Executing an effective sump conversion
Mike Johnson | TLT Best Practices June 2010
The cost and effort required to overcoming deposit problems from degraded oil goes well beyond a simple fluid replacement.
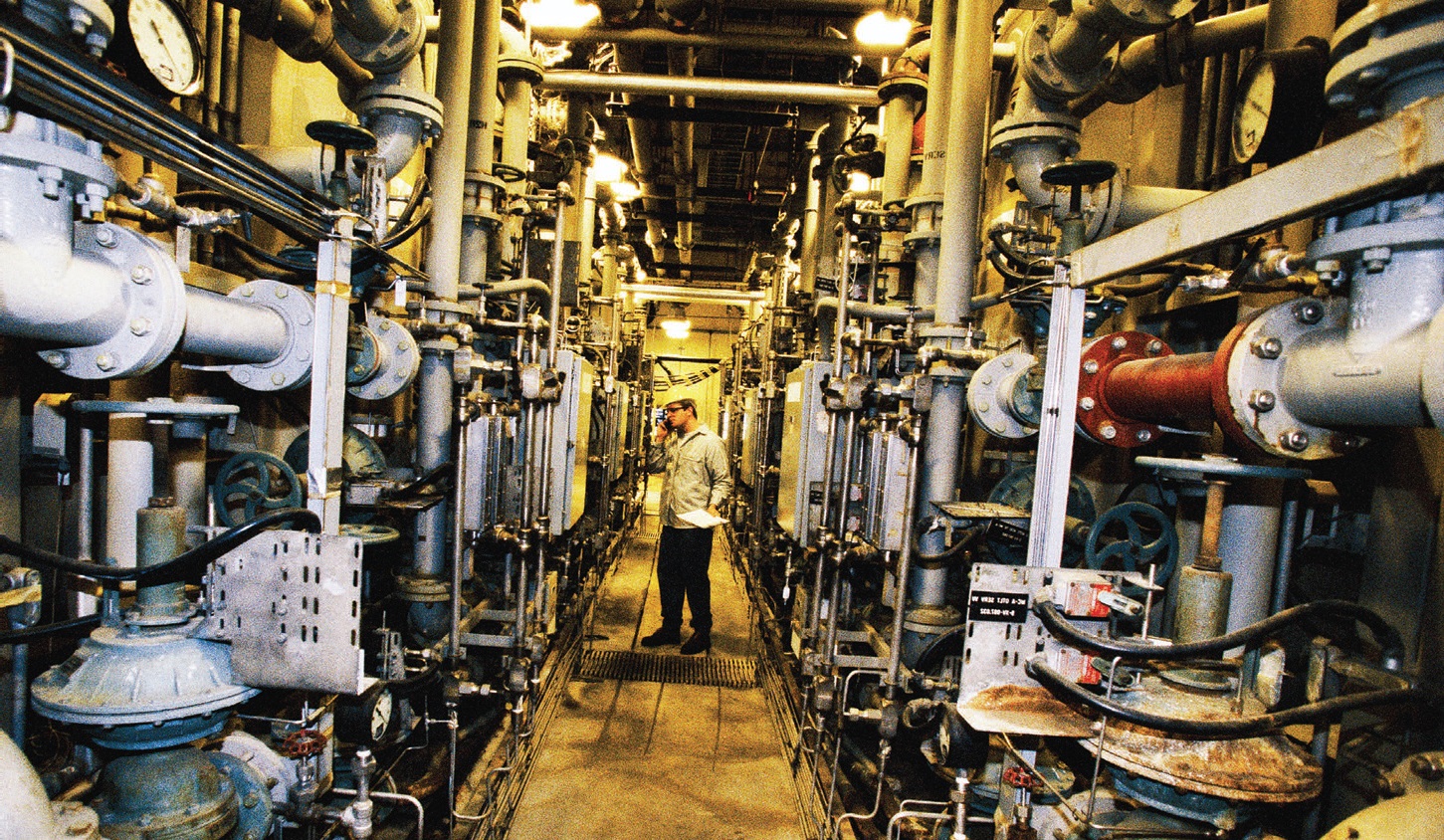
KEY CONCEPTS
•
Aging lubricants produce progressively higher levels of sludge, insoluble polymers, carbon deposits and other insoluble oxidation byproducts.
•
The physical flushing process depends on the lift and drag forces from turbulent movement of the fluid to dislodge soil from the laminar sublayer of stagnant fluid.
•
Chemical flushing incorporates the use of cleaners, solvent blends and oil-soluble detergents to gradually remove crusted or layered carbon residues.
For anything less than ideal circumstances, machines impose tremendous stress on the lubricants designed to protect the loaded surfaces. Through their routine operation, machine components can cause shear stress and heating. Often components rupture the protective fi lm and generate wear debris. Machines churn in or suck in air that creates bubbles and, within pressurized flow circuits, superheat and vaporize the lubricant. Human actions can complicate the picture as well, as routine repairs often introduce additional process and atmospheric contaminants. The act of opening the system to affect component replacement, and the components themselves, introduce contaminants. The routine work of machine lubrication, both oil and grease, offers numerous opportunities to further corrupt the sump with atmospheric solids, moisture, process chemicals and other lubricants.
As a consequence of these realities, at the end of the lubricant’s useful life, there is often an increased level of residue and decay that, like an abscessed tooth, must be removed to prevent long-term damage and destruction to enable the new lubricant to achieve its expected life cycle.
This article will review the mechanisms of degradation and discuss methods and equipment useful to flush out debris and decay in order to assure a healthy, fresh start with the new lubricant charge.
LUBRICANT DEGRADATION
Lubricant degradation is a complex process. As lubricants age, they produce progressively higher levels of sludge, insoluble polymers, carbon deposits and other insoluble oxidation byproducts. These waste materials are caused by chemical reactions with air, water, process contaminants and other chemicals that find their way to the sump. These reactions fall under an umbrella called oxidation. Oxidation is a general term used to describe a complex series of chemical reactions, chemical changes and a formulation of new molecular species within a sump. Initially, oxidation was characterized as a chemical reaction just involving oxygen. The definition was eventually expanded to include any reactions involving electron transfer (
1).
Oxidation is a complex process but in general terms follows a three-stage series of chemical changes, characterized as:
Stage 1. Initiation
Stage 2. Propagation
Stage 3. Termination.
Stage 1 – Initiation. Initiation involves the formation of a reactive molecule called a free radical, which is an atom or molecule fragment with one or more unpaired electrons. The biggest contributor of free radicals is oxygen itself. Contaminants that are rich with oxygen (air, water) feed oxygen to the system.
UV radiation (sunlight), wear metals, extreme temperatures induced by compression of trapped air, extreme temperatures induced by metallic contact and wear, existing varnish and sludge within the system and flow electrification (electrical arc-discharge) in high-flow circulation systems all promote the formation of free radicals. Free radicals are highly reactive and short-lived. They quickly combine with hydrocarbon components to form alkyl radicals and hydroperoxi-radicals.
Stage 2 – Propagation. Propagation occurs when hydroperoxi- (peroxide) radicals react with the base oil or additives to propagate into oxygenated hydrocarbons, including alcohol, acids and sludge (
2). When high temperatures exist, the peroxide radicals split and sustain the chemical reaction. If iron and copper (wear) metals are present, peroxides can catalytically split to continue the reaction, even if the sump temperatures are low.
The propagation can become autocatalytic with the chemical reactions themselves, providing the feedstock to start the next cycle.
Stage 3 – Termination. Termination occurs when the designated oxidation inhibitor breaks the reaction and stops the cycle. There are several types of oxidation inhibitors used in lubricants, including:
•
Chain breaking-electron donor
•
Chain breaking-electron acceptor
•
UV absorber
•
Peroxide decomposer.
Antioxidants vary between brand and product types. Typically, R&O oils (turbine and compressor oils) use either phenolic and/or aromatic amine type inhibitors. These are characterized as chain-breaking inhibitors because they absorb reactive radicals to form a stable radical. Since the antioxidants can react more quickly with the radical than the base oil itself can, the reaction chain is broken (
3).
AW and EP oil formulations depend on phosphorus and sulfur compounds (sulfides, disulfides, polysulfides, phenothiazines, dithiocarbamates, thiadiazoles, thiarams) to inhibit oxidation. These agents act to decompose unstable alkyl hydroperoxides into a more stable alcohol form. Sulfur-based antioxidant behavior is complex, with potential to produce sulfurous byproducts, acid and sulfur dioxides. When produced, sulfuric acid is a powerful catalyst for lubricant polymerization and degradation (
4). Aromatic and sulfur-containing compounds (peroxide decomposers) also tend to encourage formation of deposits.
These deposits accumulate in the sump, corrupt the existing lubricant and sour the system. If these, and the previously mentioned degradation byproducts, are allowed to remain in the sump at the time of the oil change, the highly reactive residue restarts the entire degradation process as soon as the new lubricant is put into service (
5).
The end-user should never be surprised by the loss of oxidation resistance and precipitation of oxidation byproducts in a sump. Tracking the depletion of the various types of oxidants (pheolic, aminic, sulfur-phosphorus) can be routinely and inexpensively performed with Linear Sweep Voltammetry (aka RULER), and with Fourier Transform Infrared (FTIR) Spectroscopy. Most commercial labs provide these test methods for the asking, so looking for evidence of depletion of these key ingredients and making the proper steps to protect the sump from deposits is not difficult.
SYSTEM HEALTH
Throughout the life of machines there are instances when a thorough internal cleansing is appropriate. New and recently rebuilt machines that depend on extensive transport lines to deliver lubricant from and return lubricant to the sump are prime candidates for system cleaning. This effort is needed to remove construction and assemble contaminants prior to commissioning.
Lubrication systems (hydraulic reservoirs, turbine generators, air compressors, gearboxes, bearing housings, paper machine oil reservoirs, etc.) eventually need a thorough flushing in addition to the routinely scheduled drain and fill. This is certainly true when switching from one brand or product type to another where the initial sump conditions are corrupted. Evidence of a need for a systematic cleansing, prior to conversion to a new product or simple replacement with the same product, is seen during the oil drain activity. Since drain plugs reside at low areas of the sumps, much of the debris accumulates and is noticed with the first flow of waste oil from the system.
Simply draining and refilling the simple sump does not remove all of the objectionable material from the sump. There are several tell-tale signs that point out the need to flush. As shown in Figure 1, material evidence in the form of sludge, rust, moisture, wear metals, gel or other viscous residue, noted at the initial moment that the drain begins, should confirm to the technician that a flush is in order. Operational changes, such as overheating of the sump, gross liquid or solid contamination and development of severe wear patterns, all point to a need to thoroughly inspect and decide.
Figure 1. Sludge appearing at the bottom of the sump is a clear indicator of the need to flush. (Courtesy of Fluitec International, LLC).
Regrettably, machine owners often wait too long to respond to a failing sump condition, particularly with high-volume circulating systems like those supporting gas and steam turbines, paper dryer systems and turbocompressors. The cost and effort required to overcome problems with deposits from degraded oil is well beyond the simple cost of fluid replacement, and at the end of the exercise the fluid may still have to be replaced. Clearly, an ounce of prevention is more palatable than the pound of cure.
PHYSICAL AND CHEMICAL FLUSHING
Material floating freely and attached to contact or non-contact machine surfaces is generically classified as soil. Soil may be composed of material that is generated internally such as varnish, carbon deposits, chemical residues, sludge, rust, etc., or may be composed of material that is generated externally such as scale, welding slag, rust, machining swarf and metal debris. Soils may be physically or chemically removed.
Physical flushing. This is a fluid circulation process designed to remove water, chemical contaminants, air and particulate matter, accomplished through the recirculation of a clean(er) fluid at a high velocity to achieve a turbulent flow. The turbulence serves to:
(a.) Mechanically dislodge, lift and entrain particulate debris.
(b.) Suspend and transport particles.
(c.) Absorb air, chemical products and water from the system.
(d.) Release the contaminants to a filter.
The physical flushing process depends on the lift and drag forces from turbulent movement of the fluid to dislodge soil from the laminar sublayer of stagnant fluid next to the tank or pipe internal wall. Obviously, the fluid must be turbulent, which is dictated by the dimensionless Reynolds number value. The Reynolds number (Re) is defined by the ratio of dynamic pressure (ρ u
2) and shearing stress (μ u / L), as follows:
Re = (ρ u
2) / (μ u / L)
where:
•
Re = Reynolds number (non-dimensional)
•
ρ = Fluid density, (kg/m
3, lb
m/ft
3)
•
u = Fluid velocity (m/s, ft/s)
•
μ = Dynamic viscosity, (Ns/m
2, lb
m/s ft)
•
L = Characteristic length (m, ft)
•
v = Kinematic viscosity, (m
2/s, ft
2/s)
Hydraulic and circulation system designers strive to create laminar flow conditions for normal operation. For the system parameters noted above, a Reynolds number greater than 4,000 suggests that the system will produce turbulent flow (flow instabilities, eddies, vortices) and less than 2,000 represents laminar flow. Physical flushing is also called power flushing, which is associated with commissioning of large volume reservoirs (turbines, compressors, extensive circulating systems) following build or rebuild.
Power flushing requires the operator to analyze the system, determine where flow restrictions may exist, use flow connectors to circumvent the restrictions and then charge the oil tank and circulate oil under very high flow conditions. For commissioning of new turbines, this activity may take several days or weeks in order to remove solid contaminants to an acceptable level. Service companies can be hired to perform this specialized activity. Cost is dependent on the scope of the task at hand.
The same approach can be applied to non-circulating sumps through the use of a directed stream of high-pressure filtered oil to physically force debris out of dead zones, off of surfaces and toward the drain portal. To accomplish this purpose, a portable filter system with controllable flow is configured with a nozzle to allow the operator to hose down the inside surfaces. If the sump itself is being cleaned, then a second pump and container is needed to extract the wash-oil from the sump and transfer it to a holding tank from which the filter system will siphon and return it under pressure to the right location.
Chemical flushing. This process incorporates the use of organic (hydrocarbon-based) halogenated, non-halogenated cleaners, solvent blends and oil-soluble detergents to gradually remove crusted or layered carbon residues. Organic solvents tend to be blends of aliphatic and aromatic hydrocarbons designed to dissolve soil as opposed to suspending/emulsifying soil. The deposits may be any of a variety of oil chemistries and, therefore, some attention to the chemical nature of the deposit is warranted. Some caution should be exercised when selecting the system cleaner to assure that the cleaner doesn’t attack system polymers (seals, o-rings, coatings).
System cleaners are added to the in-place fluid and are left to work in the system for a period of time (dictated by the cleaner type, sump volume, extent of deposits, maintainable temperature). At the end of the cycle, the in-service oil is discarded. Since chemical cleaning depends on chemical reactions between the residues and the select cleaner, this process requires patience. The cleaner supplier should propose a dilution rate and time in circulation to accomplish the intended purpose. Since the cleaner initiates a chemical reaction with the residue, maintenance of an appropriate system temperature is important. The warmer the system temperature, the shorter the duration, and the better the results of the flush.
Once the prescribed conditions are fulfilled, the lubricant is drained hot and disposed. As much as possible the stagnant areas in the sump should be opened and drained, leaving little of the cleaner-lubricant mixture in the system. Following a complete drain, the system is then charged with a petroleum-flushing fluid that is compatible with the intended system lubricant, and the system is cycled under turbulent conditions for a period of time to wash down any residual cleaner-lubricant mixture. Once again, the system is completely drained, including the stagnant locations. Following this, the system reservoir and piping may yet have to be vigorously scrubbed in order to remove resilient deposits.
After the system fluid is replaced, an additional period of circulation and aggressive filtration is appropriate. With both methods, it is likely to disturb stagnant contaminants and set them loose in the system. To avoid harming the sensitive control portions of the system and/or mechanical components, a high-performance filtering system should be introduced for a period of time during the process to remove contaminants. The approach would be useful in other circulation systems, as well.
During the evaluation of the system to determine if a flush is needed, if it is apparent that the system lubricant is still serviceable, then a long-term varnish-removal approach, using either ion exchange resin technology or electrostatic filtration, may be a better option. This approach is passive and slow but protects the investment in the system fluid and would be more closely associated with filtration and condition control than flushing.
The American Society of Testing and Materials offers a guideline, ASTM D6439-05, for cleaning, flushing and purification of steam, gas and hydroelectric turbine lubrication systems. The principles contained therein could be applied to non-circulating systems, as well.
CONCLUSIONS
Prior to a sump conversion, the equipment owner should observe for tell-tale indicators of a need to clean the sump thoroughly. The flushing process may be perceived to be an expensive, complicated and time-consuming extra task for an oil change. However, some conditions justify the effort. Highly contaminated reservoirs on critical systems warrant extra attention to assure the full potential of the new fluid.
Flushing should be required for new and rebuilt equipment prior to commissioning. Physical flushing methods incorporate high system flows and turbulent action of the fluid in the system to physically dislodge and remove contaminants and sediments.
Chemical flushing methods introduce agents that dissolve deposits during operation using the system’s resident fluid. The system cleaner-lubricant mixture is removed, and then a fresh oil flush is used to completely wash out any remnant of the cleaner prior to commissioning activities. System flushing is a costly, specialized activity that should be considered for outsourcing, if possible.
REFERENCES
1.
Wooten, D. “The Lubricant’s Nemesis – Oxidation,”
Practicing Oil Analysis, March, 2007.
2.
Ameye, J. and Kauffman, R.E., “Antioxidant Analysis for Monitoring Remaining Useful Life of Turbine Fluids,”
Turbine Lubrication in the 21st Century, ASTM STP 1407, Edited by W.R. Herguth and T.M. Warne, Eds.
3.
Ibid.
4.
Gatto, V.J., Moehle, W.E., Cobb, T.W. and Schneller, E.R., “Oxidation Fundamentals and its Applications to Turbine Oil Testing,”
Journal of ASTM International, April 2006, Vol. 3, No. 4.
5.
Ibid.
Mike Johnson, CLS, CMRP, MLT, is the principal consultant for Advanced Machine Reliability Resources, in Franklin, Tenn. You can reach him at mike.johnson@precisionlubrication.com.