Hydraulic fluids in wind turbines
R. David Whitby | TLT Worldwide March 2010
A hydraulic transmission system makes wind turbines lighter, cheaper and more robust.
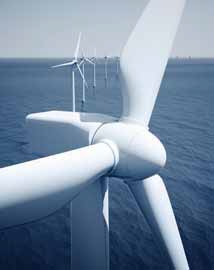
Modern wind turbines use speed-increasing gearboxes to couple the slow rotation of the blades to the high-speed of the generator.
www.canstockphoto.com
In November 2008 I wrote about the problems with lubricating the gearboxes of wind turbines. Now a solution may be close to practical application in replacing the gearbox with hydraulic power transmission.
Edinburgh, Scotland-based, Artemis Intelligent Power has been developing Digital Displacement® hydraulic power technology since the 1980s. At that time, professor Stephen Salter and his colleagues at the University of Edinburgh were investigating how to extract energy from waves. Hydraulic transmission seemed to be the best solution, but energy efficiencies at low power inputs are comparatively low.
Artemis’s solution was to replace the port plates and swash plates in conventional hydraulic pumps with computer-controlled, high-speed solenoid valves. This enables very high operating efficiency in part-load conditions and unprecedented controllability, especially in multiservice and synchronized applications.
Most large modern wind turbines use speed-increasing gearboxes to couple the slow rotation of the blades to the high speed of the generator. However, these gearboxes are heavy and prone to failure, and
in situ replacement is expensive. Other wind turbine designs use low-speed generators directly coupled to the shaft of the rotor. Though reliable, these machines are costly, very heavy and need full-power electronic frequency and voltage converters to condition their power for supply to the electrical network.
High-pressure oil-hydraulic transmissions have long been considered for wind turbines, but the part-load efficiencies of the conventional hydraulic pumps and motors have been too poor to make them attractive. In 2009, with the backing from the U.K.’s Carbon Trust, Artemis completed a prototype hydraulic transmission for a 1. 5-megawatt wind turbine.
The system uses a ring of 68 cylinders arranged radically around the turbine shaft. As the shaft rotates, it drives the pistons into the cylinders, pressurizing fluid that is used to power a pair of hydraulic motors. These in turn drive generators. A microprocessor monitors pressure inside the system and, depending on its level, activates high-speed solenoid valves to switch each cylinder in or out. Tests show that at most wind speeds, the unit operates at more than 90% efficiency, which is competitive with conventional gearboxes.
A continuously variable transmission ratio allows the rotor to be operated at the best speed for optimal power capture, while the synchronous generator is driven at a much higher constant speed. The hydraulic transmission shares its load across many pumping modules and so avoids the few highly stressed line-contacts that are inherent in gearboxes. The ability of hydraulics to limit pressure to a safe working value avoids potential overstressing of the driveline. Short-term storage in accumulators can smooth out wind turbulence.
The Artemis hydraulic system, which weighs 6 tonnes, compared with 15 tonnes for a conventional gearbox, makes wind turbines lighter, cheaper and more robust. It also eliminates the costly power electronics used conventionally to produce AC electricity at the optimum frequency for the grid. This is because the Artemis system lets the generator run at the optimum speed, even if the turbine is turning slowly.
Artemis notes that hydraulic drives are used in industrial processes involving sudden shocks and have well-established durability records. The company believes that repairs should be cheaper than with gearboxes because the design allows components to be removed individually without the need for floating cranes. It also will be suitable for retrofitting to existing machines and for use in the next generations of very large turbines.
In addition to working on wind turbines, Artemis has developed four major partnerships with a large oil company, two Tier One automotive suppliers and a leading manufacturer of off-road mobile hydraulics to apply the Artemis core technology in their sectors. In the course of this, it has built component and technology demonstrators for both small and large applications.
In November 2009 Artemis won The Overall Carbon Trust Innovation Award. In addition, the company is planning to fit a hydraulic transmission system to a wind turbine by 2011 to demonstrate the hydraulic system in practice.
David Whitby is chief executive of Pathmaster Marketing Ltd. in Surrey, England. You can reach him at pathmaster@dial.pipex.com.