $1 million a year. The fire-resistant fluid we developed would ignite under some circumstances but wouldn't spread. Now that we have this fire-resistant fluid in place, if we get a wheel well fire, it will cause a little damage but we won't lose the aircraft."
Fire-resistant fluids save not only money but countless lives every year. However, even without statistics, it's reasonable to assume that money is wasted and casualties occur because the wrong fluid is used in the wrong application. What could present a stronger impetus for resolving some of these issues as quickly as possible?
FOR MORE INFORMATION
Factory Mutual's new Fire Technology Lab: click here.
Link to video - ICL Industrial Products' demonstration of how readily some hydraulic fluids will continue to burn after removal of an ignition source. www.fyrquel.com.
REFERENCES
1. In Europe and elsewhere, other tests are now replacing these methods.
2. W.D. Phillips, PowerPoint presentation from the STLE 2010 Annual Meeting & Exhibition, May16-20, Las Vegas, Nev. – ‘Fire Resistant’ Hydraulic Fluids: An Accurate Description?
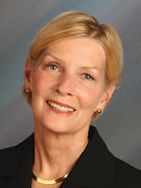
Jean Van Rensselar heads her own communication/public relations firm, Smart PR Communications, in Naperville, Ill. You can reach her at jean@smartprcommunications.com.