Why superconductivity = super opportunity
Betty Catalina Kohanloo | TLT Cover Story September 2009
Motors built with high-temperature superconductors are smaller, lighter, quieter, more powerful, use no fuel, don’t pollute—and have application in all aspects of everyday life.
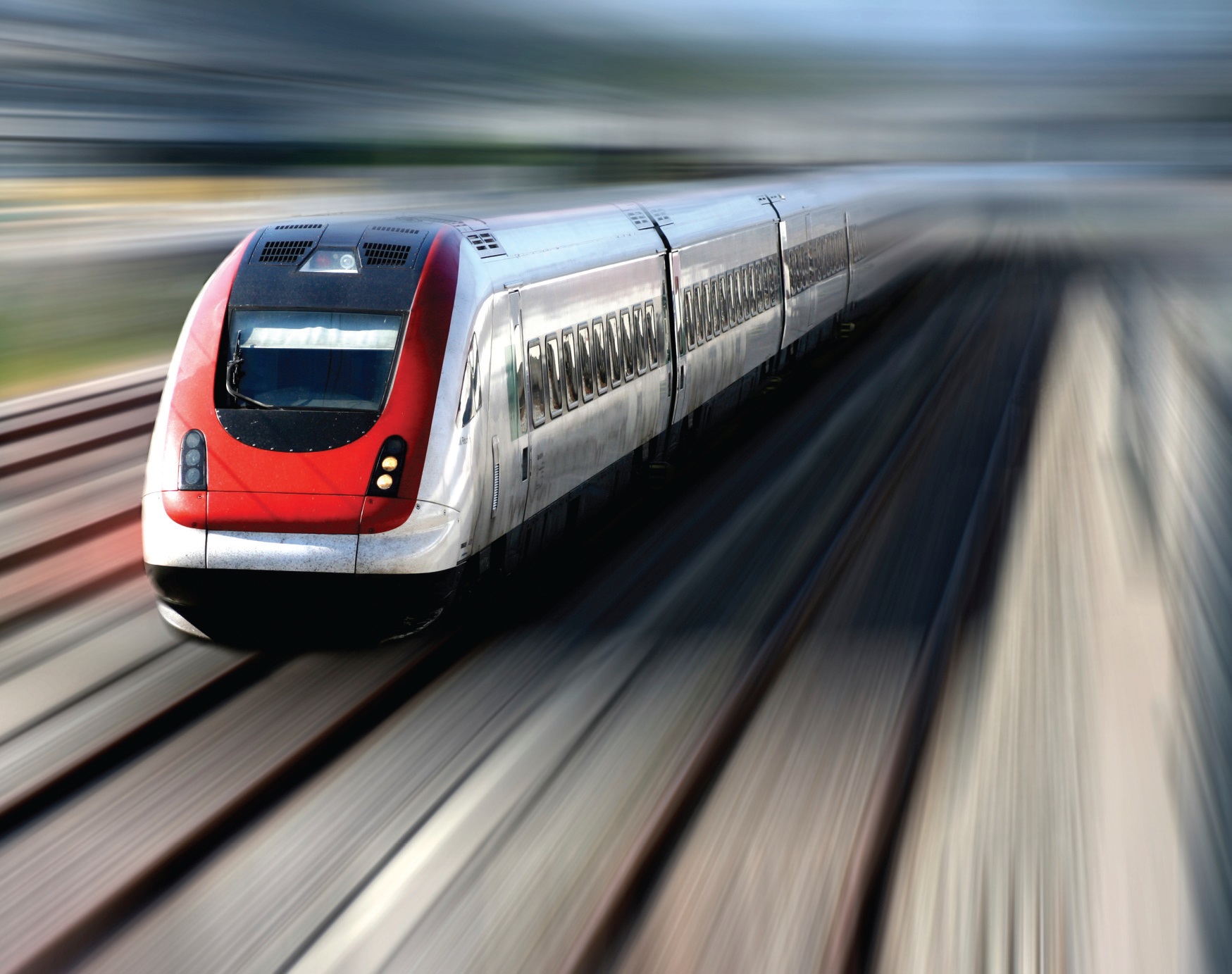
www.canstockphoto.com
KEY CONCEPTS
•
Superconductor properties include zero electrical resistivity leading to uninterrupted currents and fields and infinite electrical conductivities at certain critical temperatures.
•
Superconductivity is a property as basic as electrical and thermal conductivities that occur in materials ranging from ductile elementals metals, brittle ceramics, alloys, organic polymers, fullerenes and carbon nanotube materials.
•
High-temperature superconductors are already in use in industrial processes, military power systems, electrical vehicles and generation and distribution systems where efficient and cost-effective energy optimization is desired.
As the flat economy has stressed both industries and consumers worldwide, almost everyone, it seems, is seeking aggressive tactics to decrease variable costs stemming from energy consumption. With economic woes mounting, the energy-efficiency concerns of the 1970s and ’80s are plaguing the world again.
The rise of resource nationalism in foreign and domestic countries, a “no drilling in my backyard attitude” by many, increased demands from developing countries and a stagnant supply has led to escalating energy prices. Since greater than 63% of all electricity in the U.S. industrial energy sector is consumed by motors, and due to high electrical costs, implementing energy-efficient strategies could help reduce unnecessary spending. By emulating the energy policies of Germany, Japan and others in the European Union, the U.S. may be able to offset energy costs.
Industrialized countries can further curb their dependence on foreign and nationalized resources by implementing the use of superconducting technology, which has been around since the 1800s. After all, modern industrial uses of high-temperature superconductors have been around since the 1990s.
So you may ask, what exactly are superconductors, and why, oh, why, have we not heard more about them? The answer is simple: Superconductivity is considered an obscure, anomalous and frictionless state of matter that occurs at low temperatures. Basically, superconductors are electric conductors that work without dissipating heat and offer frictionless electrical resistance that leads to the elimination of power loss and heat generation.
Properties of superconductors include zero electrical resistivity leading to uninterrupted currents and fields and infinite electrical conductivities at certain critical temperatures, often resulting in levitation phenomena. Closed loops of superconducting wires exhibit frictionless motion when cooled to low temperatures. This frictionless flow, in turn, allows electricity to be carried with almost zero electrical resistance, yielding a low-loss conduction of high-density currents. This uninterrupted current, in turn, creates an energy-saving technology that has applications in just about every aspect of modern day life.
Superconductivity is a property as basic as electrical and thermal conductivities, or heat capacity, and it occurs in materials ranging from ductile elemental metals, brittle ceramics, alloys, organic polymers, fullerenes or carbon nanotube materials. The superconductive state is a state of matter; it is, after all, a discrete phase ordering transition that occurs at low temperatures and is evidenced by more than 7,000 compounds, a still-growing number.
Due to the varied properties of these materials, a number of processes are implemented to optimize their superconductivities so a range of materials from wires, coils, sheets and thin films can be produced. The induced superconductivity resulting from the electron pairing of closely spaced thin layers of metal also can be exploited in electronic devices, chips and/or other circuitry.
Wind turbine using high-temperature superconductor transformers.
High-temperature, unconventional superconductors consist of a large family of layered materials of which the copper oxides of yttrium, barium, bismuth and/or lanthanum are the most notable. These are fairly common, as their critical temperatures can range from 24 K to 135 K with the upper temperature range being close to that of liquid nitrogen. These high-temperature superconductors (HTS) would have enormous savings potential, as a liter of liquid nitrogen costs about $0.60 vs. $25 for the same amount of liquid helium. Generally HTS are available in three material forms: bulk, thin films and wires and tapes.
Copper oxide or cuprate HTS, discovered in 1986, were the first materials to show that superconductivity can occur above 30 K in very bad conductors such as non-metals. The uniqueness of the cuprate family is their strongly correlated electron mechanisms which result in electron coupling, subsequent spin alignment and magnetic field strength. It is this unique coupling of the solitons (electron-electron pairing) and bisolitons (electron-hole pairing) which causes the strongly correlated behavior of electron spin and magnetic fields, thereby producing the anomalous high-temperature superconductivity.
The discovery of high-temperature superconductivity in ceramics spurred intense research as scientists envisioned magnetically levitated trains, frictionless and lossless electrical conductivity. Due to their low weight, energy efficiency, higher temperature currents and magnetic fields, this article focuses solely on HTS, which are the most industrially relevant. Since HTS wires and tapes are more efficient and more compact than regular copper technology, stronger electronics and superefficient and lightweight electric motors and generators can result.
Magnetic levitation phenomena evidenced by a superconductor. (Courtesy of Metal Oxide Technologies)
Large-scale applications of HTS have presented a major challenge to materials scientists due to the requirement of much larger currents, lengths of wire and stronger magnetic fields. Special processing such as sintering, rolling and annealing that produce longer wires have solved some of the remaining technical issues. Yet, while successful applications existed, a number of technical challenges plagued the field. Initial problems arose from their brittleness and grain structure. Such effects proved difficult when it came to shaping these materials into long, flexible superconducting wires, coils that were needed for many large-scale uses.
To circumvent other problematic issues, coated conductors, which are composed of highly textured thick films of HTS, are deposited on flexible tapes, allowing for the effective generation of longer high quality wire. This led to the introduction of the first-generation Bismuth-based copper oxides, although their cost has often limited their use. Yttrium-based copper oxides (YBCO) have proved somewhat more problematic due to the difficulty of growing these in bulk.
YBCO-HTS, discovered by C.W. Paul Chu at the University of Houston, nevertheless showed a relative ease of small-scale fabrication and robustness when compared to other HTS materials. Ingenuity allowed the use of thin-film YBCO-HTS in small-scale, high-speed electronics, logic and microwave chips that show sharp bandwidth characteristics. These are found in modern-day cell phones, PDAs and in semiconductor Joseph junctions that require sensitive magnetic field detectors such as SQUIDS. These are commonly used in satellites, receivers and mobile and/or aerospace communication systems which need to filter out atmospheric noise.
C.W. Paul Chu, discoverer and inventor of the YBCO-HTS, is also founding director of the Texas Center for Superconductivity at The University of Houston. (Courtesy of The University of Houston)
One company, Metal Oxide Technologies (MetOx), has already developed an operational continuous-coated conductor single-pass processing system. The MetOx’s coated conductor system is able to produce over 15-meter YBCO-coated HTS conductor tapes using a 100% low-vacuum process that eliminates the need for high-vacuum equipment and/or clean room environment. To date, the system represents the lowest compact, capital cost approach to fabricating large scale, stable and uniform YBCO-coated conductors.
NASA Radio Observatory, a highly sensitive detector that uses superconductor detectors.
Comparing superconducting tape with a copper busbar. Both carry about 1,000 amps, but the copper busbar is a quarter-inch by three inches in cross section compared to the 6-micrometer-thick, 1-cm wide metal tape HTS. (Courtesy of LANL Super Conductivity Center (MPA-STC)).
As parallel systems can be installed and operated in a small manufacturing footprint, a scalable production capacity of 5,000 kA-m/yr to 1,500,000 KA-m/yr is feasible. The development of such systems makes the implementation of cost-effective fabrication techniques possible, which would further help commercialize HTS technologies. MetOx’s Lou Castellani states, “MetOx has an operational prototype production line producing limited amounts of second-generation HTS wire, and we are currently seeking funds to build a full-scale production line that we expect to be operational in late 2009 or early 2010.”
Advances in research and cost-effective technologies will make it possible to design smaller electronic equipment and stronger, more efficient power transmission cables able to operate through severe weather without power losses. “There are waiting markets for HTS wire, and the first would be the replacement of first-generation HTS wire and low temperature superconducting wire in commercial and government applications. Copper replacement will take a bit longer, not because of lack of market interest but because of the normal prototype to commercial adoption cycles associated with any new technology,” adds MetOx’s Castellani.
Nevertheless, such technicalities have not hindered the application of first-generation-coated HTS, which are being commercially introduced in advanced technologies that make use of high-horsepower superconducting bearings and motors that can be used in electric aircraft, naval and aerospace applications.
According to Dr. Rich Schiferl, director of advanced technology at Baldor Electric Co., “The discovery of YBCO systems has resulted in active development of HTS wire and coils for industrial electric motor and utility generator applications. For a 6,000-hp (4480 kW) industrial motor, the input power to the cooling system for the superconducting coils operating at 30 K will be about seven kW or 0.16% of the rated output power of the motor.”
These HTS motors are already in use in industrial processes, military power systems, electric vehicles and generation and distribution systems where efficient and cost-effective energy optimization is desired. High-horsepower HTS motors already can cut energy losses by more than half while eliminating most greenhouse gas exhaust. They also reduce the size and weight of motors, generators, power transmission and supporting components while delivering the same amount of power with no power or heat losses.
Dr. Paul N. Barnes, research group leader at the Air Force Research Laboratories AFRL/RZPG, says, “As aircraft systems become more electrically driven, there is a need for greater electrical power, namely at the multimegawatt level. Simple scaling of conventional airborne power generators is not a plausible solution since these components cannot provide multimegawatt amounts of power without placing an undesired burden on payload and space. Only proactive efforts on novel power systems such as HTS technology will address these concerns.”
William C. Livoti, industry engineer-power generation and fluid handler at Baldor Electric Co., says, “Bigger isn’t always better, and smaller, more powerful HTS motors can be advantageous to plant customers. Once an equipment is introduced and configured into its designated area, it may become necessary to remove components for maintenance, repair and replacement. Compared to conventional motors, HTS motors offer significant size reduction and mobility, which can facilitate maintenance.”
HTS bearing. (Courtesy of the Air Force Research Laboratories AFRL/RZPG)
Size reduction is also important for the transportation sector. According to Barnes, “Superconducting components made using YBCO conductors can enable megawatt-class-power airborne systems due to the reduction in size and weight over the conventional counterparts. Improvements in these areas as well as better stability will lead to unprecedented power densities for military, air, ship, terrestrial and aerospace applications.”
HTS motor. (Courtesy of the Air Force Research Laboratories AFRL/RZPG)
Nevertheless, cost seems to be the major factor in the commercial implementation of the technology. Industrial HTS motors are fundamentally similar to current electric motors, but their performance in terms of size, weight and efficiency improvements offer an attractive economic advantage to conventional motors. Compared to high-efficiency inductor motors, HTS motors are approximately half the volume, lighter, close to 50% more efficient and offer lower in-life cycle costs—often more than $50,000 in savings.
Dr. Schiferl adds, “The first cost of an HTS motor, using currently available HTS wire, is strongly determined by the cost of the HTS conductor; so much that this one material cost can overwhelm the other component costs. This is a primary reason that HTS industrial motors are not fully commercialized today.”
Yet Schiferl believes that HTS motors can be economically viable for a broad market if their first cost/sell price and payback from lower operating costs can occur within the first couple years of purchase. “Based on the current state of the technology and costs, it is likely that economic viability is at least five years out in the future,” adds Schiferl.
Yet, this has not hindered the use of HTS wires in magnetic levitation trains used in Japan and Europe, which can operate at close to 150-500 miles per hour. These Maglev trains do not need engines or fuel but rather consume electricity in terms of superconducting loops, which offer significantly longer service life than autos, trucks or airplanes, while being quieter and emitting no pollution. Since Maglev trains can move passengers and freight at much higher speeds at significantly lower costs and with significant energy reduction, their air, or underground low-pressure operation tunnels, could theoretically make it possible to get from Los Angeles to New York in an hour.
Central Japan’s Railway MLX01 Train, a >500-kmph Maglev train that uses superconducting magnets to literally float above the guideway or track. (Courtesy of the Coalition for the Commercial Application of Superconductors)
Maglev systems also can offer significant safety advantages over conventional railroads. Since the distance and speed of the vehicles is automatically controlled and maintained by the frequency of the electric power fed into the system, the possibility of collision is eliminated. Maglev trains and transportation systems also offer lower guideway costs ($12 million vs. $40 million-$60 million per mile), five years of payback time, and allows the use of existing, conventional railroad tracks.
The potential for HTS extends from Maglev trains to smaller and faster electronics to high-mileage, gasoline-independent electric motors that are quieter and 50% smaller than conventional motors. The smaller size and weight of HTS equipment also offers industry and consumers tremendous money-saving opportunities due to their lower first-acquisition cost and reduced operating costs. HTS technology promises to revolutionize the transportation sector, leading to superefficient vehicles. This, in turn, will help in making significant reductions in greenhouse gases while easing our dependence on the fluctuating price swings of fuel and oil.
World’s first commercialized 138 kV HTS cable system installed in Long Island, New York’s commercial power grid. The HTS cable can carry 574 megawatts of electricity, enough to power 300,000 homes. (Courtesy of American Superconductor)
And, yes, the elusive mechanism that obscures the technology will eventually become known. If the macrostructure of the superconductor could be controlled and predicted at the micro level, then, through specific processing, i.e., annealing and sensitive magnetic characterization techniques, it should be possible to control both critical temperatures and currents, resulting in more evenly coated wires that are longer in length. This would lead to changes in the overall electron dipole moments and spin arrangements, which lead to the ensuing altered electron and/or hole carriers. It is, after all, the electrons and respective magnetic moments that give rise to the strongly correlated quantum effects that produce the HTS phenomenon.
Betty Catalina Kohanloo is a doctoral candidate in applied physics at Rice University in Houston. You can reach her at bcrostro@rice.edu.