Refrigeration Lubricants: Transitioning to new refrigerants
Dr. Neil Canter | TLT Cover Story December 2009
New technology is leading to products that are safer, longer-lasting and more environmentally friendly.
KEY CONCEPTS
•
Refrigeration lubricants lubricate internal parts, remove heat generated during compression, clean the system, act as a fluid seal and reduce energy requirements.
•
Regulatory drivers such as the Montreal protocol and global warming have prompted the industry to transition from CFCs to HCFCs to HFCs and now closely evaluate HFOs. Other refrigerants still under consideration are ammonia, carbon dioxide and hydrocarbons.
•
A goal is to improve the efficiency of refrigeration systems. This will be accomplished through changes in system design, re-evaluation of refrigerants and evaluation of new lubricant basestocks and additives.
The need to cool specific environments to either keep food from becoming rancid or to keep us comfortable during the summer requires the use of sophisticated compressors. Lubrication is an important aspect of this process, as the components in a compressor need to be maintained in a hermetic environment. The lubricant also must be compatible with a volatile liquid or refrigerant used by the compressor to remove heat from the system.
Figure 1 shows the basic heat-removing operational procedure, which is known as the compression refrigeration cycle (
1, 2). Starting on the right side of the diagram, the compressor acts to compress the refrigerant from a low-pressure gas into a high-pressure gas operating at a higher temperature.
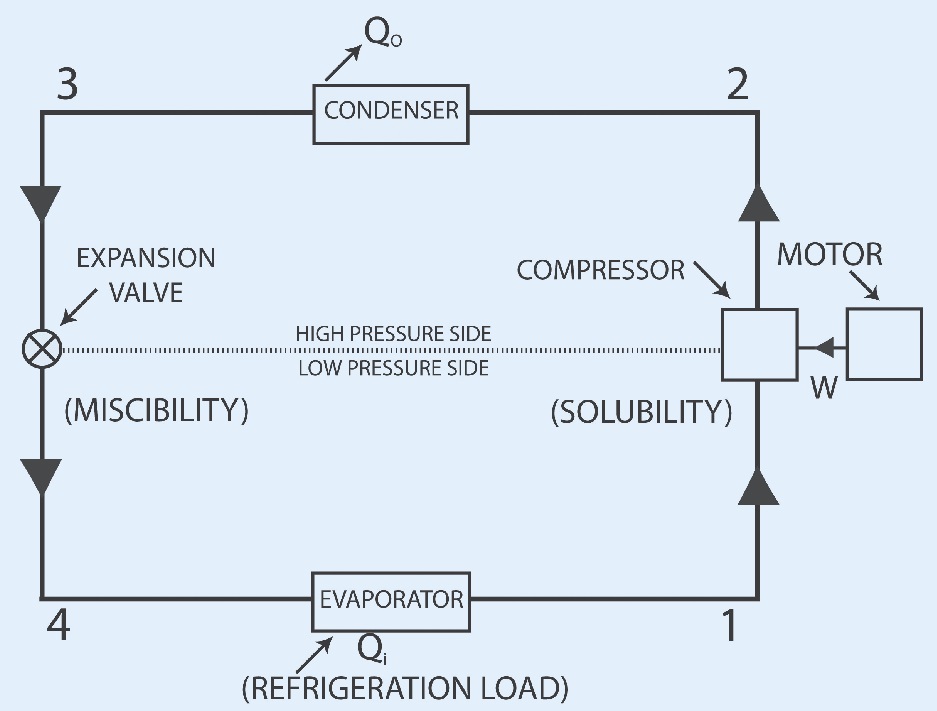
Figure 1. The compression refrigeration cycle is the basic procedure used to remove heat from a refrigeration system. (Courtesy of BV Advanced, a division of BVA, Inc.)
In moving counterclockwise, the high-pressure gas moves through a condenser, effectively removing heat from the system, and is converted into a high-pressure liquid. The refrigerant then passes through an expansion valve that reduces its pressure and boiling point. This converts the refrigerant to a low-pressure liquid.
In a final step, the liquid refrigerant passes through an evaporation that enables it to pick up heat from the environment and be converted into a low-pressure gas. In this vaporization step, the refrigerant in effect acts to cool the system. The cycle is now complete as the refrigerant is prepared to go through the compressor again.
In the sealed system, the relationship between the lubricant and the refrigerant is important. The lubricant travels with the refrigerant through the compression refrigeration cycle, which means that their interaction is a critical factor in impacting performance. In fact, the chemical properties of the refrigerant and the lubricant determine whether they are totally miscible with each other, partially miscible or immiscible.
LUBRICANT FUNCTION
STLE-member Glenn Short, director of BV Advanced, a division of BVA, Inc., in Wixom, Mich., says, “The refrigeration lubricant must lubricate internal parts, remove heat generated during compression, clean the system, act as a fluid seal and reduce energy requirements.”
STLE-member Ken Lilje, director of R&D for CPI Engineering Services, a subsidiary of The Lubrizol Corp., that is located in Midland, Mich., further elaborates, “Different lubrication regimes are required, depending on the compressor design and operating conditions, and these parameters must be considered when selecting the lubricant. When a gas is compressed, the lubricant in the compression zone picks up some of the heat of compression, which is subsequently dissipated elsewhere in the system.
“The lubricant also assists in keeping the refrigeration compressor clean,” Lilje adds. “While a mode of filtration is usually present, the lubricant helps transport various solid contaminants to the filter for removal. Refrigeration systems also have a variety of ‘non-contact’ surfaces that require sealing (e.g., cylinder/piston walls). The lubricant seals these surfaces and prevents the refrigerant gas from passing through.”
STLE-member Liwen Wei, president of Novitas Chem Solutions, LLC, in Houston, says, “Two other functions the lubricant performs are to control foam and reduce noise generated by moving parts of the compressor.” Wei also cautions, “The presence of oil in the refrigeration system is expected to influence the heat-transfer performance of the refrigerants and thus affect overall system performance.”
Wei brings up the concept of “entrapment” in the system as the lubricant travels with the refrigerant as it escapes from the compressor. He explains, “Lubricant entrapped by refrigerant can be in quantities up to 5% or more. This entrapment, if not managed properly by making sure of sufficient refrigerant miscibility or low enough viscosity or by making hardware accommodations (such as an oil separator), can lead to poor oil return resulting in oil starvation.”
This entrapment also can coat the inner surfaces of the system devices responsible for evaporating and condensing the refrigerant. This phenomenon can lead to a decrease in the effectiveness of the heat exchange, which also reduces the performance of the refrigeration system.
LUBRICANT DISTRIBUTION THROUGH A COMPRESSOR
STLE-member Dr. Valéry Dunaévsky, senior compressor engineer for Ingersoll Rand Climate Control Technologies in Minneapolis, discusses the following techniques for the movement of lubricant through the open drive shaft reciprocating compressor (one of the most popular types of compressors utilized in transport refrigeration).
“In the early 1950s,” he says, “an oil pump was introduced into mobile refrigeration compressors to increase their life and reliability compared to previous designs which relied on splash and gravity fed lubrication to the crankshaft bearings. An oil pump continuously supplies oil to the crankshaft bearings and shaft seal. After passing through the journal bearings and seal cavity, the oil contributes to the oil fog lubricating other components and then returns to the sump.”
Dunaevsky adds, “A second source of lubrication is windage that occurs as a result of the rotating masses in the crankcase creating a vortex of the surrounding mist/vapor that pools the oil from the sump, at the optimum clearance between the oil level and the lowest point of the rotating masses. This intensifies mist lubrication to all internal components in the compressor.” A related CFD (computer fluid dynamics) model, developed by Dunaevsky and colleagues, is shown in Figures 2 and 3, and evidence of a vortex has been proven by a recently conducted experimental analysis (
3).
Figure 2. This simulation shows gas velocity vectors associated with an initial stage of a formation of the vortex that is generated in the compressor sump by rotation of a crankshaft within a surrounding mist. (Courtesy of Ingersoll Rand Climate Control Technologies)
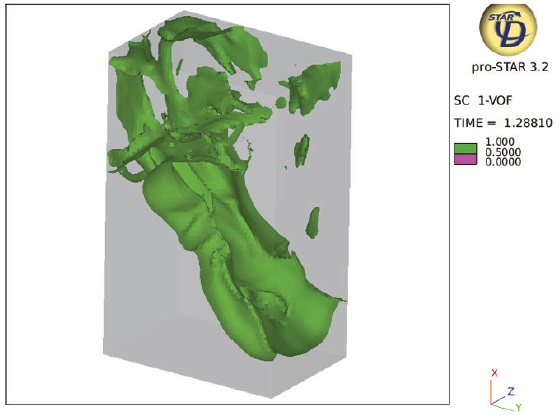
Figure 3. The vortex of a crankcase mist leads to the extensive formation of blobs of oil in the sump at the optimum location of the oil level in relation to the lowest points of the rotating masses. (Courtesy of Ingersoll Rand Climate Control Technologies)
Oil carried out with the refrigerant represents a third source of lubrication, according to Dunaevsky. This process enables the oil to lubricate compressor valves upstream of the piston as well as the system valves and contributes to the oil fog in the crankcase upon the return of the oil.
Examples of refrigeration compressor systems include: an Open Reciprocating Compressor (
see Figure 4) and a Refrigeration Chiller (
see Figure 5).
Figure 4. This Open Reciprocating Compressor is an example of a refrigeration compressor system. (Courtesy of The Lubrizol Corp.)
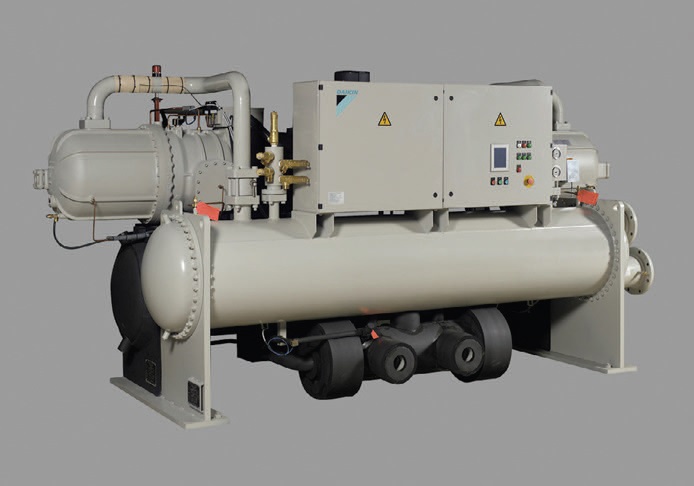
Figure 5. A Refrigeration Chiller cools water for use in air conditioning applications to provide cooling/dehumidification. (Courtesy of Novitas Chem Solutions, LLC)
LUBRICANT SELECTION FACTORS
Lilje considers refrigerant miscibility/solubility to be one of the key factors needed in lubricant selection. He says, “Picking lubricants for refrigeration applications are complicated by the fact that many of the commonly used refrigerants are soluble in the lubricant. This means that the ‘fluid’ actually doing the lubrication is a combination of both lubricant and refrigerant (often called ‘working fluid’), and the viscosity of this fluid is less than that of the lubricant alone. Typically, vapor/liquid equilibrium data is determined and used to predict what lubricant viscosity is required for a given compressor design. Miscibility of the lubricant and the refrigerator liquid phase often plays a key role in the return of lubricant to the compressor. This impacts compressor reliability and efficiency.”
Dunaevsky further elaborates on the effect of oil/refrigerant miscibility and system performance. He says, “Overall, the degree of miscibility is an important characteristic and must be considered in the connection with the design of a refrigeration system and its components. For any given refrigerant, the percentage that can be dissolved into the lubricant depends on four factors: (1.) Degree of miscibility of the refrigerant, (2.) Pressure of the refrigerant vapor, (3.) temperature of the lubricating oil and (4.) Length of time the two are in contact.”
He continues, “The percentage of the refrigerant that can be dissolved in oil increases considerably as the temperature of the oil decreases and the pressure of the refrigerant vapor increases. If during a short time, a large quantity of refrigerant vaporizes under the right conditions, then severe oil foaming will result leading to its migration out of the compressor thus endangering its operation.”
Miscibility is dependent not just on the refrigerant and the lubricant but also on the percentage of lubricant and the temperature. Diagrams showing the miscibility of two polyol ester (POE)-based lubricants with the refrigerant R404A are shown in Figure 6. R404A is a hydroflurocarbon (HFC)-based refrigerant that is a blend of three refrigerants: R125 (pentafluoroethane), R143 (1,1,2-trifluoroethane) and R134a (1,1,1,2-tetrafluoroethane).
Figure 6. Miscibility of two refrigeration lubricants A (Figure 6(a)) and B (Figure 6(b)) derived from the same basestock (POE), with the refrigerant R404A is different and dependent on the percentage of the lubricant and the temperature. (Courtesy of Ingersoll Rand Climate Control Technologies)
Good miscibility and solubility facilitate the return of oil to the compressor, which is important for its reliable operation and for system performance. For example, if oil return is hindered, then oil accumulated in the evaporator prevents normal heat transfer, and that reduces the efficiency and capacity of the system. In fact, the main factors that affect oil return are its miscibility with a refrigerant and a system designed to promote oil return.
Short indicates other issues that need to be considered include thermal stability, volatility and compatibility with other materials used in the refrigeration system. He says, “Both the thermal stability and volatility of the lubricant must be considered based on the application. Lubricants must be compatible with components such as metals, coatings and elastomers that are used in the refrigeration system. It is also desirable for the lubricant to have thermal conductivity to promote effective cooling.”
Wei provides other items that must be considered when recommending a lubricant: “Above all, the lubricant must provide lubricity and be stable enough over the lifetime of the compressor. Contaminants such as water, impurities and total acid number (TAN) must be kept to an absolute minimum so that the problems such as capillary plugging cannot occur. Viscosity is also an important consideration because this parameter must be low enough to provide less drag (better energy efficiency) and good oil return properties.”
One other element that is becoming more important is retrofitting of compressor refrigeration systems with newer refrigerants that exhibit no ozone depletion and low global warming potential (GWP). In moving to a new refrigerant, measures must be taken to ensure that the lubricant is compatible and stable.
Jeff Berge, manager of R&D for Ingersoll Rand Climate Control Technologies, furnishes an end-user perspective on the testing that is conducted in choosing a lubricant for a specific application. He says, “The first step in our evaluation involves physical and chemical testing of the lubricant: color, viscosity, moisture level, acid number, particulate count and FTIR analysis.
“The next step in our evaluation process involves material compatibility in high-pressure sealed tubes as identified by ASHRAE (American Society of Heating, Refrigerating and Air-Conditioning) Standard 97,” Berge says. “The exception is that we run these tests at higher temperatures and extended durations due to our severe environment: lubricant/refrigerant compatibility with metal components, lubricant/refrigerant compatibility with elastomers and gaskets; and compatibility of lubricant/refrigerant in presence of processing fluids.”
Once a lubricant and refrigerant is selected for a specific compressor, then a series of endurance tests is conducted for a specific time. Berge says, “The lubricant condition is monitored periodically throughout the duration of the test for chemical stability, acid number, moisture content and wear particles. At the conclusion, the compressor is disassembled, and all the moving parts are carefully inspected for dimensional changes and wear. O-rings and gaskets are inspected for swelling, deformation or cracking. When issues of lubricity or material compatibility arise, and to minimize complexity with system chemistry, we have taken the position to alter the component design rather than incorporate additives in the refrigerant/lubricant system.”
REFRIGERANT OPTIONS
The use of a refrigerant in a closed system dates back to 1835 (
1). The original compounds used include ethyl and methyl ethers, ammonia, carbon dioxide, sulfur dioxide, methyl chloride, ethyl chloride and light petroleum distillates.
Many of these original refrigerants are flammable and can cause irritation upon exposure. The search for safer alternatives led to the development of chlorinated fluorocarbons (CFCs) in the 1930s. These refrigerants enabled the large scale development of the refrigeration and air conditioning units we all utilize today.
Two of the CFCs used successfully as refrigerants were R12 (dichlorodifluoromethane) and R22 (chlorodifluoromethane). The former was utilized primarily in refrigeration while the latter worked well in air conditioning. R22’s selection was due to its higher efficiency and greater capacity as compared to R12.
Use of CFCs expanded into propellants for aerosol products, which led to the release of large volumes of this refrigerant into the atmosphere. The excellent stability of CFCs enabled them to rise into the Earth’s stratosphere and negatively impact the ozone layer. CFCs release chlorine radicals when exposed to ultraviolet light in the stratosphere which react with ozone.
Raymond Thomas, New Applications Group for Honeywell Corp., in Buffalo, N.Y., says, “The issue of ozone depletion caused by the presence in the atmosphere of the previously used long-lived, chlorine-containing molecules gave rise to the Montreal Protocol which mandates the replacement of these ozone-depleting substances. As a result, the CFCs have been eliminated and the phase out of the hydrochlorofluorocarbons (HCFCs) is ongoing. Both of these types of refrigerants contain chlorine which, in these molecules, creates issues with respect to ozone depletion. They have been replaced by the HFCs that do not contain chlorine.”
The Montreal Protocol, prepared in 1987, called for the banning of CFC refrigerants in developed countries by the end of 1995. HCFC refrigerants had been developed as a transition to safer refrigerants. The most prominent of the HCFCs is R22 (chlorodifluoromethane) which is relatively inert to ozone but has been found to contribute to global warming. R22 has a global warming potential (GWP) of 800 and its use is being phased out in the U.S. starting in 2010 with a total ban by 2020.
Industry attention turned to the use of HFCs that do not cause ozone depletion. Examples include R134a which is used widely in automotive air conditioning systems.
But HFCs also contribute to global warming, which is placing them under scrutiny. For example, R134a has a GWP of 1,300. The search for replacements has led to the evaluation of hydrofluorinated olefins (HFOs). Thomas says, “In Europe, R134a has been targeted for replacement because of its global warming. HFO-1234yf (2,3,3,3-tetrafluoroprop-1-ene) has emerged as the leading candidate as a low global warming refrigerant in mobile air conditioning. New low GWP refrigerant blends are under development for use in commercial and industrial refrigeration. There is some renewed interest in carbon dioxide and hydrocarbons for commercial use but installation costs and safety issues have limited their application.”
The F-Gas Directive on Mobile Air Conditioning, enacted in 2006, states that no automobile manufactured after Jan. 1, 2011, can contain a refrigerant with a GWP above 150. This directive effectively bans the use of R134a in 2011.
Table 1 shows a summary of how regulatory changes are affecting the use of refrigerants.
Table 1. Chronological listing of the regulatory drivers affecting the use of specific refrigerants in the past, currently and in the next 20 years. (Courtesy of Novitas Chem Solutions, LLC)
Lilje discusses the other main alternatives for HFCs. He says, “Carbon dioxide (R744) has a main advantage of exhibiting of GWP of 1. But there are a number of disadvantages including the fact that many carbon dioxide applications require trans-critical operation. This means that discharge pressures likely will approach 2,500 psi. In contrast, HFC discharge pressures are generally 200-350 psi. Equipment changes will be required for safety reasons, and efficiency may not be acceptable in some applications.”
He continues, “Hydrocarbons such as isobutane (R600a) and propane (R290) are currently used in some parts of the world for domestic refrigerators. These refrigerants have low GWP and good efficiency but have the main disadvantage of being extremely flammable.”
A final option is ammonia (R717) which is widely used in industrial systems. Lilje adds, “This gas is both toxic and flammable and special accommodations must be used to insure safe operation, especially in applications with potential public exposure.”
In discussing the refrigerant changes made in response to the Montreal Protocol, Berge says, “We have historically used R12, R502 [a blend of R22 and the CFC refrigerant, R115 (chloropentafluoroethane)] and R22 in our transport heating, ventilating and air conditioning (HVAC&R) products (
see Figure 7). We transitioned from CFC to HFC refrigerants starting in 1995. Where we used R12, we now use R134a. Where we used R502, we now use R404A [a blend of the HFCs R125 (pentafluoroethane), R143a (1,1,1-trifluoroethane) and R134a].”
Figure 7. Refrigeration system used in transport heating, ventilating and air conditioning products. (Courtesy of Ingersoll Rand Climate Control Technologies)
Berge continues, “Where we use R22, we have moved to R407C [a blend of the HFCs R32 (difluoromethane), R125 and R134a]. We selected these HFC replacements after extensive analysis and evaluation because they most closely match performance (efficiency and capacity) and system operating characteristics (temperature and pressure) of their predecessors. This has imposed minimal impact on our system designers and most importantly on our customers who use and service our products.”
Thomas indicates that the objective in replacing the old refrigerants is to minimize any changes that a customer sees when using the new refrigerant. He says, “All the options therefore behave very similarly to the original refrigerants, but there are differences.”
An example noted by Thomas is the replacement of R22 with the HFC refrigerant R410A (a combination of R32 and R125) in home air conditioning. Thomas says, “R410A has a higher vapor pressure than R22, but there are gains in efficiency. However, there are many factors to consider when talking about entire refrigeration and air conditioning systems. For example, when OEMs were searching for a replacement for R22 in residential equipment, several refrigerant blends were available that came very close to performing like R22. But when you apply new efficiency standards, R410’s higher vapor pressure allows for smaller equipment and compressor displacement, which saves the OEM in material costs.”
SELECTING BASESTOCKS
The changes made in moving from CFCs to HFOs have impacted the type of lubricant basestock that can be used in conjunction with the refrigerant. The original lubricants used with CFCs and HCFCs were based on refined naphthenic base oils.
For applications that required better stability at higher or lower temperatures, alkylated benzenes were used. Dunaevsky says, “We found that attempts to use a more environmentally friendly refrigerant R502 [a blend of R22 and R115 (chloropentafluoroethane)] were not successful as the base (mineral) oil was not adequate for the refrigerant, particularly as it thickened at low temperatures. The answer was the use of an alkylated benzene that mixes well with CFC refrigerants and maintains favorable viscosity (thickness) at all operational temperatures.”
He continues, “However, alkylated benzene-based compressor oils are not compatible with chlorine-free HFC refrigerants such as R134a, R404A and R407C. Accordingly, POEs, which are compatible with these refrigerants, replaced alkylated benzenes in our systems.”
The CFCs and HCFCs used mineral oils. All the new options use synthetic lubricants like polyalkylene glycols (PAGs) and esters. Thomas adds, “There have been attempts to use mineral oils with the HFCs. These attempts have had limited success. The synthetic oils are more hydrophilic than mineral oils and therefore need to be handled more carefully.”
The HFC refrigeration industry has moved to basestocks that are primarily based on either PAGs or POEs. Lilje says, “POEs are the lubricants of choice for most stationary refrigeration applications. PAGs are used in most automotive air conditioning applications. Alkylated benzenes and polyvinyl ethers (PVEs) are also used in some applications.”
Thomas indicates that the new fluorinated refrigerants such as HFO-1234yf are compatible with POEs and PAGs. He adds, “Use with mineral oils is not currently recommended because of problems with mutual solubility and miscibility.”
Wei indicates that the use of refrigerant blends can enable OEMs to use mineral oils. He says, “Two ways to utilize mineral oils are to include a hydrocarbon such as R600 (butane) in the refrigerant mix or to include polar basestocks such as POEs or PAGs in the lubricant mix.”
Ammonia, carbon dioxide and hydrocarbon refrigerants all have requirements for specific lubricants. Short says, “Ammonia has been used as a refrigerant since 1850. This refrigerant is very energy efficient and does not present an environmental problem with low ozone depletion and GWP. The main lubricant basestocks used are highly refined Group II and Group II base oils. For low-temperature applications, polyalphaolefins (PAOs) also can be used, particularly in blends with mineral oils. PAGs are also useful, particularly in Direct Exchange Evaporators.”
Carbon dioxide has emerged as a viable refrigerant for current and future applications because of its low GWP. But challenges exist in working with carbon dioxide. Wei explains, “The high-temperature and operating pressures for using carbon dioxide in Mobile Air Conditioning Applications (160 C and 13 Mpa) means that special attention must be paid to the stability and wear performance of the lubricant. Refrigerant miscibility is important, so PAGs and POEs are the basestocks of choice.”
Short sees advantages from using both PAGs and POEs with carbon dioxide. He says, “PAGs have better lubricity because they form carbonates with carbon dioxide. But POEs when used with additives have superior miscibility with carbon dioxide and can provide good performance under heavy-duty antiwear/extreme pressure operating conditions.”
A recent paper compared the performance of a PAG-based lubricant vs. a POE in a carbon dioxide refrigerant atmosphere (4). Better performance was seen with the PAG because of the formation of carbonate layers leading to better performance. In contrast, the hydrolysis of the POE lubricant led to a drop in viscosity of the lubricant and, as a consequence, inferior results.
For hydrocarbon refrigerants, mineral oils are the predominate lubricant. Lilje adds, “More polar lubricants (such as PAGs and POEs) also are used in some industrial applications to help reduce lubricant dilution and improve operational efficiency.”
Each of the lubricant basestocks has advantages and disadvantages in working with specific refrigerant types. Wei summarizes, “PAGs and POEs are polar basestocks that have significantly better HFC and HFO miscibility and excellent low-temperature characteristics compared with mineral oils and alkylated benzenes. But the two polar basestocks are much more hygroscopic.
He continues, “Mineral oils require special refining to reduce the impurity levels (wax and sulfur content) in order to be used for refrigerant applications. Naphthenic oils are much preferred to paraffinic oils due to improved R22 miscibility. Alkylated benzenes offer better stability and improved miscibility with HFCs as compared to mineral oils.”
With ammonia, Short recommends PAO, alkylated benzene blends, particularly at low-temperature. He says, “In carbon dioxide refrigerant applications, end-capped PAGs provide a performance improvement over conventional PAGs. PAOs also can be used in low-temperature applications, even though this basestock is not miscible with carbon dioxide.”
ADDITIVES
Small treat rates of additives are formulated into lubricants used with HFC refrigerants. Wei says, “Additives typically used are to boost antiwear protection, metal passivation, acid scavenging and defoaming.”
The movement away from chlorine-containing refrigerants has led to a greater need for antiwear additives in specific applications. Additives used in small quantities can boost the performance of POEs when used with HFC refrigerants. Special types of additives may be required for use with PAGs as conventional types of these additives may not be compatible.
Dunaevsky says, “It is well known that chlorine-containing refrigerants such as R12 possess some lubricity properties. These refrigerants can react chemically with metals in the refrigeration system to form protective surface films composed of metal chlorides.”
The antiwear additives are based on sulfur and phosphorus chemistries and can boost the performance of the lubricant. But due to their chemical reactivity, care must be taken in their selection.
Dunaevsky adds, “Antiwear additives may reduce the lubricant’s overall stability. Some additives work best when combined with other additives. An additive is only used after thorough testing to determine whether it is (1.) Removed by system dryers, (2.) Inert to system components, (3.) Soluble in refrigerants at low-temperatures so as not to cause deposits in capillary tubes or expansion valves and (4.) Stable at high-temperatures to avoid adverse chemical reactions such as harmful deposits. Testing to check additives can best be done by sealed-tube and compressor testing using the actual additive/base lubricant combination intended for field use.”
FUTURE DRIVERS
Berge summarizes the challenges facing those manufacturers of transport refrigeration compressors. He says, “The biggest regulatory driver is the focus on the direct GWP of the HFC refrigerants that we use. If and when we move to low GWP alternatives, the challenge we face is maintaining and/or continually improving life cycle cost, energy efficiency, reliability, durability, simplicity and serviceability of our products.”
Increasing energy costs as well as environmental concerns are driving the OEMs to improve the efficiency of their refrigeration compressor systems. Lilje says, “Refrigeration and air conditioning applications consume a significant amount of the global energy production. Most OEMs are working diligently to find increased efficiency in their systems. This work includes component redesign, varying operational parameters and refrigerant re-evaluation. The results of these efforts could well impact the performance requirements and choice of the lubricant.”
As part of this approach, OEMs are looking to reduce the refrigerant charge and become more environmentally friendly. Thomas explains, “Charge reduction is a common thread. This is sometimes done by using secondary refrigerant fluids, conversion to water-cooled condensing and more recently the application of micro-channel heat exchangers. OEMs also are using life cycle assessments of energy usage required to run their systems. Refrigeration systems that have a lower direct contribution to climate change and also are very energy efficient over their lifetime will be very competitive in the current and future business climate.”
Wei sees the refrigeration compressor industry focusing on enhancing the heat-transfer process and improving compressor efficiency. He says, “The refrigeration industry as a whole is a business to trade one form of energy (mechanical work) to another (cooler temperatures). As the industry eliminates substances that can cause ozone depletion and global warming, the efficient use of refrigeration energy is focused almost exclusively on new refrigerants such as refrigerants’ capacity to cool and the thermodynamic conditions to circulate such refrigerants. More and more attention in the last 5-10 years has been given to lubricant and additive chemistries that can enhance heat-transfer and compressor efficiency.”
Dunaevsky agrees that improvement of heat-transfer would be very beneficial. He says, “Recent studies have shown that the heat-transfer of a refrigerant is a strong function of lubricant properties. When a lubricant is added to a refrigerant, either an enhancement or degradation in heat-transfer performance is achieved relative to that of the refrigerant, depending upon the lubricant’s viscosity, miscibility and concentration. Addition of copper-based nanoparticles to the lubricant has been shown to boost the heat-transfer properties of the refrigerant.”
Dunaevsky is also calling for an upgrade in the hydrolytic stability of POEs. He says, “One of the main concerns is the operation of POEs under adverse conditions. Under the right conditions, ester hydrolysis can occur to produce undesirable byproducts such as carboxylic acid that can react with some metals and elastomers. Enhancement of the POEs with improved hydrolytic stability or transition to oils resistant to hydrolysis, such as PVEs for example, may promote robustness of a refrigeration system and in some cases its simplification by removing the filter dryer.”
Short sees a trend towards smaller refrigeration compressor systems that put more demands on the lubricant. He adds, “Efficiency will be more critical as there will be more emphasis placed on superior cost-performance and minimization of energy use. Innovations such as new lubricant basestocks or additives may be required. For example, newer types of lubricants such as PVEs were not available 20 years ago. The structure of more common types of synthetic lubricants also may be modified for improved performance. In some cases, a liquid lubricant may not be required as some systems could use coatings on compressor equipment.”
The future use of refrigeration lubricants will initially be dictated by the movement toward new refrigerants such as HFOs that exhibit minimal GWP. The compressor industry anticipates that POEs and PAGs will remain as the basestocks of choice with HFOs. Longer term, the goal will be to continuously improve the efficiency of compressor systems.
REFERENCES
1.
Stein, W. and Mead, T. (1993), “Refrigerant and Refrigeration Oil Trends,”
Lubrication,
79 (3), pp. 2–3.
2.
Short, S. and Rajewski, T. (1995), “Lubricants for Refrigeration and Air Conditioning,”
Lubrication Engineering,
53 (4) , pp. 269–274.
3.
Dunaevsky, V. (2009), “Mist(erious) Mechanism of Lubrication of a Pumpless Refrigeration Compressor,”
Presented at the STLE 64th Annual Meeting & Exhibition, May 17-21, Orlando, Fla.
4.
Nunez, E., Demas, N., Polychronopoulou, K. and Polycarpou, A. (2008), “Tribological Study Comparing PAG and POE Lubricants Used in Air-Conditioning Compressors Under the Presence of CO
2,”
Tribology Transactions,
51 (6), pp. 790-797.
Neil Canter heads his own consulting company, Chemical Solutions, in Willow Grove, Pa. You can reach him at neilcanter@comcast.net.