Real-world oil analysis: Part IV
Jack Poley | TLT On Condition Monitoring July 2010
Do it right or don’t do it.
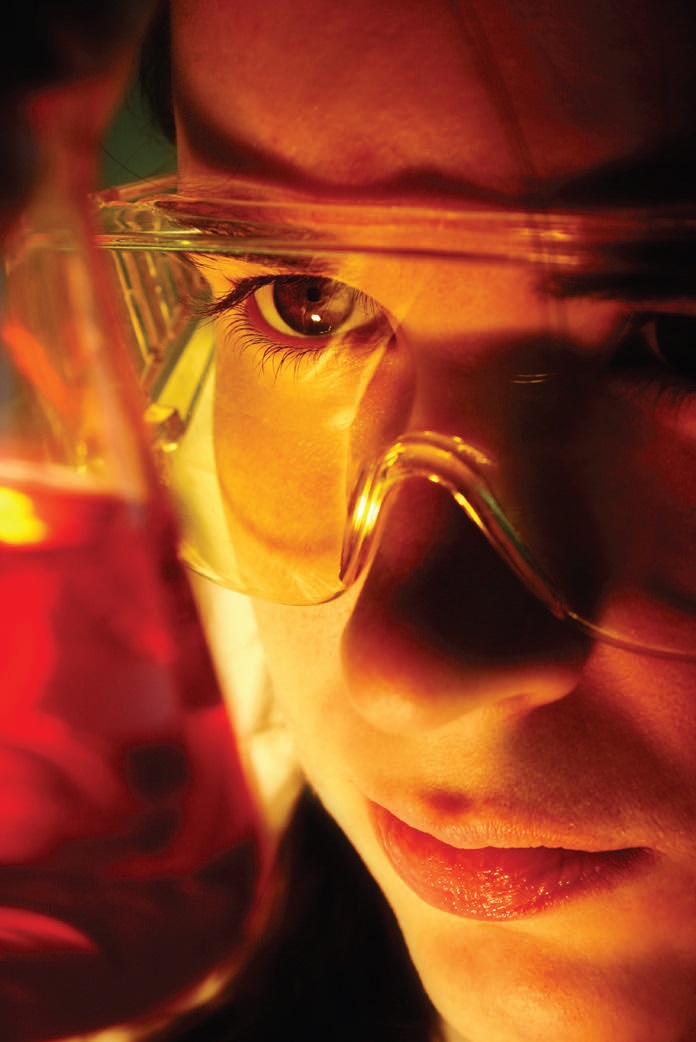
There is nothing more frustrating than oil analysis programs where failures are missed because indicative tests were missing at evaluation time.
www.canstockphoto.com
Lately I’ve seen numerous examples where established programs are in full swing but test packages have been minimized, resulting in a lost diagnosis opportunity. In a couple of these cases the evaluation hinged on the need for useful test data that weren’t available because the test was eschewed for the sake of budget or because of ignorance. Penny wise…and so forth.
This prompts me to revisit the factors one should consider when selecting a suite of tests to perform on a given component. There are different ways to approach this, certainly, but one of the very best ways is to consider what can go wrong with a particular component, then ask: What test or tests will give me the earliest and most dependable warning that problem ‘X’ will occur?
Some basic, if obvious, points to consider:
1.
One fixed suite of tests is not going to cover a variety of components at the same level of effectiveness. One size does not fit all.
a.
Corollary: Some tests are excellent for finding problems in specific components but ineffective or marginal otherwise.
b.
Corollary: Various instruments that determine a specific property are just that—varying in terms of detection ability, quantitative range, interference, repeatability, precision, etc. The more important the result is for condition assessment, the more important it is to select the most effective method.
2.
The decision to sample a component must be based on the production and revenue scheme (remember, it’s all about money). Accordingly there’s no economically valid reason to trim a testing package to save a few dollars if loss of use of this asset could put one out of business for any appreciable time interval. Most assets meet this test.
3.
Don’t assume the lab knows the best tests to apply for
your operation. You may have special or unique needs and conditions that people unfamiliar with your operation would never anticipate, let alone inquire about. This is the case in many operations, particularly where truly varied machinery exists or where there are distinct logistical and functional differences in a multifaceted operation or where there are environmental conditions that someone not familiar with the operation would never suspect or consider.
a.
Corollary: Before you specify or agree to a test package, get a second opinion, perhaps from a qualified consultant, perhaps from someone you know who is involved in a similar operation that is applying oil analysis successfully.
b.
Corollary: There is nothing more frustrating than oil analysis programs where failures are missed because indicative tests were missing at evaluation time.
c.
Corollary: Failure modes can develop that are not detectable via oil analysis or that would have needed an exceptional test not readily discernible based on available evidence. It is, however, egregious to incur failure modes or prefailure trauma for lack of employing industry-typical tests. That’s human error in the oil analysis program.
Getting back to what can go wrong, let’s look at a typical small-medium-speed four-cycle diesel engine. Pick a manufacturer. Diesel engines probably have more moving parts than almost any component type, so there’s a lot going on.
Diesels also have complex chemistry systems in play, all aimed at the lubricant:
•
Lubricants must not only lubricate but also absorb heat from combustion, including piston cooling, controlling fuel soot, providing antiwear protection against several wear modes, holding up under reduced viscosity from fuel dilution, etc.
•
Most diesels are liquid cooled, adding another layer of complexity as well as the risk that the coolant may seep into the lubricant (or vice versa), resulting in impaired lubricity, general trauma and possible engine seizure.
•
Fuel quality, while not an issue in North America these days, can be a huge factor in locales where it is not good.
With all the concerns and possibilities, it turns out we need to apply quite a variety of testing to arrive at a suitable, technically sufficient package for diesel engines, mundane as some think them to be:
•
Wear Metals
o
Fe (iron), Al (aluminum), Cu (copper), Pb (lead) – these are the Big Four of wear metals, those that tend to dominate when wear occurs, because they comprise the vast majority of parts within the component.
o
Other wear metals are ancillary but may perform the valuable function of isolating a part, e.g., a Babbitt bearing will yield Pb and Sn (tin), maybe Sb (antimony) when wearing abnormally.
•
Contaminant Metals
o
Si (silicon), often indicative of abrasives or dirt, while also an oil additive as a foam inhibitor, is an essential measurement.
o
Coolant additive metals are various: Si (out of favor but still around at times), Na (sodium), K (potassium), B (boron) are all possible indicators when coolant is leaking into the lube sump.
o
Environmental considerations such as mining materials in the air must be considered. Most of the time Si would be the principal measurement for guarding air intake systems. What if, however, the engine is operating at a Ti (titanium) mine or a Cu mine? Wouldn’t either of those elements be a potential indicator of air intake filtration compromise (or vents in the equipment’s other compartments)? They certainly would.
•
Additive Metals
o
Si has already been mentioned, but we have a host of additive metals possibilities. Most common are Mg (magnesium), Ca (calcium), P (phosphorous) and Zn (zinc), but Mo (molybdenum) and Ba (barium) are not uncommon. What’s the point of testing these? To be sure what’s purported to be in the lube is in it and to detect intrusive metals, indicative of contamination (wrong oil) or formulation change.
o
B, Na and K might also be additives on the lube side, though less frequently than those mentioned previously.
o
There are always specialty additive possibilities. The challenge here is to become aware that they exist in order to test for them.
•
Other Contaminants
o
Fuel dilution (leaks or delivery impairment)
o
Fuel soot (combustion, timing, duty cycle)
o
Coolant (glycol)
o
Water (condensation/bad sample, catastrophic coolant leak).
•
Degradation (lubricity and other lube performance impairment)
o
Acid number (is this necessary, or even useful?)
o
Base number (is this necessary, or even useful?)
o
Oxidation (don’t even think about—it’s necessary).
We’ve set the table—next column we’ll discuss this in depth and pick our testing suite.
Jack Poley is managing partner of Condition Monitoring International (CMI), Miami, consultants in fluid analysis. You can reach him at jpoley@conditionmonitoringintl.com.
For more information about CMI, visit www.conditionmonitoringintl.com.