Biological control in MWFs
Peter A. Oglevie | TLT Shop Floor August 2009
Just as with a human’s diet, too much of one thing and not enough of the other can mean bad health for your operation.
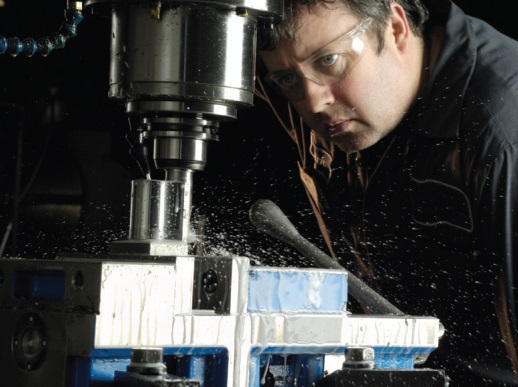
The shop floor is not a sterile environment. Anything and everything that can happen will happen.
www.canstockphoto.com
My daughter is about to spread her wings and fly. She graduated from high school with high honors and wants to be a medical doctor. This will require commitment and dedication, and she’ll be in school for a long time before she sees her first patient. Considering this, I asked her a simple question: “Is this what you want to do?”
“Dad, I can’t see myself as anything else,” she said.
I talked to her about the possibility of going into infectious disease research because she could save millions of people with her work instead of the hundreds as a cardiologist. She said, “That’s not what I want to do, Dad.” My daughter is a lot like me, she likes the challenge of diagnosing and treating the problems rather than the environment of the laboratory.
How does this relate to lubricants?
Biological control in metalworking fluids is critical to the success of the process. Without biological control, there are problems with rust, skin irritation, stability, bad smells and poor tool performance. On the shop floor, our main line of defense against a biological attack is a well-formulated product with properly spelled out parameters for its use. The shop floor counts on regular additions of fresh fluid to the system to replenish the preservative package. If this control breaks down, complaints will occur and tankside additives under the control of the laboratory become necessary.
Once a product leaves the laboratory and hits the shop floor, a lot of things happen to it. With insufficient training, we lose control of it the day it goes into a machine. Following are two examples that might show how the most basic control—concentration—can lead to problems. In both cases, the complaints resulted in skin irritation.
I was at a plant with a sawing operation. The operator complained to me that his skin was irritated, and he even showed me a rash on his belly. We checked the coolant concentration and found it to be running half the recommended concentration. The operator never tested the coolant concentration, as he relied on the blue color for his control. When his system didn’t get enough preservative package (biocide and fungicide) to protect the system, his mold counts went out of control. The fluid pH dropped, and he had problems. I treated the system with a tankside additive and scheduled it for a total cleanout and sterilization. Two weeks later, he was doing fine.
I was at a plant with roll-forming processes. I met with the sales engineer and loaded our trunk with tankside additives. We had already assumed we were having biological problems. We started inspecting the machines, pulling samples for the lab and talking to operators. We didn’t see mold on the tanks or hear of odors. We checked the concentration levels in the machines and found the mixtures running almost double the levels recommended by the laboratory. We adjusted the concentrations in the machines. When we received the lab reports, we confirmed the suspicion. No bacteria or mold, but concentrations running at twice the recommended levels. The skin irritation was most likely caused by too much preservative (biocide and fungicide) and not from biological-related problems.
The shop floor is not a sterile environment. Anything and everything that can happen will happen. These two cases illustrate how biological preservatives can cause problems from opposite ends of the spectrum. Too much can lead to the same problems as too little. In both cases, the shop floors were more than willing to institute controls on the systems to eliminate the problems, and they did.
My daughter, the future doctor, will use diagnostic tools and medical history to determine the cause and treatment of ailments. A bad diet will mean surgery or the necessity to take a pill developed by a researcher in a laboratory. A good diet and you may never meet her. She’s a lot like me; she would rather work on problems we can’t avoid. I’m proud of her and know she’ll be there to cure those who need help.
Pete Oglevie is president of International Production Technologies in Port Washington, Wis. You can reach him at poglevie@intprotec.com.