Good practices
Peter A. Oglevie | TLT Shop Floor April 2010
All you need are the right tools and proper instruction to solve problems on the shop floor.
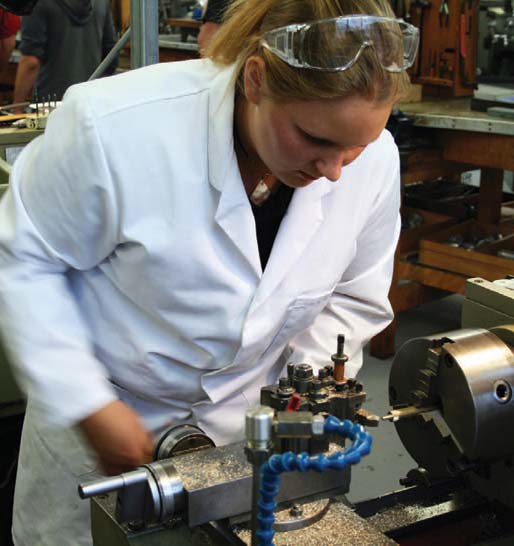
Good shop floor practices are the result of good guidance.
With the days getting longer and warmer temperatures, spring has finally arrived. While I enjoy this time of the year, I’m feeling a little stressed because I have to get my taxes done.
So what do taxes and the shop floor have in common?
For the sake of skipping the negative references, I’ll go straight to the one difference I enjoy. In my mind, neither are exact sciences. For example, you can take your taxes to 10 different accountants and get 10 different answers. On the shop floor, you can use 10 different metalworking lubricants and all make the same part. The difference from one lubricant to another is often process-driven.
I have a lot of respect for people who work on the shop floor. In my years of experience, I have seen them overcome serious problems and get the parts out the door, often working under adverse conditions with little or no guidance.
Sometimes I think management could learn from the IRS, The instruction we follow to fill out our taxes are complicated, but they do limit how we can interpret the tax code.
I’m reminded of a conversation I had with Al, a shop supervisor, who called me because a customer complained about too much lubricant on metal-formed parts his shop had made. When I got to his shop. We went out on the shop floor to fund out what happened. We inspected the returned parts and found excessive oil-based forming lubricant on the parts. It was no wonder considering the parts were supposed to run with a solution at no more than 15% concentration.
As we inspected the operation, I questioned the operators about why they had used the oil-based lubricant. The operators explained the forming die was a six-station progressive die. They applied lubricant with a roller coater at the entrance to the die cavity. The problem came in the fifth station. This station put the extrusion in the metal.
When the operators ran the solution, the workpiece was dry by the time it reached the extrusion, and the punch galled up and stopped the run after 20 parts. They replaced the punch and ran another 20 parts before it galled up again. They should have stopped at this point but did not. They substituted an oil-based forming lubricant from the next barrel in the rack and ran the order out with no problems.
The shop floor’s interpretations of the order were to make the parts and ship them. The customer’s interpretation spelled out part-specification and the type of lubricant to use. The difference in interpretations led to the company having to pay a penalty.
Al and I installed an airless sprayer on the press and dedicated a nozzle to the extrusion punch. That took care of the galling on the punch and allowed us to go back to using the metalworking solution. We made sure to insert a lubricant and application requirements with the job order so the operators would not substitute lubricants.
Good shop floor practices are the result of good guidance. Much as the IRS tax code spells out what you can and cannot do, shop floor personnel also need direction. Give them guidance on approved lubrication to make a part properly and they will. Sometimes all we need is the right tools and some instruction to solve a problem on the shop floor.
As you can see, we made the same parts with two different lubricants in this instance. The shop floor shipped the parts as required. No one told them about the residue problems they created until they were a problem. We were lucky the shop floor used a lubricant that could be easily cleaned and not effect the material surfaces.
I am glad there are instructions to understanding the tax code. Of course, it is also nice to have a computer program to guide me and limit my creative interpretation of the code.
Pete Oglevie is president of International Production Technologies in Port Washington, Wis. You can reach him at poglevie@wi.rr.com.